Introduction: Flat File Base
In a previous, paper-based age, flat files were important professional furniture for architects, engineers, and artists. They kept blueprints and drawings uncreased and wrinkle-free in wide, deep drawers that pulled out all the way. Nowadays, flat files have evolved into a hipster design accessory -- Pinterest ideas abound! People use them to support drafting boards, set them up as coffee tables, or, occasionally, use them for actual print storage.
My wife is a graphic designer and letterpress print artist. She has a wide-ranging portfolio of prints new and old, as well as different paper stock. It had been stored in plastic totes under our couch, but with the rental of a new studio it was was time to clean out the apartment and get those papers in their proper place.
She found a great deal on a flat file on Craigslist. It is a beast -- nearly four feet wide, three feet deep, and super-heavy. It's also not that tall, so we needed to elevate it up on a base that would bring it up to table top height, add some extra storage for art supplies, and make it easy to move around. The solution was a simple plywood cabinet on casters with deep drawers. The project took about $125 (could be well cheaper if you made some different material/caster choices) and 6 hours to make with simple tools. I did the whole thing with just a circular saw and a drill; for faster, more accurate work, a table saw would be very helpful.
You will need these materials:
- 1 sheet of 1/2" plywood
- 1 sheet of 3/4" plywood (if I was doing it over I would do it all in 3/4" plywood)
- 4 casters, two locking; the dimensions in here are for 4-1/2" casters
- 16 1-1/4" x 1/4" dia. machine bolts for caster mounting
- Screws (I prefer Spax brand #6 wood screws made for going into edge grain of plywood without splitting)
- Wood glue
- Drawer slides
You will need these tools:
- Circular saw
- Drill and impact driver
- Square
- Clamps
- Measuring tape
Step 1: Building the Carcase
In cabinetmaking, the carcase is the 5-sided "box" for a project, be it a kitchen cabinet, a dresser, or whatever. There are dozens of ways to build a carcase, but they boil down to two main methods: frame and frameless. As plywood has evolved and become cheaper over the last 50 years, frameless methods have become more and more common. This involves joining plywood panels together with rabbetted corners, glue, and/or Kreg-style pocket screwing. I chose to do much simpler butt-joints to save time and because this was a utilitarian studio tool, not a fine piece of furniture.
The carcase for this cabinet has a footprint of 45" x 33-1/2", and is 9-5/8" high. This was calculated to fit inside the stamped-metal rim underneath the flat file, which would keep the base from slipping out, and, once it was mounted to casters, bring it up to precisely the same height as the neighboring desk. Adjust your dimensions to fit your flat file accordingly.
I made the top and bottom out of 1/2" plywood to save money; in retrospect, that was a mistake. Use 3/4" stock -- the flat files are too heavy for thinner material. It is not in any danger of collapsing, but the carcase does deflect some around the casters. All of the dimensions I will give assume a 1/2" top and bottom; adjust accordingly.
Cut two sheets at 45" x 33-1/2" using a circular saw with a finishing blade and a clamped straightedge for nice clean cuts. It's best to go ahead and drill bolt holes for mounting your casters at this point, before the whole thing is assembled. Cut three rib pieces at 33" long by 8-5/8" wide using the same methods. Cut a back at 8-5/8" wide by 45" long.
Screw and glue the three ribs to one of the large sheets, one flush with each edge and one in the middle. Pull them flush with the front edge so that they are 1/2" in from the back edge. Put the back on, filling in that 1/2" gap and securing through the bottom and into the back of each rib. Especially if you are using lower-grade plywood, it may take some wrestling to get the pieces flush and straight.
I use Spax brand #6 trim-head screws, which are specially made to join plywood and MDF without splitting or pre-drilling. If you are using regular drywall screws, make sure to pre-drill with an 1/8" bit and countersink head.
Step 2: Drawers!
The carcase is 45" wide and 33" deep overall. From the 45" width, subtract 2-1/4" -- the width of 3 3/4" thicknesses of plywood that make up the sides and middle divider -- and you end up with two clear spaces that are 21-3/8" wide by 32-1/4" deep. The drawer slides I got are standard big orange box store stock, specially made for long extension. They take up a 1/2" on each side, which leaves 20-3/8" width for the drawers. They also are only 22" long, meaning they can't extend far enough to take advantage of the full depth of the carcase. So, that leaves drawer footprint of 20-3/8" wide by 24" deep.
Use a circular saw and straightedge to cut two pieces of 1/2" plywood to 20-3/8" wide by 24" deep. Cut four sides that are 8" high, with lapping butt-jointed corners. Secure three sides to the bottoms and to one another with glue and screws. In the fourth side, cut a 1-1/4" deep by 4" wide notch out to act as a handle. To make accurate, square crosscuts with a circular saw on narrow pieces of wood, just clamp down a Speed Square as a guide.
To attach the sides, follow the directions on the package. Generally, you'll want to slide the slides apart, and secure one side to the carcase and one side to the drawer, with the front end of each half of each slide aligned slightly back from the front edge of the drawer or carcase. Each brand of slide will have its own setback/alignment directions. To ensure your slides are straight and square (very important; otherwise your drawers won't fit) cut a strip of plywood to act as a spacer block when screwing in the slides.
Step 3: Casters + Assembly
With the drawers in, you can now glue and screw on the top -- make sure to mark your centerline on the top piece so it hits the center rib dead-on. It may take a bit of persuasion to land just right.
Through-bolt your casters on. The rear ones may be a bit tricky to reach. Insert the drawers, stand up the cabinet, and lift the flat file on top. Put the locking casters in front, where you can reach the brake.
I used the rest of the 3/4" plywood to make a top for the flat file that could be used as a work surface. I embedded 8 neodymium magnets, countersunk and secured with Gorilla Glue, to help keep the top in place. It sort of worked -- bigger magnets next time!
Now, the whole thing easily wheels out into the middle of the room to operate as a work surface for cutting and mounting tasks or as a secondary desk.
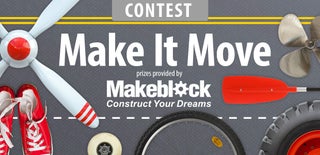
Participated in the
Make it Move Contest 2016