Introduction: Dining Chair From a 2x4
Before I even realised the 2x4 competition was going on, I had a spare 2x4 and had been watching far too many of Paul Sellers' woodworking videos, which had filled my head with delusions of being a proper woodworker. It struck me that there are plenty of "rustic garden chair from a 2x4" type guides around but not many making something a bit more refined-looking. I wanted a project to practise my carpentry skills on so I thought why not see if I could make a decent-looking indoor chair from a single 2x4? Here's how I got on.
Step 1: Planning
The first step was to figure out a rough design for the chair and work out if I could actually get that much usable wood from one 2x4. Here in metric-land, rough softwood timber comes in pieces about 2440 x 95 x 45mm, roughly 8' x 1 3/4" x 3 3/4". When I talk about "2x2" or "2x1" I mean the resulting size from resawing that wood into halves or quarters, though it isn't that exact size in inches.
The basic plan was to cut the wood into three sections: a 50cm piece I would resaw into two 2x2 for the front legs, a 90cm piece that would provide two 2x2 for the back and back legs, and a 100cm piece I would resaw into four 2x1 strips that would then form the rest of the frame- the seat sides, stretcher and back spindles/rails.
I figured out that I could get three ~30cm pieces, six 40cm pieces and three ~20cm pieces which would let me build the frame of a reasonably sized chair. The third image here shows the cut list to provide those lengths.
The part where I went totally off-piste was the back angle. The back of a dining chair should slope backwards at about 8 degrees, which sane people achieve by cutting a shape out of a larger piece of wood, but this would result in far too much waste. I had to figure out a way to take a single continuous 2x2 and introduce a shallow bend into the middle.
I'm new to the whole chair anatomy thing- the final image shows the words I'm using for various parts of the chair, which I may well be using incorrectly but it beats calling them "vertical back part" and "horizontal back part".
Step 2: Resawing
Step one was to cut the entire 2x4 into the lengths I wanted: 50cm, 90cm and 100cm. A tape measure, pencil and mitre saw made quick work of this.
Once I had the lengths I needed I had to resaw them into thinner pieces. Any sane woodworker would use a table saw to do this, but I don't have a table saw so had to improvise. I fitted a 4 tooth-per-inch blade on the bandsaw as a general purpose blade can't cut this thickness of wood without clogging. I also clamped a feather board to the table and clamped both ends of the fence to try and keep it cutting as square as possible.
It's important to get the cut in the middle of the wood so the two resulting pieces are the same size - to do this I made a short cut into one end, then measured the distance from the fence to the cut, and adjusted the position of the fence until the saw was going to leave the same amount of wood on both sides.
When resawing long pieces of wood on a small bandsaw you'll end up with the weight of the board hanging off the far end, which is bad news. If possible, find an assistant to support the wood coming out of the cut to avoid having to reach around the blade. I wouldn't advise resawing this way, but if you do do it, pay attention and be safe!
Once you've resawed to the width you need, cut the 2x1s down to the lengths from the cut list and you have your raw lengths ready for cleaning up.
Step 3: Plane Sailing
Cutting a thick piece of softwood on a cheap bandsaw with a coarse blade will probably result in wavy cuts. This job was no exception. I took the wavy wood over to a bench vise and planed down the cut surfaces until smooth. You could use a powered sander here instead of a plane, but be careful not to take off too much material.
Step 4: Fancy Touches- Back
After dry fitting the back together to see how it looked, I began to feel like I was just creating another boxy square design without any of those decorative flourishes that set fine furniture apart from its rustic and flatpack cousins. Before I started assembling the chair I decided to:
- Cut some cutouts from the spindles to make them more slender-looking
- Cut a slight radius into the top and bottom rails
To make the cutouts on the spindles, I made a template out of a scrap of plywood, used this to draw the cut lines on the spindles and cut them out on the bandsaw. The template for the top and bottom curve on the rails could be drawn freehand but I cheated and cut this one on the laser cutter.
I also clamped the three spindles together and sanded a slight radius into the ends with the nose of a belt sander, so they would be tapered slightly where they met the rails - this again makes them look a bit more slender, and also hides any slight misalignment as I was still honing my dowel-joint-making skills at this point.
Step 5: Fancy Touches- Legs
Continuing the little design touches, I decided to
- Taper the bottom section of the legs down to a smaller "foot"
- Chamfer the top parts of the legs into a pyramid so they don't just terminate in a square end
To chamfer the tops of the legs, I used a woodworking gauge to divide the top of each leg into thirds (like a tic-tac-toe board) and scribed a line 5mm down from the top edge, and cut the four bevels on the bandsaw.
To taper the bottom of each leg, I needed to cut two wedges out on adjacent sides. To do this I had to mark and cut one wedge, then mark the second one on the cut face. Each wedge is 150mm x 15mm so the foot is about half the area of the leg which seemed to look like the right proportions.
