Introduction: Handcrafted Leather Briefcase
So you are interested in making a leather briefcase? Well sit down and strap in because we are going to go for little ride. This is the first time I have ever worked with a textured leather, but I saw this piece of awesome Horween USA leather and could not pass it up.
This Instructable will show you how to make a gusseted briefcase. I have not gone into great detail on some of the leather working basics (cutting things out square, basics of saddle stitching, etc.). If you have not learned how to do a saddle stitch or use a carpenter's square yet, favorite or save this Instructable and come back to it later on after you have had a little practice to figure out the basics.
I also want to mention the amazing guys at Landwerlen Leather in Indianapolis, Indiana. The guys there have been a tremendous help over the years from when I was first getting started all the way until now. All the supplies I used to make this briefcase were purchased from them. I am incredibly lucky to have them a short 20 minutes drive down the road from me.
Let's get to it!
Step 1: Step 1: Tools and Supplies
Tools
Bare Necessities
- Large carpenter's square
- Cork backed ruler
- Knife (can be a utility knife, Xacto, etc)
- Cutting mat
- Hammer/maul
- Stitching chisels
- Striking surface
- Needles
- Wing dividers
- Scissors
- Scratch awl
Intermediate
- Strap cutter
- 1" oblong punch
- Center hole punch (1/8" and 5/32")
- Round end punch
- 1" English Point End Punch
- Rivet setter(s) with appropriate rivet anvil(s)
- Tapered maul
- Ball peen hammer(s)
- 4' ruler/straight edge
- Diamond awl
- Edge beveler
- Front end cutters (for rivet posts)
- Needle nose pliers
- Misc circular stencil/mason jar lid
- Center rule
- Lighter
- Rotary Cutter
- Burnishing tool
- Stitching pony
Not needed, but makes life a lot easier
- Japanese style knife
- Round knife
- McKay knife
- Trend Routing Guides*
- Fabric ruler
- Fabric tape measure
- Anvil
- Thin neoprene tape (serves as non-slip backing for tools)
* I love using these routing guides to help set out my panels on
sides of leather. It helps me visually see how much a panel is going to take up, and also be able to visualize the entire panel to avoid bad parts of the side of leather.
Supplies
- Waxed thread
- Side of 5/6oz leather
- Glue and/or Contact Cement
- Burnishing agent (Tokonole, Saddle Soap, or Gum Trag)
- Double cap rivets (Jiffy Cap Rivets 407D and 409D)
- Brass solid post and burr rivets (size 12)
- 1" Buckles (#3)
- 1" Trigger snaps (#2)
- 1" D rings (#2)
- 1" Rectangles (#2)
Step 2: Step 2: Cut List: Measure Twice, Cut Once!
Below are the dimensions for the cuts you will be doing. It is extremely important that you layout ALL the measurements/dimensions for the panels and pockets on the side of leather before you start cutting. You want to make sure that you do not mistakenly cut apart a usable section that was vital to the bag. When I made my first messenger bag, I cut the side in half before I cut out my gusset. That meant I had to go out and buy another side of leather. Don't be my like me. Be smart.
- 5"x41"* - This is the gusset of the bag
- 21"x17" - This will be the back panel/front flap
- 12"x17" - This will be the front panel
- 10"x17" - This will be the laptop pocket
- 7"x8" (2) - These will be the front pockets
- 1"x42"** - This will be the shoulder strap
- 1"x18" (2) - These will be the bag straps
- 1"x11" - This is the top handle
- 1"x6" (2) - These are the handle attachment anchors
- 1"x5" (2) - These are the D-ring attachment anchors
- 1x4" (4) - These are the buckle anchors and trigger snap attachments for end of shoulder strap
- OPTIONAL: 4.25" x 16.5" of 7/8oz natural vegetable tanned leather
- This will serve as a reinforcement for the top of the bag and will REQUIRE that you use solid post and burr rivets to successfully attach the top handle with rivets
* The actual length of the gusset may vary. 40" is USUALLY plenty, likely 38-39.5". It has been a different measurement for each of the 7 messenger bags I have made. Leather thickness and temper will affect this, along with how you measure/cut the rounded corners.
