Introduction: Dredd 2012 Costume Tutorial
In this instructable I'll be showing you how I made my homemade Judge Dredd armour, the armour tutorial will include instructions on how to make both the armour and the helmet as well as tell you exactly what extras you can buy to complete the look!
I will provide you with all of my personal templates in pepakura format and JPG so I suggest you head over to Tamasoft and download yourselves Pepakura Designer 3 if you dont already have it!
I have tried to break this project down into smaller, more manageable steps as I know I hate being overwhelmed with a wall of text!
Main Materials used:
EVA foam (12mm, 6mm and 3mm)
Worbla (optional material)
Elastic
Mesh spacer fabric (Base material used to make the vest)
Black Pleather
Long Zipper (Brass Preferably)
Black corduroy
Black Ribbon
Hot glue
Assorted spray paints
Acetate plastic
Super glue
Spray adhesive
Nylon webbing
Plastic buckles
PVA glue
White chalk
Main Tools Used:
Dremel Tool ( sanding drum bit )
Heat gun ( can be substituted with a hair dryer)
Scissors
Stanley knife/ X-acto knife
Hot Glue gun
Sewing machine
Foam brush
This project took me 2-3 weeks to complete working on it about 2 hours a day (although I did have to learn how to sew...) and as you can see it produces some pretty good results! I hope you all enjoy reading through this and learn some new things!
Step 1: Getting Your Templates and How to Scale Them
First things first! Click HERE to download all the template files I created as well as a helmet file made by Dung0beetle. The helmet file has been specially unfolded to be made out of foam. The files contained in the folder you download are a couple pepakura files as well as some JPG templates as well. The pepakura files are easily scaled within the pepakura designer program but unfortunately the JPG's will have to be scaled using word which is a little less simple.
Step 2: How to Scale Your Templates
Scaling in pepakura:
When scaling in pepakura there are two key functions you should learn to help you along, one function is the button to scale the entire model where you can enter either a width, length or a depth value. This function is easy to access as it is one of the buttons along the tool bar which you can see in one of the photos above!
The other function is the measure distance function which allows you to measure the length between any two points on the template to help you more accurately scale your templates. To access this function simply right click on the right half of the Pepakura designer program, a selection box should pop up and it is one of the options near the bottom. Once clicked if you click on one point on the template and then another it'll give you the length between these two points which will help you accurately scale the piece to your body.
Scaling in Microsoft Word:
For the JPG templates you will need to scale them in Microsoft Word. This is a fairly simple process as well as all It requires you to do is:
First crop the template down as small as you can as shown in the image above, cropping the image down to its very edges helps you to scale it as accurately as possible
Second right click on the image and select the size and position option, this will bring up a window that will allow you to scale your image by length and width
Scaling the templates to your own size:
The best way to scale the templates correctly is to look at reference photos off the internet from google search. By looking at the size of the armour in comparison to the actor's body, this will help you to figure out what lengths to measure on your own body. For example you can see that the shoulder plates measure from the top of the shoulder to just above the elbow, you should therefore measure that length on your body and scale the shoulder templates accordingly. Another example that can easily be seen is the size of the vest (the side that is connected to the zipper) runs from the actors waist to the bottom of the collar bones and so again you can measure that distance on yourself and scale things accordingly
* the two shoulder templates should be scaled to the same length top to bottom, but they wont be the same width
** the default size on the helmet is quite large, I have a 23.5 inch head circumference and it was large on me slightly so I would suggest reducing the size of the helmet before printing
Step 3: After Scaling Your Files
After Scaling your files:
If you had to re-scale your files in pepakura you'll notice that all the pieces may have jumbled around, this always happens when you re-scale a file. You will need to rearrange the pieces back inside the pages before printing. After which you have successfully scaled and printed all your templates
Step 4: Making Your Helmet Out of Foam
Materials/tools used for this step:
12mm EVA foam (or 6mm if you can get your hands on it)
3mm EVA foam
hot glue (or spray adhesive)
Super glue
Hot glue gun
Stanley knife/X-acto knife
Scissors
Heat gun/hair dryer
Assorted Spray paints
Dremel tool
Masking tape
Sun visor
Building your helmet:
You will be building the helmet out of foam as it is the fastest and easiest way to get some good looking results on the helmet. Most people when they take on a helmet build use pepakura and plastic to create their helmets but it requires a lot of sanding and can take weeks if not months to complete just the helmet! Using foam I managed to complete the helmet from scratch in two days!
