Introduction: Custom Wood Othello/Reversi Board
My girlfriend loves the game Othello, so for her birthday I decided to build her a custom game board and pieces. The game is very straightforward in terms of components. There are pieces with white/black on each size, and an 8x8 square with holes for the pieces to sit in as the board.
I designed all of the parts in Fusion 360 and CNC milled them out of wood, all purchased from Home Depot. The project costed < CAD75 and took about 10 hours to complete.
I started off using a ShopBot CNC Router in my University's Makerspace, but eventually moved to a Shapeoko XXL that I purchased used to feed my new CNC addiction.
Although I made this with a CNC machine, I will also include instructions on how to make this without one.
Like this project? Let me know and I can do some more games. I was thinking of doing Catan next.
Step 1: Tools & Supplies
Materials (all bought from Home Depot):
1.5" x 1.5" x 2' Oak & Poplar Planks (for the pieces holders)
1/4" x 1.5" x 3' Oak & Poplar Planks (for the sides)
3.5" x 1/4" x 3' Oak & Poplar (for the pieces)
3/4" x 1' x 3' Pine Shelving Board (for the main board, this was the smallest size available)
Wood Glue
Danish Oil or Any Other Finish
Tools:
CNC Router (1/8" and/or 1/4" end mill)
200 Grit Sand Paper
Electric Planer (optional)
Circular Saw, Table Saw, Bandsaw, or Sliding Mitre Saw (anything to cut a straight line)
Clamps
Tools (Without CNC):
Plunge Router
Scroll Saw or Band Saw
Step 2: Design & Model
To get an idea of how I wanted the board to look I drew a rough design on paper, used graphic design software to plan out the dimensions/proportions and overall look, and transferred everything to individual 3D modelled pieces.
Want the 3D design files? Let me know in the comments and I can upload/send them.
Step 3: Glue
The pieces needed to be light on one side and dark on the other. To achieve this effect, I glued the 3.5" x 1/4"x 3' pieces of oak and poplar tightly together to make a single 1/2" sheet of two-coloured oak/poplar.
To do this, I generously applied glue to one surface, stuck the pieces together, and tightly clamped it down to my work surface, letting everything sit for 24h to fully dry and strengthen.
I wanted the sides of the game board to represent both the dark and the light "teams" (so as not to show favouritism to either), so I repeated this step with the 1.5" x 1/4" x 3' pieces as well - making another single 1/2" piece of two-coloured oak/poplar.
Step 4: Cut Parts (The Board)
This is where the CNC comes in, or, if you do not have a CNC, a plunge router, a bandsaw/scrollsaw, and a lot of time.
The Board
The first cut I made was for the playing surface - the main part of the game board. I cut 64 places for the pieces to sit in the middle. I modelled this in Fusion 360 and cut it using a 1/4" double flute up-cut bit on my CNC Router.
Don't have a CNC? This can also be done (tediously so) with a plunge router. After cutting, I used a fresh exacto knife to remove unwanted fibres left behind from the cut and finished it with 200 grit sand paper.
I then cut the board to an even 10"x10" square on my table saw and lightly sanded the edges.
Step 5: Cut Parts (The Pieces)
The Pieces
The second cut on the CNC was for the 64 game pieces. This cut was made out of the 3.5" x 1/2' x 4' piece made in the gluing step.
Before cutting with the CNC, I used an electric planer to shave off 1/8" from each face of the board, making its new thickness 1/4". This made the pieces smaller so that they would fit well inside reasonably sized pieces holders. This can be also done by facing each size with the CNC rather than using a planer, or simply leaving the board as is and having 1/2" thick pieces.
To cut the pieces, I modelled in Fusion 360 and cut using a 1/8" two flute up-cut bit on my CNC. I left tabs so that the pieces wouldn't fly out after the cut was done (even though some of them still did because the wood was warped), so I used a Dremel Tool to cut them out of the stock piece.
Don't have a CNC? This can also be done (even more tediously so) by cutting out each piece with a bandsaw or scroll saw. You could also purchase large radius doweling, cut it in to multiple small circles, stain one half of the small circles, and glue them together individually.
I then took a sanding block, clamped it in a vice, and sanded each individual piece by hand with 200 grit sand paper. The finished product was great, and each piece had its own unique look.
Step 6: Cut Parts (The Pieces Holders)
The Pieces Holders
To hold the pieces while playing the game, I wanted to have each side have a holder the colour of their "team". This was the third cut on the CNC made out of the 1.5" x 1.5" x 2' pieces using a 1/8" 2-flute up-cut bit. I cut the holes shallower than the diameter of the pieces so they could be picked out easily. I also left quite a bit of wiggle room, as the pieces would get stuck when the hole was cut too tight in my test pieces.
Don't have a CNC? Using a plunge router, a chisel, or cutting and gluing this as 3 separate pieces can also be done to make this part.
I used a chop saw to cut these to size (10"+1/2"+1/2" = 11") afterward so that they would fit on the edge of the board.
I then cut the 1.5"x1/2" glued piece in to two pieces, each the length of the board (10"), for the other sides.
Step 7: Dry Fit
Now that I had all the main cuts finished, it was time to dry fit everything and make some final small adjustments. Pressing everything together tightly and taking careful measurements, I cut each piece to fit flush with the others. It looked great and I couldn't wait to finish it.
Step 8: Engrave (optional)
Since this was for my girlfriends birthday, I wanted to make it special by engraving her name in it. I used a 30 degree engraving bit to etch her name in to the side pieces with the CNC. If I had a 60 degree engraving bit, that would've been much preferred due to the ability to increase detail.
The engraving turned out well and was an excellent personalized touch.
Step 9: Glue (Again) and Finish
The final step was to glue the pieces together and apply a finish to the wood to make the grain pop and protect the wood.
I used carpenters glue and a home made 90-degree angle clamp jig I learned about online. It is basically four 90-degree corners and a rope system to tighten it all together. I glued everything upside-down so that the board was flush with the top of the pieces holders and sides. I had one clamp that would fit the width of the board so I used it to push the sides together.
I finished using Clear Danish Oil which did the trick perfectly.
Step 10: Finished Product
This was my first woodworking project, and it was a tough one. I made a lot of mistakes that I hope no one else will make by following this guide. Major lesson learned from this project: its cheaper to buy the more expensive but correct parts up front then to try and make-shift out of cheaper materials.
Also, measure twice cut once. Thats something I never seem to get.
Anyways, I hope you liked this and feel free to ask any questions in the comments!
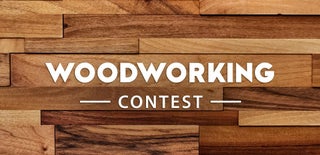
Participated in the
Woodworking Contest