** This is the TOTAL strap length that works for an average sized male with this design. If you want to make an adjustable strap, you will need at least 52" strap cut to make the two ends of the adjustable strap.
I usually start the cutting process by unrolling the leather and using my 4' straight edge to cut a straight line at the back of the hide. This allows me to have a good starting point to mark out the gusset. After I cut out the straight edge along the back, I will mark out the gusset.
After I mark out the gusset I then use my Trend Routing Guide set to the different panels sizes, and lay them out on the leather that fits best. Try to avoid the holes and blemishes as best as you can on the hide. You can also you a large carpenter's square to mark out the panels too. I highly recommend putting thin neoprene tape on the back of your measuring tools to make them non-slip. I also put it on the bottom of my anvil to prevent it from scratching leather or other surfaces. After everything is marked and measured out; its time to cut. After all the gusset, panels, and pockets are cut out; I will use a strap cutter set 1" and cut 2 or 3 long strips to make sure I have plenty of 1" strips for the handle and anchors.
Step 3: Step 3: Rounding Corners and Marking Stitch Lines
Once everything is cut out, it is time to round the corners. The bottom corners of the panels will end up being the bottoms of the bag. I like to mark out the rounded corners using a circle stencil I got off of Amazon. Before I had this, I would use the lid of a saddle soap container and flat washer to mark my corners. What ever round object you have on hand will work.
The bottom corners of the 8"x7" (height x width) pockets will have large radius corners. The top corners of the 8"x7" pockets will be a smaller radius corner. I like to mark this with the stencil also. I also measure and mark the hole for the corner rivet before I cut/punch the corners. It makes it easier to accurately measure. Mark the hole with scratch awl 3/8" from top edge and 3/8" from side edge. Go ahead and round those corners and punch the rivet holes. After that, mark your stitching line with wing dividers. I set mine at 3/16" but there is not a right answer here.
ALL of the corners on the 21"x17" panel will be the larger corners. This is because the top of the panel will be the front flap of the bag.
Like the pockets, the 12"x17" and 10"x17" panels will have small rounded corners on the top. These can be immediately cut or punched out. These bottom corners on these panels will have large radius corners also. You can punch them out separately, or glue/cement the panels together and then punch out the corners. I cement them together and will not round out the corners until later to make lining up edges much easier. If you go this route, you must bevel and burnish the tops of the pockets before cementing them together.
Step 4: Step 4: Burnishing Edges and Punching End Points
Use your an edge beveler to bevel all of the edges of the 8"x7" pockets. Bevel the top edge of the 12"x17" and 10"x17" panels only. The other edges will be finished towards the end when the bag is sewn together. After the edges are beveled, use your burnishing agent and burnishing tool to burnish the edges. I will usually burnish an edge 2 or 3 times with Tokonole to get the look I like.
Then bevel and burnish the the top 13 - 21" of the 21"x17" panel. This will be the front flap that closes the bag. This can be done later on, but its easier to bevel the edge when the panel is not sewn to the bag.
Mark the stitch line on the 4.25"x16.5" strip of thick veg tan leather, and then bevel the edges. Then burnish the edges.
Now its time to punch the end points on our straps, handle and various anchors.
- 1"x6" and 1"x4" - English Point for both ends
- 1"x5" and 1"x11" - Round punch for both ends
- 1"x18" - End point on one end, round punch on the other
- Measure and mark holes on these straps to make it easier before punching the ends
- Round End: first hole is 3/8" from end of strap; next hole is 1/2" from first hole
- English Point End: There will be 5 holes; start 2" from end; 1" spacing between each hole
Step 5: Step 5: Attaching Buckles
There are a lot of photos for this step because I think it is difficult to effectively get my point across with words alone. These next few steps will be a little picture heavy to make it easier to follow along.
