Introduction: Custom Car Bubble Top
One of my bucket list projects has always been to build a reproduction of Ed Roth's magnificent Mysterion show car. To make a short story long, he built it in 1962, showed it for a couple years, sold it to fellow custom car guy Ray Farhner in about 1966. Ray showed it for a year or so but the car was so poorly built the frame kept breaking just hauling on a trailer to shows. It was mercifully destroyed in 1967, never to be seen again. Revell made a model kit of the car and Mattel made a Hot Wheels version. It is undoubtedly the least documented, most famous car of the golden era of car customizing. Above is the magazine cover that made me fall in love with the car and the second photo is of the reproduction I built, finishing it in 2016. I even wrote a book about the car and my project!
This instructable is on how a bubble top is made for one of these show cars.
Step 1: Designing the Top
Of course the first step is to design the top. There is very little information in the literature on the car. Fortunately Revell produed a plastic model kit of the car. Under close scrutiny, the model is not very accurate in key details but it is a very good reference for scaling major parts of the car. It is an accurate 1/25th scale. The top base outline is very accurate from my investigation so I used it to draw that shape. I did scrounge some very useful photos of the real car. The photo above shows how I was able to get a very accurate profile design by extracting a couple key dimensions from the model kit, transfer those to the photograph, then scale the rest of the critical dimensions.
Step 2:
Using my full size design, I built the pattern for the top shown in the first two photos above. It was built from common plywood and 2x4s from the lumber store. This is all that is needed to make the top! The bottom outer rim of the top is cut into a 3/4" plywood sheet. Then a strong 2x4 cage is build over that hole. I stress strong; it must be able to absorb a ton or so pressure and not deform. All the plywood edges that touch plastic were rounded over with a 1/2" radius router and sanded smooth. This is all that was required to yield an optically clear transition.
With this pattern, I had to find a company that could use it to literally blow the bubble top. I found such a company in Los Angeles that specializes in blowing plastic bubbles for scientific uses, for advertising signs, etc. They are only about an hour and half drive from my home so I threw my pattern in my pickup and headed down there.
The manufacturing process is really pretty simple if you have the proper tools. All you need is an oven to heat a 6' square sheet of Plexiglass to 350F and a 20 ton press that can accommodate said 6' square sheet. I jest of course. You have to find a company that specializes in this product. To make the top, the company heated a sheet of 1/4" thick Plexiglass in one of their several dedicated ovens. The plastic softens to the perfect rubbery consistency in a narrow temperature range of 240F to 255F. Too cool and the bubble won't blow, too hot and the plastic is damaged. They then manually took the sheet out of the oven which was now like a sheet of rubber. They moved fairly quickly because there is a window of about a minute before the plastic cools below the workable temperature. The plastic was placed on the bed of a big hydraulic press and they lowered the press which has a 1" thick steel plate which in turn presses down on my pattern, sandwiching the plastic between the pattern and the press bed. The final step is to literally blow the bubble in the soft plastic with compressed air until it reaches the proper tallness, then wait a few second for it to solidify into the final shape. I had two tops blown just in case I damaged one in building my project. I needed both it turned out. Be sue to ask the operator to blow the part quickly. If done too slow, the plastic is cooling and becoming more rigid and that induces stresses in the stretched plastic that will cause headaches in using the final product.
Note the bed of the press is white. This is a cloth covering that serves to protect the soft plastic but more importantly it spreads out the air stream that is injected under the plastic to blow it up. Without this diffusion layer, the air jet can prematurely cool the first spot of plastic it encounters and distort the top.
That's it. I threw the mold and two top bubbles in my pickup and headed home.
Step 3:
First photo above shows the two tops on my shop floor. They came out perfect. I then had to modify the top to fit the rim of the car I was building. The second photo show how I cut the bottom rim to shape to fit the fiberglass body rim. An air or electric cutoff saw with a thin, grit blade does a great job. The problem is any cutting method leaves a rough edge which has deep scratches. These scratches if not removed will initiate cracks that will ruin the plastic bubble. Plexiglass is very strong IF it doesn't have any defects on its edges. It is used as windows in jet aircraft as testimony to its strength. There is a very simple trick to sealing the edges of Plexiglass to remove these stress risers. I first removed the deepest scratches by sanding the edge with 100grit sandpaper. Then here is the trick; just play the flame of a propane torch along the edge. The plastic instantly melts to a polished surface eliminating the problem. Practice on some scrap plastic because applying too much heat will distort the bubble and ruin the plastic. You will be amazed how little time is needed for the flame to perfect the edge. The flame itself does the work, it only has to contact the plastic for a fraction of a second. You can move so fast, there is no danger of damaging the plastic.
WARNING: DO NOT use ANY solvents on the plastic after it is blown. There are internal stresses induced into the plastic as it is stretched to shape. The cooler the plastic while stretching, the more stress induced. These internal stresses are released if the plastic is contacted by solvents (lacquer thinner, polyester fiberglass resin, etc.) and the surface will craze with a maze of micro-cracks. This phenomenon does not happen in flat sheets of Plexiglass which are passivated with no internal stresses.
The final three photos show my top mounted in its car rim, then a photo of it tinted with catalyzed urethane clear paint to achieve the look of the original. Luckily the solvents used in the paint did not attack the plastic. I was lucky. The top was glued to the rim using urethane adhesive from the home center in the final photo. The top has a layer of masking tape to protect it during car construction. Use a compound leverage glue gun on this stuff since a standard cheapie glue gun doesn't have the power to squeeze this viscous compound out of the tube.
The rubber rim shown in the photos was a half-round 1 1/8" shape I found on the internet. It was glued to the top with Super-Glue which welded it permanently.
Step 4:
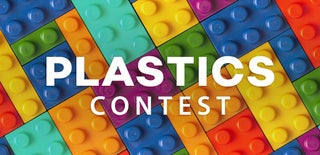
Participated in the
Plastics Contest