Introduction: Celtic Dagger From a Vintage File
This Celtic dagger is made from a repurposed vintage file that I had lying around my shed. It's crafted using only a 1" belt sander and a Dremel. No forging, annealing, or hardening are needed.
For shaping the dagger, you will need:
- An old file
- A 1 inch belt sander
- Safety gear (eye protection, work gloves)
- A grounding strap (to reduce static shocks)
For acid etching, you will need:
- Muriatic acid
- Hydrogen peroxide
- Metallic sharpie
- Electrical tape (optional)
- A cool design
- Nitrile gloves
- Eye protection
- A plastic container
- Buckets of water
- Fine grit wet-dry sandpaper
For finishing, you need
- Some wood for the handle and scabbard
- A Dremel rotary tool
- Two part epoxy
- leather stripping
- Clear polyurethane
Step 1: Smooth and Shape Your File
This is my first knife. I started this project with a vintage Bell Systems file. I decided on this one because the full handle makes for a nice, thick tang. I've heard modern files are only hardened on the outside, so be careful. If the sparks coming off the file change, you are probably hitting soft metal.
Anyway, put on your protective gear. Attach your grounding strap to something metal, and to yourself. I didn't use one, and got shocks in my hands about 3 second apart the entire time. Not dangerous, but gets old really fast.
Using the 1" belt sander, begin removing the file teeth and shaping the blade. This will take a while. The file is hardened steel.
Take care shaping the cutting edges. You want to get them close to sharpened, but don't go too far or you'll be removing more metal to straighten any dips along the edge.
You should also shape the tang at this stage, so it's narrower than the base of the blade. I shaped the tang later in the process (look for that picture in the guard and handle steps), and marred my etched design in one spot.
Step 2: The Tang and Guard
I wanted to put a brass guard on this, to I purchased some solid brass line cleats from a local boat store. You need to remove the brass between the screw holes to make a slot.
Once you have your slot, start grinding the tang so that it fits into the slot. I got the guard to slide just over the base of the blade.
If you don't like the size of the cleat/guard, grind it down to the look you want. Brass is very soft, so go careful here. Use a fine grit belt to polish it up.
If the guard moves around against the blade too much, continue to the acid etching step, and secure it with J B Quick Weld when attaching the handle.
Step 3: Acid Etching Your Design
Put your design to paper. I chose a style of Celtic braid so it could follow the blade. You will need to transfer it, or freehand it. Regular pencil will show up on the metal.
Put the mirror image on the reverse side. The metallic sharpie and electrical tape block the acid from reaching the metal, so you are going to basically create a negative image of the finished design.
Note: On my bearded Viking Axe, I used nail polish to lay out the design. I tried metallic sharpie here, as I thought it would be much easier. But I didn't think that the acid would eat the metal in the metallic sharpie. The result is much better than I would have hoped.
Paint the parts you want to stay shiny with the sharpie. Cover the blade edges and tang with electrical tape.
Put on your eye protection and Nitrile gloves. In a WELL VENTILATED AREA, pour your one part muriatic acid (e.g., 1 pint) into your plastic container. I used a plastic paint roller tray.
Add 2 parts (1 quart) hydrogen peroxide. Don't add acid to peroxide. I hear bad things happen if you do this backwards.
Carefully place the blade into the bath. The longer you leave it, the more defined the etch will be. I left mine for around 3 hours. Once it's done, rinse thoroughly. Use 300 grit wet-dry sandpaper (under water) to GENTLY remove the remaining sharpie.
Step 4: Handle and Scabbard
I chose walnut for my knife, as I like the natural color when it's wet.
Cut your wood into suitable sizes for the handle and scabbard. Trace out your tang with the guard in place, and blade without the guard. You will need to sand a spot for the guard to sit in later.
Start Dremeling to half the thickness of the tang, and a little more than half thickness of the blade. Test fit them often until the wind meets without gaps. The scabbard should allow the blade to be drawn and inserted smoothly. Make sure there is extra room for the point to go into, as you still need to sand things down.
Once your fit is good, fit the guard to the blade, fill both sides of the handle with epoxy, and clamp tightly, pointing up. If there is space between the guard and blade, fill that with a little J. B. Quick Weld.
For the scabbard, put a thin line of epoxy just on the mating surfaces and clamp, point side up, until set. You don't want epoxy setting up on the inside, as this will block the blade.
Once the epoxy is set, sand the wood to the shape touch want. On the scabbard, sand or Dremel grooves for the guard to settle into. Use progressively finer grit to smooth things out.
Step 5: Detailing and Finishing
Add some embellishments to your dagger. I used 4mm leather stripping, and an old dirk frog (basically just a leather loop). Once it's to your liking, finish with polyurethane to protect it, and keep all the leather secure.
Your dagger is done, you can sharpen it to a pretty fine edge, if you are so inclined. Remember to check your local laws as to length of knives you can carry with you.
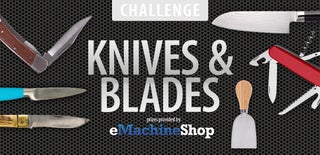
Participated in the
Knives and Blades Challenge