Introduction: Custom Stamp With Brass Inlay
Ever since I got into making I've wanted my own stamp. My first attempts included cork, potato and wood. These didn't satisfy me; they were either too hard to use or just plain ineffective. So, in this Instructable I aim to show you how to make your own laser-cut or handmade stamps with wooden handles and brass inlays. Another issue is that I have no lathe. All good tool handles seem to be turned, and yet I could see no way of buying a lathe, so I modified my pillar drill/drill press to allow light wood or metal turning.
I don't claim to know everything about this process, so feel free to experiment, whilst keeping safety in mind!
Always read text in red as it is a safety warning!
Step 1: Gathering Materials and Tools:
For this project you will need some basic materials, I wanted to make it as simple as possible to allow anyone to attempt it,
You will need:
1. Some scrap hardwood, I used some wood from an old windowsill.
2. A thin brass rod, I purchased this from my local Diy store.
3. Brass plates, thick and thin, I had these lying around but I'm sure you'd find some at any scrap merchant.
4. Threaded rod, this can be found at any Diy store
5. Some scrap brass or metal, you probably have something lying around, if not any junk shop will have something.
6. you will also need some adhesive backed foam sheets. You should be able to buy these from any craft store
As well as these materials you'll need some basic tools. I used a laser cutter to engrave my stamp, but you should easily be able to cut yours manually.
Tools you will need:
1. Pillar drill/Drill press, make sure that this is sturdy enough to turn wood.
2. A hacksaw and other basic tools.
3. Some sort of sturdy vice, I used an industrial vice but a lighter one would be fine.
4. Sandpaper and files; for most of the project I used 400 grit paper, and some basic metal files.
5. Some sort of strong glue, superglue should do fine.
6. Scalpel (If you don't happen to have access to a laser cutter)
7. And finally you will need some laser compatible vinyl sheets (if you are laser cutting) or some lino if you are using a knife to make the design.
Step 2: Designing:
The first step in building anything is to have a design. The following instructions will show you how to plan and cut out the embossed part of the stamp.
If you don't have a laser, try and keep the shape as simple as possible so as to keep the cutting easy and uncomplicated.
* Start up your cad software, anything like 2D design, illustrator, InkScape will do. These will all work but I recommend Inkscape as it is free and very easy to use.
Draw out a simple pattern in your software, remembering that the coloured parts of the design will be engraved, so the final file will be a negative. Also remember to mirror your image horizontally.
Export this design as a Dxf file and load it up in your lasers software
Step 3: Cutting and Cleaning:
There is no defined setting for cutting vinyl on lasers, so you are going to have to play about with the settings. Though I suggest that you set the cut path to repeat multiple times with lower power, this stops the cutting from being so violent. (I used a 70W machine with the settings: cuts-peed, cut-power = 25, 60 engrave-speed, engrave-power = 100, 60)
After cutting, wash off the dust that will be left behind and put the pad aside for later in the build process.
*Note* I reversed these images to show the design better *Note*
Step 4: Centring the Wood
To turn the wood we need to firstly mark a centre and insert a mounting point.
mark the centre on the wood on both the top and bottom. In case you are unfamiliar with how to do this, just draw lines connecting opposite corners of the wood. The centre is where the lines cross.
Drill out the centre and insert a screw. This will allow us to crudely mount the wood for milling. (I know this is not the best way, but if you are sensible and careful, it's perfectly safe.)
Be sure that the screw is at least 2 inches long. We don't want the workpiece flying off the drill.
* Using a simple wood chisel chop off the corners and sand down any sharp edges. This is an important step as it will make your job a whole lot easier when turning the piece.
Step 5: Rounding the Wood
Before we turn the wood we need to do some simple modifications to the it so that the milling process will go smoothly without any hitches. Because we aren't using a proper lathe we need to take into account that the drill is not designed for strong lateral forces. To counter this we are going to round off the edges of the wood.
Using a simple wood chisel chop off the corners and sand down any sharp edges. This is an important step as it will make your job a whole lot easier when turning the piece
Step 6: Making a Lathe Jig:
We need to turn our pillar drills into lathes, this is a really simple process and shouldn't take more than a minute
We need to set up a makeshift tailstock. This should reduce wobble on the workpiece and make the whole thing a whole lot safer: To do this I simply clamped a centre punch into a small vice on the work platform.
Now we can tension the press. do this by linking bungee cord over the feed handle and hooking it to something under the workbench. This will pull the workpiece down and keep it pressed up against the tailstock.
Now you can mount the wood in the chucks; open them up fully and slide the screw up past the jaws. Tighten it whilst making sure that it is not off centre.
