Introduction: 555 Timer and LED Repair for Inflatable Display
My wife bought this inflatable lawn decoration last year, but unfortunately last year's severe winter was too much for it. The snowmen worked all Christmas season but when it was time to put the decorations away, we had snowstorm after snowstorm and I couldn't get to the deflated decoration to put it away. When the snow finally thawed, I plugged it in to make sure it still worked, and it inflated as I expected. I folded up the display and put it away for the year. When I unpacked the snowmen this year, one of the lights would not light up. I broke out my multimeter and tested the leads going to the PC board, and it was receiving 12v so something was wrong with the circuit. I cut the wire and brought the part inside to work on it in my workshop.
<
Step 1: Surgery
I tried to get the original circuit working, but it was very corroded and rusted. I used some rubbing alcohol to clean off the corrosion so I could see if there were any glaring problems. I didn't see anything obvious, so I tried hooking it up to some 12v power.
Step 2: Power Adapter
After I cut the wires of this LED board, I needed an easy way to connect it to a power supply. I had a little screw-terminal and a 5.5mm barrel jack connector. I also had a scrap of perf board that was just the right size. I connected them all together and now I can easily connect a standard 12v AC adapter.
With the power connected, I poked around the board with my multimeter, testing voltages. Then I tried touching a jumper wire to the board in a few places to see if I could at least make the LEDs light up steady, but I didn't have much luck. When the LEDs did come on, they were very dim and they would flicker quickly.
I unplugged the wire and plugged it back in, and suddenly the light came on again, but it only ran the light pattern once. If I unplugged the wire a few times and reconnected the power quickly, I could occasionally get the lights to flash, but it always stopped after one loop. I decided to build a more reliable circuit to replace this one.
Step 3: New Circuit Design
Since the original circuit was made with surface mount devices (SMD), and I was replacing everything with through-hole devices, I had to simplify the replacement a bit to make sure it would still fit in the 52mm holder. The original circuit had some sort of microcontroller, that would switch between several different patterns but I decided I just needed 2 states for the LEDs, dim and bright. I took a 555 timer circuit from this site and modified it a bit.
I used this site to determine how many LEDs I could have in an array and still have them be bright with the 12v input voltage. I decided that I would use 4 arrays of 3 LEDs connected in parallel to the 555 timer to blink, and another 2 arrays of 3 LEDs that would stay on. This would give me the dim and bright modes I was looking for.
The attached PDF is an updated version of the layout I used in this Instructable. After I printed the circuit, I realized there were a few things I would have changed, like larger input voltage pads and a few upright resistors to save space.
Parts:
18 LEDs
555 timer
7 x 1k ohm resistor
2 x 1m ohm resistor
1uF capacitor
Attachments
Step 4: Transferring the Circuit
I am still trying to perfect this step. I just cut out the design and hold it tight into the corner of the copper board before I iron it onto the board. I leave enough paper on the one side of the design that I can keep my fingers out of the way because the heat will creep through the board and burn you.
I print the designs out on a regular laser printer. If you don't have a laser printer where you will be doing the etching, make sure you print a few extra copies of the design.
I haven't found the correct amount of heat and pressure yet. I have had a few transfers that came right off the paper and perfectly covered the board, but the majority have been a little thin here and there and needed to be filled in with permanent marker. If the paper starts to scorch or burn, you've gone too far. I usually use the pointy end of the iron to put a little extra pressure on certain parts of the design.
I usually have to fill the design in almost entirely with an ultra fine permanent marker. The toner often comes off on the tip of the marker, so I have to scribble the marker on a piece of paper to keep the ink flowing.
Step 5: Etching
I have only been etching circuits for a short time, and I haven't done much experimentation with different types, but this method has been working well for me and it doesn't waste a lot of etchant.
Step 6: Reusing the LEDs
I usually use desoldering braid to remove parts but I decided to try a new vacuum pump and I really like it.
I used to think these little desoldering pumps were gimmicks, but I was really surprised how well it works and how easy it is. If you solder, you know that without flux, it can be very difficult to get the solder to stick where you want it. It doesn't take a lot of suction to remove all of the solder pooled on top and most of the solder that dips down below the surface of the circuit board. If you do it right, the parts just fall right out of the board.
Step 7: Drilling and Soldering
I use 2 different sizes of tungsten carbide cutters to drill the holes in the board. I drill a pilot hole from the copper side and punch through the other side, then I widen the hole from the back with a larger bit. Be careful not to push too far or go too deep from the blank side because you can push the copper right off the other side of the board.
I used a little hot glue to cover the 555 chip for a little waterproofing. I also hot glued the top ring down to keep everything in place.
Step 8: Splicing Wires and Reinstalling
ICs like the 555 timer are very sensitive to reversed polarity. I have ruined chips before by hooking circuits up backwards, so you have to take extra care not to get the wires mixed up.
I cut the 2 wires to different lengths so that the splices would be offset and I wouldn't have to insulate them from each other. I twisted the wires together in an inline splice like this guide explains, but to relieve any stress from the joints, I tied a knot in the wire a little further up the line.
I soldered the wires together to ensure that they wouldn't come apart. I could have used heat shrink tubing to cover the connections, but I decided to wrap everything up in electrical tape instead. I was more concerned with everything staying together than in making it look pretty, and I was already doing these steps outside so I opted for the simpler solution.
Step 9: Finish
The end result worked better than I hoped. The lights are as bright as they used to be and the dim blinking matches the style of the other lights enough that it isn't too obvious that it is different. Now the red snowman looks too dim and I might have to make another repair board to make it brighter!
Step 10: Bonus: Previously Repaired AC Adapter
When we first got this decoration, we immediately set it up on the lawn with the included stakes. The next morning, I found it halfway down the street, wedged under a parked car. The short 4 inch stakes were no match for the strong winds. When it blew away, the plug was damaged and I had to do surgery on the AC adapter pack to make it work again.
I used a plug from a broken oscillating fan, soldered to remains of the plug terminals inside the adapter, then I wrapped the brick with electrical tape and hoped it would hold out the rain. The fix held and still works a year later. I bought 12 inch tent stakes to hold it down and have not had a problem with the wind since.
UPDATE:
I recently had to make another repair on these snowmen. The power supply got soaked in a heavy rain and I had to replace it. I made another Instructable about the process.
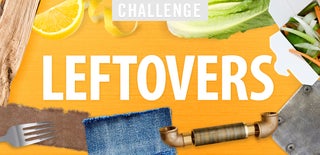
Participated in the
Leftovers Challenge
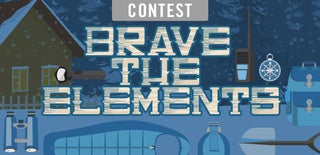
Participated in the
Brave the Elements Contest
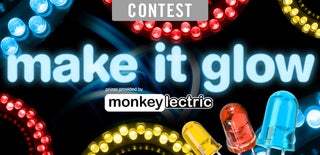
Participated in the
Make It Glow! Contest