Introduction: Hardcover-- Concrete End Table
This project explores many techniques and materials and combines them into an elegant final product with a versatile end table. I am very excited with how this project came together, and the experiences and techniques learned along the way.
In this Instructable, I am going to cover the process I followed to develop this project. I will share what I learned along the way and how I recovered from mistakes. Look to links for ideas, inspiration, and guides! My hope is that you don't use this instructable as a step by step recipe. However, I hope you use the ideas and techniques explored here to inspire and drive your creative process.
Notes:
There are plenty of things that could have gone better. I note these at the bottom of each section as notes.
EDIT: Click the "download" button on GIFS to watch them.
Supplies
Supplies in final product
- 80 lb bag of Fiber Reinforced concrete
- Titanium Dioxide Powder
- QUICKCRETE 20-lbs Quick-Setting Cement
- (1) Melamine shelf Board
- Oak finish board
- Polycrilic
- 2 park Epoxy glue
Step 1: Inspiration
"No design works unless it embodies ideals that are held common by the people for whom the object is intended."
- Adrian Forty
I wanted to experiment with a more substantial materials that have character and a story to tell. I wanted to enrich this material with an element that shows a story of myself to tell. Thus, the material would reflect upon myself, the user, and myself upon it.
Color:
Concrete naturally dries to different levels of gray depending on the brand. Through a series of tests, I did not like the darkness of the gray with the letters. A quick google brought me to many topics about adding Titanium Dioxide to concrete to make it white. Turns out, it is also used in buildings to absorb pollutants from the air
Text:
I wanted the text to be personal while also filling the surface. My first thought was to use news papers to create a saturated surface of text. However, I decided to use the first page from some of my favorite books along with some literary classics.
Form:
I spent many hours searing the pages of Pintrest, exploring shapes and ideas presented by other makers and product design community. You can explore that board here. The most inspiring precedent is The Magazine Stable by Brad Wray workshop.
Step 2: Design
I worked up the final design in my most comfortable 3D modeling program, Rhino 3D. Any program can help you with this, along with just sketching out the design and providing yourself proper dimensions and details.
I worked through a dozen design options before arriving at the final design. I wanted to keep the form-work as simple as possible while being interest and complex. Rhino is great for iterative and free-form design work, but the freedom makes it easy to over complicate things.
The form is simply based on a 45 degree triangle. I added for flat areas where the 45 degree joints would otherwise come to a point. This allowed for an area for the concrete to sit on the ground, and attach to the board.
Once the design was complete, I designed the form work and planned out how to attach the boards together. Pulling the boards apart and flattening them, I printed out myself a cut plan, and an assembly plan.
Step 3: Formwork
There are dozens of methods to form concrete. Consider the type of finish and complexity of the final form. For this, I took precedent from Home Made Modern.
Supplies:
- Melamine Boards
- These boards have a sheet of vinyl on the front and back that helps prevent water from being absorbed into the wood and form a smooth finished surface. I found these boards cut to width in the shelving section of my big box hardware store.
Tools:
- Circular saw
- Straight edge
- Clamps
- Tape measure
Cuts
I find it easiest to form a dimensioned cut plan to lay out my cut sequence. Laying out the Melamine on supports, mark out the cuts, and then add the distance between the edge of the saw guide. Then, clamp the straight edge to the board.
I then cut 1-5/8" thick strips to form the side walls of the formwork. These where cut from plywood sheathing I had on hand. The specific width of the strips meant that I had a 5/8" overlap on the melamine sides, and 1" to form the concrete.
NOTE: When making the 45 degree cuts, make sure that the blade is tilted in the correct direction. Refer carefully to the design drawings and cut sets. (This is why I always buy more than I need......)
Step 4: Formwork Assembly
Tools:
- Driver
- Tape
- Framing Square
- Vise clamps
Again, I have an assembly plan before joining the pieces. When building the form work, I work as if I am making a finished piece of furniture. This way, I apply the same scrutiny and patience to the project.
I drilled holes along the face of adjacent boards. Then using clamps and a square I attached the pieces together. Use a framing square to assist in lining up the boards. I used tape to loosely hole the pieces together before I attached them with screws. You can easily replace tape with a second pair of hands.
At this time, I cut 6-8 inch lengths of 8" steel rods to use as rebar. It is crucial to have these ready before the pour begins.
NOTE: When I first drilled the holes, I marked out the width of the board incorrectly, thinking the board was 1 in.... To prevent this, instead of measuring, use the side of a board to mark its thickness.