(you will need to reference the images above to see what I mean by each of these steps)
As you can see in the first image there are two pieces in the pepakura file, one is the main body of the helmet and one is the raised lip on the helmet. The main body of the helmet should be made out of thicker foam to give it structure, use either 12mm or 6mm EVA foam (I used 12 mm because I had no 6mm foam). Using superglue to glue together the helmet will speed up the build time significantly and is stronger than hot glue. You may need to use your dremel tool to bevel some of the edges of the foam when trying to make sharp angles in your helmet such as those at the top around the badge (see one of the attached images to see what I mean).
Once you have the main body finished out of thicker foam you can cut the second piece out of 3mm foam (use scissors as it is faster and easier when cutting thin foam). This large piece wraps around the helmet as you can see by the red part of the pepakura model. You can spray spray adhesive onto the thinner 3mm section and carefully lay it onto the main helmet body be sure to reference the model to make sure you are putting it down correctly. The badge detail can be made by sketching onto the template from the pepakura file, you can then transfer your sketches onto thin foam to glue onto the helmet.
Step 5: Sealing Your Helmet
Sealing the foam:
Before you can paint your foam you will need to seal it! EVA foam is porous and so absorbs liquid... as well as paint, so to seal the surface you should use a foam brush to paint PVA glue onto the surface of the foam, you should paint on at least 4 layers (or until the foam has a smooth/shiny surface) waiting about 30 minutes between each coat for it to dry or until the foam has a shiny surface. Then you are ready to move onto painting and finishing your helmet!
*I do not endorse any particular brand of PVA glue, just purchase the cheapest brand you can find and it should work fine
Step 6: Installing a Visor
Installing the visor:
For a cheap visor I used a black tinted plastic sun visor, it is much thinner than visors used in motorcycle helmets and so it provides less resistance when you bend it. This is much better suited to installing in foam helmets as foam isnt rigid and so installing visors is harder as it is. Using a sun visor makes it easier and cheaper to install a visor.
The pepakura file you downloaded named helmet visor contains only the visor. The key with this is to cut it about 3-5mm larger around the template except for the section at the bottom which is straight. This is so that you have enough excess plastic so that you can glue the visor in more easily.
Once you have the visor cut out use your stanley knife cut along the edges of the helmet where the visor will sit, make sure you leave about a 3mm border between the outer edge and your cut. Once you have cut into the edges go inside the helmet and slice away the excess foam, this should leave a ledge against which you can glue the visor. (reference images above) Use superglue to glue the visor in place, this provides a strong hold and only takes seconds to set! I would glue certain parts of the visor down first with hot glue to hold it in place before using super glue. Make sure that your visor is glued in evenly on both sides! measure how far down you glue it with a ruler as you can see in one of the images above.
Step 7: Painting Your Helmet
Painting the helmet:
First make sure you mask off your visor very well both on the outside and on the inside in case overspray gets inside your helmet. Then lay down a base coat of silver paint on the helmet and let it dry for an hour or so, then take a pain brush and some vaseline and paint scratches and scuffs in vaseline over the silver, this makes a chipped paint effect when you paint the next layer onto the helmet.
Then paint over the entire helmet in metallic black, in one of the images above you can see places where the vaseline is below the newly painted black layer. Let the black dry again for about an hour and once the black paint has dried you can take a cloth and wipe off the area's where you painted vaseline. If the paint doesnt chip straight away you can use your nail to gently scratch the area where the vaseline is/was and it should chip away revealing the silver base coat.
Then mask off the parts of the helmet that arent meant to be red, to save on using up all your tape you can use newspaper to cover the larger area's. Then paint more vaseline ontop of the chipped paint area's, be sure to go outside of the chipped area slightly so that the next time you wipe away the vaseline some black paint will show around the outside of the silver.
