Introduction: Build the Rainbow Apparatus
The The Rainbow Apparatus (a.k.a The Astral Chromascope) is an optical contraption that lets you see the colorful energy from ordinary things! In this Instructable, I will show you how to build your own to explore the technicolor vibes of the stuff around you!
Step 1: Gathering the Materials Needed
This build requires a 3D printer and some basic soldering and assembly skills. You will need:
- A 3D printer.
- Clear packing tape (or a lamination machine).
- White paper.
- Scissors.
- A DC wall adapter recycled from some discarded electronics.
- An adjustable mini DC-to-DC step down converter.
- 20mm high-power LED stars, in the colors of red, green and blue.
- A multimeter (optional: a variable voltage bench-top power supply).
- A soldering iron and rosin core solder.
- Some scrap wire, some wire cutters and a wire stripper.
- Electrical tape.
- Some sort of glue for plastics. Something semi-permanent like E6000 is a good choice.
- Optional: Green felt to cover up the bottom of the base.
Sourcing the Power Supply:
The power supply is a regular "wall-wart" type that comes with most electronics. Ideally you have some lying around from discarded electronics that you can use. Most wall warts will put out 4.5V, 5V, 9V, 12V or sometimes even 24V. The other important rating is whether it is DC (common) or AC (less common) on the output.
For this project, you will need either a 9V or a 12V adapter minimum. It needs to put out about 9 watts minimum. The wattage is simply the product of the output voltage and the output current written on the label. For example, if the label said the output voltage was 9V at 1A, it would mean it puts out exactly 9 watts. If the adapter had a 12V output with a current of 0.85A (850mA), it would mean the output would be 10.2 watts and would also be suitable.
For your own safety, do not use a power supply larger than 12V or 2 amps!
Sourcing the parts from eBay:
Most of the electronic parts can be obtained from eBay very inexpensively. For the LEDs, search for "20mm LED star". You will likely find many choices of colors and wattage. Get one (or several) of each primary color, red, green and blue and pick the 3 watt variety. Make sure the size is 20mm so that it will fit properly on the 3D printed base.
The other critical part of this build is an adjustable mini DC-DC step-down buck converter. These are small circuit boards that convert a higher DC voltage into a lower voltage. You will need one that has an adjustable voltage on the output. The ones I use are really small (17.5mm by 11.14mm) and the 3D printed base has a cut-out for that particular size.
I've seen them on eBay with the title "5Pcs MINI360 3A DC-DC Step Down Buck Power Supply Converter Module MP2307 Chip", but the exact same thing are sold by many sellers. Make sure the picture matches and that there are two solder pads on each end of the board. See the picture for the right type and the wrong type.
Step 2: 3D Print the Parts
You will need to print the following parts from their STLs:
- 1x Base.stl
- 1x EyeGuard.stl
- 3x Pillar.stl
- 1x Retainer.stl (print using "spiralize" mode)
- 1x Ring.stl
- 1x TurnWheel.stl
For advanced users who want to customize the design, I have also included the OpenSCAD source file.
Step 3: Print Out the Projector Screen Template and Decal
- Load the attached ".svg" template into Inkscape and print.
- Either use a lamination machine to laminate the page, or:
- Cover the white circle and the decal with parallel strips of clear packing tape.
- Repeat on the reverse side.
- Cut out the circle.
- Cut out the decal.
Attachments
Step 4: Assemble the Projection Screen
- Insert the screen into the ring part to ensure a proper fit.
- Apply some adhesive around the edges to secure it.
- Slide in the retaining ring for additional support.
Step 5: Learn Some Electronics: What Is a Buck Converter?
A buck converter is a device that converts one DC voltage to another DC voltage, sort of like a transformer, but for DC rather than AC.
When lighting small LEDs, it is common to use a resistor to limit the current, but for higher power LEDs this would be very inefficient as a lot of energy would be converted into heat!
To avoid this, we can use a custom constant current LED driver, or we can use a generic buck converter that outputs an adjustable voltage. A buck converter won't limit the current, but the current going through the LEDs is proportional to the voltage. So if we start with a low voltage, we can raise it slowly until the desired current flows through the LEDs. It's not plug-and-play like a LED driver, but it does the job just as well when properly adjusted.
For the following steps, we will start with 7V output on the buck converter and then very gradually turn it up. This step is crucially important, because if we overshoot the operating voltage, the current will increase dramatically and something will let out the magic smoke!
Step 6: Initial Assembly and Voltage Tuning
Cut the DC connector off the end of the wall wart's cord and separate the two wires.
