Introduction: DIY Kiteboard/wakeskate/longboard
DIY
kiteboard/wakeskate/longboard
This isnstructable will contain information on how to build a kiteboard, the same building method can also be used to make several other boards(wakeboard, skateboard, wakeskate etc.).
Materials needed:
Epoxy resin
Wood (with few knots)
Hardwood, (cumajru or similar)
Glassfibercloth
Power Tools:
Bandsaw
Powersander
vacuum laminating equipment:
Vacuum pump (refrigerator pump)
cover plastic (PE or other that does not stick to epoxy)
bleeder plastic(cover plastic with holes)
excess glue absorbing cloth(fleece blanket)
Other:
Basic workshop tools
long clamps
T-nuts to install bindings.
Bindings
Patience
Design:
when it comes to kiteboard shapes there are many alternatives and designs available, Google kiteboard you will be surprised. If you have a favorite board you want to copy, you can place the board on a sheet of paper and then trace around it. Or you can visit your local surf shop and ask nicely to trace on of their boards.
Using a surfboardCAD will also be a great alternative, this will give you whatever you like.
On the internet you will find many free surfboard drawing programs, one of the simplest being Board CAD (http://www.boardcad.com/news.php). This is the software I have used the most.
Draw your profile and outline of the board in this software. Make the profile the same thickness all over, this will save you time when it comes to sawing. I will cover this later. The profile does not have to be “original” feel free to experiment with different shapes. See pictures.
The length and width of the board depends on the weight and skill of the rider. See the site chart on this site. (http://www.surfertoday.com/board-size-chart/kiteboard.) The kiteboards in this instructable are 136 cm long and 40 cm wide (at the widest). I can’t find the find the files I made on my computer as of now, but I will upload them later. When it comes to the rocker, how much the curve it under the board, I recommend 3-5cm, measured at the nose and tail, when the board is placed flat on the ground. The rocker does not have to be symmetrical, but most kite boards are.
Draw your outline and rocker of the board, click the print button. Then you will get many pieces of paper, glue/tape them together, now you are ready to proceed to the next step.
Step 1: Making Tempelates:
Making a template:
Now that you have your board on paper, you need to make a plywood template. This template will be of grate help, when you make your cuts. To make a plywood template, take the paper you printed and tape it down on a piece of plywood. Then saw the shape out. When it comes to the outline, you only need to make a half piece, you can use the same piece on both sides, just by flipping it.
The rocker outline is a bit different, as I have mentioned earlier if you make the profile the same thickness all over you only need to cut one place, (see picture)
Step 2: Sawing Profiles
Marking the profiles:
Place your rocker template on the wood you want to use, and draw a line. Then offset the template 11mm (or whatever you want) then make a new line. Continue this way until you have a piece of wood with many lines. Be creative, you don’t have to use a single type of wood, you can vary between types of wood, to get the colors and couture you want.
Saw the profiles:
place your marked pieces of wood on your bandsaw and saw. Be sure to have the bandsaw set correctly. If the wood you’re using is 2.5cm or thinner you can use a high-end hacksaw, but the blade does almost always wander, and make nasty cuts. But you can add a blade guide to the hacksaw. Then it is usable also wit thicker dimensions, but not at all great.
After sawing you end up with many pieces of wood, maybe 9 if your board is 40cm wide and the pies of wood 5 cm wide. Notice 9 pieces of wood this adds up to a total of 45cm width. This is to be sure everything adds up in the end.
Step 3: Gluing Porfiles
Gluing profiles:
Place your profiles on the rail-clamps, with the smallest face facing upwards. Add glue. Clamp them gently. Place pieces of wood at both ends, four pieces in total, one on the underside and one on the top, Use clamps. These pieces of wood are to align all the profiles. After attaching the alignment pieces. Tighten the larger clamps hard, but not so hard that you squeeze out all the glue. Let it the glue dire. You can use polyurethane or normal wood glue. I think normal wood glue is the best; it is cheap and “non” toxic.
Step 4: Rough Sanding and Cutting Outline
Rough sanding:
After the glue is fully dried, rough sand the top and bottom of the board. A power sander with 80 grid Is strongly recommended.This is to make it simpler to draw on the lines.
Cut out the outline:
when cutting the outline using a router will make the best cut. But you can also use a jig-saw. Place the template you made earlier on top of the “board” then trace a line with a pencil. Mirror the template and do the same on the other side. Now cut out the shape.
But as you see the board in this intractable has a fancy shape at the end. This shape is cool, and makes the board more unique. To make this ornament you need an additional template. The same proses as the other templates applies to this one as well. You can draw on the computer, but Surfboard CAD software’s does not provide the correct “tools” to make these types of shapes. I found drawing on paper to work the best. Fold a piece of paper, and draw half of the shape, then cut it out with a scissor. Then trace the design to a piece of wood(witch you cut out afterwards) or directly onto your board.
If you are using a router to make the cuts, it is best to use a router bit with a ball bearing on. This bit allows the temples to fulfill their full potential. Place the templates on the “board” with clamps. Then use your router to cut out the shape.
Step 5: Final Sanding.
Final sanding:
When all has dried. Draw lines illustrating where to sand. ( see picture) Keep the bottom of the board flat. Sand down the sides of the top face of the board. Finish with fine sand paper, and remove all nasty cuts and scratches. These will become visible after laminating.
