Introduction: Bowling Alley Lane to Table
True story- "Hi Peter, we picked up a section of a bowling alley lane from a local building supply salvage company, could you turn it into a dining room table with a fir base to match?? So of course I said "I'll see what I can do!!"
I'm writing this Instructable so you can see what I did... just in case you (or someone you know) has an extra chunk of bowling lane laying around ; )
The laminated piece of fir was roughly 43'' x 84'' x 3'' thick, It was made up of 35 - 1 1/4'' X 2 3/4'' nailed together. The salvage company cut the lane into chunks and was selling the pieces. I thought all bowling lanes were made from maple but it turns out that sometimes they only use maple for the first 20 feet, then switch to fir for the rest of the lane.
Step 1: Prepping the Table Top
The top probably weighed 250 lbs ( so thankful for a forklift ) and the edges were in really rough shape.
I needed to square and true up the edges, but I first had to counter sink the nails that were used to laminate the fir together. I used a small chisel to carve out around all of the nail heads and then drove them deeper in with a hammer and a bolt. Using a hand power planer with a new blade, I was able to true up the edges enough so that I could laminate a new edge all around the top.
I machined 1 1/4'' x 3'' solid fir to wrap the edges, then using my biscuit joiner I put two rows of biscuits to fasten the edges on. I aligned and glued the ends on first, and then the long sides (using waterproof polyurethane glue). I rounded over all of the edges using a 1/4'' round over bit in my trim router, then came the hours of sanding and filling the cracks with wood filler ( the best-est part !! not ).
I know it's not standard practice to cap the ends on a laminated solid wood top with a piece of solid material, but I had no other way to cover the plywood that had been glued to the underside. I was fairly confident that because of how dry the top was, expansion and contraction should not be a problem. I forewarned the clients of this and they said it would add character if it some movement should occur.
Step 2: Machining the Legs
Once I determined the base design, I would need 2 - 3'' x 3'' x 60'', 2 - 3'' x 3'' x 21'', 4 - 3'' x 3'' x 30'', 4 - 3'' x 3'' x 27'' posts, that would be mitered together. Since I did not have any 3'' x 3'' fir stock I decided to make hollow legs using 3/4'' thick fir boards.
I've built many different sizes of posts over the years using this method. Each section of 3'' x 3'' post requires four sides - 2 pieces 3 1/8'' wide and 2 pieces 2 9/16'' wide x the length of post required plus a couple of inches for cutting.
First, saw cut 13/16'' high a 1/4'' from the fence ( only on the 3 1/8'' wide boards, both sides ). Then you reset the saw and cut 1/2'' high and 13/16'' ( to the outside of the blade ) from the fence and cut a rabbet down the length of the board.
**SAFETY NOTE** be sure to use a push stick that pushes the off cut all the way past the blade! If you don't it could catch between the fence and the blade and come shooting back at you !!
Save the off cut pieces for gluing up the posts.
Step 3: Gluing Up the Posts
Tape a piece of off cut from the rabbet down the length of the two - 2 9/16" wide boards, then run three beads of glue down the two - 3 1/8'' boards with the rabbet and assemble the four pieces. Using 5'' wide stretch wrap as a clamp, wrap the entire length. The off cut pieces ( taped on the sides ) put pressure on those pieces to pull the four sides tightly together.
The nice thing about doing hollow posts this way, is that you can maintain the nicer grain on all four sides of the post. In my case edge grain fir, and you can make any size post you require.
It is also far easier to cut rabbets down the length of a board than try to cut a cut a 45 degree miter joint down the edges.
Step 4: Construction of Legs
After the legs have dried and the stretch wrap was removed, I used a flush trim router bit to remove the slight overhang and glue.Then I dressed all four sides of the post by running them though a planer bringing them down to 3'' x 3'' square.
I mitred both ends of all posts on the chop saw ( using stops to make sure like pieces were the same length ). I cut two biscuits in each mitre, glued and clamped the pieces to make the three squares that made up the base.
Step 5: Finishing
Using a random orbital sander I thoroughly sanded the legs and table top down to 150 grit sandpaper. I stained the legs dark and the top a lighter stain as requested.
I prefer using a good quality water based stain ( Saman water based stains ). I find it goes on a lot more uniformly than solvent based stains, primarily because water based stains have a longer open time and can be applied with a stain sponge and wiped uniformly with a clean cloth.
After letting the stain dry overnight I sprayed on 3 coats of clear water based lacquer in a spray booth, lightly sanding in between coats. The booth in the photo is the one I built over a year ago. It was strictly designed for water based finishing (and is also one of my Instructables ).
If you don't have access to a spray booth - I have seen and done some pretty good finishes using wipe on polyurethane applied with a foam brush.
Step 6: Assemble
The assembly is pretty simple. I cut three - 3" strips of 1/4'' mdf for drilling templates, one the inside width of the two bases ( 24" long ), one the outside width of the bases ( 30" long ), and one the distance in on the cross member ( 8" long ). (see photo #1)
To make sure all the holes line up I stacked the three pieces and drilled the pilot holes, then it was just a matter of drilling the holes in the legs using the mdf templates. Using the 8" template I drilled pilot holes in the cross member. After drilling I carefully positioned the pieces, then I used 4'' screws ( from the top and bottom ) to hold the whole unit together.
Once the table pieces were moved to their permanent location, the top was centered on the base and screwed on from underneath using 4'' screws . Heavy felt pads were applied on the bottom to protect the floor.
Step 7: Conclusion
FYI, it took 3 of us to carry the top into the house and place it on the base. The amount of fir in the top is equivalent to a 14"-15'' diameter log 7 feet long, plus 1 sheet of 1/2" plywood.
The owner told me afterward that he could have gotten a nine foot piece ( I'm so grateful he went with the seven footer! ).
I don't anticipate much movement in the fir itself ( expansion and contraction ) because of how dry the fir was initially, but if some cracking does occur it will most likely be minimal and just add character to the bowling alley top.
My clients were more than pleased with how it turned out, and they now have a very heavy, unique conversation piece.
Cheers !!
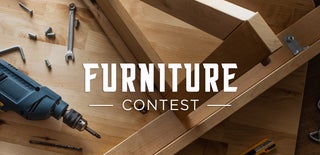
Runner Up in the
Furniture Contest