Introduction: Bearded Dragon Enclosure With Webcam and Remote Monitoring
My daughter and I built this enclosure when her bearded dragon outgrew his old one. It's based on the standard "crossfire" design, (4'x2'x2') with some modifications that I hope improved on the original. It's 3/4" oak plywood. I normally would have gone with something cheaper, but pine is toxic to beardies. Fortunately the third sheet had enough material leftover to build a little stand with storage.
It has a web-accessible interface for a webcam, temperature monitoring, and even historical temperature graphing.
This is a guide on how we did it. Feel free to come up with your own ideas, improvements, simplifications. I put this instructable together to try to help out some other would-be cabinet maker/beardie owner.
REMEMBER: It's up to you to verify measurements, fits, etc. I made a best effort to be as accurate as I could be. When we were building I didn't always remember to grab a camera.
Step 1: Material List and Tools
Here is what we used to build the enclosure. Your mileage may vary.
(3) 4'x8' sheets of 3/4" oak plywood
(4) 3" carriage bolts with flat washer and nut
(2) 2'x4' luan or 1/8" plywood
(4) 1'x2' ceramic tiles
(2) Roughly 20" x 22" pieces of 1/4" tempered glass or acrylic. You'll want to wait until the build is almost complete before you buy this! You may need to adjust your measurements.
(2) Plastic sliding door tracks, 48" long, slotted for 1/4" glass.
(2) 8"x16" metal soffit vent covers (you can buy four if you don't want to make the oak vent covers)
(5) 3" round soffit vent covers
(3) 8' 2x4's
(4) 3/8" leveler legs
(4) 3/8" t-nuts
~10 ft. of red oak cabinet trim moulding
Box of 1" wood screws
Wood glue
Roughly 4 sq ft of aluminum screen
Box of 8d or 10d finish nails
(1) Raspberry Pi with Raspian
(4) DS18B20 Temperature Sensors
(3) 10" or 8.5" ceramic clamp lamps
(1) UVB fixture with a T5 reptisun 10.0 UVB tube
(1) USB web cam
(4) 90-Degree Surface Mount Hidden Spring Hinges
(4) 35 mm 105-Degree 1-1/4 in. Overlay Soft Close Hinges
(4) Wooden cabinet knobs
(1) 3/4" Twin-Screw Cable Clamp Connector
(3) 3-gang romex handy boxes
(3) 15 amp dimmer switches
(4) 15 amp dual receptacles
(1) 15 amp GFCI receptacle
(1) 15 Amp Digital In-Wall Timer
(2) 3-gang switch covers
(1) 3-gang receptacle cover
(1) 6' appliance cord
Approx. 5 ft. of 14 awg romex
Some scrap low voltage wire like cat-5
(~20) Wire nuts for 15 awg wire
(8) 3/8" button plugs
Wood putty-- I bought the pre-colored stuff to match my stain.
(2) rolls of Red Oak Veneer edging
Styrofoam for furniture
Bag of sanded grout
Polycrylic semi-gloss finish
tube of GE Silicone I caulk
Tools (some optional):
Router
Jig saw
Hand plane
Drill
Drill bits
Angle grinder
Table saw or skil saw
Phillips Screwdriver
Wire strippers/cutters
Hammer
Nail set
Hot glue gun and glue sticks
Household iron (one you can get glue on)
Step 2: Cut Out the Side Panels
Cut out the two side panels as shown. I built a simple router jig (picture 2) and used a 3/4" dado bit to cut the 3/4" dadoes. They are about 3/8" inches deep. This is important: if the depth isn't correct, the rest of your dimensions will be slightly out of wack.
CHECK YOUR MEASUREMENTS AS YOU PROCEED THROUGH THIS INSTRUCTABLE . You may have to adjust them.
You could go without the dadoes and simply butt the plywood together, but it won't be nearly as strong. Another option is to use angle brackets to hold the whole thing together.