Paint over this again in your metallic red colour, try to match it as best as you can to the colour of the helmets in the movie. Let the paint dry until it is no longer tacky and once again wipe off the area's where you painted vaseline to chip the red paint.
To add the final layer of spray paint mask off everything except for the badge so that you can then spray gold paint on top of it. Let this gold paint set for an hour or so so that is it fully dried.
The final step is to give all the coloured parts of the helmet a black wash. A black wash is where you water down black acrylic paint very slightly and paint it onto a surface, you then gently wipe away some of the black paint after it has dried slightly, leaving behind some black paint on the surface that replicates dirt. The more gently you wipe away the paint the more you leave on the surface and the dirtier it will look.
Step 8: Padding Your Helmet
Padding your helmet:
Unfortunately there is no simple way to pad out your helmet correctly. Ideally you should use a soft foam more like sponge to pad out your helmet as it allows a bit more wriggle room in terms of different people using the same helmet. You should put on your helmet and try to move it around on your head to find where you need to fill in space to make it better fit your head. I found that my helmet looked best when my head was in the back of the helmet.
This completes the helmet part of the tutorial!
Step 9: Chest and Back Armour Plates
12mm EVA foam (or 6mm if you can get your hands on it)
3mm EVA foam
hot glue (or spray adhesive)
Super glue
Hot glue gun
Stanley knife/X-acto knife
Scissors
Heat gun/hair dryer
Assorted Spray paints
Dremel tool
Masking tape
Chest and back armour plates:
These are fairly easy parts to make as they are flat pieces that do not require using your heat gun/ hair dryer. There is a small amount of simple layering that needs to be done on these pieces. it will require you to use 12mm (or 6mm) as well as 3mm EVA foam. Raised detail can be done using the thinner foam using spray adhesive to stick it on to the surface.
For recessed detail you simply cut the recessed shape out of the thicker foam, once cut you can then press the foam section you cut out into the foam as deep as you want the recessed section to be (obviously cant be any deeper than the thickness of the foam itself) and super glue it along the seams on the back to hold it in place. Once glued in place you can use your stanley knife to cut off the excess foam on the back and make the armour plate level.
Once you have the pieces done like in the first picture you have to choose one of two options, you can either use Worbla to strengthen the armour plates and give them a leather texture or if you want a cheaper option you can opt to leave the armour as just foam.
If you choose not to use worbla you will need to use the thinner foam to add a border around the armour plates, this is used to sew the armour onto the vest later on (as shown in one of the photos above). To do this simply hot glue the plate to a sheet of 3mm foam and cut about a 5-7mm border around the armour plate.
If you choose to use worbla then watch the attached video showing how I formed my worbla onto the armour plates. Worbla is a thermoplastic and so can be softened by heat, use your heat gun or hair dryer to soften the worbla until it is no longer a rigid sheet, you can then use your hands to carefully mould the plastic over the foam armour. Once the plastic is formed over the foam you should trim off excess plastic leaving a good 5-7mm border around the armour plate.
For the front armour plates, the bottom two plates are actually bent slightly. This can be done after worbla is applied (if you opted to use worbla), as can be seen in one of the photos above I used my stanley knife to cut a "v" shaped groove in a line out of the foam at the back. You can then heat the worbla along this line at the front until it softens slightly, then you can bend the armour plate back and hold it in place until the worbla hardens again.
Step 10: Eagle Shoulder Armour
Which parts to use thin foam and which to use thick?
Generally its pretty easy to figure out when to use thick or thin foam by looking at reference photos of the armour. However, the shoulder armour has so many different layers that it is hard to figure out exactly how to go about getting all the layering correct. If you look at the first image I show you exactly how to use the template.
(Look at the photo of the shoulder template with different coloured sections)
The red sections should be cut as one single piece out of your thicker foam, this forms the base. The shoulder armour requires heat forming to get into the correct shape, the top should be a gentle complex curve to wrap around your shoulder and the bottom piece is bent into a curve to wrap around your arm. Watch the other attached video on how to heat form foam to learn about how to do this.
The green sections should be cut out of 6mm EVA foam the black detail lines on the badge can be scribed into the foam using a ball point pen, go over these lines multiple times. This will leave a permanently dented line in the foam.