Step 5: Concrete Mix
Supplies:
- Crack resistance concrete with Fiberglass fibers
- Quikrete quick setting patch
- 1lb Titanium Dioxide powder
Proportions
While designing, I explored diffrent types of concrete mixes and additives to lighten the color of the dried concrete. In the end, I found that Titanium Dioxide kept the color to a light gray, while not compromising the strength or set time of the mix.
- 1 Park Quick setting mix
- 1 Park crack resistance mix
- 1/8 part Titanium dioxide (approx)
Straining to remember grade school math, I calculated the volume of each pour in cubic inches, and then used google to translate that into real numbers, like cups. Each pour needed about 24 cups of concrete.
So for the amount I needed of each ingredient
- 12 cups Quick set
- 12 cups Crack resistant
- 6 tablespoons Titanium dioxide
NOTE: When doing the math, I rounded all my numbers up to a whole number. I wanted to be sure I had more than enough for each pour. If you were to mix too little, you would have little time to make a new mix, and the new mix would likely be a diffrent color.
Step 6: Mixing
Tools:
- 5 gallon bucket
- measuring cups
- Disposable gloves
- access to clean water
- Dust mask
**Concrete and ESPECIALLY titanium dioxide can be harmful if inhaled. Don't risk it. Wear a mask.**
I began by filling my 5 gallon bucket with all the raw indigents, then mixing the dry ingredients slowly, so that the Titanium does not become too airborne.
Next I added 4 cups of water to start. Make sure if you have well water (much like mine) you use filtered water. Minerals in the water can change the color and composition of the mix.
Using gloved hands, I turn the mix over to incorporate the water. Once too dry to mix, I added more water. (Some experience with concrete will give you knowledge of how much water to add for a perfect mix) Mix until you achieve a consistent mixture that you could pick up and hold in your hand (refer to above GIF).
Step 7: Pouring
The form used required an open face pour. This method is much like pouring a concrete slab, where the finished side is exposed and must be finished before curing. However, the bottom of the mold will also be exposed and becomes the finished exterior surfaces.
Tools:
- Finishing tools*
- Orbital sander/Reciprocating saw
Once the mix is complete, work quickly before the concrete sets up in the bucket. I usually add an extra cup to the mix AFTER I am happy with the constancy. This gives me a little extra time to muck about.
Handful by handful, I added the concrete to the form work, using your fingers to spread the mix out to all corners. Poke and shake to force the mix into all corners. Fill the form work till the concrete reaches the top. Work the concrete to somewhat flat with your hand. I then pushed the rebar pieces into the concrete before beginning to finish.
I used a scrap end of the Melamine board to finish the surface. There are plenty of concrete tools on the market, but they are expensive and are another tool for me to misplace. Working the surface of the mix from one side to the other, I began to work the mix to flat and level with the sides of the form. You will notice as you work the surface, a watery mix will work its way to the top. This will make it easy to make a smooth finished surface.
Take a break from finishing the surface to vibrate out air bubbles. I used a reciprocating saw along the bottom of the form work for a few minutes. Then put the finishing touches on the surface.
**Spongebob narrator voice** 24 hours later
Now that the first pour is cured, I fasten a board across the surface to be sure it does not fall out of the form work. Then, I flipped the formwork to the next side and repeated the above steps.
Step 8: De-Molding and Patchwork
After 3 days of pouring, I was super anxious and exited to see what all that work has produced! However, remember to take it slow. The concrete is still green, and there could be issues with the pour that could snap the concrete if forced too hard.
Tools:
- Crowbar
- Hammer
- Driver
- Patience
I started by removing all the screws. Then using the hammer and crowbar, I began to peel the form from the concrete. Taking it slow, the form revealed itself, and boy was it imperfect. After years of architecture school, I have learned to love materials for what they are, but this showed some serious structural imperfections....
Thinking on my feet, I grab what was left of the Structural Repair mix of quickcrete and mixed a ply-able batch. This specific mixture of Quickcrete is made to have a high plasticity, allowing for patchwork to corners without formwork.
First use a spray bottle to wet the surface being patched. Then I worked the mix into the cracks using my fingers and a dowel rod. Then smoothed it out using a putty knife. I then used the spray bottle the wet the surface and again smoothed the surface. The extra water makes it easier to achieve a smooth finish.
Step 9: Finishing
Tools/Supplies
- 80-220 Grit sandpaper
- Compressed air
- Polycrylic
- Synthetic paintbrush
Once the patches where dry, I had quite the mess on my hands. The patch left sharp areas and surfaces. Turns out, you can sand concrete! Starting with 80 grit, I sanded the roughest areas till they where no longer jagged. Then, I worked my way up the grits to 220 grit. I followed this with compressed air to remove all the dust.
