Introduction: Brushless Motors
This instructable is a guide/overview of the motor technology behind modern enthusiast quadcopter motors. Just to show you what quadcopters are capable of, watch this amazing video. (Watch the volume. It gets very loud) All credit goes to the original publisher of the video.
Step 1: Terminology
Most brushless motors are usually described by two sets of numbers; such as: Hyperlite 2207-1922KV. The first set of number refers to the stator size of the motor in millimeters. This specific motor stator is 22mm wide and 7mm tall. The old DJI Phantoms used 2212 motors. The stator dimensions usually follow a trend:
Taller stator allows for a higher top end performance (Higher RPM ranges)
Wider stator allows for a stronger lower end performance (Lower RPM ranges)
The second set of numbers are the KV rating for the motor. The KV rating of the motor is the velocity constant of that specific motor, which basically means that the motor will create a back EMF of 1V when the motor is spun at that RPM or will spin at an unloaded RPM of the KV when 1V is applied. For example: This motor paired with a 4S lipo will have a theoretical nominal RPM of 1922x14.8 = 28,446 RPM
Actually, the motor may not reach this theoretical speed because there are non-linear mechanical losses and resistive power losses.
Step 2: Fundamentals
An electric motor develops torque by alternating the polarity of rotating electromagnets attached to the rotor, the rotating part of the machine, and stationary magnets on the stator which surrounds the rotor. One or both sets of magnets are electromagnets, made of a coil of wire wound around a ferromagnetic core. Electricity running through the wire winding creates the magnetic field, providing the power which runs the motor.
The configuration number tells you how many electromagnets there are on the stator, and the number of permanent magnets there are on the rotor. The number before the letter N shows the number of electromagnets there are in the stator. The number before the P shows how many permanent magnets there are in the rotor. Most out-runner brushless motors follow the 12N14P configuration.
Step 3: Electronic Speed Controller
An ESC is the device that converts the DC electricity from the battery to AC. It also takes in data input from the flight controller to modulate the speed and power of the motor. There are multiple protocols for this communication. The primary analog ones are: PWM, Oneshot 125, Oneshot 42, and Multishot. But these became obsolete for quadcopters as new digital protocols arrived called Dshot. It does not have any of the calibration issues of analog protocols. Since there are digital bits being sent as information, the signal is not disrupted by the changing magnetic fields and voltage spikes as opposed to their counterpart. Dhsot isn't really appreciably faster than Multishot until DShot 1200 and 2400, which can only run on a few ESCs at this point. The real benefits of Dshot are primarily the two-way communication capacity, particularly the ability to send room data back to the FC for use in tuning the dynamic filters and the ability to do things like turtle mode (temporarily reverse the ESCs to flip the quad over if it's stuck upside down). An ESC is primarily made of 6 mosfets, 2 for each phase of the motor and a microcontroller. The mosfet basically alternates between reversing the polarity at a certain frequency to regulate the RPM of the motor. The ESC's have a current rating as that is the maximum amperage draw the ESC can sustain for long periods of time.
Step 4: Efficiency
(Multi strand: Purple Motor Single Strand: Orange Motor)
Wire:
Multi stranded wires can pack more volume of copper in a given area compared to a single thick wire wound around the stator so the magnetic field strength is slightly stronger but the overall power draw of the motor is limited due to the thin wires(Given that the multi stranded motor is constructed without having any crossover of the wires which is highly unlikely due manufacturing quality). A thicker wire can carry more current and sustain a higher power output compared to an equally constructed multi strand motor. It is harder to build a properly constructed multi stranded motor therefore most quality motors are built with a single strand of wire(for each phase). The small advantages of multi strand wiring are easily trumped by the manufacturing and mediocre designing, not to mention that there is a lot more room for mishap if any of the thin wires overheat or short circuit. Single strand wiring does not have any of those problems as it has a much higher current limit and minimal points of short circuit. So, for reliability, consistency, and efficiency, single strand windings are the best for quadcopter brushless motors.