The blue section should be cut out of 3mm foam ignoring all the black lines, you can scribe that detail on later using a ball point pen
The yellow sections should also be cut out of 3mm foam and once again ignore the black lines until you have all the green yellow and blue foam pieces glued together, then you can go through it all scribing the lines in with a ball point ben.
Once you have all the thinner foam detail done and the base shoulder armour heat formed you can glue the detail onto the base shoulder using hot glue.
Just like with the front and back armour plates you will need to add a small border around the shoulder armour and can use either EVA foam or use worbla for this.
Step 11: Rest of the Armour Plates
Knee, elbow and the other shoulder pad:
These knee/elbow pieces require much less layering than the shoulder, as before the base is made of the thicker 12mm foam to provide a strong base. you can then layer 6mm foam for the raised detail by hot gluing it on. The knee pads require no border to be made.
The second shoulder is very similar to the first shoulder armour, the top plate needs to be heat formed into a complex curve to better fit around your shoulder while the lower plate is heat formed to wrap around your arm. They again require a border to be made out of thinner foam, however the top plate actually requires two borders! The first one being a thicker 6mm foam and the second being a thinner 3mm foam boarder again being a 5-7mm border.
Shin armour:
The shin armour is another simple armour piece to build. Use the pepakura file for templates, it should be made out of 12mm foam and will require sanding the edges as there are sharp angles in it just like I taught you about in the helmet section of this tutorial. The centre section is raised and can be made by hot gluing the centre piece of foam when it is slightly raised out of the rest of the armour.
Step 12:
Belt buckle and badge:
To make the belt buckle and the badge you simply print out an image of the screen used pieces scaled to the correct size using the method I outlined in the helmet tutorial section about scaling JPG's in Microsoft Word.
This should require the use of both 6mm and 3mm foam, the base of the belt buckle that you layer detail ontop of should be made out of 6mm foam while the badge's base should be made from 3mm foam. You can scribe all detail lines in using a ball point pen.
Step 13: Painting Your Armour
Painting foam parts:
Before painting your foam you must remember that like with the foam helmet you should use a foam brush to paint PVA glue onto the surface of the foam, you should paint on at least 4 layers (or until the foam has a smooth/shiny surface) waiting about 30 minutes between each coat for it to dry or until the foam has a shiny surface. Then you are ready to move onto painting!
(Worbla requires no sealing with PVA glue so you can skip that step when painting if you used it)
For the shoulder, knee and elbow armour plates I suggest you paint a base coat of black all over each of the pieces. For the more basic shoulder, the lower section is actually just completely black so you can leave that as it is now. For the rest of the pieces you will need to put down a second colour so get out your masking tape!
The eagle shoulder piece should have everything masked off except for the raised detail, this is the same for the knee and elbow pads. For the other shoulder's top section you should mask off the two borders you added and leave everything else uncovered.
Once everything is masked off you should paint the shoulder plates gold and the knee pads should be sprayed a navy green colour. When those colours are down you will want to make these armour pieces dirtier using the same black wash method outlined earlier in the helmet building part of the tutorial.
You can see the big difference it makes to the gold paint in the pictures above! It really helps bring out the details. This finishes off the shoulders and knee pads!
For the belt buckle and badge you should paint them gold after sealing them with PVA glue, then finally you should also add a black wash onto those pieces to match the rest of the armour.
Step 14: Making Your Badge Removable
Making your badge removable:
To make your badge removable you can add velcro to it and the chest armour as seen in the photo above. To do this i cut out a short length of both sides of velcro and press them together. I then hot glue one side to the badge and let it set, once set I put hot glue on the opposite side of the velcro pieces and I pressed the badge into the socket on the armour letting the hot glue cool and set again. This allows you to remove you badge and keeps it in place when you place it on your armour.
This completes the armour plates part of the tutorial!
Step 15: Sewing Together Fabric Parts
Materials and tools used:
2 yards Mesh Spacer fabric (can be found here for you american costumers!)
