Introduction: From Scraps to Marking Gauge
Lately, I've found myself on a fine woodworking kick. The deceptive simplicity and relatively forgiving nature of wood has a certain appeal; as does the chance to develop new skills. From what I've found, a point is reached in woodworking where pencils and rulers become less effective and a new set of tools are needed. One of those tools is the marking gauge.
A marking gauge is a tool designed to follow the edge of a piece of wood and cut a fine line some set distance in from the edge. It's especially useful for marking dovetails, but any time you need a line that runs parallel to an edge; the marking gauge should be the first tool you grab.
There's only one critical dimension on this project (one face must be flat). Because of it's simplicity, the low cost of materials, and how elegant the final result is, this is a great beginning project for someone interested in exploring fine woodworking.
You can see in the photo's above the prototype that I built first. We'll be pulling some ideas from that for this build and improving on it significantly.
Tools Needed
Hand Saw
Hack Saw
Clamps
Small Carpenters Square
Drill
Various Drill Bits
Chisel
Hammer (Ballpeen is optional)
Sandpaper
File
Sharp Knife
Supplies
Scrap wood
1/2" Square Stock
A finishing nail
glue
1/8" Rod or Dowel (material is irrelevant)
Epoxy and/or CA glue
Wood Finish (your choice)
Rags
1/2" Brass Plate (optional, but nice)
Thumb screw and bolt
Step 1: The Glue Up
I happen to have a few scraps of wood from a project I just finished up. Any wood will work fine but for a small project like this, it's fun to use something exotic. The local woodworking store sells off-cuts at $3 USD per pound, it's a great way to experiment with different kinds of wood.
Once you've selected your pieces, glue and clamp them together. Make sure that one large face is relatively flat. It doesn't have to be square to any of the sides, but it does need to be flat. After the glue dries, take a piece of sandpaper; set it down on a flat surface abrasive side up, set your work piece down and sand away. Just make sure to keep even pressure.
Step 2: Cutting to Size
Using a saw, cut the marking gauge to size in all the appropriate dimensions. For those who fall into the type a crowd, about 4 inches long, 2-3 inches tall, and about an inch thick will give a good final result. Not to big, not to small. For everyone else, just eyeball it. I ended up having to cut a few edges off along the length as well. You may or may not have to do this.
And don't worry about keeping your edges square unless you want to, this is the woodworking equivalent of free verse: No rules!
Step 3: Cutting the Hole, and a Tool Is Born
After everything is cut to size, it's time to start making this piece of wood into a marking gauge!
I've cut my half inch square stock down to size (about 10 inches) and use it as a reference for where I want the hole to be in my marking gauge. At this point it's probably important to talk about how a marking gauge works, as that will help you understand why things are done a certain way.
The basic idea is that instead of a pencil or pen, a marking gauge uses a blade or awl to cut a fine line in the wood. Having a longish, flat face means you'll have a straight line, and it's important to make sure the bar that holds the blade or awl is set high enough up the marking gauge so you can hold the marking gauge firmly against the piece you intend to mark.
With that said, make a mark in the center of body and roughly 2/3 of the way up and you'll be fine. You can see in the first photo that I used the square stock to check the position of everything. Happy with that, I drilled a pilot hole using an 1/8" drill bit and then enlarged it with a 3/8" drill bit. Using the drill makes the next part much easier.
A good fit around the square stock will make for an accurate gauge, so take your time here. I used a half inch chisel to carefully cut away the excess wood around the hole until it was squared up and fit snugly around the square stock. A few passes with a thin strip of sandpaper gave a great fit.
Step 4: A Little Bling Serves a Purpose
Laminates, for all their advantages, do have some flaws. One of them being a tendency to break along the glue joint. Yes, glue is stronger than nails or screws but it also tends to be less forgiving. One of the best ways to add strength to a laminate is to add some form of mechanical connection. In this case, we'll be using brass rod and epoxy to give this a little bling and a lot more strength.
There's no science behind where the pieces go, I just made a few marks until I was happy with their position and drilled some holes. I'm using 1/8" brass rod, so I used an 1/8" drill bit. Two go through the face, and two go through the bottom as well. To prove that I didn't use a drill press, check out how skewed my exit holes were in the last picture compared to the entry holes in the second to last picture.
The choice of material for these pins is irrelevant. I chose brass because it would look great when sanded and finished, but wooden dowels, aluminum rod, steel, etc would work just fine.