Step 6: Bending Over Backwards
This part was done more as a personal challenge to myself and to see whether I could make the chair from a single 2x4 worth of wood. The sensible way to make a back leg with a bend in it would be to trace the outline on a piece of 2x4 wood and cut it out. I only had two straight 2x2s which I needed to introduce a bend into, so I decided to cut them at an angle and rotate one of the pieces, so I could glue them back together with a lap joint at an angle.
The 90cm 2x2 wouldn't fit in the bandsaw and I couldn't reliably get a perfectly straight cut on it anyway. This is another part of the process which would have been much easier with a table saw. As it is, I had to clamp the 2x2 between two workbenches, and clamp a long straightedge to it at a 10 degree angle to guide the jigsaw. 10 degrees is more angle than I would have liked, but anything shallower would have made the cut impractically long - each cut was about 25cm long and took several minutes of painstaking jigsawing, but I ended up with a cut surface that was flat enough to glue up. These joints were the only ones that used screws, because just clamping them together resulted in the two halves sliding apart, so I drilled and countersunk two holes through each joint to accept wood screws that held the two halves in the right position while the glue dried.
Step 7: Starting to Assemble
With all the pieces made, it was time to start assembling. The easiest way to assemble a chair of this shape is to glue the back together as one piece, and the front similarly, then attach the two parts of the frame together with the sides of the seat and stretchers.
The first part to be assembled was the back. To make the dowel joints I'd drill two 28mm deep, 9mm diameter holes into the ends of the spindles and the sides of the rails, and glue a 50mm section of 9mm dowel into the joints. The holes were deeper than they needed to be to allow a little room for glue at the ends.
Having done this the hard way, I'd recommend drilling the holes into the ends of the spindles, measuring their position and drilling the corresponding holes in the rails, because drilling accurately placed holes into the softwood end grain was tricky.
Gluing the back together required a bit of ingenuity as I didn't have a single bar clamp long enough - I'd really recommend you figure this sort of thing out before starting as it's quite stressful trying to improvise clamping arrangements while the glue is drying!
I also drilled the holes for the stretcher, but didn't glue it up on its own. I made sure to drill the holes in the ends of the side arms of the stretcher so they were pointing straight forward/back in the chair, which made assembling the frame much easier than if they were drilled straight into the ends.
Step 8: The Final Stretch
Right. Take a deep breath and mentally prepare yourself. Lay everything you need out where it's accessible: a glue pot, spreader stick, lots of paper towel for wiping up squeezeout, enough dowels of the appropriate lengths and all the frame pieces.
Glue the holes in the stretcher, insert dowels and fit it together.
Place the back of the chair on the workbench facing up, glue all the holes and insert dowels. Glue the protruding ends of these dowels, and fit the stretcher onto the lower set of dowels. Glue up the seat sides and fit them onto the upper dowels.
Add glue to the exposed holes in the side parts you just added, insert and glue up the remaining dowels, and fit the front legs onto those. Take a breath.
Make sure all the joints are fully pushed together with as little gap as you can manage - a little persuasion with a mallet can help out, but don't go wild on it. Set the chair upright on its legs and make sure it's not crooked or twisted. You can add a strap clamp or bar clamps to hold it all together while it dries.
Admire the chair from all angles - this step is important.
Once this was done, I grabbed a piece of plywood and jigsawed a seat to fit over the seat sides with corners cut out for the legs. The idea was to upholster this with fabric and upholstery foam (inspired by, naturally, Paul Sellers' video on how to upholster a chair seat which came out when I was half way through making this chair) but I ran out of time for the contest deadline so for now a seat pad will have to do. And I was trying to make something that didn't look like garden furniture...
Step 9: What Did I Learn?
- Making furniture is tricky and time consuming. I've built working model aeroplanes in less time than this chair.
- Don't expect to be able to drill precisely positioned holes in pine end grain
- Just because you can resaw lumber with a bandsaw, doesn't mean you should
- 10 degrees is too much rake for a dining chair: it's nice and relaxed to sit on but you wouldn't want to eat at a dining table sitting in it.
Despite all this, a piece of simple everyday furniture from scratch is definitely one of the more rewarding things I've made, and I'm sure I'll build more in future. Hopefully this goes to show just how far you can make a 2x4 go with some ingenuity and a healthy disregard of practical limitations :)
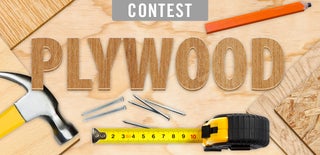
Participated in the
Plywood Contest
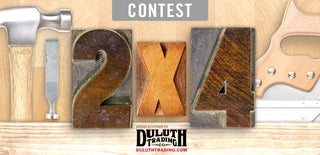
Participated in the
2x4 Contest
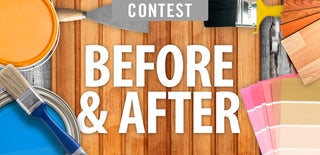
Participated in the
Before and After Contest 2016