Introduction: DIY Carbide Lathe Tools for Cheap
I recently got into wood turning, and I wanted to have a nice set of tools. Most lathe gouges and chisels are high speed steel (HSS), but they require constant sharpening and leave something to be desired. The premium wood turning tools use replaceable carbide inserts that stay sharp considerably longer, but you also pay a premium for them.
Instead of paying around $100 per tool, I set out to make my own. After it's all said and done, I've got $53 dollars invested in two carbide cutting tools, and I've got 6 regular steel chisels and gouges left from the materials that I bought for the project.
Not too shabby - here's how it's done!
Step 1: Gather the Materials
I've seen some Instructables where people turned their own hardwood handles, used copper plumbing to make custom ferrules, cut or machined their own tool shafts, and even hollowed out the handles and loaded them with shot to reduce vibration. While I will probably do this eventually, I wanted more instant gratification. I wanted a set of carbide cutters to use between now and then. So... I decided to just use a cheap set of donor chisels as the handles for my own carbide lathe tools.
I bought a set of 8 lathe tools from Harbor Freight for $20. I also purchased a pair of carbide inserts from Easy Wood Tools on Amazon. I decided on the Ci0 round cutter and the Ci1-R2 radiused square cutter. Both carbide inserts came with their own 8-32 hold down screws.
If you're following this guide verbatim, here are the links to exactly what I bought:
http://www.harborfreight.com/wood-lathe-turning-to...
https://smile.amazon.com/gp/product/B0039ZYQLW/
https://smile.amazon.com/gp/product/B003A00J6M/
You'll also need:
A tap and die set, specifically an 8-32 tap.
A scratch awl.
A center punch.
A drill and bits. Something to pilot drill with, and a 1/8" bit. (#29 if you have it)
A combination square.
Something to protect bare metal. I have Johnson's Paste Wax, so I used that.
Step 2: Layout Your Work
I set out all of my tools and the inserts to test fit which tool would hold each insert the best. I decided to use the 1/2" round tool to support the square cutter, and the spear point tool to mount the round cutter.
Hold the parts together, and inspect how they line up, front and back. You want the carbide insert to be centered on the width of the chisel shaft, and you want the insert to extend beyond the cutting edge of the original tool but still have enough material left over to tap threads through the full thickness of the chisel.
Once you've got it lined up the way that you want it, use the inside of the carbide insert as a guide and scratch a circle into the steel tool shaft.
***Be aware that the carbide inserts are razor sharp! You must use care when handling them so that you don't cut yourself. Wearing heavy gloves is a good idea.
Step 3: Find the Center
Now that you've got a rough idea of where you'd like to locate the carbide inserts on each tool, it's time to mark the exact locations for drilling.
Using a combination square, scratch a center line down each tool. Set the square to be a little shy of center, and scratch a line down each side. Adjust your square if you need to, and draw another set of lines, until you find the exact center line along each piece of steel.
Using the same square, scratch a line through the center of your circle that's perpendicular to your center line. Now you've got crossing lines that should be centered in the first circle that you scribed.
Step 4: Center Punch and Drill
Make sure to take a close look at the marks you've made. If something doesn't line up right, now is the time to fix it! If you're satisfied with the marks on your chisels, use a center punch to mark that spot for drilling. This helps you line things up, and it will guide the drill bit to the right spot without 'walking' around before it starts cutting.
Using a pilot bit, line up the mark from your center punch, and drill all the way through the chisel blade.
Follow that drill with the 1/8" (or #29) to prepare for tapping the threads.
Note, you can use the 1/8" bit first, but I like to drill pilot holes with drill bits that I don't mind breaking.
Step 5: Tap the Threads
Using an 8-32 tap, it's time to put threads in the holes you've drilled.
The secrets to tapping threads, especially in steel, are to use lots of lubrication, take it slow and steady, and clear the cuttings out of the tap.
Start the oiled tap, as straight as you can get it, into the chisel blade. Keep in mind that you are cutting away metal. You'll need to turn the tap forwards until you feel resistance, and then turn it back a little bit to clear the cuttings. It's a 'two steps forwards one step backward' sort of process. You may even need to completely unscrew the tap to clean the metal cuttings out of it. Clean out the chips frequently so that you don't fill up the flutes in the tap and start jamming the tool. It's better to use up oil and paper towels than it is to break a tap.
When you're finished tapping the threads, take a moment to clean everything up. Oily metal shards don't mix with tools, wood, or paint very well. They're also hot, and they make unpleasant splinters.
Step 6: Countersink the Holes
The screw for the carbide inserts that I used extends just a tad beneath the flat surface on the bottom of the carbide. Because of this, you'll need to countersink the holes just a touch to fully tighten the screws and hold down the carbide inserts.
I used a 1/4" drill bit, and drilled down just enough to reach the full width of the head of the bit. You can test fit your inserts between drilling to custom tailor this clearance, but that's the depth that worked for me. Just don't go too deep and reduce the length of the threads more than you have to.
Step 7: Protect the Metal
One of my chisels was a tad rusty, so I sanded off the rust. I wouldn't use sandpaper on a nice chisel, but it was 1/8th of a $20 purchase, and I'm only using it as a tool holder, so I decided not to feel too bad about it.
Unprotected metal will rust from the humidity in the air, so it's important to coat your tools with something to keep out the moisture. I had Johnson's Paste Wax on hand because I use it on my tablesaw, so I applied it to the unprotected blades of my chisels. Many other products exist, but check to make sure that whatever you use doesn't contain oils or silicone that can cause problems with paint and finishes.
Step 8: Final Assembly
Now you can screw your carbide inserts to the lathe tools that you've prepared!
Check that they fit nicely. Be sure that they're centered on the chisel blades, and that the cutting surfaces of the original chisels don't extend beyond the base of the carbide inserts.
You want the carbide to be screwed down tight, but be cautious because carbide is brittle and can shatter under pressure. There is a such thing as too tight.
Also, remember that the carbide blades are sharp!
Step 9: Grind the Extra Threads
If your hold down screws extend beyond the bottom of your chisels, you'll probably want to grind down the excess and make them flush so that they don't catch on your tool rest. I did this with a bench grinder, but you could do this with many different tools. Hacksaw, Dremel, sanding disc, etc. If you expose bare metal, make sure to protect it with some wax, as well.
Step 10: Closing Thoughts
I will still probably tweak these tools a bit, but they turned into a very nice (and affordable) set of carbide cutters! I'm happy throwing chips on the garage floor again.
I need to figure out a nicer way to align the square cutter while I tighten it. The premium tools that use these inserts have a shelf milled into them to locate the cutter and to keep it from rotating when you tighten the screw. For now, I'm happy enough with indexing it by hand until I get it just right. Again, be careful of how sharp the blades are when you're handling them!
I'm also curious about the feel of round bottom tools. Most chisels are flat, but you get a nice feeling from rocking and rolling a round gouge on your tool rest, so I will eventually try to come up with a way to mount these cutters on a round bar and achieve that feel.
What do you think? Have you done a project like this? What did you do better? What should I do next time?
Thanks for reading !
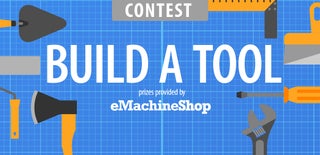
Runner Up in the
Build a Tool Contest 2017