P.S. One of the reasons that multi stranded wires are worse for some specific motors is due to skin effect. Skin effect is the tendency of an alternating electric current to become distributed within a conductor such that the current density is largest near the surface of the conductor, and decreases with greater depths in the conductor. The depth of skin effect varies with the frequency. At high frequencies the skin depth becomes much smaller. (For industrial purposes, litz wire is used to counteract the increased AC resistance due to the skin effect and save money) This skinning effect can cause electrons to jump across the wires within each coil group effectively shorting them to one another. This effect usually happens when the motor is wet or is using high frequencies of more than 60Hz. The skinning effect can cause eddy currents that in turn creates hot spots within the winding. This is why using using smaller wire is not ideal.
Temperature:
The permanent neodymium magnets used for brushless motors a quite strong, they usually range from N48-N52 in terms of magnetic strength(higher is stronger N52 is the strongest to my knowledge). Neodymium magnets of the type N lose part of their magnetization permanently at a temperature of 80 °C. Magnets with the N52 magnetization have a maximum working temperature of 65°C. A vigorous cool-down does not harm neodymium magnets. It is recommended that you never overheat the motors as the enamel insulating material on the copper windings also have a temperature limit and if they melt, it can cause a short circuit burning out the motor or even worse, you flight controller. A good rule of thumb is that if you can't hold onto the motor for a very long period of time after a short 1 or 2 minute flight, you are probably overheating the motor and that setup will not be viable for extended use.
Step 5: Torque
Just like there is motor velocity constant, there is a torque constant. The image above shows you the relationship between the torque constant and the velocity constant. To find torque, you just multiply the torque constant with current. The interesting thing about torque in brushless motors is that due to the resistive losses of the circuitry between the battery and the motor, the relationship between the torque and KV of the motor is not as directly related as the equation suggests. The attached picture shows the actual relationship between torque and KV at various RPMs. Due to the added resistance of the entire circuit, the % change in the resistance is not equivalent to the % change in the KV and therefore the relationship has a weird curve. Since the changes are not proportional, the lower KV variant of a motor always has more torque until a certain high RPM where the RPM headroom of the high KV motor takes over in strength and produces more torque.
Based on the equation, KV only changes the current it takes to produce the torque, or inversely, how much torque is produced by certain amount of current. The ability of a motor to actually produce torque is a factor of things like magnet strength, air-gap, cross-sectional area of the windings. As the RPMs increase the current rises dramatically primarily due to the non-linear relationship between energy and RPMs.
Step 6: Additional Features
The motor bell is the part of the motor that will take the most amount of damage in a craft so it is imperative that it is made of the best material for the purpose. Most cheap Chinese motors are made of 6061 aluminum that easily deforms in a hard crash so stay away from asphalt while flying. The more premium side of the motors use 7075 aluminum which offers much greater durability and longer lifespan.
The recent trend in quadcopter motors is to have a hollow titanium or steel shaft as it is lighter than a solid shaft and has great structural strength. In comparison to a solid shaft, a hollow shaft is of less weight, for a given length and diameter. Moreover it’s a good idea to go ahead with hollow shafts, if we our emphasis is on weight reduction and cost-cutting. Hollow shafts are much better to take torsional loads compared to solid shafts. Additionally, the titanium shaft will not strip as easily as the steel or aluminum shaft. Hardened steel can actually be better in terms of functional strength than some of the titanium alloys commonly used in these hollow shafts. It really depends on the specific alloys being discussed and the hardening technique used. Assuming best case for both materials, titanium will be lighter, but slightly more brittle, and hardened steel will be tougher but slight I heavier.
Step 7: References/ Resources
For extremely detailed testing and overview of specific quadcopter motors, check out EngineerX on YouTube. He posts detailed statistics and bench tests the motors with various propellers. https://www.youtube.com/user/EngineerX
For interesting theories and other extra information on the FPV racing/freestyle world, watch KababFPV. He is one of the greatest people to listen to for educational and intuitive discussion on quadcopter technology.
https://www.youtube.com/channel/UC4yjtLpqFmlVncUFE...
Enjoy this photo.
Thank You for visiting.
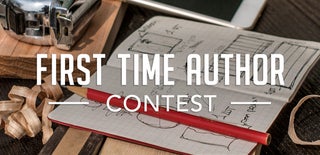
Participated in the
First Time Author