Introduction: DIY Stereo Plywood Speakers
This is a project for a quality pair of stereo speakers.
I have decided to try make a curved shape body with 6 speakers in total (2 tweeters, 2 mid and 2 sub bass). My initial requirements was for the speakers to cover as much as the human hearing sound spectrum as possible (I ended up with 52Hz~18kHz which is more than decent).
It is a simple but time consuming project, so bare with me.
Supplies
Other than the raw materials, there are also quite a lot of tools that are required.
Material:
Lots of plywood (thickness: 1.5mm, 3mm, 5mm)
Spare MDF
Oak Logs between ∅11~13mm
2 Tweeters
2 Mid range speakers
2 Sub woofers
Screws (doesn't really matter what type)
Amplifier PCB
2 Signal Splitter PCBs
RCA connectors
~24AWG Wires
AC input connector with fuse and switch
Transformer outputting the voltage required for the amplifier (12v AC for this board)
Wood glue
Tools:
Saw (hack saw, copping saw... doesn't matter)
Drill
Drill bits (∅1.5mm, ∅2mm, ∅9mm)
Hole saw (∅70mm, ∅100mm)
Screw drivers
Sandpaper
Flat, curved, square files
Soldering iron
Heat shrink tube or electrical tape
Wood glue
Clamps
(And all the handy-dandy useful workshop measuring and marking out equipment)
Step 1: Preparation of Materials
This project will require quite a bit of preparation (mainly wood). I have decided to use mainly plywood for the build with oak logs on the front for the looks. These are the sizes of wood pieces I used:
1.5mm Plywood - 890*170mm (show-face grains perpendicular to the length of the strip) x6 pcs
5mm Plywood - 160*400mm x4 pcs
3mm Plywood - 160*150mm x2 pcs
∅110mm Oak Log - 20mm thick x2 pcs
∅130~140mm Oak Log - 20mm thick x4 pcs
Step 2: Components Required
The most important part of the whole project is of course the speakers themselves. So I gave myself a generous budget and sot some with decent sound quality. All of the speakers are rated 30watts and I have a mix of 4Ω & 8Ω speakers. Together, they produce almost the full spectrum of sound humans can hear (in this case: 52Hz~18kHz).
A 12v transformer is used to power the Amplifier PCB since it only takes in AC. The only other things required are the RCA jacks for inputs and outputs as well as the AC input socket.
I would also recommend to prepare two 3.3μf bipolar capacitors rated for 25v or higher, this is used in series with tweeters in order to protect them from low frequencies and power surges. (The capacitance required might vary between different types of tweeters, but between 1μf and 15μf generally works)
Step 3: Amplifier Circuits
Since I'm not playing small for this project, it made sense to pare my speakers with a decent amplifier board. So I settled with this one which has stereo outputs and bass. The four potentiometers sticking out the front are for: Bass Volume, Treble, Bass, Volume.
I'm not really planning on giving a detailed explanation of the circuit itself since that can be a-whole-nother instructables. So if you are making this speaker, just buy an amplifier.
The only other PCB I have is two signal splitters that takes the output signal for each stereo output and compresses it into a set frequency range for the mid speaker and tweeters. A bipolar capacitor of 3.3μf is also required to be connected in series with the tweeters in order to protect the tweeters from current surges.
Step 4: Full Circuit Architecture
The First image illustrates a basic overview of the final circuit. However, if you ae making this project, you might have a slightly different setup. I will post a clearer digital schematic here soon.
I would advise at this stage to do a quick check on the circuit. So connect everything up and check if it works. This prevents the hassle of potentially troubleshooting later. If you circuit doesn't work, check your connections and components.
Step 5: Plywood Lamination Crash Course
In order to make the curved plywood shape, the 6 pieces of plywood have to be laminated.
Laminating plywood is simple, one take a few layers of thin plywood, spread wood glue between the layers, bend it into the shape required, secure and clamp it, wait for it to dry, done. That's basically how it works (I'm ignoring the small details).
But making a perfect bend and without gaps in-between the plywood layers by hand is difficult, so a mould is required.
Step 6: The Mould
I made a makeshift mould from some spare plywood and some MDF. There is an image for the dimensions the mould should be.
Using some L brackets, screws and masking tape to support the wood pieces, a strong structure is made.
Step 7: Laminating
Two curves will be made, so each curve will use 3 pieces of the 1.5mm plywood.
The most important thing to do first is to identify the show-face. This is the side of any of the pieces thats going to to be the top surface. (Tip: Choose the best looking piece). Once identified, make sure you set it aside for now and keep it clean.
Take one of the remaining two pieces of plywood and use a damp cloth to wipe any dust of it. Now take a roller or a paint brush and apply a thin layer of wood glue over the entire side of wood. Spread the glue evenly. Take the other piece of plywood and place it ontop of the glued surface. Aline the two pieces of plywood so the corners all match. Now apply a thin layer of glue over the surface of the second piece. Take your show-face piece of wood and place it on the glue show-face facing away from the glue.
Now move onto the next step quickly.
Step 8: Moulding
You find that the pieces of plywood slip and move around quite easily over each other. We will use this to our advantage as this lets us bend the 3 layers of plywood around the curve of the mould easily. Once you bend it around the curve, secure it with a clamp so it doesn't move anymore. Make sure the two ends of the plywood layers are roughly the same distance away from the top of the curve. Wipe the excess glue off the wood.
Now clamp the whole thing down, most importantly the edges. Now its in shape, we can watch glue dry.