I had planned on leaving the interior and underside areas of the finished table with no text. So, I sealed these areas before moving onto the ink transfer. I applied the polycrilic with the synthetic brush being sure that it got into every crack and hole by jabbing the brush at the surface. This left big areas of air bubbles that had a creamy white color. To remove this, gently poke at the surface and brush away the bubbles. Without doing this, the poly will not dry clear.
Step 10: Text Transfer
This was easily my favorite part of the entire project. One of the most common quests undertaken during the holidays in school was to transfer text/images onto various surfaces for gifts. People have tried and failed with numerous methods, but the best and most consistent simply uses Polycrylic. I followed this Instructable by TheCrafsMan for help.
Supplies:
- Polycrylic
- Paper
- Water
Tools:
- Synthetic Paintbrush
- Laser Printer
- Roller
- Scrub brush
- Sponge
I started by compiling text that was important to me. You can easily find the first page of many books online with a quick Google search. I copied and pasted the text into Illustrator to orient and scale. Then I rasterized the text to flatten it, and mirrored it. Remember, pasting any text or image from paper will be a mirror image of itself. I then printed the images onto Letter sized laser paper, using a laser printer. (I have no clue if a laser printer is necessary... or how this magical fairy science works.)
Start by painting on the polycrylic with a synthetic brush (natural brushes will shed into the acrylic). Work quickly after painting the first area to apply the paper. You want to work with poly before it becomes tacky as the paper will not stick. Use a roller to evenly apply the paper. Allow to dry for 24 hours.
Once dry it is time to remove the paper. Use water to soak the paper and a scrub brush to scrub off the paper. Do not scrub too hard or you can scrape off the ink.
Step 11: Attaching the Board
I was worried about how to attach the board properly to the concrete. I tested between using E600 and a two part epoxy. The E6000 was too rubbery when it dried, and after working back and forth on the board, it broke off. With the two part epoxy, it took a hammer to break off the board.
Supplies:
- Two part epoxy
- Appearance board (oak, pine, walnut, ect.)
Tools:
- Clamps
- Speed square
- Tape
- Disposable cup
- Stirring stick
Before attaching the board, I cut it to length and sanded it down to 220 grit. I used a spade drill bit and 80 grit sand paper to ruff up the edges that are being attached to increase the surface area between the two, thus increasing the attaching area.
I prepared the epoxy in a disposable Dixie cup before setting up the board with the concrete base. The hardest part was clamping up the two pieces while maintaining square. I showed an image of the situation I ended up with. I used a pipe clamp to hold is against the concrete, and 2 bar clamps to keep the board square. Allow at least 24 hours before removing the clamps, and 48 hours till applying any force.
Step 12: Finishing the Oak
This step was a little backwards. In a perfect world I would finish the oak BEFORE attaching it to the concrete. Alas, it is not a perfect world. This method is something I used before with a liming wax, and really brings out the grain in white oak.
Supplies:
- Finishing wax
- Danish oil
Tools:
- Wire brush
- Rags
I used a rag to wet down the face of the wood. This will loosen the soft fibers of the wood. Then, I used the wire brush to scrape along the wood grains where the softer wood is. You will notice that the softer woods will be pulled out of the wood and leave a gap in the face of the wood. Do this for the entire face before lightly sanding down the face to remove any extra barbs of wood.
Use a rag to apply the wax to the grain. Press the wax into the pockets then wipe the excess off. This will leave the entire board darker like a stain. I then started sanding the face to lighten the wood. The wax applied to the pockets will not get removed by sanding unless you sand... extremely hard....
Finish by sanding back to 200 grit. Then I applied the danish oil evenly over the surface with a rag.
Step 13: Glamour Shots
Wow was this a lot of work.... And although there were hiccups along the way it was all a great learning experience. This is currently sitting next to my sofa at the very top of the stairs, meaning its the first thing people see as they walk up. It is a constant conversation piece and has received much love from my friends on social media.
Being my first post on Instructables, I appreciate any feed back you may have. I would also love to see what you have made, or what interests you! feel free to share them with me!
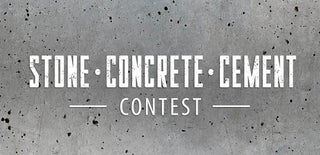
Second Prize in the
Stone Concrete and Cement Contest