Cut out the 7.5" x 15.5" holes for the side vents. I used a 4.5 inch circular saw for most of the cut, then finish with a hand saw.
Step 3: Cut Out the Two Shelves.
Measure and cut the two shelves. One will need to have additional cuts to accommodate the lights. I don't get into specifics on the light cutouts-- your lights will likely be different and so will your interior layout.
My example: I put two 10.5" squares in at the inside opposite corners, then off set the third roughly in the middle (as shown in pic #1).
I cut the long rectangle to take my 24" UVB fixture. I made a few square cleats from scrap to hold the UVB in place.
I used (3) 10" clamp lamps in my vivarium, but other sizes and types could work. Remember to size them so they fit in the top cavity.
Step 4: Assemble the Two Sides and Shelves
Fit your shelves into the dados on either side. Apply a generous amount of wood glue into the dado, making sure it is evenly spread.
Drill and countersink (2) 1" wood screws through each dado from the sides and into the shelves, making sure it's good and tight. The countersink should be 3/8" in diameter and deep enough to accept the dowel buttons without going too deep and undermining the strength of the wood. Leave to dry overnight.
Gently knock in the dowel buttons over the screw holes after giving them a thin coat of glue.
Don't forget to clean up the excess wood glue with a damp rag or it will ruin your finish. Cheap plywood (ANYTHING you get from a Big Box) has a very thin veneer-- you can't sand it far at all.
Step 5: Cut Out the Back Panel
Cut out the back panel. Make sure you don't need to tweak your measurements. It should fit snugly into the back.
I used a 3" hole saw to cut the holes for the back vents.
Step 6: Install the Back Panel
Fit the back panel into the enclosure. I put a generous amount of wood glue on all the edges, then when I was happy with the fit, I drove 10d finish nails through the sides and the shelves into the back. I put a nail about every 6" inches.
You'll see from the picture that I waited until later to drill the 3" holes in the back for the vent. I'd recommend in hindsight to do that before you install the back panel.
Step 7: Cut Out Front Face Pieces
Cut out the top, bottom and sides (x2) for the face of the enclosure.
Step 8: Attach Front, Bottom, and Side Face Pieces
Attach the top face piece. Glue and nail the piece in place. Use a clamp if possible to hold it firmly. Then, attach the bottom face, glue and nail it. Finally, install the 2" side faces. Try to make them all as level and smooth as possible.
The band edging (veneer) and the cabinet trim molding will hide most of the butt joints.
Step 9: Cut the Back Top and the Back Bottom.
Double-check the dimensions above. Your plywood might be warped, or your earlier cuts could be just slightly off.
Once you're sure, cut out the "back top" and "back bottom" pieces.
Step 10: Attach Back Top and Back Bottom Pieces
Attach the back top and back bottom panels. Glue them on three sides, then drive finish nails through the sides into the panel. You should clamp them overnight.
Step 11: Cut the Top Doors
Cut the top doors. These are the top of the viv and open on hidden hinges to reveal the lighting cavity.
Attach two knobs with glue and the screw provided with the knob.
Step 12: Add Door Stops Inside the Light Cavity
Cut scrap plywood and line the inside of the lighting cavity so the doors have a stop. It should be 3/4" from the top.
I tried to make it continuous all the way around to minimize the amount of light that could leak through. Screw and glue.
You'll also need a strip of plywood to run perpendicular to the other stops (pic #2). This is run between the two top doors. Measure and install an approximately two inch strip.
Step 13: Install the Top Doors
Install the two top doors with the (4) four 90 degree hidden hinges. Follow the manufacturers instructions. I bought the hinges at one of the Big Box stores.
I made liberal use of a hand plane to get a perfect fit. You'll want them tight, but not so tight that staining and finishing makes it too small or scrapes the sides.
Step 14: Install the (2) Two Sliding Door Runners
Cut the two plastic sliding door runners to fit your opening and glue them into place in the opening as in the picture. I used two-part epoxy.
