Introduction: Gypsy Wagon Building
This wagon was built by a collaboration of Paleotool (author of Building a Gypsy Wagon), myself (PaleoPunk), and our friend, AmericanPikey. The AmericanPikey recently retired and wanted a mobile retirement home. The vardo design presented itself as a good option because it is cheaper than a regular house, no land ownership is required (check local regulations for more details), and it's far more cool than an "off the lot" RV. The vardo is also attractive as a retirement home because utilities cost little to nothing depending on how you live. Towable on the highway, this wagon combines the design of centuries past with mobility and economy required for modern life.
The one we built here is two feet longer than Paleotool's to accommodate an indoor kitchen and more storage. The overall length of the wagon is approximately 10 feet long and is 7 feet wide. The floor on the inside is about 5 feet across with one-foot ledges extending over the wheels.
Step 1: Design Planning
In terms of planning, the basic design sketch from Paleotool's vardo was what we started with. The wagon was made as long and as wide as was possible as was safe on the 10 foot trailer. After estimating the basic lumber quantities, a trip to the big box lumber store was made, wood stacked, and allowed to dry for several weeks. Longer would be better for stability, but the new owner was itching to start.
Step 2: Materials
This wagon began with a new 10ft. by 5ft. flatbed utility trailer costing about $1000 (US). Flat bed trailers, while difficult to find cheap, are much easier start with than another kind of trailer that is being re-purposed. Something like an old cargo trailer requires a lot of work to dismantle and prepare for building. Unlike the average re-purposed trailer, the utility trailer's the floor structure already exists and the metal side rails give a strong base to help support the walls.
Pictured in the trailer is a pile of lumber that, from a "big box" store, cost about $1200 (US) including necessary bolts, washers, nuts, screws, wood glue, etc. In the end, we added another couple hundred dollars of screws to the pile. The total for the basic build ended up at about 2400 US dollars (including the trailer).
Step 3: Preparing the Trailer
The large dual purpose gate/ramp that came with the utility trailer did not fit with the plans for the final wagon and was removed. An angle-grinder was used grind off the hinges. Looking back, I think it would be an interesting thought to consider integrating the ramp either as a ramp or as some kind of folding porch. It would take considerable planning and engineering, but it is interesting to contemplate for future designs.
Next the tail lights were moved to the rear of the frame so that they would be more visible on the road.
Note; it is important to use thread locker when using nuts and bolts wherever possible so that things don't come loose on the highway.
Jacks are important to stabilize the wagon while at rest. To stay more on budget and keep the design simple, we installed spring loaded mechanical jacks. They are not the most high tech, but they do their job. They are permanently attached (welded) to the underside of the wagon. A locking hinge allows them to folded up under the body during travel.
The tongue jack came with the trailer. It is permanently attached and very sturdy. Because the jack did not come with a foot, it had to propped on a board to spread the weight otherwise it would have sunk into the ground like a cookie cutter through dough. A foot was added later.
Step 4: Basic Box
The base of the wagon is a box that is about a foot deep and heavily reinforced. This holds up the rest of the structure. This step is made much easier by the style of utility trailer because the trailer came with a steel frame already outlining the box. The steel frame means that additional reinforcement is unneeded for the box.
We began by cutting boards from 1" exterior plywood to the length of the trailer (10 ft). Because we were using 8 ft long plywood we had to piece together the boards, so we ended up using an 8 ft and a 2 ft length for each side. The ledge boards (see the next step) are the same length, so those were cut at the same time (which is why four ten foot lengths are pictured).
These boards become part of the undercarriage, getting a lot of wear and tear on the road. They also have great potential for water damage. To protect them, they were painted with high quality oil paint. We chose black as a nice inconspicuous clean color for undersides.
Holes were drilled through the steel trailer frame and the boards were bolted on paint side out. In the corners of the box, notches had to be cut in the corners of the board to accommodate the steel frame (see pictures). The boards were also glued together at the seams (where the two and eight foot boards met) and in the corners. The corners of the boards were screwed together for extra stability. When building something that will taken on the highway, strength is of the utmost importance.
Step 5: Box Ledges
Ledges serve to extend the space inside by sticking out from the box by a foot on either side. The wall are then built up from the ledges. The ledges can make the sleeping space wider, extending out over the wheels, keeping the seating, benches, and storage above floor level.
Like the box sides, the outsides of the ledges were painted with black oil paint for protection from the elements. To hold up the ledges while they were being attached, a board was clamped across the top of the box and then the ledge boards were clamped to the temporary support board. The ledges were then screwed to the box.
As I mentioned in the previous step, our boards were not long enough to span the length of the trailer. So to strengthen the box as a whole, we put to two foot sections to the rear in the box part and to the front on the ledges, effectively staggering the joints. The joint in the box was also strengthened by a plywood scab.
Step 6: Braces
Much of the weight of the wagon is supported by the ledges so they must be reinforced. Braces were installed under the ledges for this purpose. The braces were painted black to match the undercarriage. This part doesn't look particularly impressive, but it's really important if you don't want your walls to fall over..