Step 5: Cut, Glue, Peen, Repeat
Brass is a fairly soft metal and a hack saw will make quick work of it. Cut the pieces to rough length making sure to leave some extra and then sand all the pieces with coarse grit sand paper. This gives the epoxy a bit more surface area, and cleans off anything that might prevent a strong bond.
Mix up some epoxy, following the instructions, spread a little onto one of the pieces and press it into place. Use a hammer if needed. I used five minute epoxy which I don't recommend as it sets up to quickly. If you are using five minute epoxy, mix a fresh batch for each piece so you'll have enough time. Worst thing would be for the epoxy to kick while you're still sliding a piece of brass rod into place... I know this from experience.
After the epoxy has cured for at least a day, use the hack saw to trim the excess away. Then use a file to file down the material until there's only a little bit sticking up above the surface of the wood. Now use the rounded side of a ballpeen hammer to mushroom the brass out.This is entirely optional, but it gives a little extra holding power. When you're happy with the result, file the brass until it's flush with the wood.
If you don't want to peen the brass, simply file until the brass is flush with the wood.
Step 6: A Touch More Bling Please!
The hardware store by me had 1/2" brass plate for sale, and I thought it would be really cool to add this onto the bar to help protect the wood from being damaged by the set screw. A bit of epoxy and some clamps left me with a nice looking piece of brass glued to a 1/2" piece of poplar. A file made quick work of the squeeze out and cleaned up the edges nicely.
I left the brass short of the end, because I didn't want it to interfere with the pin. In hindsight I should have put the brass all the way to the end, as it looks kind of silly to my eye now.
Step 7: Add the Set Screw
I used a 1/4"-20 thumb screw and a 1/4-20 nut as my set screw because I had it lying around. Use whatever size screw and bolt you'd like.
Center your drill bit directly over the top of the square hole you cut a few steps ago and carefully drill a hole down. Try to keep this as straight as possible. Now the really tricky part:
We need to make a recess for the bolt to fit into. This is partly for aesthetics, but mostly, it makes for a stronger glue joint. Use a drill bit that's just a bit larger than your nut and carefully, very carefully, drill the recess. Don't go too deep and try not to let the drill bit catch and dig in.
If your hole is slightly off-centered like mine is, use a sharp knife to carve away the extra material. Then glue the bolt into place. I ended up using CA glue, as I had run out of epoxy at this point and it seems to be holding up well.
Step 8: Putting the Mark in Marking Guage
There are a few different camps when it comes to marking gauges, and like anything else on the internet this has resulted in many an unnecessary argument. It all comes down primarily to how the gauge actually marks the wood. Some people prefer a knife-blade style gauge, some prefer a pin, and some prefer a round gauge. It's ultimately you're choice, and all three accomplish the same task.
This is a pin style gauge, and the pin is simply a finishing nail with the head snipped off it. Once the head is off, I fit it into the drill chuck and then sharpened it using a piece of 180 grit sandpaper.
I used a 1/16" drill bit to drill a pilot hole near the end of the square stock as I didn't want the wood to split. The nail just fit snugly enough that it won't come out through normal use, but I will be able to push it out if it needs sharpened or replaced.
Step 9: Shaping, Sanding, Sealing
If you'd like, use a file or sand paper to round over the edges so the gauge will feel comfortable in your hand. Once you're happy, it's time to start sanding. I worked my way from 180 grit through to 400 grit and decided to stop there. The woods I used (bamboo, bubinga and zebrawood) are very beautiful woods, which is why I went up to 400 grit. had I used something like oak or pine, I would have stopped at 220. Go as high as you'd like, but remember this is a tool. Tools are meant to be used, not looked at. Don't make it look so nice, you're afraid to scratch it up!
For my tools and work surfaces, I tend to use danish oil. It's easy to apply, makes the wood look nice, and it doesn't stink like some other finishes. It's personal preference, but make sure to wear gloves and the appropriate safety gear (IE: respirator) and dispose of your applicator properly. I use old t-shirts to apply my finishes, and just simply rub it into the wood. Two to three coats should be enough. After it dries, I use a bit of beeswax polish and rub that in as well.
Step 10: You're Done!
You did it! Now you can mark straight lines to your hearts content!
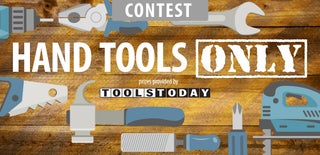
Second Prize in the
Hand Tools Only Contest 2016