Step 6: Adding Hardwood Rails
Optional, add hardwood rails:
Adding hardwood edges is awesome and makes the board tougher, but requires a bit more work. It also requires a clean cutout of the profile, with the use of a router(or good bandsaw skills). Use your template and cut out an additional profile, make this a thin one, only 3-6mm. If you are making a fancy shape on the ends. You need to use the same template to make a line on a big piece of hardwood, and then cut it out with a band saw. When gluing on the hardwood rails. Use plenty of glue; you can mix in sawdust if you have large gaps. Use tape to hold the rails in place when the glue is drying.
Step 7:
Vacuum laminating:
You can laminate the board in different ways, you can either use vacuum which requires some equipment, or you can laminate old fashion. I use vacuum bagging, because this gives the best result, and you can add the convex shape to the bottom.
The process of vacuum laminating requires.
:vacuum pump (refrigerator pump)
Cover plastic (PE or other that does not stick to epoxy)
Bleeder plastic (thin cover plastic with holes PE or other plastic that does not stick to epoxy)
Excess glue absorbing cloth (fleece blanket)
To make a concave shape under the board you will also need a mold. To make the mold use the rocker template to make 3 profiles out of a 2*4 plank. Make a box out of them, and place a plywood sheet on top of the box. But place the center 2*4 with a slight offset to make the plywood surface a slight convex. The convex can be from 3-6mm. Now you are ready to start vacuum laminating.
Place fiberglass-cloth on the underside of the board, then epoxy, about 100 gram on each side should be enough. But it depends on the type of fiber glass cloth you are using and how big your board is. When all the epoxy is evenly spread out place the bleeder plastic on top. Then flip the board and apply epoxy, fiberglass and bleeder cloth on this side as well. Now place a Fleece blanket on both sides of the board, put the entire setup inside the vacuum bag existing of PE plastic. Suck out all the air and place weights on top of the entire setup, to make the board fit into shape.
The vacuum bag is made of construction plastic duck tape and a simple valve, there are many ways to make this, use your imagination.
As you can see the instructions on how you vacuum bag is a little bit short, but there is a lot of information on the internet about how you can do this. and there are lots of stores that will be able to supply you with whatever equipment you need. As you can see from the picture, I have only used construction plastic, duct tape, and some pneumatic pieces to make the vacuum bag. How you laminate "old-fasion" is well described here; http://www.surfersteve.com/glassing.htm
Step 8: Hot-coat
Sanding:
When the epoxy finally cures take the board out of the vacuum-bag. Trim off the excess overlapping epoxy, with a sharp knife. Gently sand down the rails.
Hot-coat:
Place the board on a stance, and apply a hot-coat. A hot-coat is a thin layer of epoxy. This layer will remove fill the fiberglass cloth and make it stronger and with a nicer finish. Apply a thin layer of epoxy on the rails as well. It is also possible to apply a thin layer of fiberglass on the rails, but I don’t see this necessary if you are using hardwood rails. The cumaru wood is water-resistant and very hard, it sinks in water.
Step 9: Adding Fins, and Inserts
Adding fins:
Normally a kite board has 4 fins, but you can add 8 or 0 if you like. When adding the fins. Attach a piece of string at the front center of the board. This sting will be used as a reference to the angle of the fins. Drill holes for the fins in the board. I made my holes 10cm from the end of the board. (see pictures) after drilling the hold jently apply epoxy to the inside walls of the holes to prevent water from contacting the wood. On my board I also added a brass cupping to make it look better and preserve the wood better.
Adding inserts:
When it comes to inserts there are many ways you can do this. You can order snowboard/kiteboard inserts from ebay. Or you can make your own. To make your own you can use a standart 6mm t nut, and tape the holes to prevent glue from entering. Here you can also use wax. I would still recommend that you buy inserts, the bought inserts are better than the improvised.
The inserts needs to be custom to your stance. To make them so. Place the bindings on top of your board and align them in the way you want them. Keep in mind to make them symmetrical and centered(obviously). Use a pen to mark where the inserts needs to be. To provide the correct stance.
Drill a hole where you have marked. Use a drillbit with the same diameter as the inserts. On my board I used 16mm. Place the inserts. And fill it up with epoxy. When the epoxy cures sand it flush with the board, and remove wax from the inserts. to make the insert extra tough you can add a little piece of fiberglass cloth on top of the insert(you will have to drill it gently to open it).
You can also make a attachment on the board. This is to have a handle you can hold the board with when laying in the water. Follow the same procedure as the adding of the inserts.
If you have any questions about the process just ask, I will try to answer as best I can. The vacuumbagging process is described in details many places on the internet, there are also several videos at youtube. I can also upload Boardcad designs if anyone needs it, but I reccomend that you design your own board its more fun!
I have started a Longboard(skate) project that will be uploaded soon, with more details on the entire process. Remember this technic can be used on many projects, its only the mind that stops you from new designs!
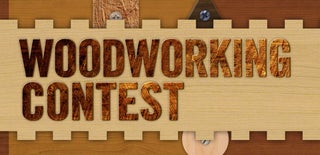
Participated in the
Woodworking Contest
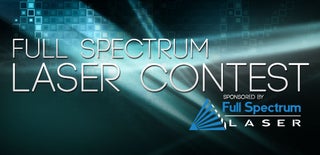
Participated in the
Full Spectrum Laser Contest