Step 9: Detaching Mould
After around 12hours, the glue should thoroughly dry. (It is important not to detach from the mould too early, otherwise the plywood will deform). Take all the clamps off, if it retains structural integrity, then its been successfully laminated. However, if it starts warping and bending, its still not done, in which case you'll need to clamp it back immediately.
When its successfully moulded, take it off the mould and set the curve aside. Now make the second curve through laminating the other 3 pieces of 1.5mm plywood. Repeat the whole laminating and moulding process. (The mould can be reused)
Step 10: Sanding and Trimming
After both curves detach from the mould, the sides will be quite rough. So sand it down so its flat and level. I would recommend starting from p80 sand paper and move to p200. Sand all the edges other than the two ends of each curve.
You will realise that the ends of the curve are shaped like stairs, they are not matching. Thats supposed to happen. Use a copping saw and carefully trim the edge off till the wood is in 3 layers. Does that make sense?
Now use a trysquare or something that does the same job and sand so both ends of each curve are level. (Try to sand/cut off as little as possible but still keep the ends level)
Step 11: More Sanding...
After the initial sanding, we have to do surface finishing. Before applying oil, the surface of the curve has to be sanded down with some carbon paper. I used a p2000 piece but anything above p1000 should give you an ultra smooth surface.
I wiped the surface with a damp cloth to remove any wood dust.
Step 12: Oiling (For Curve)
For the oiling of the curve, I used some Tung oil. With a paint brush and a cloth, spread the oil over the whole show-face surface and use the cloth to rub the oil into the wood fibers. I would recommend to go over the edges and a bit into the inside with Tung oil as well.
Step 13: Body Panels
These panels are what all the internals will be mounted on.
The design is pretty simple: take the 4 pieces of 160*400*5mm wood rectangles, cut a semicircle of ∅16mm at one end. I used a copping saw but any saw can probably do the job. Once again, sand the edges.
Step 14: Soldering
Soldering only takes up a small amount of the project. All there is to do is to solder some wires to the RCA connectors and the AC power plug & switch.
I have put either heat shrink tube or electrical tape over all the solder connections so everything is insulated.
Step 15: Cutting and Drilling on the Back Panels
There are a few places where a connector or plug has to poke through the panel. So I have measured and marked out the dimensions of each component.
The PCBs also have to be mounted to the back panels via M3 8mm screws so I have also marked where each screw will go. This allows me to drill a pilot hole of around ∅2mm to guide the screws.
Once everything has been cut out, sand the show-face down with some carbon paper. Then coat it with a thin layer of Tung oil and let it soak in.
Step 16: Initial Circuit Assembly
Now everything can be attached, screw all the PCBs and connectors in.
Connect all the boards and plugs together as shown in the image above or from the architectural diagram in step 3.
Step 17: Attach Back Panel
There are many ways to attach the back panel to the curve. I have chosen brackets to hold the structure and shape and filled the gaps with wood glue. This obviously isn't the best option, but it gets the job done.
Both panels are attached the same way to the 2 curves. (Remember that the PCBs face the inside and the ports face the outside)
Step 18: Front Panel
The two front panels will house all the speakers as well as the oak logs. But for the speakers to fit it, holes for the speakers must be drilled on both plywood panels and the oak logs. Make sure to measure the diameter of you speaker in the correct place before cutting/drilling.
I achieved the holes through using 2 different sized hole cutter and a hand held drill. (I would advise to use a pillar drill if you have one and try to avoid using hole dill bits, reason being these drill bits are not hugely accurate and the RPM and clutch on a hand held drill is no where near as competent as pillar drill). However I did not have many options so I had to use what was in stock.
However I soon found out that the drill takes too long to drill through the oak logs, so I temporarily ditched the oak logs idea.
Step 19: Drill Holes on the Side
Measure the dimensions and positions of the 4 potentiometers that will be poking out. And drill the appropriate holes for them. In this case, I used my ∅9mm drill bit.
Step 20: Add Brackets
Briefly put the front panel where it will be attached, and use a pencil to trace out the outline of the bottom of the panel on the curve. Now screw in some brackets so the panel can later be mounted. Make sure the flat top of the bracket is aligned to the line.
Do the same for both speakers.
Step 21: Secure the Speakers
Take the two front panels and and place the show face up. Fetch the 6 speakers, place them in their allocated hole. I then took my ∅2mm drill bit and drilled pilot holes into the wood where the screws will attach the speakers. Now I used some M4 5mm screws to secure the speakers in place.
Do the same for both panels.
Step 22: Attach and Assemble
Rest the panel in a stable position on the curve. Connect all the speakers to their ports. Then you can move move the panel into its mounting position and screw the screws through the bracket to secure it in place.
Step 23: Base Board
Cut out the base board on the 3mm thick plywood with dimensions 15*17mm. Sand it and drill pilot holes where it will be attached to the rest of the speaker. Screw the transformer onto one of the base plates and connect it to the rest of the circuit before screwing that base board on. Then screw the screws but be careful not to screw too fast otherwise you might split the wood.
Step 24: Knobs
Twist all the potentiometers to their neutral position and put their caps/knobs on.
Step 25: Done!
Guess what? Its done!
*cough Only took 2 weeks... *cough
Now that everything is done, its time to plug and play.
Congratulations if you have made it this far into the instructables and somewhat understand what I was talking about.
If you have any questions or tips, the comment section welcomes you!
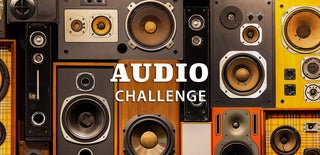
Runner Up in the
Audio Challenge 2020