Introduction: Fully Plywood Guitar AKA How to Annoy Purists
Plywood gets alot of stick in the guitar world, being reserved for mostly only the cheapest guitars. However after much searching on the internet I have concluded it doesn't matter what an electric guitar is made from as much as many people might think, if it's well made and setup at least.
I thought I would attempt to improve plywood's poor reputation and to really hammer home the point I decided to make the neck and fretboard from plywood too, which as far as I can tell hasn't been done before (multilaminated necks have been but they appear to have the grain all in line which disqualifies them from plywood status)
The short video is my friend Joe playing the guitar (Tbh I can barely play) and the long video is the whole building process.
Step 1: Materials and Tools
Tools used:
- Bandsaw- A jigsaw or coping saw would also work, just take longer
- Circular saw- Or handsaw
- Fret slotting saw- Apparently a junior hacksaw works for this, I have a little dremel attachment that worked ok
- Plane- At least as large as a No.4, I used a No.7 which is an amazing tool
- Chisels (Sharpened!) and mallet
- Sandpaper- A range of grits
- Files, Rasps, Sandpaper glued to a flat piece of wood etc.
- Drill and bits
- 1 metre ruler or tape measure
- Stanley knife
- Clamps
- Set square
- Vernier calipers
- Router- not essential but probably the most useful tool
- Straight edge- I used a spirit level
- Soldering iron
- PPE!
- Workbench with vice
A lot of these tools aren't essential and you can make do without, but all the tools makes life far easier.
Materials:
- 1/4 sheet of 12mm HARDWOOD plywood (2ftx4ft)
- Glue- PVA and superglue
- Something for the nut
- Hardware:
- Tuning heads
- String retainers/trees
- Screws or bolts with threaded inserts to attach the neck to the body
- Pickups
- Bridge
- Control knobs
- Fretwire
- Trussrod
- Wireing:
- Potentiometers for volume and tone controls
- Jack socket
- Switches
- Self adhesive copper foil- to line the control cavity with
- Guitar strings
- To avoid having to cut the fret slots you could buy a preslotted fretboard
- Control cavity cover- sheet of plastic or something
Step 2: Design Decisions, Cutting and Gluing
- Body shape
- Electric guitar bodies tend to be smaller than 340mm by 440mm so that's how big the body pieces should be cut, unless you want an oversize body.
Glue and clamp the body pieces together, I didn't have many clamps so screwed it all together around the edges, though far from ideal it seemed to work ok.
- Guitars are normally about 42mm thick but it doesnt really matter, I used 3 layers of 12mm ply which gave 35mm thickness.
- Number of frets and scale length
- This will determine how long the neck is made. Enter your scale length and number of frets into a fret position calculator (https://www.stewmac.com/FretCalculator), the distance from the nut to the last fret plus about 200mm is how long the wood for the neck must be cut.
- I used 24 frets and a 650mm scale length (approximately the standard 25.5inch) which gave 487.5mm to the 24th fret. I cut the wood for the neck (487.5 + 200 + a bit extra) 700mm by 25mm.
- 6 layers are required to make up the width, plus a few extra layers just at the headstock.
- I glued these together in 3s, to make two halves which I later sandwiched the trussrod between.
- I made all straight cuts with my brothers fancy new circular saw, but a panel saw would work just as well. The neck pieces need to be cut as straight as possible though.
Less wordy cut list:
- 25mm by 700mm - 6 of
- 340mm by 440mm - 3 of
Step 3: Shaping the Body
You need something to cut around. I made a full scale printout of a guitar I wanted to copy but you could draw it freehand, or a combination, use a printout but modify it. I highlighted the outline as it was blurry.
Cut around the outline, a bandsaw is ideal but a jigsaw or coping saw would also work.
The saw marks need to be removed with sandpaper and files. A bobbin sander or sanding drum in a drillpress is ideal but the more manual approach is fine, just longer.
The edges need to be shaped. A router with roundover bit is easiest, but files and sandpaper would also work, or perhaps a belt sander. Now would also be the time to add any ergonomic contouring if desired, I like the simplicity of without though.
Most plywood tends to have voids in it, now is a good time to fill these. With sawdust and glue or my prefered method of applying superglue then sanding over it while the superglue is still wet, then repeating till filled and smooth, this only works for smaller voids.