It was a challenge to find the runners, but they are available online.
Step 15: Cut the Cabinet Doors
Cut the front cabinet doors. Attach two knobs with glue and the screw provided with the knob.
Step 16: Cut the Cabinet Sides
Cut the sides for the bottom cabinet.
Step 17: Cabinet Front
Cut the cabinet front. I used a jig saw to make the holes (marked with "X"'s)
Step 18: Cut the 2x4's for the Base Cabinet and Assemble
Cut (4) 43 1/2" 2x4's.
Cut (4) 18 1/4" 2x4's
Assemble them with plenty of glue and screws, making sure to countersink the screw heads so they don't get in the way later.
NOTE THE POSITIONS of the lumber in the pic! Your longest dimension should be 43 1/2".
Step 19: Assemble the Cabinet
Attach the cabinet sides onto the frame with glue and finish nails. The sides should line up perfectly with the front two by fours.
Then attach the cabinet face in the same manner. You'll notice that the cabinet face overhangs the frame and the side panels by about a quarter inch each side. This will make it easier to attach the iron-on veneer.
Measure and cut a luan or 1/8" plywood panel for the back of the cabinet and attach with nails. Measure and cut a sheet of luan or 1/8" plywood to fit inside the cabinet if desired.
Finally, I used scrap pieces of 3/4 plywood to cover the top of the cabinet. This is important for two reasons:
1) It adds height to the cabinet so when you attach the upper and lower portions, you'll have sufficient clearance to open the cabinet doors. Don't worry what it looks like, as long as it is strongly attached. The upper section will completely cover it.
2) It gives you something to bolt the top to.
At this point, you can dry fit the two cabinets together to make sure you have a good fit. When satisfied, Drill four holes through the bottom of the top cabinet into the lower cabinet. Countersink the holes so the tile will fit flat when you add it.
Push the (4) carriage bolts through the floor of the top cabinet, then add the washer and nut from below. Tighten.
Step 20: Attach Cabinet Doors
Attach the overlay hinges following manufacturer's instructions. I also added some magnetic catches.
Step 21: Veneer Edging and Attach Trim Molding to Cabinet Face (optional)
Measure the opening. Measure and cut your trim molding so it covers the sliding door tracks and overhangs the sides of the opening by approximately a half inch. This will make up for any gaps in the glass.
Attach with finish nails and glue.
The veneer edging is usually an "iron-on" type. Position it to cover the exposed plywood "sandwich" and apply with a hot iron. Repeat for all the edges that are visible on your enclosure. You can use a piece of sandpaper to plane down any overlap of the edging.
Step 22: Oak Louvers and Vents
You can purchase these oak louver vents, but they're pricey. I made mine out of 1" x 2" oak boards for half the cost. I cut 45 degree mitered corners, then clamped and glued the frames together. I cut strips of oak about 1/8" thick so they fit snugly in the frame and simply glued them in place.
If you go with wood, screw and glue it over the 7.5" x 15.5" vent hole.
Alternatively, you could use 8"x16" aluminum sofit vent covers like the ones I used inside (pic #3) which attach with small 1/2" wood screws.
To attach the (5) round soffit vent covers, run a ring of silicone around each round soffit vent and insert into the five holes you cut in the back panel.
Step 23: Prime and Paint the Inside of the Cabinet
I painted the interior before staining the exterior, thinking it would be easier to sand off any mistakes.
Make sure you give the plywood a light sanding, then prime with a latex primer. Sand the primer lightly when dry, then paint with a latex paint. I used stuff I already had to paint the light cavity white and the actual interior of the vivarium sky blue.
Step 24: Stain and Finish
Stain the outside of the cabinet, if desired. I used five coats of satin polyurethane on the exterior and sealed the inside with five coats of Polycrylic, which is low VOC and less toxic to the dragon.