Strip about 5mm off the ends and make sure the ends do not touch. Now, with the wall wart plugged in, use your multi-meter to measure the voltage on the ends of the wire. Note down which end is positive for later.
Now unplug the wall-wart and solder the wire ends to the "in+" and "in-" pads on the DC-to-DC converter. Be absolutely sure you get the polarity correct and that you are soldering to the input side of the board (check the reverse side of the board for labeling).
Before proceeding, measure the voltage on the output pads. Turn down the little tuning screw until the voltage reads 7V and make note of which direction you need to turn the tuning knob to increase or decrease the voltage. Notice how sensitive the adjustment is. You will need to be able to adjust the voltage in fine increments for the next step.
This is important: before proceeding to the next step, set the output voltage no higher than 7V! Also, make sure you are using red, green and blue LEDs! The choice of the starting voltage comes from the sum of the voltage ratings of these particular LEDs, which are 1.8V, 2.0V and 3.3V respectively.
Step 7: Wiring Up the LEDs and Fine Tuning Current
- Set the LEDs on the slots in the base and cut the length of wire you will need to wire them up in series. You will need to go from the + of one LED to the - of the next.
- Solder the LEDs in series. A set of set of bench top helping hands is very helpful for this task!
- At the beginning and end of the LED chain, solder two longer lengths of wire, preferably of two different colors, so you can keep track of which is positive and which is negative. This wire needs to be long enough to go through the holes, wrap around the channel on the back, and into the notch for the buck converter.
- Glue down the LEDs to the slots on the base and feed the longer wires down one of the vertical shafts.
- Flip over the base. Solder the "-" wire to the "out-" terminal of the DC-to-DC converter. Mind the polarity—if you get it reversed, the LEDs will not light!
- At this point, the "+" wire is still disconnected from the "out+" pad. Set your multi-meter to DC amps and plug in the wall wart. Connect the multi-meter in series with the loose wire and the pad and ensure the current is around 400 mA.
- If you need to adjust the current, do so by turning the adjustment screw by very tiny amounts and checking the current.
Note: If you have a bench-top power supply with a built in current meter, it would be easier to use that to tune the voltage and brightness of the LED chain separately.Once you find the correct operating voltage, you can then adjust the voltage on the DC-to-DC regulator to match that ideal operating voltage prior to hooking up the LEDs.
Step 8: Finishing the Wiring and Testing
- Unplug the wall wart and solder the "+" wire to the "out+" pad to complete the circuit.
- Secure the DC-to-DC converter in the recess using a dab of glue and wrap any excess wire in the channel.
- Plug in the wall adapter and make sure it works.
Now, plug in the wall wart for final testing. The LEDs will likely be rather bright and uncomfortable to look at, so don't do that (instead, turn off the lights in your room and look at the pretty colors that are projected on your walls!).
Before proceeding with assembly, let it run a couple minutes and check back regularly to make sure that it is not getting too hot to the touch. If it is, dial back the voltage on the DC-to-DC converter—do it slowly and be very careful not to turn it the wrong way! You can let the LEDs run warm, but not hot enough to melt the plastic, produce weird smells or burn your house down!
As an added safety precaution, do not run this device unattended!
Step 9: Completing the Base
Cover the DC-to-DC converter and channel with electrical tape. Then, cut out a piece of green felt use it to cover the bottom of the device. Use some glue or spray adhesive to stick the felt on the bottom.
Step 10: Completing the Assembly
Proceed with the assembly by gluing in the three pillars into their slots in the base. Then fit the projection screen on the top of the pillars.
Now, put in the eyeguard (I call it that because it keeps light from blinding the user). The eyeguard and the turn wheel are similar in appearance, but the smaller one is the eyeguard. It has partitions on the inside to keep light from the LEDs from mixing.
Place the eyeguard on the base and align it until all colors blend into a white-ish color that covers the entire screen. Run a bead of glue around the edge and tack it down. Use double-sided tape to attach the decal to the base.
Step 11: Have Very Groovy Time!
Now, put the turn wheel over the eyeguard. This final piece should not be glued down. You can rotate it to partially obscure the light and make cool color patterns! Stick various objects, such as 3D print scraps, behind the screen to cast totally groovy rainbow shadows!
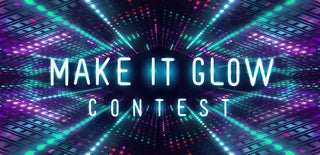
First Prize in the
Make it Glow Contest 2018