Introduction: Easy and Beautiful Cutting/cheese Board
In this instructable (my first), I will show you all how to build a simple yet beautiful wooden cutting board that is very easy to make without sophisticated tools. Speaking of tools, the only complicated tool required is a saw that can cut nice thin and straight strips of hardwood. There are a few different types of saws that can get the job done, but for ease of use, efficiency, and possibility for error, I would suggest using a table saw for cutting your hardwood. A good solution for people that don't own a table saw themselves would be to either find a friend/ family member that can help, or even to go to your local home improvement store where they might rent one out. In the end, some handy tools for this project are as follows:
Table Saw (cutting strips/ trimming the finished board to size).
Plane (for levelling the board).
Orbital Sander (for sanding out saw marks/ ruts and to get a nice finish).
*Drill/ Driver (for any optional extras like handles, cleats, etc).
Clamps (Get three or more wide jaw clamps that can span the width of the board).
To get a nice looking board, it is very important to select your woods with care. If you decide to make a thinner cheese board that won't be used for chopping etc, then the builder can get away with using cheaper medium hardness woods. This does NOT mean that a nice product can be built with construction grade softwoods like pine, a good wood that is cheap, but still hard enough is aspen. Aspen can be bought cheaply, looks good oiled and has a decent hardness to it. If making a cutting board, then your choices get slightly more restricted, I like to use very hard woods such as maple, blood wood, walnut, and purple heart. A particular favourite of mine is purple heart due to it's hardness, variety in sizes, and lower cost compared to traditional hardwoods like maple, plus it looks really nice stained. One thing to note with purple heart, however, is that the purple colour is an oxidation forming on the surface. To get it's beautiful characteristic colour, it can be helpful to let the wood oxidize for a few hours after sanding before applying any finishing coats to let it redevelop that colour. Another tip is to select wood with similar qualities, as realistically no air can be devoid of any moisture, different woods swell and deform at different rates, so if you choose wood species with drastically different swelling qualities; there is a chance that the board might swell to a point where it wobbles before you can get the oil on. A little extra expense in selecting the right woods for the board is well worth the trouble especially when it's time to finish the board. For my board, I chose to use some interchanging strips of blood-wood, and hardcore maple with a large slab of blood- wood in the centre. The client also wanted the small brass cleats in the photos at either end of the board. Along with the wood, you will also need some consumables:
Glue (for the lamination of your strips).
Wood (check Wooddatabase.com for information on different species).
Sand paper (Varying grits anywhere from 60-320).
Shop Towels (for applying oil/ cleaning up, paper towels can also work in a pinch).
Gloves (latex or nitrile gloves for oiling and gluing the wood).
Without any further ado, here's how to make a nice cutting board.
Step 1: Getting Ready to Glue
Cutting the strips is quite straightforward. Come up with the dimensions of the board and figure out how many strips you want and the layout of the board. Once you've cut the strips, lay them up to visualize the board, and finalize the pattern, what I then like to do is clamp it up, check the gaps, and figure out where the strips might bend or twist. This step is important because it shows you where the most tension is required and the best clamp placement spots.
Step 2: Laminating the Board
This step is where time management become crucial, Wood glue sets up fairly quickly, so it's important not to doddle. As for glue, I prefer Titebond 3 for it's water resistant qualities and strength. I first lay all of my strips side ways and apply a good bead. I then use my finger to distribute the glue all over the strips. The amount of glue can be tricky, for too little can cause a weak join, and too much can be a pain to clean up/ sand. I find that applying enough glue to fully cover the surface in a fairly thick coat of glue, however, a little does go a long way, so it can be helpful to apply, smooth then determine if anymore is needed. After the glue is applied, quickly square up the edges a speed square or some other 90 degree piece and apply the clamps. While clamping the board make sure that the sides don't lift up and that all the strips are still level and flush with each other. Finally, put your weights on the board and let it dry (I leave the glue overnight).
Step 3: Planing Down the Surface
The next step is to plane down the high spots of the board to create a level surface free of knolls etc. At this time you may notice some cracks that weren't filled with glue. I like to quickly fill them with glue and let them dry.
Step 4: Sanding and Finishing the Cutting Board.
This is the most rewarding part of the project. After the glue in the cracks dries, I square up either end with my miter saw, however, this can be accomplished with any saw. I then use 60 grit sand paper to sand out any imperfections, after that is done I work my way up the 220 with the sander, then switch over to hand sanding with 320. Once all the sanding is done, I prepare the surface for oiling. To do that, use a clean, oil free cloth or even paper towel to remove any dust from the cutting board. It can be helpful to use a damp cloth to pick up the dust. Once the surface is prepared, rub in several coats of mineral oil, and install any optional extras. Some people like to install handles etc, but the client wanted small brass cleats as this board is destined for their boat. I find that especially with brass screwed it can be simpler to use two part epoxy to install the cleats with screws dipped in epoxy. Once the epoxy dried, I refinished the cleats with 220 on machining oil for a more used look/ less glossy look.
Step 5: Enjoy the Finished Product.
Since this cutting board was constructed of high quality hardwood, it should last for years with minimal maintenance. The only real maintenance is an occasional coat of mineral oil as the oil layer fades over time, and a resurfacing to get rid of any scratch marks.
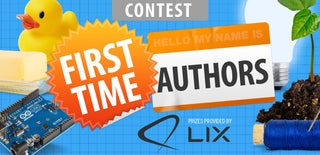
Participated in the
First Time Author Contest 2016
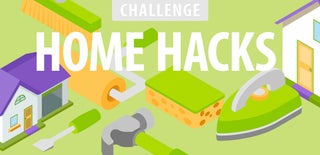
Participated in the
Home Hacks Challenge