Introduction: Cascade Coffee Table With Hidden Compartment
I just moved from Maryland to Connecticut. My landlord and roommate in Maryland had a whole shed full of tools, and allowed (and encouraged!) me to make full use of his stash. When I decided to move, I panicked about loosing access to all of these tools, and the idea for one last hurrah surfaced in my mind.
I set to work in SketchUp to model the following coffee table. I planned to use pine 2" x 2" boards from Home Depot in varying lengths to make an end-grain coffee table with a level top but a random, low-res-stalactite-looking underside. I decided to obscure a compartment among the vertical pieces of wood, both to make the design lighter, and because extra storage is always nice. The lids to the compartment were designed to blend in with the over all look of the table so that it appears solid to people not in the know.
I did take some inspiration from this Mikasaurus Instructable (why am I always drawn to that guys's projects?): https://www.instructables.com/id/scrap-ends-table/
Update (6/23/15): Almost there! The extra layer of masonite is being glued to the lids as we speak. Then I just need to sand, finish, and figure out how to take some good photographs!
Step 1: Modeling and Planning
I chose to use Google's SketchUp for this project because the "push / pull" (extrusion) tool is pretty intuitive. Basically, I just created an array of 1.75" squares in my desired dimensions, then pulled the bottoms to the length I wanted. I was going for a random distribution, but kept all of my lengths to even inch increments between 3.75" up to 15.75". I also decided on a depth for my secret compartment of 10.75", and added it to the model to ensure that the outside boards completely hid it. I added 7" legs to the bottom of the box for a total height of 17.75" (I looked at a few tables from Ikea to decide on this height). I also added lengths of board under the box from 1" to 6" in even inch increments.
Next, I made a length map within illustrator. I decided to make this life-sized so that I could lay out the pieces as I cut and glued them. I also took a count of each length and made a cut list to follow. Then I headed to Kinko's to get two over-sized prints made of the schematic.
If you open the schematic, you will see that there are three boards with + marks and grey hatching. Since my compartment is secret, and I planned for the lids to be flush, I needed a way to raise the lids so that one could insert a finger. Originally, I was imagining a dowel-button. I brainstormed ways to do this with my father, and he suggested making the whole "button" on of the board segments. I decided to make three, one for each lid section, so that some lids could stay down while the compartment was accessed, and thus, things could stay on the table.
Step 2: Cutting and Gluing (and Jig-Making, Oh My!)
Shopping List
I bought several 6' sections of select pine 2" x 2"s. You will save some money if you buy 8' boards, but, I drive a Miata, and 6' is about the limit that I can hold steady while chopping a few inches off one side. I believe I used somewhere between 10 and 15 boards. I ended up foregoing most of the pieces I had modeled under the secret compartment to save on pine, let more light under the table, and keep the weight down (although the result is a more top-heavy table, but hey, I like to push limits). I also bought two 4' x 2' pieces of 1/2" MDF for the box and jibs, and I already had approximately a 4' x 2' piece of masonite to use for the lids. Finally, I got a big selection of hardware and one 3/8" dowel.
Hardware included ~40 #10 1-1/2" screws, 10 #10 3" screws, 11 threaded insert nuts and furniture bolts to go with them, and 4 cam connector sets.
Cutting
This part is pretty self explanatory. I started with my largest sized pieces and worked my way down. I like to use painters tape to mark a guide on the cop saw fence, so I can cut a whole group after only measuring once. I was intent on getting the perimeter pieces cut first, so I could start gluing them up. It may be possible to streamline the cutting process to cut down on waste wood—I did this on the fly, so maybe it wasn't the most efficient way. When I got towards the end of a board, I would measure it to see if it was long enough to contribute to the length set I was working on. If it was not, I examined whether I could get two smaller pieces from my list out of it. I kept the piles of cut pine in labeled bundles to make the layout step quicker.
