Introduction: DIY Low Cost Air Hockey Table
A professional air hockey setup is usually available only in arcades due to the sophisticated systems that are required to operate it. Our goal was to build a DIY air hockey table, bringing this gaming experience at home.
By using commonly available materials we have succeeded in making a cost effective and easy to build air hockey table. Our project uses the power of modern technologies such as lasercutting and 3d printing to make a customized and easily scalable system letting one build the game according to their preferences.
There is no better joy than seeing the puck gliding smoothly on the cushion of air and dropping into the goal. Follow on to build your very own air hockey game and we can ensure you that it will lead to hours of fun!
Do drop a vote in the games contest if you liked the project and check the video linked above.
Step 1: Overview of the Playfield
To conceptualize the air hockey table, we first designed it on fusion 360. We customized our playfield to a reasonable size making it easy to setup yet keep the fun factor of the game. Here are few features of our diy system:
- Using the power of digital fabrication, various parts like the playfield and strikers were made. With present laser-cutting and 3d printing precision the components have a clean look and are durable.
- An electronic counter facilitates keeping track of the score and provides a display for maximum three digit numbers.
- The design uses a vacuum cleaner that features a blower option to provide the playfield with constant airflow. Giving another purpose to the vacuum cleaner and making it house friendly.
- Embedded LED strips enhances the gaming atmosphere and adds an aesthetic aspect.
- The use of common household materials drastically reduces the cost to build this game.
- Form factor makes it easy to mount on a table or a floor and lets one store it away conveniently too.
Step 2: Principles of Air Hockey
The principles of air hockey are very similar to regular ice hockey, the primary differences are:
- Air hockey is a game which can be played on a tabletop whereas hockey is a game that requires a big arena/field
- Hockey is played as a team of 6 whereas air hockey is usually a single player game
- And finally, in hockey, the puck is made to slide smoothly across the playfield using a layer of ice whereas in air hockey a cushion of air essentially levitates the puck millimeters above the playfield reducing friction. This makes the game extremely fast-paced and enjoyable.
The lift generated to levitate the puck is achieved by creating tiny holes all over the playfield in a grid that blows air at high pressure from underneath. The air is then forced through these holes and exits with a high velocity countering the weight of the puck making it float on a layer of thin air.
Step 3: Materials Needed:
The following is the list of all the components needed to make your very own air hockey table. All parts should be commonly available and easy to find.
HARDWARE :
- 1/4" Plywood - dimensions; 80cm by 50cm
- 1" by 4" Pine Wood Plank - 8 ft long
- 3D Printing Filament- PLA or ABS
- M3 Threaded Insert x 8 - (optional)
- M3 Bolt x 8 - 2.5cm long
- Wood Screw x 12 - 6cm long
- Wood Screw x 30 - 2.5cm long
- Acrylic
ELECTRONICS :
- Arduino Uno
- Push Button x 2
- LCD Display
- LED strip (RGB)
- Jumpwire
- 12V Adapter
The total cost of the model came to around 50$ which in comparison to the products in the market is almost half the cost!
Step 4: 3D Printing
We used a 3d printer to make several of the custom parts. As most parts didn't need much strength, we printed them in PLA which we recommend as it is also easy to print. The following list contains the total number of parts and their printing specifications. All the STL files are provided in a folder attached below, allowing one to make their needed modifications if necessary.
- Striker x 2, 20% infill (one colour for each player)
- Goal x 2, 20% infill (one colour for each player)
- Corner Guard x 2, 40% infill
- Corner Guard (mirrored) x 2, 40% infill
- Electronics Compartment x 1, 20% infill
- Acrylic Spacer x 12, 20% infill
The parts took a total of 48 hours to print and were done on our ender 3 printer.
Attachments
Step 5: Laser Cutting the Parts
The play-field needed to have a grid of 1mm holes. This would be a tedious job if done manually thus we decided to use the power of laser-cutting. The following list are several parts that were laser-cut for the air hockey game. The file attached below contains the 2d drawings of all the parts for laser-cutting.
- Playfield, white 2mm
- Diffusing Panel x 2, white 2mm
- Top Panel x 2, white 2mm
- Striker Base x 2, orange and blue 2mm (one colour for each team)
- Puck, black 2mm
Attachments
Step 6: Post Processing
The 3d printed parts have few supports and thus require a bit of post processing. Use pliers to gently remove the support material and sand any remaining bit of plastic. After we lasercut the playfield we realised that few of the air holes were still blocked. If one faces similar issues you can easily use a sharp point like the tip of a compass to poke out the covered holes. Hold the sheet against a lightsource letting you know which holes are blocked.