2 yards Any type of shiny black fabric for lining
0.5 yards of black pleather
0.5 yards black corduroy (as thick a grain as possible)
Black thread
12 yards of black leather cord (1mm thickness or less)
Thick string (5mm or thicker)
Plush Stuffing
2 yards black elastic (1/2 inch wide)
Black nylon webbing (1 inch wide)
Velcro (or two extra black zippers)
White chalk
6 Plastic buckles (for 1inch webbing)
One long zipper (preferably brass)
Spray adhesive
Scissors
Basic sewing machine
Large sewing needle
Stapler
Sewing the vest together:
Using the templates for the vest front and back that I gave you, you should take them, your mesh spacer fabric and your lining material. Trace one of each of the templates onto the two materials using your white chalk (this can be rubbed or washed off later with a damp cloth) and then cut these traced shapes out using your scissors.
Unfortunately there is no template for the fabric parts of the shoulders. To make the template I simply draped some of the mesh spacer fabric over my subjects shoulder (may need help from someone to do this) and placed the shoulder armour on top of the fabric. Using chalk I then traced around the outside of the shoulder armour leaving about an half and inch border around the armour (in one of the images above I illustrate this process). I then cut out the shapes I traced in chalk and cut the same shape out of the lining material.
Once you have all your pieces cut out use spray adhesive and spray on to the back of all your mesh spacer fabric pieces, then lay your lining material onto the back of them. This keeps the two pieces of fabric from moving around when you try to sew them together.
To sew the edging onto the vest take your ribbon and cut out a suitable length for the piece you are about to sew it on to, to figure out what length you need just roughly wrap the ribbon around the edges of the piece and cut out a length slightly longer just to be safe.
Use your sewing machine to sew the edging on. Use a pin to pin the first part of the ribbon to the vest's edge, be careful to make sure you fold the ribbon over the edge as evenly as you can. Once you have started sewing the ribbon down you can remove the pin and manually fold the ribbon over the edge using your hands, sewing little by little until you work your way around the entire edge.
Step 16: Making Leather Gauntlets
Making leather gauntlets:
To make the leather gauntlets you will be using the black pleather you purchased. It requires some leather piping and because I couldnt source it in Hong Kong I made my own. To do this take your thick string and cut a long length of it as well as a long strip of your pleather about 1 inch wide, make it as long as you can possibly do so as you need the piping for the gauntlet as well as the collar which comes later on.
Once you have your strip of pleather and your string, fold the pleather over the string and use a stapler to temporarily fix the pleather over the string, do this at about 1-2 inch intervals all the way down the piping.
To make the templates for your gauntlets measure the circumference around your wrist and just below your elbow, you should add about 2 inches to both of these measurements so that the gauntlets can fit over your jacket sleeve. You then take these measurements and make the template as described in one of the images above.
Once the templates are cut out, use your sewing machine to sew the leather piping onto the top and bottom edges and cut them to length, to make it so that it is easy to put on and take off your gauntlets you can sew some velcro strips onto the pleather as shown in the image above. Alternatively you could also just as easily sew a zipper onto the gauntlets instead.
Finally you can remove the staples using your stapler.
Step 17: Making Your Collar
Making your collar:
Using my templates you can make a fairly accurate judge dredd collar, I actually improved upon the template after making the collar for myself so it should be a mroe accurate size and shape when you make yours with my updated template. You will want to use white chalk to trace the two "U" shaped templates onto black pleather and the long strip template onto your black corduroy. Try to have the grain of the corduroy perpendicular to the strip. Be sure to check the pepakura file and mark out which "U" shaped piece is the top piece and which is the bottom, this helps later on.
Cut out your material using scissors, you will also need more of your leather piping so have a good length of that on hand as well (the leather piping goes around the outside edge of the "U"). Once everything is cut out you can start sewing! Be sure to sew everything inside out so that you get nice clean edges. First take your two "U" shaped pieces and pin the inside edges together, make sure you have to top sides of the pleather facing eachother so that you are sewing this inside out. Once you have sewed around the inside edge of the pieces also sew one of the straight edges at the top of the "U", leave the other one as this will allow you to stuff the collar later on. (keep referencing the images above to see what I mean if it is unclear)
Next step is to sew your black corduroy onto the outer edge of the bottom piece of pleather, again doing this inside out. DO NOT sew the curduroy to the outer edge of the top piece.
