Introduction: Dinosaur for Your Swing Set!
I wanted to replace a bench swing that had broken on my girl's swing set. The set itself is fine and all, but nothing to write home about. The bench was broken beyond repair and needed a complete overhaul. I felt like I could do something a little better than what was originally in place so I said hey why not a dinosaur. I figured a Triceratops would make the perfect dino for the project. Before I get a bunch of angry comments... I know... it's really just a Torosaurus in a different stage of development, but come on, science has already taken a planet, the Brontosaurus and who knows what else from my childhood.
Alright now I had an idea of what I wanted to build, but what materials was I going to use to construct a replacement? I had thought about making a simple bench from wood with two dinosaurs on the sides out of plywood, but I really wanted this thing to pop, so I decided to jump/dive right into fiberglass.
On a safety note. My girls are will be turning three soon they can use the swings by themselves, and I would not feel comfortable if this was a swing that they could self propel, walking behind something like this and getting hit by it while in motion would really make for a bad day. This bench was and is the only part of the swing that they need assistance to use, since I or another adult had to be standing there pushing them I figure there will be no chance for one of them to be on it while the other was walking behind while in motion.
Step 1: Find Your Project
So I kept looking at this sad old swing and figured it was time to get off my butt, put my Super Dad cape on and get to work.
Step 2: Design
I took the original measurements for the old bench and built my design around those so that it would fit into the original frame.
Step 3: Research
I wanted to make it out of fiberglass and had no previous experience with composites, where to start? Well there are many great related instructables on this site, and since my wife is AMAZING she got me two books for Christmas:
Composite Materials: Fabrication Handbook #1 (Composite Garage Series)
Composite Materials: Fabrication Handbook #2 (Composite Garage Series)
both by John Wanberg.
I also used the amazing great Google. All very excellent resources.
Step 4: Digesting the Research
Alright so for most of this article I've been using the term "Fiberglass" well.. while I did use fiberglass cloth in the construction using fiberglass on its own is sort of incorrect since this is a fiberglass composite. So here's a run through of the correct terminology. What this really is GFRP (Glass fiber reinforced plastic). The matrix I used was Polyester reinforcement.
The final product is actually a composite which is constructed and made up of the following. A chemical or mechanical bonding of dissimilar materials such as glass fiber and polyester resin, whose cumulative properties are superior to the individual materials... Awesome... say what?
Matrix is the liquid used for this project, polyester resin.
Reinforcement is the woven fiber used, one of the most common and what I used in this project was fiberglass, but carbon fiber,
Kevlar, etc... could be used.
Lay up is the process of building up multiple layers.
Laminate is applying materials to a mold.
If I misunderstood something from my research please leave a comment (polite) so I can correct it.
With all that laid out one of the things that should be understood about using a polyester matrix, is that you cannot use it on foam like you can epoxy. You can if you have some medium acting as a barrier between the two but seeing as this was my first attempt with the materials I didn't want to miss something and have my mold to dissolve mid lay up. Since I had no intention of making a duplicate I decided to go with a one of mold out of cardboard wrapped in packing tape. As far as ease of construction and cleanliness this definitely worked for me, however if you want a finished product with a little more detail and a lot less finish work I would recommend going with foam and epoxy.
Step 5: Supplies and Materials
Safety Equipment that is a must:
Respirator
Gloves I went with a box of Nitrile.
Safety glasses, but preferably goggles.
Tools:
Cheap brushes or a fiberglass roller
Measuring cups
Paint sticks
Orbital sander
Dremel with cutting disks
Detail sander (optional)
Heat gun (optional or necessary depending on your level of patience).
Utility knife
Putty knife
Hacksaw
Materials:
Fiberglass cloth for this project I used about 60sq ft
Fiberglass mat <1sq ft
Polyester resin I used about two gallons.
Bondo Filler
Bondo Fiberglass filler
Packing tape
Acetone
Cardboard
Four three foot lengths of 1/4 inch course threaded rod.
Four three inch 1/4 course thread hex bolts
Four 1/4 fender washers
Eight 1/4 washers
Eight 1/4 course lock nuts
Sharpies
3M 6inx24in Reflective Tread
Two 1/4 u-bolts for 1 1/2" pipe.
Step 6: Safety
Get a good respirator and plan on living in it, you can skimp out on all of the tools and materials on the list, but you only have one set of lungs. Polyester resin is pretty toxic on its own, but when you get to the sanding I still wouldn't trust just a dust mask. You're going to be making a lot of fine powder and getting glass in your lungs is not good.
Eyewear, I wore safety glasses for the sanding and cutting, but a pair of goggles would be a wise investment, the fumes from the resin can cause burning.
Gloves and long sleeves, getting any of this on your skin can cause burns.
Step 7: Creating Mold
I used a single piece of cardboard for the bench then built off of that. I measured, cut, and shaped cardboard until I had what I wanted for each piece. As you can see I shaped the tail with multiple pieces of cardboard, for the head I tried to keep it all one piece, I made the legs, horns, and tail separately then taped them on. For the eyes I cut a tennis ball in half removed the felt and taped the halves to the head.
Step 8: Prepping the Mold
As far as prep work I added the raised area between the seats because I figured with only a flat sheet of composite holding the two halves up would be too much stress on the base. Since all my research stated that resin does not stick to packing tape I did not wax everything down before I started.