Step 7: Building the Frame
The frame of the air hockey table is made of 1" by 4" pine wood. The inner dimension of the frame or the playfield size is 80cm by 50cm. Using a circular saw and a guide, we cut down four pieces of wood, two strips of length 80cm and two of length 54cm (as the width strips will overlap the length strips). Once done lightly sand the edges to make the surface smooth and even.
Step 8: Cutting Wooden Spacers
To attach the acrylic playfield to the frame we made wooden spacers to support it from the bottom. From the remaining pine wood cut 12 strips of 1.5cm in width. Then using a hacksaw cut them in half to end up with 24 spacers. Not only do these blocks support the playfield but it provides the right spacing to attach the plywood bottom panel.
Step 9: Gluing the Spacers
The acrylic playfield's top surface sits exactly 2cm below the top of the frame. As the spacers need to support the acrylic from the bottom, draw a line 2.2cm from the top accounting for the 2mm acrylic thickness. Leaving around 5cm from either side, glue the spacers equally spaced out from each other. On the length strips glue 5 spacers and on the width strips glue 4. We used normal wood glue to stick the blocks making sure to align them perfectly on the line and then clamped them overnight.
Step 10: Screwing the Frame
We used three woodscrews per joint to secure the frame together. Mark out on the width strips the wood's thickness on both sides and center three equidistant holes. We used a 5mm bit to create a pilot hole on both pieces of wood and countersunk the hole to allow the screw head to be driven in flush. Using a speed square ensure that the pieces are square and correct any imperfections. This is important as the playfield needs to fit snuggly into the frame, as gaps will create air leaks.
Step 11: Slots for the Goals
The width of the goal in a table is officially 3 times the diameter of the puck. Thus on the two width pieces we marked a rectangle of length 15cm by 1cm a centimeter below the top surface making sure the goal was centered. Then we bored out two holes to allow the jigsaw to fit through and finally cut along the line. One could also use an oscillating cutter like Fein to produce very neat cuts. File the edges to remove any remaining material.
Step 12: Attaching the Acrylic Playfield
Simply apply a generous amount of glue to the wooden blocks and place the acrylic sheet. Once done rest some weight along the edges, like the tools lying around, till the glue cures. Then with a spirit level ensure that throughout the table the surface if flat and leveled.
Note: It is important for the playing field to be perfectly leveled as minute depressions can cause the puck to not glide smoothly over those regions.
Step 13: Sealing the Gaps
To make sure that all the air comes out only from the holes from the playing field one needs to seal any gaps. Use a hot glue gun or a silicon gel (used to seal aquariums) to close any leaks along the acrylic panel.
Step 14: Making the Bottom Panel
The bottom panel has the same dimensions as the playfield. We chose a remaining piece of 5mm plywood from a past project for the bottom, although one can choose any wood that provides a certain sturdiness. To allow the air to flow into the playfield, we cut out a hole of the size of our adaptor into the middle of the base. In our case it was of 5cm in diameter but it depends on the personal blower being used. We used a jigsaw to cut out the hole and then cleaned the surface with a dremel
Step 15: Attaching the Bottom Panel
Now that the bottom panel is ready one can flip the air hockey frame. Apply glue on all the wooden blocks and place the bottom panel. For precaution we decided to drive in few screws to make the joint even stronger. Then using a glue gun seal any gaps between the panel and the frame.
Step 16: Adding the LED Holders
Roll out the LED strip along the length of the play-field and cut it to the nearest "cut mark" on the strip. Then evenly space out the five 3d printed spacers with the slot facing up and glue them in place. Let the parts glue overnight with clamps and then slip in the LED's into their slot on the prints.
Step 17: Soldering the LEDs
The two LED strips situated on the two edges of the table are connected in series using four wires (+12v, red, green, blue) to essentially form a long LED strip. Solder wires on one end of one strip then pass it through the hole in the acrylic panel and take it out from the other hole on the opposite side. Solder this end of the wire to the second LED strip. This is then connected to the controller box using jumper connectors. The controller box is then secured to the bottom wood panel using screws.
