Introduction: Cast Iron Kettle Fire Pit
So I decided to tackle this project because I love to do anything DIY if I feel I have the skills and because I think it's always way more cool if you can say you made something yourself. I mean, how much pride do you get by telling your friends, "Yeah, I picked up this fine piece of China from Wal-Mart." So this is how I made my own fire pit, I hope you enjoy. I feel I should also say that some of the steps later on in the project got a little sketchy so I'm telling you now, do as I say, not as I did. Something could go wrong and you could get hurt.
Step 1: Compile Materials
So to begin of course you need to find something to contain your fire in. I was able to find an antique cast iron sugar kettle at a local farm auction. I felt a little guilty spending $150 dollars on it, but later doing some research, I found that they can go for several times more than that, so I felt a lot better. Some fire pits are actual pits that are in the ground. It makes sense. I however, wanted to have mine suspended from legs. I found some great spring harrow tines that came with the chisel points at a nearby farm equipment salvage business for $7.50 each. I scrounged up the steel pulleys out of a junk pile I have on my farm and the steel used to make the brackets for the pulleys was also sourced from a pile of scrap. The wooden wagon wheels were actually given to me by a friend of mine I go to church with. That pretty well sums up the materials I used for this project aside from two bolts and nuts that I used to hold the pulleys into their brackets.
Step 2: Tools Needed
I apologize for not taking any pictures of the tools that I used, I was more caught up in documenting my progress rather than my processes. For a project like this you will really need to have a fairly well equipped shop of metal working tools. Basic hand tools like hammers, adjustable wrenches, and hack saws unfortunately will not get you through this kind of work. The tools that I used for this...
- Oxygen/Acetylene cutting torch
- Welder (Oxy/Ace could be used but electric welding is much cheaper)
- Angle Grinder (I used both 4 1/2" and 9")
- Electric Drill and/or a Drill Press
- Cable Puller
- Adjustable Wrench
- Black Smith Hammer
- C Clamps
- Square
- Tape Measure
Step 3: Hanging the Kettle
On the rim of the kettle there were two pegs that are used to hang the kettle over a fire. I decided to use these pegs to suspend the kettle from the frame and legs assembly. This is a simple way of hanging the kettle and allows it to swing slightly inside the frame. The pulleys that I salvaged fit nicely under the pegs and the only problem was getting them to hold securely to the legs for the frame. I started with 1/4" plate steel and traced out a shape onto the steel and cut it out with the Oxy/Ace torch. I ground the edges smooth and then used that piece as a stencil to cut out three more. I used a drill press to drill a hole in each of the plates where a cross bolt would go between two pieces and through the pulley. All four plates were lined up and bolted together then I ground all the edges smooth so that the four pieces were identical. Two back plates were cut and welded in between the side plates. The two assemblies were then welded onto two of the harrow tines to be used as legs.
Step 4: Sizing the Wheel
In the introduction I mentioned how some of this project got a little sketchy and even a little dangerous, well this is it. The wagon wheels that were given to me ended up being too small. It was really my own fault because when I contacted my friend who had posted them along with other old wagon parts for sale on Facebook, I asked if he had any 45" rims. He did and he just let me have them. Later trying to make the harrow tines (legs) fit between the kettle and the wheel I realized I'd asked for the wrong size. I actually needed a 49" rim. I did not panic though since I'd gotten two old wheels. I figured that I could just cut a section out of one wheel and splice it into the other. That's when things got tricky and where I say to anyone wanting to do something like this, take your time and find a properly sized ring of some sort because it's not very easy trying to just splice in a section from one rim into another. So like I said in the introduction, do as I say, and not as I did; but since I did it I'll try to explain it.
Using a little geometry I calculated that I needed to squeeze in almost 19" into the rim in order to make it the right diameter. That was way more than I expected and at this point I did panic a little bit, but I decided to keep going. I welded one end of the 19" section to a cut end of the first rime. Then began the sketchy part. Trying to open up the first rim 19" was a real chore because the rims once cut actually collapsed instead of springing open. I tried using jacks which became out of line and unstable and the whole contraption violently collapsed several times. Finally I secured the wheel rim to a heavy farm implement frame and welded a hook onto the wheel rim, then used a cable puller to stretch open the rim. Voila! I clamped another piece of the donor rim to keep the welds and the first wheel rim in line rather than having a kink where the two ends of the rims met. You can see the kink that had to be straightened out in one of the pictures above. This alone took and entire afternoon. and was by far the most laborious part of the project.
Step 5: Attaching the Legs
After the fiasco with the wrong size of rim the rest was smooth sailing. All that was left was to weld the legs onto the now properly sized wheel rim. The best I could do was eyeball straight out from the hanging pegs on the kettle and mark with a soap stone where the legs with the pulleys would be placed. I decided that the top of the wheel rim would look nice if it were level with the top of the bracket holding the pulley. With a small square I marked a line even with the top of the pulley bracket. Then I just went back with some more geometry, figuring the circumference of the rim and dividing that by four to determine where the last two legs would be attached. I measured around the rim 1/4 of the circumference either direction from the two legs with the pulleys and finished welding the last two legs into position.
Step 6: Finish Assembly
Finally at the end of the project. Something that I've been wanting to build for years. All that was left to do is set the kettle in place in the frame. Here I recommend having a buddy help with the heavy lifting. I estimate my kettle to weigh in the neighborhood of 150 lbs., or in my case I used some chains and the loader on my utility tractor to lift into place. Just make sure and line up the pegs on the kettle into the pulleys and you're all done and ready to start a fire, have a beer, and hang out with some friends.
Thank you for reading!
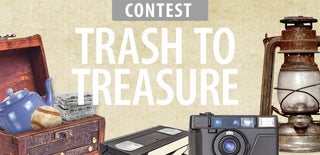
Participated in the
Trash to Treasure Contest 2017
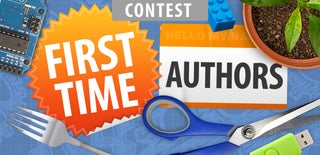
Participated in the
First Time Authors Contest 2016