Introduction: Building a Workbench Out of Pallets
I am a bit of a sucker when it comes to looking for cheap ways of getting wood for my projects.
A couple of weeks ago I was running some errands when I came across a large sign that had a magic word on it - Free!
The free item in question were pallets. Intrigued, I pulled over and saw a mother-lode of pallets.
I had recently noticed however that there was a lot of material online around using pallets for wood projects. Further research also told me that the wood used in pallets, while looking a bit worse for wear, can be made from a large number of types of wood, including many desirable hardwoods.
The bounty that was before me gave me an idea...
Earlier this summer, I moved my shop to a slightly larger space.
Because of this move, I now had the opportunity to finally have a proper workbench and allow me to retire the old Black and Decker Workmate that had served me faithfully for many years.
Since I was fairly keen to try a project with recycled pallets, I figured that a basic workbench would be the perfect first addition for my new shop.
So, I loaded up a few choice pallets from the pile into the back of my truck and headed home.
Supplies
- Pallets - If possible find pallets that are 8 to 10 feet long
- Pallet buster - I got mine from Amazon
- Miter saw
- Drill with screw bit
- 2.5 inch deck screws
- Tape measure
- Crowbar
- Hammer
- Locking pliers
- Paint
Step 1: Disassembling the Pallets
The first thing I did once I got my bounty home was to do a bit of research on what it was that I had.
The issue with wood pallets is that, while the majority are made more or less "local", there is always a possibility that a pallet could originally have come from anywhere in the world.
Every country has its own standards on how a pallet is made, and in some places, it is acceptable to treat pallets with some really nasty stuff.
Most pallets are stamped with an industry stamp that indicates the country of origin of the pallet and what sort of treatment the pallet went through.
In order to avoid exposure to anything nasty I need to ensure that the pallet had a treatment stamp of :
- HT (for heat-treated) and/or
- KD (for kiln dried) and/or
- DB (for Debarked).
Any pallet that carries only those markings are considered safe for use since they would likely not have been chemically treated.
Another thing to look out for on a pallet are signs that liquids had been spilled on them - since we have no way to really know what was spilled, it's usually safe to just avoid using that pallet.
Once I was determined that the pallets meant me no harm, I set about the task of dissembling them.
For the first few pallets, I started to disassemble them using the tools that I had at hand - a crowbar and a claw hammer.
Once I started into the first pallet I immediately noticed a few issues:
The cross-boards of the pallet tended to split very easily when I tried to pry them up with the crowbar - making the boards unusable. Using the hammer to knock the cross-boards off of the pallet's stringers had the same effect as the crowbar - a lot of splintered wood
My arm was starting to get really sore from all the hammering. Obviously I needed a better approach, so I went back to do some more research online.
During a search on Amazon, I came across a specialty tool called a pallet buster.
In essence, a pallet buster is just a special crowbar with a long handle to provide leverage with 2 prongs on the business end that are used to straddle the pallet's stringers and applies even lifting pressure to both side of the pallet cross-board (which in theory reduces the risk of splintering the wood).
A quick purchase on Amazon and a few days later I had my pallet buster.
The first thing that struck me was that at 18 pounds, it was a pretty heavily built contraption.
Now that I had the proper tool for the job, I started disassembling my first pallet.
The first (and toughest) step in the disassembly process was removing one of the end boards.
To work properly, the pallet buster needs to be able to straddle a pallet stringer. The issue that I found is that with some pallets, the spacing between the cross-boards can be fairly small, and I needed to carefully shoehorn the prongs of the pallet buster between the gaps in order to keep from potentially damaging the boards.
To remove the first board, I started by prying the board off of one of the outside stringers until the board was free. I then moved down to the center stringer of the pallet and pried the board off of that stringer.
Finally, I moved to the last outside stringer of the pallet and pried the cross-board until it was completely free of the pallet.
From this point on disassembling the pallet becomes much easier.
With the additional space on the stringers now being made available with the removal of the first cross board, removing the remaining cross-boards is done by first prying off the boards from the outside stringers of the pallet, prying the board from the center stringer as the last step.
When it came to the last cross-board, I did have to take it a little more carefully since the stringers were effectively flapping in the breeze since they were only attached to this last board.