Glue Up and Jig-Making
I realized I would need a jig or two to streamline the gluing process. The first jig was created to glue the outside (double) rows. I just made a simple, long box that was just wide enough to hold two boards together. I drilled 1-1/2" holes along the length for the head of my clamps (it turns out I wasted some time drilling a few holes my clamps were not long enough to reach, take note of this).
I unfurled my schematic on the shop floor and began to lay out my boards. I chose to arrange the end grain so that it made a kind of chevron pattern. I double checked the length of each piece, and chose the best orientation as I laid them out, then I re-checked both of these qualities as I glued pairs. I used wax paper to protect my jig from squeeze-out. I then glued sets of two pairs together. I did a couple sets of three pairs, but realized that I wanted to keep it to two pair, which was a workable size to even out with the chop saw.
The second jig I made was just two reference surfaces screwed together at a 90º angle. This jig was used to glue whole sides together. If I did it over again, I would probably add squares at the end to keep the 90º angle rigid.
Step 3: Box Construction
Building a box out of MDF is pretty easy, but remember, this box needed spaces for the lid-openers removed. This meant a bottom with some large notches and five side pieces. The nominal dimensions of the box are 22.5" x 12" x 10".
The box sides are only screwed together for now. I was not sure if I was going to have to disassemble it for my move.
Step 4: Lids
Using the chop saw, I cut many many many slices of pine to disguise the masonite lids. I chose the thickness by adding the masonite thickness to the box depth, and subtracting that length from the length of the shortest flanking board (see photo). I arranged the pieces, spread a layer of glue, laid them on (no good images of this, since I had to work fast!), and clamped a spare piece of masonite over the tiles while they set. Then, I sanded the edges to ensure a good fit.
The lids have a slight warp to them. At first, I was thinking about trying to sand them flat, but I was afraid that as they got thinner, they would warp more, and I'd be back to square one (get it?!). I decided to glue extra masonite to the bottom of the lid to stiffen them up some before sanding. This also has the added benefit of making a cheater rabbit joint around the lids.
Step 5: Assembly Part 1
Using the lid thickness to offset the compartment from the sides, I drilled 1/16" holes from the inside of the compartment, into the pine walls for three of the sides. I left the side where the lid-openers go for the moment, realizing that attaching a heavy pine wall exclusively to the two panels might stress their single joint. I drilled out the holes in the pine walls for threaded insert nuts, and drilled out the holes in the box walls for the matching bolts.
For the side that wasn't done yet, I decided to buy cam connectors—the fun little connectors frequently found on ikea furniture. They were kind of a pain to find in my new town (oh yeah, I didn't finish before the move, but it meant I got to buy my very own 20v DeWalt drill!). I got the female parts at Home Depot and found the bolts at Lowe's. This was after visiting Home Depot and two neighborhood hardware stores to find the insert nuts and bolts. Sheesh.
Step 6: Assembly Part 2: Opening Mechanism
The boards used to raise the lid are simply held in place by a combination of dowels driven into the pine wall they but up to and notches in the compartment. The movable boards are slotted so that they are free to slide upwards on the dowels, and are kept on track by the compartment.
Step 7: Assembly Part 3: Cam Connectors
Working with cam connectors is tricky. You have to get 3 measurements to simultaneously line up. Often, these sets are metric, but luckily, they seem to pick measurements that convert well.
My trick was to make a sort of paper jig, and I think I still had issues with the drill walking.
I will finish this section tomorrow, my photos aren't loading.
Step 8: Assembly Part 4: It All Comes Together
So, apparently the charger for that new drill is defective. Hopefully Home Depot will give me an exchange tomorrow, I am so close to finishing!
Edit: I exchanged the drill. Hopefully this photo sequence of the assembly is helpful. The lids still need some sanding, and to have the bottom layer glued on to reduce the warp, but you get the idea. More tomorrow!
Step 9: Sanding
Read some tips about sanding end grain, blah blah blah.
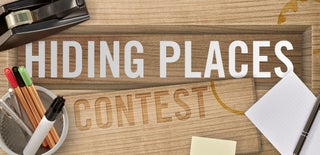
Participated in the
Hiding Places Contest