Introduction: Disc Sander
After using for years my laptop as flexible disc Sander through a supplied accessory, and securing it temporarily "a little here and a little there, I decided to DIY a disc sander fixing all recovery materials, to cost almost 0.
Before going in the description it is necessary to make a
WARNING:
ATTENTION: IMPORTANT MESSAGE:
Electricity is potentially dangerous. Don't do anything with it completely do not understand or do not have the slightest doubt about. Whatever you do, the result is your personal problem and you can't blame this instructable or its author. ' ' This is including personal injury, financial loss and any type of damage, including but not limited to the fall of civilisation and the total destruction of the universe as we know it '.
I RECOMMEND TO ALWAYS UNPLUG THE MAINS SWITCH, AND, AFTER CHECKING THE ACTUAL POWER FAILURE MAKE CONNECTIONS.
in other words:
ATTENTION: ANYONE WHO TOUCHES THE WIRES COULD DIE!!!
(this phrase is not a threat but it is only by way of warning, of course)
Attachments
Step 1: The Motor
the engine was recovered from an old dishwasher wreck.
First I disassembled the hydraulic part from the motor itself, and cut with a hacksaw and cut through the so-called "snail" in order to remove the impeller.
I removed all pieces of the rotor leaving integrates only the basis or support that goes to enter the pump through the pivot screw.
A heavy piece of wood (beech type) was used to create the disc, obtained with the bandsaw or jig saw.
In the Middle I run a hole that will accommodate the apical part of the post.
Step 2: The Disc
Contact glue PuTTY type I glued the two pieces together.
After a few hours I put the screws for a safer fixing, obviously by piercing beforehand, with a fine tip, to prevent sagging or cracking of the wood.
Step 3: The Velcro System
I opted, in my disc Sander, for a quick on-off sanding disc: the velcro system, which is already equipped with most discs that I got to see on the market.
I've got a velcro belt, of the type that also has adhesive on the underside and I covered the entire disc.
As you can see in the picture, I used velcro type complementary to that present on the lower surface of the sanding discs that I had provided.
The back of the plate has been resurfaced, for reasons "aesthetic" always with always hook tape.
Step 4:
After that I dedicated to the construction of the container of the motor with its support of the workpiece.
As material I used chipboard for construction and to support;
As protective material-electric parts cover I used a sheet of plexiglass from 1 mm fixed co of small screws.
Step 5:
After securely fastened with three screws on the front of the engine support, and have fixed the starting capacitor at the base through a simple hole the same diameter of the screw of the capacitor, I started to build the base of the workpiece.
As you can see in the first picture, it's a support that incorporates into it, through the fixing with screws, motor support, forming a single unit.
For the front cross, as he had to accommodate the lifting the hinge base plate, I preferred to use instead of wood chipboards for greater robustness.
As the base of the piece I used a MDF shelf that was coincidentally the right fit;
It was enough to run the channel at the swivel plate and fasten it in the right position.
When the base is lowered in its working position, you create in the bottom area a small Chamber that houses the sawdust, which, through a hole measuring approximately 5 cm, is extracted from a vacuum cleaner that I from time to time.
Since the pot turns counter-clockwise, I ran the hole in the right side of the lower Chamber.
Step 6:
To give greater stability and to mitigate any vibrazionial, I set of rubber along the bottom perimeter of the structure,
As I said, I used the plexiglass as a lid; of the pieces cut to size, fixed by means of small screws and connected with each other through a drizzle of hot glue.
Could not miss the power switch and power cord connections which was fastened from the inside with a plastic clamp to prevent inadvertent sfilasse for some traction.
In a final stage, not documented by photos, I colored Matt Black all over, except the base.
I preferred it in transparent Instructables.com community, it seemed a little more spirit "Spartan" typical of us instructables-mens.
Thanks for your attention, I hope I was of help to anyone, and if you vote my realization it will be greatly appreciated.
Hello from Torx
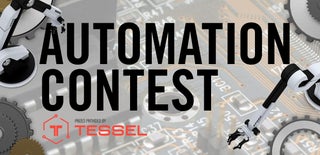
Participated in the
Automation Contest
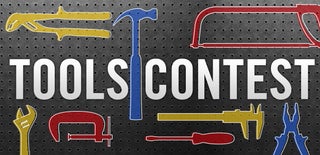
Participated in the
Tools Contest