The next step is to sandwich your pleather piping in between the outer edge of the top "U" piece of pleather and your corduroy. Be sure to have the piped section facing inside as this is again for sewing the whole thing inside out. Pin these three pieces together at regular intervals to hold it all together, It is best at this point to hand sew along this edge but you can attempt to use your sewing machine if you wish.
You can now turn the collar inside out through the small flat edge you left un-sewn. Once turned inside out you can stuff the collar through the same small hole, stuff it well but dont make it too stiff, stuff it just enough for it to be plump and rounded. Finally to finish off the collar you can sew up the small hole. To do this fold all the material into the hole slightly and pinch down, while pinching down you will need to hand sew across the material you have pinched together.
Step 18: Sewing Your Armour to the Fabric
Sewing your armour to the fabric:
To attach your armour plates such as the back, front and shoulder armour, you stitch them to the fabric parts you just made using black leather cord.
If you used worbla you need to make holes in it as you are hand stitching the armour on. Take a nail or a screw and on top of a wooden chopping board hammer the nail down into the plastic at regular intervals (about 1 hole every 1cm or less). This helps accurately mark out all the positions that you need to drill and will make it easy as the drill bit will sit in the dent you create from that process. Then you simply drill through each of these marks with a thin drill bit (I used a 1.5 mm drill bit). Once that is done you can start to stitch the armour on by hand using a sewing needle and your black leather cord, be sure to stitch it on tight.
If you didnt use worbla then you can simply stitch through the foam without drilling holes, just try to make sure you stitch at regular intervals.
Step 19: Strapping All Your Armour Together
Strapping all your armour together:
With this step there isnt much to be said, simply sew straps and buckles onto the fabric parts as shown in the diagram above. Most can be done using a sewing machine but the more parts you sew together the harder it gets to use a sewing machine for the job so you may need to hand sew the last couple of straps or elastic on.
You will notice in the diagram that some two straps are sewn on top of the two chest armour plates. If you used worbla you will need to drill holes through the worlba so that you can hand sew the straps through the armour and the fabric vest. I drilled two holes in each chest plate to sew through.
Step 20: Finalizing and Extra Bits
Finalizing:
To finalize your costume the last parts you have to add strapping to are the two shin armour plates, the elbow and knee armour and finally the belt buckle. To do this I used elastic once again, reference the photos above to see where I added elastic. Once that is done you have completed your costume.
To put your costume on you should have a black leather (or pleather) jacket and black jeans to wear underneath all the armour as well as some black boots.
Optional bits:
There are certain extras that you can purchase that can add a lot to the cost of the costume but really add to the look of the costume as a whole.
First is a set of black airsoft knee and elbow pads, you can rip off or cut away the plastic armour on it and hot glue your foam elbow pads in place onto the fabric. This makes the strapping much easier as the elbow/knee pad already has adjustable straps. (I definitely suggest doing this)
Second is a pair of black leather pants if you so wish to use them, this however may get very hot when wearing the costume for any extended period of time. (Not very necessary)
Third is a black airsoft tactical belt as well as an assortment of black tactical pouches of different shapes and sizes to go onto the belt. You can fill these with grenades and pistol magazines if you so wish or leave them empty.
Fourth is to buy a set of black airsoft gloves with a plastic section over the knuckles that resembles carbon fibre (reference image above)
Finally is a glock 17 airsoft pistol and a black pistol holster for it to strap onto your leg.
With all these extras your costume will be all that much more amazing and complete!
Step 21: Like You Walked Right Off the Set
The final tip I could give you on how to make it look like you really are a street judge on active duty is to dusty up your armour vest. To do this simply grab a few pieces of white chalk, put them into a sock and smash the sock against a hard surface for awhile. Once you have smashed the chalk into smaller pieces you should be able to rub the sock onto the surface of the armour and vest and this should allow some chalk dust to come through the sock onto the vest and armour!
Hope you enjoyed this tutorial, if you like my work click here to head over to my facebook page and see everything else I am working on!
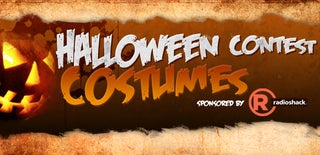
Participated in the
Halloween Costume Contest