Introduction: Custom Vinyl Window Decal
I'm sure you've seen quite a few of these. There are all types of decals displayed in vehicle windows. Whether it is displaying a favorite band, a local business, stick figure families, or your favorite political statement, vinyl window decals are a great way to express yourself. They look great and when applied to vehicle windows, they stay a little higher out of the dust and debris that plagues a typical bumper sticker.
This project walks you through the process of creating your own vinyl window decal. With only a few, low-cost materials, and access to a digital craft cutter, you can create these in no time. If you don't have access to a digital craft cutter, ask around at your local area makerspaces. Chances are, someone there has one, or knows where you might find one. Or if you want to purchase one, you can find them at very reasonable prices as well.
For this project, I will be using a Silhouette Portrait digital craft cutter. My local makerspace, The Maker Station, received this as part of an Instructables Build Night program. This is a great machine and you can find them for about $150 retail, if you do not have access to one. The Portrait has about eight inches of cutting width, and will accept nine inch wide media, so that is the size material I will be using.
Materials Needed
- Silhouette Portrait cutter (~$150, but look for a makerspace!)
- White Craft Vinyl (9" wide) (~ $10 for 10 foot roll)
- Transfer Paper (9" wide) (~ $10 for 10 foot roll)
- X-acto knife
- Digital image to use as your decal
Software
- Silhouette Studio Basic (free!)
I choose white vinyl because I like the look of solid white window decals. There is a wide range of colors and prints available, if you would like to try something different for your project. I bought 10 foot rolls to have plenty for other projects, but as you will see, this project only used a small amount. You can also find single sheets of sign vinyl for smaller runs of decals. Silhouette Studio Basic is free to download, or you buy upgraded versions online to add additional features. For this project, the basic edition will work just fine.
Step 1: Prepare Image
The first step is to actually create the decal that you want to cut. I used the logo for my local makerspace. Here is where I ran into the only limitation of the Basic edition of Silhouette Studio. The Basic edition does not support scalable vector graphics (SVG) files. So first I opened up the logo SVG file and just exported it as a rasterized image at a size close to what I wanted to use to minimize scaling issues. I decided to make decals approximately four inches in diameter because that seemed to be a good size for my compact car's window. Plus, at four inches I can just barely fit two decals across on the cutting area of the Portrait.
After opening up Silhouette Studio, use the File -> Open menu to bring in the bitmap logo image. Position the image in the upper left corner of the workspace area. I was able to select and scale the image to the final size i wanted by dragging the corners of the selection box. Make sure you check your Silhouette Studio workspace settings, and select your exact model of cutter (Portrait, in my case). Otherwise your workspace area might not accurately reflect the capabilities of your cutter.
Step 2: Trace Cut Lines
To define the actual cut lines, you need to trace your image. Bring up the Trace panel using the toolbar buttons in Silhouette Studio. Select the image object to be traced, and update any trace settings to match your desired result. In my case, I disabled the high and low pass filters, set the threshold to maximum (100%) and reduced the scale to the minimum (4). This seemed to produce the exact cut lines I wanted. Now click the "Trace" option under the Apply Method section. This will generate traced cut lines from your image.
Drag your image out of the way to inspect the cut lines remaining. If you don't like the results, just hit undo a few times and try again. I played with various settings before I found the right result. At this point, once you are satisfied, just delete the original image object from the workspace. As I wanted to fit two decals across with width of my media, I selected the traced decal object and hit copy and paste. Then I positioned the second decal to the right of the first. You can follow this technique to set up multiple copies in the workspace, or to bring in different images for the same workspace, if you like.
Step 3: Configure Cut Settings and Blade Depth
The next step is to set up the cut settings. Use the toolbar buttons to bring up the cut settings panel. There are lots of materials to choose from that will provide you setting suggestions. There are three main settings you will need to vary depending on the material and type of cuts you want to make. The blade depth (using the provided ratcheting blade), the thickness setting, and the cutting speed. You will need to experiment with your specific material to find out what works for you. There is a handy "test cut" feature at the bottom of the cut settings panel, that will cut a small square with an inset triangle. This allows you to tweak your settings until you get the results you want.