First step is to take 1"x4" strip and use the 1" oblong to punch a hold in the center of the strip. This is going to be wrapping around the buckle and forming the anchor that will attach to the bag, so you want to make sure it is centered as best as possible. This is where a center ruler is extremely helpful. Next you will want to glue below the oblong hole on one end, then wrap around the buckle and clamp together with binder clips. Repeat this for the second buckle. Next, I measure and mark where to punch the holes in the anchor to rivet the buckle to the pocket. First hole will be 5/8" from end and the second hole will be 5/8" from the first.
Now it is time to mark where the buckle will be attached to the 8"x7" front pockets. Measuring from leather strip around the buckle, it will be 3.5" from top of pocket and 3" from both side edges. Mark around the edge of the buckle with scratch awl. Then mark the holes to punch in the pocket with the holes already punched into the buckle anchor. Punch the holes into the front pocket.
After all the holes are punched, it is time to rivet the buckle anchors to the bag. I use Jiffy Cap branded double cap rivets. I use the 407D and 409D solid brass rivets. I use a CS Osborne cap rivet setter. You want the post on the back side and you want the cap on the front side. You will be striking the cap to set properly set the rivet. To get the best results, you will want a specific sized rivet anchor that will allow the rivet to sit in a domed seat. This will keep the rounded surface and prevent deformation/marking the rivet. You can also set on a flat anvil surface.
Push to cap down on top of the post, pick up your setter and give it a few whacks with your mallet or maul. With my 24oz Barry King tapered maul, it only takes two hits and I can feel when the rivet is set through the handle. It might take some practice if you have never set rivets before. Repeat the process to set the rivets for both buckle anchors.
Step 6: Step 6: Attaching Front Pockets to Laptop Pocket
Now its time to attach the front pockets to the laptop pocket. The pockets should have 1" on every side, so 1" down from top of panel, 1" from the side edge, 1" from bottom, 1" from other pocket. After the pocket is positioned, mark out location with scratch awl, including the holes for the rivets. I will mark with a scratch awl on the inside of the pocket a L and R for the left and right side pockets. This helps me keep straight which pocket I used for which side of the laptop pocket.
Then punch out the holes for the rivets.
Then its time to glue up the pockets. I set a glue line on the back side of the pocket with a pair of wing dividers set at ~1/4" (does not have to be perfect. Its just for a visual boundary for the glue. I will then spread my Seiwa glue on to the back pocket using a plastic glue spreader. Line up the pocket with the marked edges and line up the rivet holes.
Now its time to rivet the pocket on to the panel. Using the double cap rivets, attach the pockets to the panel.
Next, its time to punch the stitching holes. I have recently upgraded my stitching chisels to Kevin Lee's basic French Style chisels. I use the 3.85mm set for this bag. I have a 10-prong chisel that makes long straights a lot easier. When I am stitching, I will overlap 4 or 5 teeth to ensure proper spacing and orientation. When going around the corners, use the 2 prong for proper spacing and patiently go around the corner 2 holes at a time.
Now its time to get sewing! I use 0.8mm Ritza Tiger thread with John James size 004 saddler needles. You want your thread to be approximately 4x the length of your stitch line. Put your needles on the thread and sew together using a saddle stitch. When you get to the end, back stitch at least 3 stitches. I like to have both my thread ends come out the inside of the pocket. Cut the thread with thread snips or scissors. Then if you're using a poly-thread, use a lighter to melt the exposed thread end(s). Then use hammer out your stitches to close up your stitching holes and get the thread to lay more consistent. I use a ball peen hammer with a polished face to hammer out my stitches. Repeat these steps for the other pocket and then move on to the next step.
Step 7: Step 7: Cement the Front Panel and Laptop Pocket Together
Now its time to cement the front panel and laptop pocket together. Use a wing divider to set a glue line for both panels. I like to scratch/mark up the leather on both pieces before I cement these panels together. It gives more surface area for the cement to get a stronger bond for the two panels.