Step 9: Glassing
Before you get excited and start mixing your resin precut your cloth, use the sharpest pair of scissors you have or can get. If you have any stringers carefully cut those out as best as you can.
Pre-measure your resin and hardener into separate cups. I was fortunate in that the garage was about 45f in the morning and got up to about 60f in the afternoon average humidity was about 35-45%. Since the hardener generates heat to start the curing process the cooler ambient temperature worked to my advantage as I was able to make larger batches of resin than if it had been summer. You can also use less hardener if you find that you're having trouble applying your mix before it begins curing. Also if it's curing too slowly you can carefully use your heat gun to help heat up the resin as it cures.
I pre-measured 20oz cups of resin into a larger cup and dropped the hardener into a separate cup. The directions call for 10 drops per fluid ounce of resin, I added 15 extra drops for anything that would get stuck in the cup. As you can see a little bit of hardener goes a long way. I counted out the first cup then marked it so I had a line to go off of for additional mixes.
For the first layer I painted resin over the portion of the mold that I was applying the cloth to then brushed the resin over making sure the cloth was completely soaked. For additional layers I just placed them on and brushed the resin over, if the resin had cured I sanded the surface down as close to the cloth as I could get then brushed the strips with resin as I applied them. My understanding is that you can sand down to the cloth on when adding additional layers because you want as little resin in between your layers of cloth as possible, but do not sand down to the cloth on your final layer. I used strips that were about 3" wide by 10"-12" long for the cloth. Make sure you add an extra 2" past where you want to cut.
I had to go back and take pictures of the process I used for the lay-up seeing as I was the only one with a respirator and I didn't want my wife to come out and take pictures during the process. You can see here what I was trying to go for in the lay up process.
One problem I did run into with the initial layer was that the weight of the front and back started pulling the ends apart, I eventually braced the ends up with some spare wood that I had, but this started after I had finished the initial lay up and right as the resin had started curing. All of this started pulling apart the cloth and created a lot of headache and extra finishing work later on down the road.
NOTE: If you're making a "one-of" mold don't get too attached to your previous work.
Step 10: Sanding, Filling, Sanding, Finishing
Once I finished laminating and everything had cured for a couple days, I flipped the dino over and started removing the cardboard. I had a lot of spots that were partially closed in, but nothing that I wasn't able to reach in and cut up with a utility knife. With the packing tape everything pulled away from the fiberglass with no issues.
If I hadn't been fighting the weight problems of the front and back and didn't have to work everything back just as it was just starting to cure I would have had a lot less sanding and leveling to do, but lesson learned, make sure your mold is reinforced and going to hold before you start the lay-up. I should have known better, but as usual I started working and got excited to see the final product.
I cut the excess around the bottom with the Dremel and a cutting disk and had no issues.
There were a couple blisters that I had to cut around and fill with the Bondo Fiberglass filler to patch up.
I sanded down what I could before I got to the fiber, added on an extra layer of just resin to help smooth things out. I then used Bondo filler to... you guessed it fill in the low spots. After that it was back to sanding, filling, sanding, primering, then seeing even more low spots, filling, sanding etc...
As for the Bondo, I measured out filler and hardener per the instructions and used my putty knife to apply it. Get it as smooth and level as you can and work quickly, it will save you a lot of sanding after application. If you are afraid of using Bondo or filler because of all the horror stories don't be. Use it per the instructions to fill in small gaps/dips and you wont have any issues.
I then measured the holes for the bottom mounts and drilled them out for the threaded rod. I folded a couple cubes of mat about 2" in size and ran the rods through those. With the cubes snug against the body I soaked them in resin so that I would have good support for the rods.
Step 11: Painting
I got everything to a point that I was ok with, at least for what this project was, I could probably have spent the next couple months filling and sanding until was perfect, but I figured for something that the kids are going to beat up and also that it was my first attempt at working with fiberglass I gave it a passable grade and went on to the painting
I bought spray paint for colors that I thought would be dinosaur looking and had fun with it. Painted the eyes, horns, waited for those to dry then masked and painted the body, masked around the mouth and seat area then painted. For the pupils I put masking tape over the eye, cut a circle and use a paint brush for the pupil. For the details I made stencils out of cardboard. At this point you should be seeing everything come together so take your time have fun with it. Since his home would be in the sand and I didn't want the girls rubbing the paint off of the floor or slipping I painted some 3M reflective tread the same red as the seats, cut two pieces to fit the floor and taped them down.
Step 12: Mounting
I bolted the supports to the body using the bottom holes. For the top I just used top holes of the supports as my guide drilled through the body and bolted it to the supports with the hex bolts. Where do the u-bolts come in? Well I found with the added rigidity of my new dinosaur the swing itself started to bind up when in motion. My solution was to add an additional point of articulation to the tops of the front two supports. I used the u-bolt to mark my holes, drilled them out, installed the u-bold and loosely put the two nuts on. Then cut out about a 1/4" section in between the bolt with a hacksaw. Took them out, put a plate on the back, reinstalled the bolts, put a plate on the front and bolted them down.
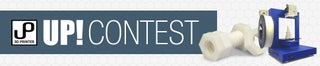
Participated in the
UP! Contest
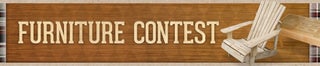
Participated in the
Furniture Contest