Introduction: Casting Your Own Skull Table Top S'more Firepit
I love S’mores. They make me happy. Especially when they’re made over a campfire in the middle of the woods on a camping trip. Mmm, those taste the best! Second best is over a bbq following a huge hamburger or rib roast. Also delicious!
Of course, the craving for a S’more can strike at any time, and should you find yourself with no campfire available and unable to procure a bbq, this simple Instructable will show you how to make your own tabletop version that you can fire up any time of the year.
Step 1: Let's Get Moldy!
The first thing we’re going to need to do is to make a mold of a skull. This skull mold will be used with plaster-of-Paris and non-food grade latex and should NOT be used for molding food products.
For this project, we are going to be making a latex mold. Latex is relatively easy to find year-round (you can get the stuff I’m using at Michael’s for fairly cheap. Download their app and use the 40% off coupon they always seem to be offering!)
Once you’re done with this project, save your mold. You can use it again and again and again to make as many plaster skulls as your dark little heart desires (a great thing if you’re building an ossuary or planning on doing some serious home haunting for Halloween). You can also use it to make resin skulls (but I suggest using a mold release spray).
Because latex is flexible, we will also be making a “mother mold” (a hard, rigid shell) to help hold the shape of your skull as the plaster hardens.
To make your latex mold you will need:
- 1 plastic skull
- 1 jar mold builder
- 1 foam brush
- Small amount of non-oil based clay
- 2 rolls of plaster-soaked cloth
- vaseline
Step 2: Sealing Up the Skull Holes
Before we begin making your mold, we need to prep your skull. My favorite skulls to use for molding are the cheap hard hollow plastic ones you can pick up for half off after Halloween. Make sure the material your skull is made of isn’t porous (this includes some plastics, clay, other plaster skulls, wood, and all actual bone). If it is porous, be sure to seal it first with a layer or two of clear coat.
If your skull has any oil-based weathering, make sure to scrub it off as it will affect the way the latex cures.
If your skull has any details that include gaps, sharp undercuts or holes, those will need to be filled with clay. If you have holes inside your eyes for optic nerves, large gaps between your teeth, or holes within the nasal cavity, fill those with oil-free clay like Sculpy or even play-dough. You also want to make sure you fill the zygomatic arch gap as well (see photo above).
Step 3: Layering Your Latex
Once all your undercuts and holes are properly filled, brush a thin layer of latex over your entire mold, leaving only the bottom bare. Allow it to dry before adding your next layer. You’ll be able to see it drying. As latex dries, it turns from a thick white to a pale clear-ish yellow.
Continue adding layers, letting them dry before applying the next until you have between 5 and 7 thick latex layers.
Once you've got all your latex onto your skull and it's fully dry, let's move onto the next step.
Step 4: Mother Mold Making
Let's make the mother mold!
A mother mold is a hard shell that we’ll build around your latex mold which will help to keep it from warping as you mold your skull. Build your mother mold like you would an oyster shell, with your skull in the middle like a pearl.
Take your now dry, latex covered skull and drape it with lightly dampened plaster cloth over just one half. I’m partial to starting on the right side (as you face the skull). Don’t worry about getting the plaster into the nasal cavity or eye sockets, just skim right over those.
Continue adding plaster-soaked cloth to your latex mold until you build up about 3-4 layers. Set your skull aside to dry.
Once all of the plaster cloth on the first half of your skull is dry, smear a bit of vaseline over the center split point and then apply plaster to the second half of your skull, overlapping slightly along the split (the vaseline keeps the plaster from sticking together), again doing about 3-4 layers.
Allow all your plaster cloth to fully dry.
Once all your plaster cloth is dry, carefully peel the two halves of your mother mold apart, revealing your latex covered skull in the center.
Before we start casting our fire skull, we'll need to pull our original skull out of our latex mold. To remove your original skull (and all subsequent plaster skulls), simply roll the edge of your latex down over the back of your skull and peel it off. As you roll it forward, it will turn inside out. Pop your skull out and then simply turn the mold right side back in. Congratulations, you now have a latex and plaster mold of a skull.
Now that we have both the latex mold and the mother mold, it's time to make our fire pit!
Step 5:
For this you will need
- cool water
- plaster-of-Paris
- Mixing tub
- Mixing tool (I use an old spatula)
- Your latex skull mold
- Your mother mold
- binder clips
- bungee cord
- can of S'mores Sterno
Place your latex mold inside your mother mold and secure the two sides of your mother mold together using your bungee cord.
Clip your latex mold to the edges of your mother mold to help keep it secure and prevent it from drooping from the weight of the plaster we'll be pouring in.
For this process, we'll be doing what's called "rotational casting," filling our mold partially full of plaster and then sloshing it around inside to create a hollow shell and then repeating the process again to help thicken the plaster shell. This creates a lightweight hollow skull that will be easier to work with when we move onto prepping the skull to install our Sterno can.
To start, you want a cup or so of liquid plaster. Mix your plaster according to the manufacturer’s directions. Be aware that the temperature of your water, as well as the ambient temperature of the space you’re working in, will greatly affect your curing time. Cool water and cool temperatures will slow down your cure. Hot water and hot temperatures will speed them up. Adjust accordingly.