Step 7: RounDing Off the Wood:
Now we get to the fun and creative part! We'll now start to make the rough shape of the handle that we will later add to in other steps.
Before you go guns blazing into you first lathe project, heed this advice! Always make sure to wear eye and hand protection whilst working with chisels. Always be careful and think about where the tool will fly if it gets caught. With this in mind you need to position both yourself and the tool out of harms way. Think about the proportions of the handle and what you want the final project to look like. You can mark lines on the wood to show where features will be simply by pushing a pen onto the spinning wood (remember to have completely rounded off the wood before you do this.)
Now you can mount the wood in the chucks; open them up fully and slide the screw up past the jaws. Tighten it whilst making sure that it is not off centre.
You can now start your drill and round off the workpiece. You can do this in either of two ways, sand it down or chisel it down. If you are new to woodturning I suggest that you use sandpaper to do all of the shaping.
Step 8: Detailing:
After rounding the wood we can start detailing it:
Once you have got yourself a cylinder, try and mark the main features of your design onto the wood. I marked out the starts and ends of the curves. Make sure to go slow as hardwood isn't too forgiving.
Start removing wood with your sandpaper, do this until you reach your desired shape.
Once you're happy with your shape simply detach it from the chucks and cut off any scrap wood.
*warning* don't take off too much material where the wood meets the chuck
Step 9: Preparing the Wood:
Now that we have our wooden body we need to flesh it out a bit with some simple brass inlays. Feel free to play about with the locations and amounts of brass, whatever you think looks good. You could even skip this step if you want.
* Firstly you need to cut the handle where the brass will be set, this can be done by mounting the wood in the drill again and pushing a hacksaw blade against the handle.
* Once you have cut off the top, you can draw around it on the thin piece of brass. Be careful not to chip the edges of the cut.
* Now you can cut out the brass. The best way of doing this would be to start off with a hacksaw and finish it using files or a disk grinder; for this I used files but a grinder would work.
Because we put a screw into the top there is a hole; we can fix this by inserting a brass rod for a nice detail on the top.
* My brass rod was a bit too thin to fill the hole. I hammered down the end to widen it; do this by placing a small piece of brass in a vice and beating it.
Now that we have prepared all of the materials we can move on to the assembly.
Step 10: Preparing the Brass Plate:
* Once you have cut off the top, you can draw around it on the thin piece of brass. Be careful not to chip the edges of the cut.
* Now you can cut out the brass. The best way of doing this would be to start off with a hacksaw and finish it using files or a disk grinder; for this I used files but a grinder would work.
Because we put a screw into the top there is a hole; we can fix this by inserting a brass rod for a nice detail on the top.
* My brass rod was a bit too thin to fill the hole. I hammered down the end to widen it; do this by placing a small piece of brass in a vice and beating it.
Now that we have prepared all of the materials we can move on to the assembly.
Step 11: Preparing the Brass Rod:
Because we put a screw into the top there is a hole; we can fix this by inserting a brass rod for a nice detail on the top.
* My brass rod was a bit too thin to fill the hole. I hammered down the end to widen it; do this by placing a small piece of brass in a vice and beating it. Now that we have prepared all of the materials we can move on to the assembly.
Step 12: Setting the First Inlay:
We have successfully prepared the materials so we can glue them into the wood. My original plan was to set it in at an angle, though I didn't have the time, but I'd love to see someone try it out.
Find the brass rod that you widened in the last step and gently hammer it into the top part of the wood. You can add some superglue to the rod before you push it in.
Step 13: Setting the Second Inlay:
spread some glue onto the brass disk and push the top of the wood onto it. Twist the wood thoroughly this should spread the glue around properly.
Step 14: Setting the Second Inlay Pt2:
Wait for the glue to dry and glue the top of the wood onto the main body. Repeat the same gluing process that you performed on the top. If you are using epoxy glue you should leave the piece to set overnight because in the next step we will need to apply some mechanical force.
Step 15: Cutting the Brass Head:
The stamps' body is nearly finished, so we are going to move onto the stamp head. This is the simple part! We are going to need the rubber stamp now, so get it ready.
* Grab the rubber design, draw an outline of it onto a piece of thick brass. You could make the outline differently shaped from a circle. Be creative! Just make sure that it is balanced so that it puts even pressure onto the image when stamping.
* Cut out your outline using a hacksaw and sand it down; this can be done with files or some sort of sander. You could even chamfer the top edge of the brass disk.
Step 16: Drilling the Brass:
Slowly drill a hole in the brass disk, coolant is not necessary as brass is self lubricating.
