Introduction: DIY Bicycle Turn Signal
Many of us use bikes for commuting and leisure, and many of us suffer from long and dark winters as well! If that's the case, you probably have a pair of bright front & rear lights, which make spotting you much easier for drivers and other road users, making cycling much safer.
There is however another issue when riding on the road: turn signals! There is a hand signal convention, but I have the feeling that many drivers don't understand it, or maybe it's dark, or you're not confident to take your hand out of the handlebar. This motivated my friend and I to build an electronic turn signal, which will be placed close to the rear light with a control switch in the handlebar.
This is hardly a novel idea, there are loads of commercial and DIY products like this, and can be found very cheap online. Our idea was to pack together a (more or less) neat set of lights, trying to keep the cost as low as possible!
This instructable participates in the Bicycle contest, have a look and give us a vote if you like!
(NOTE: this project tries to make cycling a bit safer by adding turn signals to your bike, it doesn't replace a good set of front & rear lights. Having the turn signals doesn't guarantee your turn is going to be expected, but when combined with safe riding and extra hand signals, it will be much easier to spot, specially when it's dark. Ride safely!)
Step 1: Part List
The components are very simple and inexpensive, the case can be made from scratch or recycled, and the tools are commonly available (check your local hack/make-space!). The total cost of all the components including a case will be around $/£/€ 5, but you probably have most of them lying around!
Electronics and casing:
- Pretty much any kind of case will do, the one we used is this one. Similar cases of different sizes and colours are readily available online and in electronics stores!
- 10x 5mm orange LEDs, cheaply available everywhere. Red LEDs could work as well, but orange is the usual colour for turn signals in cars, so easier to recognise.
- 1x Diode, can be a standard LED
- 2x BC547B transistors. Most NPN hobby transistors will work fine!
- 2x 10uF electrolytic capacitors
- 2x 470kΩ resistors
- 1x 33Ω resistor
- 1x Three Positions 3 Terminal SPDT ON-OFF-ON Mini Toggle Switch
- 1x On/Off switch/button
- 2x AA batteries or 3.7V 250mAh (or simimilar) rechargeable battery
- Zip ties or old bike light strap to fix the lights to the saddle and the control switch to the handlebar
(Note: the 10uF capacitors and 470kΩ resistors can be varied, as they control how quick the LEDs blink, see step 3 for more details)
Tools
- Soldering iron
- Drill/Dremel
- Hot glue gun
- Screwdriver
Step 2: The Case
It needs to be big enough to fit all the electronics inside confortably, and it's a good idea to allow room for the two arrows, such that they're clearly separated, this will make it easier to understand by drivers. Keep in mind that you want to strap it to the saddle post with a zip tie or similar, so it needs to be light enough.
Once you have your case ready, you need to drill 5mm holes for the signal LEDs, in any design you want, we've found that 5xLED arrows work well. Depending on how you plan to fix it to the bike, you will need more holes: in our case we use an old rubber strap from a broken bike light, which uses two bolts, as you can see in the pictures. If you don't have something similar, a zip tie will do, just drill to holes close together on the back of the case and slid a zip tie through them, which can be locked onto the saddle post.
We found it easier to place the LEDs in the holes, and bend their ground pins together towards the centre, as they all go together. In a similar fashion, positive pins from the same side are grouped together. You can use a glue gun to fix them better, just place a big blob on each of them after positioning their pins! Even without glue if you solder their pins together they should stay together quite nicely.
A 5mm hole was drilled on the top to fix a standard on/off switch which controls the overall power from the battery.
Last but not least, you need a small hole somewhere convenient to get wires to the switch which will be located in the handlebar, in our case we drilled a 3mm hole, just enough to squeeze the three cables together. The tighter the fit, the more waterproof it will be!
Depending on the case and the drill you use, it may be a good idea to use fine sandpaper to get a nicer finish.
Step 3: The Electronics
We wanted the simplest possible circuit to keep the cost as low as possible: the best option is to use an astable multivibrator. It uses two transistors, two diodes and two capacitors to create a square wave output waveform: for us this means automatically switching the LEDS on/off/on/off/... periodically, exactly what we need!
This configuration is very well explained in many websites and books, for more information check here for example. The transistors act as switches, letting current flow through them depending on the current on their base. The capacitors are the times in the circuit, they both alternate between charged and discharged states, activating the transistors intermittently, which causes the LEDs to blink.
The values of the resistors and the capacitors will determine how fast the LEDs blink, although the combination of 470Kohm resistors and 10uF capacitors produce a nice blinking pattern for out turn signals, feel free to experiment with different components! These values for our components were obtained from here.
Have a look at the circuit and familiarise yourself with it, it's a great idea to prototype it in a breadboard to make sure everything works and to help understand it.
Once everything is working, the best way to put the electronics together is to use a perforated board, which has a copper side and plastic side. You can introduce the components from the plastic side and solder them together in the copper side. There are loads of great resources which deal with soldering this kind of boards, check here and here!
You will need to measure your bike and cut some long cables which will run form the saddle to the handlebar, along the top of the frame, check the pictures for details. A good idea is to use a three position switch, where the default position for the toggle is centre, move it to the right two start blinking the right hand side arrow and vice versa.
Step 4: The Handlebar Switch
This part is quite open to imagination. If you have another bike light strap lying around, it would be a neat solution, we didn't, so we just used a zip tie and a small plastic square with a 5mm hole to fix the switch, and two smaller holes close together for the zip tie.
Despite its simplicity it's tightly fixed and works fine.
Step 5: Fit Everything in the Bike
Installing everything in your bike is very easy!
Strap the lights under the saddle, it's a good idea to keep them pointing horizontally or a bit upwards so that drivers see them better. In our case, the bike light strap we use has a height regulator so we can point them wherever we need. If you're using a zip tie, consider adding some kind of padding or foam piece to keep the box horizontal.
Use several zip ties to keep the cables tight and safe along the top frame bar.
Fix the control switch in the handlebar, where it's confortable for you. This may depend on your handlebar type (mountain bike or road bike?) and your hand position, find a spot you like!
Step 6: Ride Safely and Enjoy Your Bike!
Thanks for reading, comments and suggestions welcome!
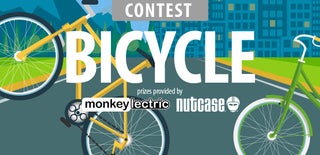
Second Prize in the
Bicycle Contest 2016