I have been using Master Contact Cement for a little while now. I do not use contact cement that often, but having the glass glue pot makes it a little easier to use because you can adjust the depth of the brush up and down. PRO TIP: if you have a glass jar like this one for contact cement, put Vaseline on the threads of the lid and jar to prevent cementing the lid shut.
Spread the contact cement on both pieces, let it cure for the specified time of the cement your using, then cement together. After you got them together, feel free to hammer it down.
Now it is time to finally punch the bottom rounded corners for these panels.
After the panels are cemented together and bottom corner is rounded, it is time to measure the linear length of the edge of the panels with a fabric tape measure. This is to verify we have the proper length for gusset. You can use the gusset itself and clamp around the bag to verify its the right length.
Step 8: Step 8: Attaching D-ring to Gusset
There are multiple ways to attach the D-ring anchors to the gusset. You can attach it to the outside with out punching an oblong hole through the gusset. I like the clean look on the outside of the gusset with passing the anchor to the inside of the gusset.
Take the 1"x5" strips and glue up around the D-rings. Then punch the holes for rivets; first hole 3/4" from the end and next one is 3/4" down from first hole.
Next its time to punch the oblong hole. You want to punch the oblong centered on the gusset, 2" down from end. I like to use a center rule to help make sure the hole is placed in center of the gusset. Next, pass the d-ring anchor through the oblong hole. Pulling it snug, mark the holes from the anchor onto the gusset. Punch the hole for rivets.
Now it is time to set the solid brass post and burr rivets. If you have not set this type of rivet, I recommend looking up the proper way to set these rivets. There is an amazing saddle maker that gives a great explanation how to set these style of rivets. I will be explaining the next few steps assuming you read that quick write up. First step is to set the washer on the rivet the post. After setting the rivet, you will want to cut the post down the appropriate length. The set round off the rivet with the shallow dome part of setter. Next step is use a ball peen to hammer the rivet face flat.
I usually only do one side of the gusset in case I need to trim the end of the gusset after the next step.
Step 9: Step 9: Punch Stitching Holes
Use a wing divider to mark your stitch line. I like to start right before the beginning of the top rounded corner. Then punch your stitching holes on the front panel.
After you have punched your holes on the front panel, count the holes. Use a scratch awl or fine point sharpie to mark every 10 or 20 holes to help keep track of the number of holes. It is important to know the number of holes to ensure you have the correct number of stitching holes on the gusset.
Now that you know how many holes you need for your gusset, it is time to begin punching the stitching holes. If you are using round dent chisels or have inverse irons you can ignore this part. You will want to mark a stitching line on the flesh side of the gusset to make sure the orientation of the stitching holes matches up. Then punch your holes into the flesh side. I will stop about 3 inches from the end of the gusset and count my holes. I will then punch the exact number of holes I had in the front panel. This is where you will know exactly what length of gusset you will need. You might need to trim off excess from the end.
Step 10: Step 10: Sew Gusset to the Front Panel
Before starting the stitching, I need to emphasize that you stitch and form the gusset around the front panel. Do NOT form the front panel around the gusset. This is to ensure the proper shape for the bag.
Use binder clips to help hold the gusset to the front panel while stitching. I constantly move a few of the clips ever 4-6 stitches to help re-align the stitching holes. The corners can be very trying on your patience. Take it slow and remember to form the gusset to the front panel. Binder clips will be your friend.
Step 11: Step 11 (OPTIONAL): Attaching Top Reinforcement
Skip this step if you're NOT adding the optional reinforcement.
Use contact cement to glue the reinforcement starting about 4.25" from top of panel and about 12.5" from bottom of panel. There should be 1/2" on either side of the piece of veg tan. I chose to stitch this reinforcement to the top of this bag. With the contact cement, it is not absolutely necessary. I have made a handful of bags without being stitched, and only secured with the contact cement and rivets.