Reem out all of the burs around the hole and sand down any scratches on the surface.
Step 17: Grinding the Nut:
I needed a way of attaching the body so i sunk a nut into the brass.
Grind down the outside of the nut, yo can do this on a grinding disk, if you don't have one you can use files.
Step 18: Finishing the Head:
The now ground down nut can be inserted into the brass, to make sure that the nut is lateral to the brass you can compress it in a vice.
Step 19: Sanding:
We've got the basic inlays done, but they need sanding down and I needed to fill a few gaps between the metal and wood. This is an easy process, just make sure that you save some of the sawdust from the milling.
*note* Never use aluminium oxide sandpaper for finishing wood as it may discolour the surface. *note*
*firstly take your workpiece to a disc sander (you can do it by hand if necessary) Slowly rotate the wood until the brass is flush with the surface.
Step 20:
If yours, like mine, has small gaps between the wood and brass you will need to mix up some wood filler, this is a simple process, I will briefly cover it here, but if you'd like to learn in more depth simply google "DIY wood filler" and you should come across some useful sites.
* Gather some sawdust that is left over from the previous steps, make sure that it has no brass shavings in it as this will cause discolouration. * Mix this dust with some PVA glue (Elmer's glue) the proportions are anything but exact, so mix it into a thick paste. * Smooth the filler into the gaps and leave it to set for around an hour depending upon the heat.
Step 21: Finding Some Brass:
Because the nut is not completely sunken into the brass disc we need to make some sort of shroud for it. As well as covering the nut it will add lateral strength. I found the brass piece in my scrap bin, but if you haven't got anything similar you should easily be able to pick something up at your local charity shop. Failing that you can mill down some very thick brass rod bought at a scrap merchant. You can do this using the polishing technique we use later in this step.
Choose a suitable scrap piece of brass.
Cut off a suitable piece of the brass and sand down the surface. You can do this by securing the brass in the pillar drill using a bolt and a few nuts. Simply turn the drill on and hold some sandpaper to the spinning metal.
Step 22: Attaching the Collar:
Cut the brass down to just above the length that the nut protrudes from the base; allow a bit of leeway for compression from use. Once cut down glue the brass onto the wooden handle.
Step 23: Inserting the Threaded Rod:
We are now going to insert the threaded rod into the handle. This will allow the two parts of the stamp to attach and detach easily. Put glue onto the rod and push it into the handle until it is protruding over the brass collar by approximately half the height of the nut in the other part of the stamp.
Now that we have all of the mechanical parts finished we can do a test fit and screw the body onto the base. If everything fits okay, great! Move onto the final step!
Step 24: Final Adjustments:
The last step in this build is to connect the rubber design to the head, to allow maximum material compatibility, we can put a foam insert between the rubber and brass.
Firstly cut the foam to the shape of the rubber, then glue it to the brass and glue the rubber on top of it.
Step 25: Using You Stamp!
You did it! You finished your stamp. Now you can go mad putting your design on any and every single surface! To get the best results you should buy some sort of inking pad online and then you're set!
Now, I don't pretend that this Instructable is perfect, far from it, so I shall share some things that I'd do differently next time; firstly, I would use a more sturdy drill, I got quite a lot of wobble causing some imperfections in the shape of the handle. As well as that I would use some more exotic wood. Mine looked a bit bland at the end, but oiling/ varnishing it will help.
Before I end this Instructable, I'm going to show you some examples of what sort of materials you can stamp to:
Wood:
Now you can be awesome like Jimmy Diresta and brand all of your woodworking projects with your logo!
skin: (make sure to use non-toxic ink for this)
Paper:
You could make your own cards for all occasions! If you made multiple bases you could decorate a card with loads of different designs.
Cardboard:
Perhaps use this to mark all of your mail to people? or just make some collages with it.
Thank you for taking the time to read this instructable! (I hope you liked it)
By all means, leave feedback in the comments, and if you make one, be sure to post a photo!
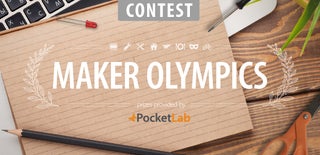
Participated in the
Maker Olympics Contest 2016
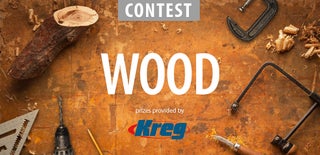
Participated in the
Wood Contest 2016
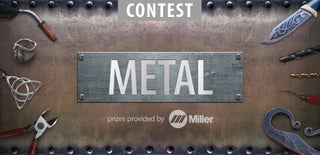
Participated in the
Metal Contest 2016