Once you are happy with the shape and how well it is sanded the body is ready to start being finished. There are many to choose from: Oil based varnish, water based varnish, spray laquer, hardening oil (eg. tung oil, tru-oil, Crimson Guitars do a guitar finishing oil). Stains should be applied before the finish if desired.
So choose your favourite finish or whatever is to hand, I used some oil based floor varnish which dries very hard. Apply coats repeatedly till you're happy with it.
Step 4: Installing the Trussrod
Before marking or cutting anything the fretboard face of each half of the neck should be planed flat, check this with a straight edge.
I think this method of installing the trussrod is unconventional though I am fairly certain it's a good idea, and seems to have worked perfectly well so I recommend it, it avoids a skunk stripe or having to have a separate fingerboard.
Using a router is by far the easiest way of making the slot for the trussrod, however some careful chiseling would probably work, or maybe a router plane (these can be made with a chisel and piece of scrapwood quite easily), which would be alot more quiet and pleasant to use than an electric router too.
The position of the trussrod needs to be marked so that the trussrod adjuster approximately lines up with the nut. The trussrod should be about 6mm below the surface of the fretboard face of the neck.
Once the trussrod slots are cut in both halves of the neck and you are happy with the fit, glue and clamp the neck together, ideally using more clamps than I did.
It is important to draw on the fretboard the position of the nut so you dont forget which way round the trussrod is or accidentally cut into the trussrod while shaping the headstock.
Step 5: Cutting Out the Pickup and Control Cavities
The centre of the body must be found, this is done by marking the centre of where the neck will be attached and by marking the middle along various points along the body then averaging them out with a straight edge.
The pickups should be mounted perpendicular to the centre line, unless you have chosen a telecaster style pickup then it is at an appropriate angle.
The pickup position must be found, I made the neck protrude into body by 68mm (it joins at the 19th fret) so the neck pickup will start just beyond that.
To position the bridge pickup the bridge position must be found. For mine, the 19th fret is at 433mm from the nut, to the bridge should be (650 - 433) 217mm from the end of the body, where the 19th fret is. I put the bridge pickup 50mm centre to centre from the bridge, it could be put closer or further, a little closer would have possibly been better.
With the pickup cavities marked out, use a drill with a depth marker on it to remove the bulk of the wood to a depth just beyond the pickups depth. This isn't essential but makes it easier.
Using a chisel and mallet or a router cut out the cavity. I tried both to see the difference, the chisel took about 20 minutes and the router took about 7 minutes. The router also left a much neater hole, but either method is fine.
For the control cavity the locations of the controls should be marked then a pilot hole drilled all the way through the body so a cavity shape can be designed on the back of the guitar around them.
Cut out this cavity leaving about 4mm thickness of wood. This may be tricky to do with just a chisel.
An alternative would be cutting the control cavity from the front and mounting the controls to the cover, this would avoid having to make the wood at the bottom of the cavity so thin, which would make it easier to do with just chisels.
Holes need to be drilled between the cavities, so wires may be passed from the pickups to the control cavity.
Step 6: Shaping the Fretboard, Neck, Headstock and Cutting the Fret Slots
The fretboard should be made flat, I used a router jig but a plane would also work.
Before any shaping is done, it is easiest to mark and cut the fret slots while the neck still has parallel edges to work off. I used a smaller dremel circular saw to cut these slots as I wanted the slots to end before the edge of the fretboard, to do this the neck shed should be marked first so you dont cut beyond the lines. This method was fiddly and probably not very accurate.
Each fret position must be measured from the nut, then a line marked using a square. Then use a saw with an appopriate kerf width (0.6mm or so) to cut each slot.
The headstock will need extra layers of wood added to make it wide enough, I added one on the top and 2 on the bottom, but this may vary depending on your headstock design.
Cut the neck so it tapers from about 58mm at the last fret, to about 44mm at the nut. These can vary depending on what you want your string spacing to be. It is best to cut fairly oversize to be safe.
Unless you want a flat fretboard, a radius should be made. I roughed it out using a belt sander, though this was fairly innaccurate. I used the No.7 plane to straighten it and finish putting the radius on. Radius sanding blocks are also available.
Shape the back of the neck using a belt sander, files, rasps, spokeshave (this might not work well on plywood), sandpaper glued to a stick etc. The aim is to make is roughly D shape and for the thickness to be around 21mm. A flat point to connect to the body must be left, about 70mm long.
At some point the voids should be filled with splinters of wood and glue.
