Introduction: Batik Silk Scarves
Batik is a method of producing colored designs on textiles by dyeing them, having first applied wax to the parts to be left undyed. This is a step by step guide for how I make Batik silk scarves.
Step 1: Drawing Your Design Onto the Silk
Since this particular kind of silk is thin enough to see through, I was able to draw out a design and then trace right over the original design onto the silk. Thicker fabrics may require projecting a pattern onto the fabric or just drawing a design free-hand.
Step 2: Stretching the Silk Onto a Frame
In order to put wax and dye onto the fabric, it needs to be stretched over a frame so the fabric doesn't touch the table. There are a few different ways to do this, but the way shown in these pictures involves taking strips of other stretchable fabric and pinning them all along the edge of the silk. Use small, thin pins (silk pins) to pin right into the rolled hem of the silk, so it doesn't leave large holes in the silk. Once you have strips of fabric all around the edges of the silk, then you are ready to stretch it on a frame, (in this case, a simple wooden frame made a couple of inches larger than the scarf size I used). Finally, you use thumb tacks to pin those extra strips of fabric into the wooden frame. This leaves your silk scarf free to float above the table and away from the wooden frame.
Step 3: Tracing Over Your Design With Hot Wax
Next, more tracing happens, but this time, with hot wax! Using a tjanting tool (a Javanese instrument for applying hot wax in batik work usually consisting of a small thin copper cut with one or more capillary spouts and a handle of reed or bamboo). You mix small pieces of beeswax and parafin wax together in the little pot of the tjanting tool. Then, by holding it over a flame (a candle or an alcohol lamp) it melts the wax inside the pot and begins to drip out the spout of the tool. When the wax starts to consistently flow out of the spout, you know it is hot enough to draw onto the fabric with. The key is to have the wax be hot enough to melt into the fibers of the silk, and not just sit on top of the silk. If it only sits on top of the fabric, it will not act as a resist when dye is added to the silk. This means that dye could seep under the wax and bleed into other parts of your design that you don't want it to. Other times, you may want it to bleed, but it all depends on what kind of look you are going for.
Step 4: Painting the Silk With Dye
Here comes the really fun part, which is adding color to the fabric. Dye acts similar to watercolor when painted on to silk. If you drop dye onto a portion of the silk where there is no wax to act as a barrier, it will bleed through the fabric pretty far, before it stops. The wax acts as an outline, or a small wall, so the dye stays in a certain area, like a coloring book design. By adding water to the dye you can manipulate the texture left on the fabric, change the value of the color, or blend different colors together, just like a normal painting.
Step 5: Melting the Wax Off of the Silk
Once you have your entire design painted, the next step is to melt off the wax from the silk. This can easily be done by using an iron you don't care as much about (because it will get dirty with wax over time) and sheets of newsprint or old newspaper. You place your scarf on the ironing board first, then lay the newsprint on top. Once the iron is warmed up, all you have to do is iron over the paper and the wax will start to melt and come off onto the paper. If your scarf has a lot of wax on it from the design, it might take a few sheets of paper to get all of the wax out of the fabric. Once the wax is removed, you are left with the areas where dye did not reach the silk, as shown in the pictures above.
Step 6: Steaming the Silk to Set the Dye Into the Fabric Permanently
The steaming process is pretty important. Steaming dyes into fabric means that the colors will not run if they ever were to get wet again. It also makes the colors that much more vibrant, once they are steamed. Most dyes used on silk will involve steaming some how.
So, after the wax has been taken off of the silk, I lay the scarf out on a long piece of newsprint, and roll the scarf up in to it. Make sure that there is an inch or two of paper still showing, on either side of the scarf, before rolling it up. Once you have a tube shape, you tape off one end of the tube and then wrap the whole tube up into a coil. Use string or tape to make sure that the paper/scarf tube stays in this coil shape.
Cover the coil in more newsprint and then some kind of towel or washcloth. Then place the whole bundle inside a tin pie pan, with a tin foil cover loosely set on top. The whole point of this paper and tin bundle is to keep the scarf from getting wet while it is steaming.
Finally, you take a big canning pot and a tin can with both ends cut open. Fill the pot with about two inches of water, and place the tin can in the middle of the pot, standing up vertically. Next, place the pie pan/tin foil/scarf bundle on top of this can, so it is essentially floating inside of the pot, not touching the sides or the water at the bottom.
Bring the water to a boil. Take the lid of the pot, put some more newsprint and a towel around it, and place that on top of the pot. Again, this is to stop any water condensation from dripping down on to the fabric and leaving marks on the silk.
Bring the water down to a simmer and let it steam for about an hour.
Once this is done, you take the bundle out, unwrap the scarf, and let it sit for about 24 hours.
The last thing to do before ironing it out, is to gently hand wash the scarf in cool water to get any excess dye out of the material. Hang dry and ironing when damp can help get wrinkles out better
Step 7: Ironing Out and Revealing Final Product!
Once the scarf has been steamed, it will be a bit wrinkled, so you need to iron it out with the silk setting of your iron. It is often good to iron on the backside of the fabric so not to leave any marks from the iron on the most vibrantly colored side.
These scarves are all different examples of scarves that I have made over the last year with my own designs.
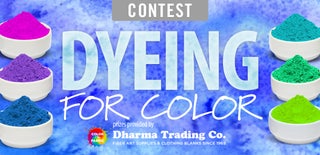
Grand Prize in the
Dyeing for Color Contest