Step 12: Step 12: Attaching Straps and Making the Top Handle
Now its time to attach the straps to the back panel. You will want to mark your rivet holes. They will be 4.5" from the side edge. This first one will be 9" from bottom of panel, the next one will be 1/2" below that hole (8.5" from the bottom of the panel). Set your your double cap rivets to attach the straps. Make sure the straps run as straight down as possible. If they are not running straight down, they might now line up with buckles.
Now its time to make the top handle. Take the 1"x11" strip, mark first hole 1/2" from edge and the next hole 1.5" down from that hole (2" from edge of strap). Repeat this for both sides of handle. Loop strap through brass rectangle and rivet together. Repeat for other side of handle.
Step 13: Step 13: Attaching Top Handle
Now its time to put the top handle on.
Need to punch the holes in the 1"x6" strips for the rivets. Punch the first hole 3/4" from edge; then the next hole is 1.5" down from that hole. Do this on both ends of the strip. Next step is to punch a hole in the top of the bag. First hole is 3.75" from the edge; the next whole is 1.5" down from that hole (5.25" from the edge). These holes are approximately 6 3/8" from the end of the flap/top of the panel. I was not as concerned with distance from the end of the flap, I was concentrating on trying to have them centered in regard to the veg tan reinforcement.
Loop the rectangle from the handle through the 6" strip, line up holes, and then feed the bag straps through. Now set rivets to attach the handle. Repeat for the other side.
Step 14: Step 14: Sewing Back Panel and Gusset
Approaching the home stretch. This is the last step between you and an assembled briefcase. Not going to lie, this is also the most frustrating step because I have not found a way to successfully secure in a stitching pony.
Best way to determine where to start the stitching holes is to line up the gusset with back panel using binder clips. Mark the dead center of the back panel and gusset. Line the centers up together and clip together. Slowly make your way out from the center aligning the edges and clipping together until you reach the top of the gusset. Make sure with the dry fit that the bag sits even and does not wobble. Sometimes this will take 2 or 3 attempts to get right. DO NOT RUSH THIS STEP. If you rush this step and mess up, you will HAVE TO START THE BAG OVER if things are misaligned.
After you insure everything is properly aligned, poke your awl through the stitching holes on each side of the gusset to help guide you where the stitching holes should start. Punch your stitching line and then re-align and clip together to before trying to begin stitching. My "sky hook" makes an appearance to make stabilizing the bag a little easier. Begin stitching, remembering to form the gusset around the panel, this will be harder because the gusset will fight you since it is already formed to the front panel.
Step 15: Step 15: Finish the Edges
Edge finishing is up to how much work you want to do. You can leave them unfinished, paint them, or burnish them. I will leave this option up to you and how you want to finish your bag.
Step 16: Step 16: Shoulder Strap
THE FINAL STEP!
Here it is. The last step. Everything is about to be complete. There are multiple different ways to make a shoulder strap. The first bag I made had a single piece strap and was not adjustable. I usually make my straps with either a 1" halter buckle or Conrad buckle.
Solid strap is great if the bag is for you and you know what length you need (I like my straps to be 42" for this design). Adjustable straps are good if the bag is for someone else, if you want a multi-use strap, or you do not know what length will work for you on this bag.
A strap made with 1" Halter buckle or square buckle is made the the same way you attached the buckle to the front pockets and made the fronts straps for the bag. For the buckle portion of strap, I make the FINISHED length 9" (measured from end of leather strip to end of leather strip, NOT including buckle and trigger snap). Make the other end long enough for your desired FINAL length of strap.
Use the 1"x4" strips to attach the swivel snaps to the ends of the strap.
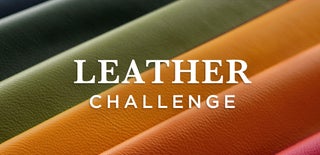
First Prize in the
Leather Challenge