Step 18: Mounting the Diffusing Panels and Corner Prints
The side diffusing panel is stuck to the 3d printed spacer with glue. Once done place the top panel and mark the five mounting holes and drill the pilot holes. Then place the 3d printed corner guards over the top acrylic panel and drive in the five screws to secure everything in place. The corner pieces have two side mounting holes and can be added if necessary. This system allows one to easily dismantle the top panel in the future if one needs to access the led strips.
Step 19: Adding the Goal
The goals can be mounted on both sides, in our case one blue and the other orange. We noticed that if we mounted the goal slightly under the slot the puck wouldn't bounce back out. Place the goal a puck thickness lower than the slot and use the four mounting holes to attach the goals.
Step 20: Assembling the Strikers
To enforce the strikers as its printed in PLA we stuck 2mm lasercut discs. This not only prolongs the life of the striker but also has a better impact against the puck as it's acrylic against acrylic. We used wood glue and drops of CA glue to join the parts.
Step 21: Air Input System
For the air input system, we decided that it would be convenient if the inlet for the blower would be on the side of the frame. To do so we needed to add an elbow to divert the air flow from the bottom to the side.
The components needed for this system are: a 3d printed adapter, 3d printed cap, a pvc 90-degree fitting and a length of 20cm matching pvc pipe. Start by making a hole in the side frame with a forstner bit the size of the printed adapter. Friction fit the 3d printed cap over the pvc fitting. Then secure both the adapter and pvc fitting with screws to the frame. Once done you can slide in the pvc pipe to join both connectors. In our case the fit didn’t produce any leaks but one could seal the joints if necessary, with Teflon tape.
Step 22: Electronic Scoring Compartment
The box requires threaded inserts to be added so that one can easily remove the cover. To do so preheat a soldering iron and sink the threaded inserts flush to the surface. Add the press switches on either side and press fit the LCD in its slot.
Step 23: Connecting the Components to the Arduino
To mount the counter unit, mark the two holes on the inside of the box. Then drill the holes in the wooden frame and secure it with two wood screws. To allow the power cables into the Arduino drill another hole in the frame, aligned with the one provided in the box. You can then pass in the wires and secure the connections.
The wiring consists of connecting the screen and the two buttons to the Arduino. Follow the wiring diagram attached above.
Screen to Arduino:
- VCC to 5v
- GND to GND
- SDA to A4
- SCL to A5
Button 1 to Arduino:
- One end to GND
- Other to D4
Button 2 to Arduino:
- One end to GND
- Other to D5
Step 24: Wiring the Power Supply
Our air hockey table requires power in two places apart from the blower itself which will have its own power source. One for the scoring system and the other for the lighting system, both can be run off 12v DC. To achieve this we created a simple power distribution system, which takes in the 12v power input from the adaptor and splits it into two. One that will power the Arduino and the other that will power the led strips. We used male and female power jacks to make the power distribution system. Follow the wiring diagram attached above to make your own.
Once that's done, one of the ends will power the Arduino:
- +V to Arduino's Vin
- GND to Arduino's GND
And the other end can be connected into the led strip's electronic box.
Step 25: Uploading the Code
The program for the scoring system is attached below. We have made a programming port in our electronics compartment so that uploading or modifying the code can be done easily. Plug in the Arduino to your computer and use the Arduino IDE to upload the program.
The pictures attached above demonstrates that the LCD display changes colour to the winning player's team colour. With each click of the button the score count increase by one and the display can show up to 3 digit numbers.
NOTE: Make sure that the Arduino is not powered by the 12v power source while connected to your computer! Doing so may damage your Arduino board.
Attachments
Step 26: Game On!
The air hockey table is ready. Attach the blower from the side and turn on the power. The puck should start floating around and from there it is game on. Enjoy slamming the puck into the goal and keep track of the score on the counter.
Step 27: Conclusion
Although in the beginning we were hesitant and skeptical whether our homemade blower powered air hockey table would work, the results have exceeded our expectations. It was a super fun project to build and it is even more fun to play with.
After having played with this setup for several weeks we are happy to say that the parts hold up and that the design has past the test. We hope you feel inspired to make your very own low cost air hockey table, as we can ensure there will be no regrets!
Do drop a vote for us in the games contest if you liked the build.
Happy making.
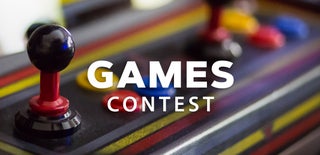
First Prize in the
Games Contest