This made removing the cross-board a bit tough to do.
In order to give the stringers some support during this final step in the removal process, I had to stand on the stringers to keep them in place (you need to be careful doing this since the stringers may tip over when you remove the cross-board - not a good thing to have to happen when you are standing on the stringer!)
At the end of the process, I had a collection of loose boards where a pallet once was.
While the boards were now taken apart, we were faced with a rather thorny issue.
Pallets are usually assembled with nails, which are now sticking out of the cross-boards and stringers that we have just disassembled.
Unfortunately, there really isn't any special tool to make nail removal easy, so I again resorted to the old standbys - a hammer and crowbar.
I use the hammer to knock back nails on the boards so that I can expose the nail heads enough to remove them with the crowbar.
Occasionally, especially if the pallet has been out in the elements a fair bit of time, I do encounter nails where their heads have disintegrated to the point that the crowbar isn't able to get a grip on them. In those situations, I used locking pliers to remove the nail.
Step 2: Making the Legs
My criteria for the workbench was pretty simple. It needed to be large and strong enough to hold any large pieces that I may be working on. It also needed to be at a height that would allow me to work without too much strain on my back.
I determined that a workbench with 4 feet by 5 feet working area set at a height of 3 feet would be the best fit for me.
From there I drew up some quick plans.
I first focused on building the legs of the workbench.
While I only had stringers to work with, I really needed to have the legs as thick as possible in order to give the workbench strength.
To accomplish this I decided to make each leg out of two stringers joined together in order to make a 4" X 4" leg.
First I cut out eight 3 foot lengths of a stringer.
Once I had the boards cut out I then assembled the 4" X 4" legs of the workbench by joining two of the stingers together with 2.5-inch deck screws.
Step 3: Building the Frame for the Top
Next I cut out three more 42-inch boards which will serve as the internal structure of the workbench's top.
With the parts cut out, I started assembling the framework by joining the 5-foot stringers against the ends of the 42-inch stringers, securing everything together with 2.5-inch deck screws and making sure that the corners of the frame were as square as possible.
Next, I took a 42-inch stringer and placed it flat along the bottom of the frame, so that I had a 1.5-inch gap between the top of the frame and the top of the stringer that I had just placed. This gap will be filled in by boards that will be used as the working surface of the workbench later on.
I centered the stringer in the middle of the frame and secured it in place with deck screws.
I then did the same with the remaining two 42 inch stringers, placing them roughly centered between the ends of the frame and the center stringer.
Finally, I cut out twelve 57 inch lengths from my remaining stringers, which will be used as the working surface of the workbench and two more 42 inch and 60-inch stinger which will be used as support braces for the workbench.
Step 4: Assembling the Workbench
I then gave all the parts a couple of coats of paint and transported everything to the new shop for final assembly.
To assemble the bench I first attached the legs to the top frame of the workbench by positioning the legs to the inside corners of the workbench frame and secured them in place with deck screws.
While I was attaching the legs I made sure that the top of the legs was flush to the top of the workbench frame and that the legs were as perpendicular as possible to the frame.
Next, I attached the 5 foot and 42-inch braces to the workbench legs with deck screws, positioning the braces approximately 1 foot off of the bottom of the legs.
Once the legs were installed, I then started to attach the work surface to the frame of the workbench.
There are a lot of options on what you can use as a work surface for the workbench (for example, a sheet of 3/4 inch plywood would work well), but in keeping with the idea of using pallets, I used the twelve 57 inch lengths of pallet stringers that I had cut out earlier.
I started installing the work surface by shortening 2 of the stringers to 49 inches and installed them between the legs that I had just attached to the workbench frame.
After that, I then laid down the remaining 10 stringers onto the workbench frame and secured them all in place with deck screws.
Once all the top stringers were secured in place, the workbench was complete.
Step 5: Finished!
I've been using the workbench now for a couple of months. So far I've been quite pleased on how well it has held up from all the punishment I've been putting it through during the course of building my projects (including other projects using wood from pallets).
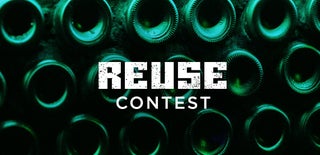
Participated in the
Reuse Contest