Introduction: Concrete Lighting
Concrete is a really cool material to work with and it is not very complicated if you are well prepared.
Design:
- I designed the light in SketchUp. This way it gives you a great idea of how it looks in 3D. It is important that it is possible to get the shape out of the mold you make. So the more advanced a your design, the harder it can be to get it out of the mold undamaged. Also, think about the weight. You want to use as little concrete as possible, but the thinner you go, the harder it is to make the mold. I would not suggest going under 1-1/2" in wall thickness.
- I printed the drawing out with measurements and got started on making the mold from plywood and 2x4's.
The mold was made so almost all parts and sides could be taken apart.
Varnish/lacquer:
- Then all the parts were given a few thick coats of varnish/lacquer. This gives a smooth surface that can handle the water and one that will protect the mold.
Wiring and Inner mold:
It is important to plan for the wiring.
There are several ways of running the wire and below, I try to explain various ways which can be combined to suit your design. For this lamp design, I have done it two different ways. The first time, I used 2" PVC pipe from the bulb area leading into a 6" pipe for the main cavity area. The second time, I used Styrofoam from bulb area leading into a tapered Cardboard box which is explained below. Using the Cardboard box, I was able to create a larger cavity and use a little less concrete, but both ways worked fine.
Styrofoam: You can use Styrofoam in places where you want the cavities. Cut the Styrofoam to the shape you need to feed the wire and install the bulb. Where needed, the Styrofoam can be hot-melt glued to the mold to hold it in place, as it will break free easily once the concrete has cured. However in some areas, you have to put the Styrofoam in as you pour in the concrete and hold it down so it stays in place. You also have to keep in mind that you have to pick the Styrofoam piece by piece to get it out which can take some time or use Acetone as suggested in comments.
Inner mold: (see photo #8) You can make an inner mold to make the lamp more hollow and weigh less. However it is challenging to make an even wall thickness and going under 1-1/2" might be risky. Working with both an inner and outer mold is more demanding and probably not something you want to try the very first time.
The ideal shape for an inner mold is tapered, so it is possible to pull it out once the concrete has cured. A simple way to do it, is to make one from Cardboard and cover it with duct-tape. Because of the low weight the concrete will push the Cardboard box up as you fill the mold with concrete. It is therefore a good idea to put a contractor bag inside the box and gradually fill it with sand as you pour the concrete. This way the box will stay in place. Keep in mind where you want the passages inside the lamp. The inner mold box needs to touch your conduit or Styrofoam pieces that leads to the bulb.
PVC: You can use PVC pipe as conduit for the wire and cast around the pipe. This is an easy way to do it, but it depends on the design. Also keep in mind that you will more than likely not be able to get the PVC out again.
Cast wire: The easiest way to do it is to cast the wire into the concrete. You will not be able to change the wire, but it is pretty well protected. Again, it's a matter of preference, design and weight.
Mold prep-release:
Before you pour concrete you need to coat all the mold sides. You can use pretty much any type of oil.
Concrete and pouring:
-I have used Sakrete and QuikCrete with equal results. For my light, I used about 1 x 80lbs bag. A cement mixer is really convenient and it allows you to get the right consistency. You want the mix to be medium, not too wet and not too dry. It all depends on how advanced the mold is. the more complicated the wetter you want it.
- Make sure to go slow when you start to pour the concrete. Use a small bucket or similar. Use your hands to tap and move the concrete around to make sure it gets all the way out in the corners. Also, if you need to use Styrofoam, make sure it stays in the place you want it to when you pour.
-As you work your way up with the concrete use a Oscillating sander or similar, to vibrate the concrete. The vibration makes the concrete move and helps filling in voids/air pockets that might be trapped. You might notice that the concrete sinks a bit, which is a sign that a void was filled up.
-When the mold is filled up, put a piece of plastic to cover it up for a day. You want the concrete to cure slowly, the stronger it gets. I usually try to leave the mold on for 2-3 days before trying to take it off.
De-molding:
-It is exciting, but go slow. Try to start with the simplest sides first. Back sides or flat surface sides. This will give you an idea of how the concrete has cured. Maybe you need to let it cure a bit longer. It will be easy to tell.
- Some sides might need some more force, so have a rubber mallet handy and tap lightly to get the sides to release.
- The Styrofoam can be taken out by breaking it apart using a screwdriver or similar. If you are adventurous you might be able to burn it.
- The concrete is still wet, so you can let it dry some more or get started on installing a bulb or run the wiring.
Good luck!
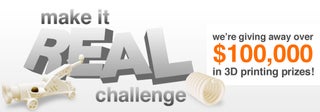
Participated in the
Make It Real Challenge