Step 6: You Spin Me Right Round Baby, Right Round
Pour your mixed liquid plaster into your skull and start immediately turning your skull mold around and around, making sure to slosh your liquid plaster all around the inside of your skull.
In the series of photos below, you can see the first cup of plaster I mixed has been poured into my mold and I am rotating it in a clockwise rotation, making sure to fully coat the sides and top of my mold.
As you rotate your mold and the plaster thickens, it will eventually turn to a sludge and stop sliding along the inside of your mold. I like to turn it so the puddle settles into the front of the skull, building up the teeth, nasal and orbital cavities first.
Add at least two to three more layers of plaster, a cup at a time, and continue rotationally casting your mold. Just like you did with your slush puddle settling at the front of the skull, allow your subsequent slush puddles from pour 2 and 3 to settle on first one side and then the other and finally use layer 4 to settle at the back of the skull.
While it’s important to get a good layer all around the edges of your mold, don’t worry too much about building up a thick layer at the crown of your skull. You'll want that thinner anyway as we're going to carve it out later on.
Once your three to four layers have fully hardened (I like to wait about 20 minutes after the last layer has set), release your mother mold and peel off your latex.
Congratulations, you have your first plaster skull!
Move immediately onto the next steps while your skull is still damp and soft. If you wait too long, you’ll still be able to do the rest of the project, but it’ll be a whole lot harder and a whole lot messier as your plaster will be fully cured and much tougher to cut through.
Step 7: Carving Out Your Sterno Hole
Now, I’m a little particular about how I like my skulls…specifically, I’m not a huge fan of the lower jaw. Don’t ask me why, just always been that way, which is why when I poured this skull, I intentionally left the lower jaw thin and brittle. Because the plaster is still damp, and therefore soft, it’s simple to snap that extra material off.
Test your skull out for balance and make sure it’s steady. If it’s not, a few quick swipes over a rough surface like a cement sidewalk or a bit of sandpaper will sand down the bottom until it sits flush. The last thing you want this thing to be is wobbly, especially when it's on fire later on.
Once it's fully balanced, take your Sterno can and place it at the top center of your skull. Using a sharp nail, trace a circle around the can into your still damp skull.
Using any relatively sharp tool you can find (screwdriver, butter knife, pocket knife, etc.) start scooping out the hole where your Sterno can will sit. It might take a bit of time, depending on how thick the parts of your skull are, but eventually, you should be able to break through to the hollow center of your skull.
Periodically put your Sterno can into the hole you’re carving to check for size and adjust as needed.
As you can see with my Sterno can, it has a small collar around the top of it that includes four small flanges to keep the can from dropping through the center of my skull. The Sterno can I’m using is specifically made for cooking S’mores and came with that collar. If you are going to use your hellfire pit purely for decoration and don’t care what sort of Sterno can you’re using and yours doesn’t have that flanged wire collar, I would recommend adding a similar collar using a few twists of medium gauge wire.
Place your finished skull somewhere warm and allow to dry for at least 24-48 hours.
Now it’s time to move onto decorating.
Step 8: Painting and Personalizing
I like to give my skulls a wash of brown acrylic followed by a wipedown with a wet rag. This leaves the skull grungy and distressed looking. Ultimately, how you decorate your skull is up to you. Have fun with it! There’s no right or wrong way to do it.
Allow your skull another 24-48 hours to dry.
Now that is a good looking skull!
ONTO THE S'MORE MAKING!
Step 9: LET'S MAKE SOME S'MORES!
- Your molded tabletop skull fire pit
- can of S'mores Sterno*
- Lighter or matches
- Marshmallows
- Graham crackers
- Chocolate bar
- Marshmallow roasting stick or skewer
Drop your Sterno can into your tabletop skull and ignite. Roast your marshmallows just like you'd do over any other fire source and enjoy!
So there you have it, your own hellfire pit. Because it’s small, it’s the perfect size for the middle of a table. Just make sure you practice good fire safety. These cans can get hot, so be careful as you handle them. The plaster will act as an insulator meaning the sides of your skull will remain cool to the touch even with the can lit, but still be careful. Make sure you have plenty of clearance above the can and never light it in an enclosed space.
To help keep your tabletop skull fire pit burning for many years to come, consider giving it a coat or two of clear sealer to help protect it and store it in a cool dry place when not in use. As it is plaster it will eventually break down and degrade if left in a damp environment without a sealer.
Alternately, you can do this exact same Instructables process using heat resistant fireplace cement, but be prepared, that stuff dries much harder and will either require the right tools to drill out the center hole for your Sterno can or you will have to mold the indentation into the skull from the beginning.
If you want even more unique and strange recipes, swing by my main Instructables page or check out my horror themed food blog, The Necro Nom-nom-nomicon.
Bone appetite!
*The Sterno can I'm using is specifically created for S'mores. You can purchase these on Amazon.com. If you can't find the S'mores specific Sterno cans, make sure the can you use is made with "ethanol" which will burn clean. Older Sterno cans and some off brand cans contain "methanol" and are not safe for direct food heating and should not be used. If in doubt, don't use it before clearing it with the manufacturer.
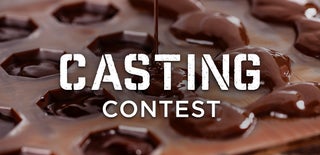
Runner Up in the
Casting Contest