The tuner holes should be marked and drilled, then the headstock designed and cut out and sanded till your happy with the shape.
The neck and fretboard should be finished. I reccomend covering the fretboard in superglue, then sanding down and repeating a few times, it leaves a hard finish and is very quick, by the time you've made a pass with the glue the beginning will be ready for sanding. The rest of the neck should just be finished in with whatever varnish you like, could use superglue too.
Step 7: Installing the Frets
Installing frets is quite a long process and really requires a whole tutorial to itself so I will only briefly list the steps and reccomend finding one of the many guides available.
- Cut slots to final depth if required
- Clean slots out
- Cut the fretwire into appropriate lengths
- Install each fret in its' slot with a little glue
- File the fret ends down and put a 45 degree angle on them
- Protect the fretboard with tape
- Level the frets (I used 120grit sandpaper glued to a spirit level)
- Crown the frets with a file
- Polish the frets
Step 8: Cutting the Neck Pocket and Installing the Neck
Clamp the neck into its' correct position on the body, line it up with the centre marks. Draw around the neck onto the body.
Use a router to cut the neck pocket out. Just chisels could probably also work, but would be quite hard to make accurate. The depth should be made so the fretboard is about 6mm above the body
Mark out and drill holes for the screws or bolt in the body then transfer the hole positions onto the neck by clamping the neck in plane and pushing the drill used to make the holes through. If using screws then drill pilot holes. If using threaded inserts drill appropriate sized holes and install them, be very careful not to split the neck. I also superglued the inserts in place for luck. I'm not sure how well screws would hold in plywood in this orientation so recommend using the threaded inserts, these are also ideal if you have to remove the neck a number of times.
If using a tune-o-matic style bridge like me you will need to make a break angle for the neck. This is most easily done by putting a wooden shim in the neck pocket and sanding it will it gives the right angle, though a better way is to make a router jig to put the angle on. Here is a useful calculator for this http://www.tundraman.com/Guitars/NeckAngle/
Step 9: Install the Nut
Either make or buy a nut. I used a piece of scrap indian rosewood because it looks nice.
Cut the nut slot to the correct depth and width (dont change the position of the fret side of it)
Cut the nut to shape then glue in place (not too much glue, it needs to be removable just in case)
The string slots need to be cut to the correct width and depth once the rest of the hardware is installed. I used a 7.8mm string spacing.
Step 10: Install the Hardware, Cut the String Slots, Setup String Action and Wire It All Up
The Control cavity needs to be lined with grounded copper foil.
Mark out and drill the bridge post holes, one of these holes need another hole drilled between it and the control cavity so a ground wire can be connected to the bridge.
Install the hardware!
Put the strings on then you can cut the string slots in the nut (I don't have any good advice on this, for the larger ones I used a small saw but for slots smaller than 0.6mm I had to just cut them out with a chisel, which was quite hard to do and didn't work that well. Just buying a nut would be alot easier, then sand the bottom till its the right height).
Adjust the truss rod while the strings are tight so the neck is straight (or very slightly bowed?). Adjust the bridge height to get the right string action. This whole process takes some time.
Wire it up, this website below has a lot of good wiring diagram, if you can't solder then it would be worth looking at some tutorials. I would also recommend using star grounding, where all ground wires stem from one point, and avoid ground loops.
http://www.guitarelectronics.com/category/wiring_r...
Make a control cavity cover, this should also be covered on the inside with copper foil.
Step 11: Final Thoughts
Though making a guitar was quite a challenge, it was easier than I expected, and was very fun.
Hopefully this will show people plywood can make a good sounding and attractive guitar.
Things yet to do:
- Control cavity cover
- Trussrod cover.
- Install the fret 22, 23 and 24. I didn't buy enough fretwire.
- Proof read this instructable
I would recommend building a guitar, whether out of plywood or more conventional tonewoods. Feel free to ask questions and I will answer as best I can.
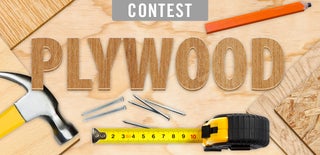
Grand Prize in the
Plywood Contest
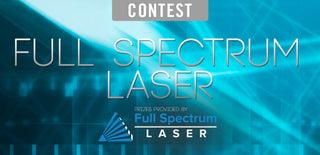
Participated in the
Full Spectrum Laser Contest 2016