Step 7: Front Wall
In this style construction, the front and rear walls support most of the structure. Everything depends on them being strong and straight.
Two hardwood battens (vertical supports) were the first step in erecting the front wall. They were screwed into the front wall of the box, and another board was attached horizontally across the top of the box flush against the battens, sandwiching them against the front wall to further stabilize them. The wagon began to gain its recognizable profile as the front wall went up. Tongue and groove pine cut to the width of the trailer makes up the front wall. Each board was screwed onto outsides of both battens.
The front window was created by using pieces cut to the length of the side of the trailer to the battens, making the battens the sides of the window.
The curve at the top was marked with string and a pencil (see pictures for clarification of this section). The string was tacked in the horizontal center and far enough down so that it just reached the maximum height of the wall (see the sketch in the first step). The string was about the same length as the width of wall making the diameter of the circle about twice the width of the wall. A pencil was tied to the other end. Pulled taught the pencil moved in a broad circle. With this contraption the top arc was drawn, and was then cut out with a jig saw.
Step 8: Back Wall
The back wall was built in the exact same way as the front, except that the battens were spaced so that they would be against the sides of the door for stability. The door was off-set from the center to create more workable space beside the door inside. Because of this, a third batten was added on the side with a wider wall for strength. The wall was built as solid wall, and the door was sawed out later with a hand saw.
Step 9: Sides
Side walls were also tongue and groove pine screwed to hardwood battens. There were two battens per side. We also added battens to the corners to which both the sides and ends were screwed. The designer recommended more battens at this stage but a compromise was later reached between weight and strength.
Step 10: Purlins (Roof Supports)
Purlins work as rafters in in this style building. They are stiff hardwood boards that hold up the roof. Notches in the top edges of the end make the purlins part of the main structure tying the front and rear walls solidly together with glue and screws. They are braced with U shaped pieces around the notches on the inside for added strength.
Step 11: Roof
The inner layer of roofing is quarter inch bead and cove plywood wrapped across the purlins. A strip of wood with the corner cut to match the curve of the roof was attached to the to top side edges of the walls to support a two inch over hang in the roof. The plywood was screwed into each purlin and the sides. This can be difficult because it's a shot in the dark to screw down through plywood and find the center of each purlin, and if the purlin is missed the screw comes straight down through the ceiling.
After the wood was screwed down, a layer of 30# tarred roofing paper was laid over the entirety. Heavy duty painted sheet metal (special order home style, not the cheaper off-the-shelf variety) was then stretched over the plywood and screwed down into the purlins with neoprene washered roof screws . The metal roof is durable and weather resistant and no maintenance.
Step 12: Living
Now, for the personal touches...
The first thing added after the body was completed was a dutch door. A dutch door opens in halves and can be closed on the bottom to keep children, pets, pests, etc. in or out, but the top can be open for light and ventilation at the same time. The body and door both received several coats of varnish to protect them from the elements.
For a nautical feel, portholes were chosen for the windows. The side windows are actual old ship portholes, about 20 inches across. A small matching door porthole was also added. The front window remained a rectangle, and was glassed in with heavy-duty Lexan. In a small space with no electricity, windows are vital for ventilation and light. The trade off for using windows for light and ventilation is very good for most people because in exchange there are no real utility costs and the carbon foot print of the house itself is very small.
The bed is about four feet off the floor, with a storage space underneath divided into an open and closed space. The open space is on top directly under the bed. A trap door in the floor of this open space, which is about a foot off the floor proper, opens into an enclosed space underneath. Benches sit slightly less than a foot off the ledges next to the bed. The space between the bench and the ledge is essentially a box for more storage. The benches also serve as steps up to the bed.
In the front between the bench and the door are shelves on the narrow side, and a stove on the wide side. The stove was purchased from marinestove.com. AmericanPikey set off on his travels before the stove was installed. He has no camera or mobile phone with which send pictures, so I don't have any pictures of the stove installed, but I did include a picture of the stove from marinestove.com. In a small space, a small stove provides plenty of heat. A heat shield was installed behind the stove to prevent a fire in the wooden walls.
The wood stove heats the space well and quickly whenever lit, and since this is not convenient in warmer climates, a small portable 2 burner propane stove is stowed under the bed to be brought out for cooking without heating the house.
After several voyages, the wagon is holding up well. A successful retirement home all around.
Thank you Paleotool for helping edit this 'ible!
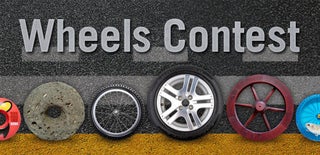
Grand Prize in the
Wheels Contest
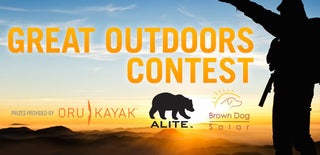
Runner Up in the
Great Outdoors Contest
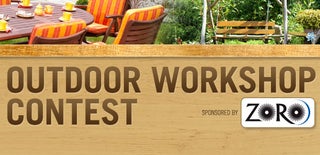
Second Prize in the
Outdoor Workshop Contest