In this case, we want to make a "kiss" cut. That is, we want to cut through the top layer of vinyl, but leave the backing layer intact. So I set the blade depth to "1", which is the minimum setting. The ratcheting blade comes wit a cap used to rotate the setting dial on the blade. If you have misplaced your cap, the Portrait cutter has recess built into the cutter bed itself that serves the same purpose.
The thickness setting relates to how much force is used to cut through the material. Since the vinyl is very thin and cuts easily, this didn't seem to be a problem and my final setting could probably have been reduced. The speed setting is how fast the cutter head will move when making the cuts. Again, you may have to tweak these based on your own test cuts to get good results.
The "sticker paper" material setting suggested a thickness (14) and speed setting (6) that seemed reasonable, so I went with those for my decal. After performing a test cut, the results seemed fine, so I kept those settings for my final cut.
Step 4: Cut Vinyl
Now you can load your media and cut your design. The Portrait has two load media buttons, one for using the sticky carrier sheet provided with the cutter (for holding through cut material) and the other for loading material that does not require the carrier. As we are only "kiss" cutting and leaving our backing material in place, we do not need the carrier sheet.
Center the media between the rollers and press the load media button. If you need to make any test cuts, you can press that option now in Silhouette Studio. Otherwise, you can press the "Send to Silhouette" option and watch your cutter go to work.
You can see from the photos that these types of cutters a capable of very impressive amounts of detail on the cuts. I had one very small cut out on my decal that was disturbed during the cutting process. I found that for the size I chose for my image, some of the lettering detail was very, very small, and could be prone to being moved accidentally by the cutter head. I'm surprised and impresses that only one small element shifted and it was to be removed anyway, so it was a non-issue.
Step 5: Weed Cut Vinyl to Final Decal
With your design cut, you can eject the media from the cutter and start the weeding process. This is where you remove any excess vinyl leaving only your desired final decal design. As you can see in the progression of photos, my decal has many small details. The lettering is a stencil-type font, so each character is made up of two or more disconnected cut-outs. This made the weeding process take a bit longer, but the elements were very easy to remove.
I used the point of a knife to catch and peel away the unwanted sections. If you have any cuts that did not sever completely, you can use an X-acto knife to complete the cuts. With the right cutter settings and a sharp blade, you likely will not have any of that do to. The tiny detail at the bottom of the lightbulb section of this logo, tended to want to pull away with the larger central scrap piece of vinyl. But it was easy to hold the element down with the flat side of my knife point in order to keep it in place as I pulled away the excess. The hard work is done and your decals are almost finished.
Step 6: Apply Transfer Paper
Cut a matching size section of transfer paper. Peel away the backing and then roll it into place across the top of your decals, being careful to avoid air bubbles. Transfer paper is only lightly tacky, so that it will retain your logo for applying it to a window, but peels away easily once the decal is in place. You can use your a small squeegee, a credit card, or even just your fingers to smooth and press down the transfer paper to make sure it is in good contact with the entire decal. You then trim off the excess edging and separate your decals if needed and they are ready to be applied!
Step 7: Apply Decal to Window
To apply your new decals, make sure the surface of the window is clean and dry. Hold the decal up to your window to get a good idea of where you want to place it. Peel the transfer paper with decal attached away from the vinyl backing. Carefully position the decal on the window and then press and smooth it on the window surface. Again you can use a squeegee, credit card, or just your fingers to make sure the decal is pressed into good contact with the window surface. Then gently peel away the transfer paper and your bright now logo decal should remain in place.
This project is very simple to do and, other than the digital craft cutter, each of these decals is less than 50 cents in materials. I only use about six inches of my 10 foot roll of vinyl so I have plenty left for other projects. With a little bit of planning (and some patience), you can churn out decals like this in no time at all.
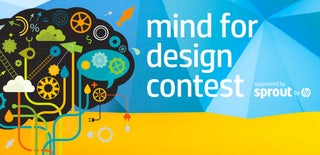
Participated in the
Mind for Design
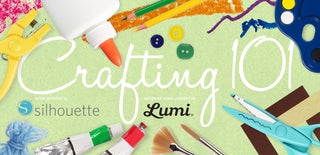
Participated in the
Crafting 101