Step 25: Electricity and Lights
I won't go too far into explaining the wiring-- I don't want to be responsible for anyone getting electrocuted! It's very basic, though, if you've done electrical work in the past.
I wanted a timer, three separate dimmers (two on the timer, one independent of it for a ceramic heat emitter),and a constant power outlet for the raspberry pi that was independent of the timer. See the photo #1 above for functions. All of it was attached to a six foot heavy duty appliance cord.
Possibly overkill. You could just run your wires directly from your fixtures or use a plug in timer and an extension cord or two.
I built custom brackets for my clamp lamps from an old erector set (pic #3). I also cut small pieces of aluminum screening to cover the spaces around the lights. Just in case my lizard decides climbing into the light cavity is a good idea. It also will keep any errant insects from escaping.
I added (3) steel mending plates (pic #2) above each lamp as added insurance against burn.
Temperatures in the light cavity have never gone beyond 105 degrees in my setup (I put a temperature probe in it). I used very small bulbs because the vivarium holds a lot of heat.
You can prop up the top doors for added ventilation. I've also been considering adding two round butterfly vents to the top doors.
Step 26: Raspberry Pi
If you're not familiar with the Pi or linux, there's way too much for you to learn for me to go into it here. It's not too difficult, though, if you're willing to learn.
All of the screens in the pictures were created using freeware and are widely available on the internet. Adafruit's website has the exact set of instructions I used to get my temp sensors hooked up and working.
I loaded my raspberry pi with Raspian Linux, one of the most widely used OS's for the Pi. I connected the four DS18B20 temperature sensors to the gpio and voila! I had temperature readings from four different locations in the enclosure. I drilled small holes in the back panel to push the sensor in.
Once you have the sensors configured, you're left with where to store the data. I went with a SQLite database and set up a cron job to periodically poll the sensors and update the DB. Tutorials for SQLite are readily available.
A simple web cam and the Motion package (freely available) and I had a live cam from inside the enclosure.
To wrap it up, I configured an apache server to host my new website. Now we can check on my beardie wherever we go!
We have a regular two-probe thermometer inside the viv, as well. You need to be able to check the temps the old fashioned way. It's also a good idea to check with an infrared temp gun from time to time.
Step 27: Furniture and Tile
We built the furniture from insulation Styrofoam. The frame was hot-glued together, then covered with a thin layer of soupy, sanded grout, spread with a putty knife. Once that was dried, we added four more layers of soupy grout, smoothing it with a wet paintbrush between coats. Each coat should be allowed to dry before applying the next.
The pieces will get heavy quickly.
Once we had them grouted to our satisfaction, we sealed with spray polycrylic, adding thin coats until two cans were completely empty (5-7 coats).
Let the furniture dry out until the smell is completely gone. We left ours to dry for about two weeks.
We bought the fake plants at a dollar store. After washing them thoroughly, we secured them to the furniture with silicone.
We used (4) 1x2 ceramic tiles (as rough-surfaced as we could find) to line the floor of the enclosure. We did not adhere them in any way to facilitate easy removal and cleaning.
I used an angle grinder to cut them to size.
Step 28: Glass
After everything else is complete, measure your opening and get your glass. I used 1/4" tempered glass. According to the instructions on my sliding door channel, I needed to buy my glass so the vertical measurement was 1/4" less than the total opening size. CHECK YOUR INSTRUCTIONS. Tempered glass is not cheap. I paid almost $60 per panel.
I also bought a small length of aluminum handle material designed to be mounted on 1/4" glass. I secured it with silicone, per manufacturer's instructions.
You could also use plexiglass and save some money, but beware: it scratches very easily.
Step 29: Wrapping Up
Well, that's it. Now does that look like a happy beardie or what?
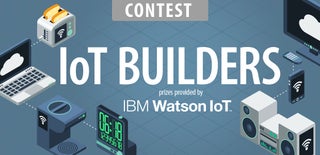
Third Prize in the
IoT Builders Contest