Introduction: Black and Coral Laser Cut Dress
Laser cut clothing is all over runways and fashion blogs so I (obviously) wanted a laser cut dress, too. And, because I have way more making impulse than shopping impulse I didn't even consider buying a dress when I knew I could make one. The hardest part of this dress is learning how to design vectors well if you haven't before. If you already work with vectors then the hardest part will be settling on a design.
Step 1: Supplies and Equipment
Materials:
Satin - about a yard
Cotton Jersey - one oversized t-shirt of 1 to 2 yards, depending on how long you like your dresses
Satin Ribbon - 3-4 yards of 1 7/8" wide
Sewing Thread - match the colors, but I shouldn't have to tell you that
Supplies:
Sewing basics - scissors, chalk, pins, etc
Sewing machine - ideally this will have a stretch stitch, otherwise use a narrow zig-zag
Laser - join a fab lab/tech shop, find a laser cutting service, make friends with a laser owner or I guess you could pick one up at your nearest laser store
Computer with vector friendly software - Illustrator is my first choice, Inkscape works well and is open source (free)
Some notes about fabric choices:
Because I was planning to use a laser on this dress materials selection became a priority. I love silk, cotton and wool as much as anyone, but natural fibers burn when lasered and fray easily afterward. Vinyl releases chlorine gas when cut with a laser which is probably bad for humans and definitely bad for the lenses in a laser unless it has special ventilation set up.
This left me with polyester as my first choice. When you cut it with a laser the edges melt and leave you with a fray resistant edge. It also comes in a huge variety of colors - I chose a pretty shade of coral. That said, I wanted a dress I could throw on to go out on a summer evening and I'm not a fan of wrapping myself in layers of plastic when it's warm.
I decided to make the dress itself from cotton jersey and use the polyester as cap sleeves and a belt. It's the best of both worlds - the cotton is soft and matte in finish, the satin adds a little sparkly formality without having to feel like I'm wearing a disco ball. Because the fabric stores I frequent seem to be avoiding stocking jersey at all costs and I really don't like the way interlock wears I opted to pick up a plain black very oversized t-shirt. Go for a good brand, the quality of the fabric will be a lot nicer. Also pre-wash it, failure to do this may result in a dress that is embarrassingly short after it's been washed.
Step 2: Pattern
I kept the styling of this dress simple to play up the satin details. I referenced the Jocelyn pattern available from Burda for my design. That dress is made entirely from woven fabric so I had to re-work the dress itself, but I used the style/design of the sleeves for what I did. (I explain the process for the sleeves in the next step.)
For the main dress I used my standard knit block. I made the pattern from tracing my favorite knit top. It takes a little craftiness to get the armscye line traced off correctly but you only have to do it once. Be sure that the top you trace doesn't have any lyrca content (unless the fabric you're using has lycra in it.)
I based the top line of the dress on the strapless bra I'm going to wear with it.
If you weren't up to patterning it all out I would simply sew a tube of fabric big enough for your hips/bust, put it on, and then draw on it what you want the top line to be and where to take it in at the waist. Knits are pretty forgiving.
Attachments
Step 3: Setting Up the Laser Files
First off, locate a laser to use. You need to be sure that you design for the size and specifications of what you're using. Also, if you have a choice choose someone that will charge based on cutting time rather than per inch. Satin cuts like butter in even the weakest of laser cutters so you'll get a much better price that way.
The laser that cut my parts has a 12x18" cutting area. It runs at 35 watts and the total cutting time was 21 minutes and 41 seconds.
I knew that my parts had to be smaller than 12x18. I downloaded the Jocelyn pattern from burdastyle.com. I opened the printshop version in Illustrator. I traced over the two sleeve pieces. I copied those traces and pasted them into an empty document. The burda file had a lot going on and was kind of slow on my computer.
Keep in mind that the pattern pieces have a 5/8" seam allowance built in. I aligned the two pieces to pretty much be one piece. I drew a 12x18" box around it so that I was aware of how large on an area I could fill. I considered adding a seam to the sleeve but I opted to tweak it down to completely fill one panel. I basically started drawing over those pieces until I liked the design. I went with a gridded pattern but you can really cut anything. Keep in mind that thin areas will be fragile.
Once you have a design you like remove all of the reference lines (like the original pattern piece traces.) Select all of it and set the fill to none and the outline to black. You are now seeing your part the way the laser will see it. It will cut all of these lines.
If you haven't worked with vectors before the two best topics to check out in the built in help system or on google are "bezier" and "boolean". These are great ways to make smooth curves and complex shapes. The better you get at using the tools in the software the better you will be at making good files that work they way you expect them to.
Another good thing to do is to print off an exact or miniature version of what you're having cut. Sometimes manipulating a real object in front of you will give you a better sense of any design mistakes than looking at a computer screen will.
Once you have everything the way you want it set up the files the way your particular laser operator wants them. Also, if you're using your own materials cut them to specifications then iron and iron again - smoother fabric gives you a more precise cut. I had to cut my fabric to 1/2" larger than the 12"x18" cutting field. Cutting the fabric on grain will also help it drape better in the finished product.
Step 4: Assembly
If you've made it this far everything left is easy.
Cut out the knit dress (if you haven't already). My shirt was just long enough to make a dress that wasn't scandalous or illegal, so I left the lower hem intact and just cut my side seams and top edge.
Sew up the size seams on the dress and finish the edges. Use a stretch stitch if you have it, otherwise use a very narrow zig-zag stitch. If you use an ordinary straight stitch the stitching lines will break as soon as you pull on the knit.
Sew a strip of ribbon folded over the neck edge of the sleeves. That cut and melted edge of the satin can be a bit scratchy, and this helps stabilize the edge against any unexpected force.
Pin the sleeves to the dress right sides together. Sew them in place. Roll the top edge of the knit (catching in the edge of the satin) and sew in place.
Step 5: Details and Finishing
I added a belt to my dress. I had some gridded strips cut at the same time as the sleeves. I pieced them together into a long strip and then carefully hand stitched them onto a strip of satin ribbon. I made a bow from the same. I should sew a hook and eye or snap under the bow to close the belt, but for now I'm using a safety pin. I don't like committing to one length but I don't want a buckle. These are the kinds of decisions I struggle with every day.
This dress will be best off hand washed, the agitation of a washing machine might start to break down the otherwise sealed edges.
I really want to incorporate laser cutting into everything now, and I have a bunch of half finished garments on my hard drive waiting to be turned into viable clothing. I'm also looking forward to fall when wearing a matte satin blouse doesn't seem like such an unappealing prospect.
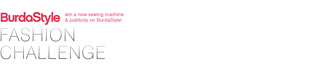
Finalist in the
BurdaStyle Fashion Challenge