Introduction: Cyclone Dust Collector by 3D Printer
Let's make a cyclone dust collector from scrach.
First of all, why do we need it? And how does it work?
Well, in my case, I want to add an other stage previous to the vaccum cleaner in order to extend the life of vaccum bag. In the end, reducing the use of vaccum bags and ensure the best suction power everytime.
The overview use is that the centrifugal force created by this fast, circular air flow drives the heavier particles, fines, and dust outward toward the wall of the cyclone chamber. They hit the wall, lose velocity, and fall down into a hopper or a bin located underneath the cyclone collector. This way, it will be able to collect a huge amount of dust with an eficiency over 97%.
Step 1: Bill of Materials and Tools
Materials:
1- ABS or PLA filament, for rigid parts. PLA
2- TPU or Flex filament for joints. TPU
2- Heat threaded inserts, M3,M4. HEAT INSERTS
3- Screws. SCREWS
Tools:
1- Soldering. SOLDERING
2- 3D printer. 3D PRINTER (Best seller)
3- Fusion 360 software.
4- Caliber: CALIBER
Vacuum cleaner used: AMAZON
Step 2: Calculations
Now, we are going to make some calculations in order to fit the cyclone design to our requirements.
I let you a link where you will be able to find how to calculate every parameter. Calculations cyclone document
I chose a standard Swift cyclone for a tangencial inlet. My requirements to calculate it comes from my vaccum cleaner which has a flow rate of 200 dm3/s and flexible pipes which limitates the area of suction and transport with a 35mm of diameter.
Note: Depending on your vaccum cleaner and their flexible pipes, you will have to adapt the inlet and outlet cyclone conections
Step 3: Design and Assembly in FUSION 360
Once we have already defined our requirements and calculated all dymensions of our cyclone, we will start to design it on 3D model.
Let's use FUSION 360 as a software to design each part of cyclone as well as the assembly or even renders.
If you don't know yet how to use, I recomend you this link, for beginners:FUSION 360 Tutorial for absolute beginners.
In my case, I designed it in two main parts, because it's too long, but it will depends of your printer size. The next step is to design the couplings to conect the ends of my flexible pipes. So, for the outlet of the ciclone, I designed a adaptor to conect a flexible pipe from my vaccum cleaner. As well as for the inlet cyclone I designed a kind of nozzle to adapt the end of other flexible pipe, which works as a inlet air flow.
Note: I recomend designing cyclone with aproximatly 4-6 mm width in order to prevent the premature wear of the internal cyclone walls, which are constantly in touch with abrasive materials.
Other recommendation, should be adding washer made of flexible material between each screw conexion in order to make it as airtight as possible.
Step 4: Print Parts
Printing parts it's my favourite step, we just need to get some material as PLA or even ABS for getting stronger and more resistant parts and TPU or any flex filament for make the seal joints.
In my case, I used heat threaded inserts, but you can use regular nuts as well, doing holes into the parts which are going to be joined.
Slicer:
Normally, I tend to use Symplify as slicer, but you can also use CURA, for free.
I let you right here a link about 3D printing parameters, depending on materials you are going to use for the cyclone printing parts: Printing material guide. It's very interesting.
Note: Ensuring our plastic 3D printed parts don't have any losses, I recommend you to use a kind of epoxy which create a surface layer which covers every tiny hole between.
Step 5: Colocating Heat Threaded Inserts
Helping us wiht a soldering iron and pliers, heating the threaded Inserts and pressing it against the hole until it got flushed.
Note: Letting the holes diameters a little bit smaller, you will get a better fit.
Step 6: Assembling All Parts
If all the parts have been made rightly. When we assemble it, everything should fit properly.
Of course, we need a container such a bucket. It should have a hole cut to fit the bottom of the cyclone cone.
Note: It's important there isn't any hole or air losses on the bucket, in order to avoid wrong functions.
Step 7: Tests of Function
To be sure that everything works rightly, we have to be aware of there isn't any air losses at any joint or through any plastic part. And realise that huge percentaje of dust and particles are being collected into the bucket.
I hope you will have enjoyed the instructable, and if you want just to replicate mine, i'm going to let you attached the .STL files for every part:
Attachments
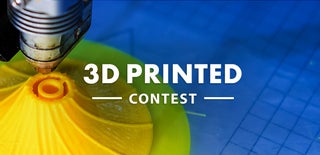
Participated in the
3D Printed Contest