Introduction: Homemade Fire Piston
I live in lovely Ol' Seattle. It likes to rain here tons, specially during winter, fall, and spring. When it rains, I like to dink around in the machine shop at my place of employment. I am also an avid hiker and camper, so this project fits right in with my interest. I designed and constructed a fire piston on the lathe at work.
A fire piston works like a diesel engine, take air, compress it fast, and Boom. There is no boom, just embers if you use the right fuel.
Step 1: Prep and Materials
This is not my first attempt to make a fire piston, my second time actually. The first time I made this I based it off of Makes Clickspring fire piston. It would work but it would not always seal; too many parts. So I designed my own using solidworks to model it up. You can view the schematics in the attached pdf. One of the tolerances is incorrect; .495 +.003 -.005 (not .050). Make any design changes you want, but the diameter of the piston and cylinder bore need to have a tight tolerance or the fire piston will not work.
Items you'll need are the following:
- 1"od x 5" long aluminum rod
- 1"od x 5" long bronze rod (I used a scrap piece of metal from a casting at work)
- 1/2" od x 3/8" id o-ring (buy some spares just in case)
- Lathe and turning bits
- Center, 1/4", 3/8" 29/64", and 1/2" drills
- Cutting Fluid
- A drop of oil or lube
- A fine file
When working with a lathe, make sure you have long hair tied back and necklaces taken off, you don't want to be sucked into a lathe. If your using the lathe properly you wont need any ear protection but you will need safety glasses to protect your eyes from flying metal missile chips. Refer to the provided pdfs for the dimensions that I used.
Attachments
Step 2: Cylinder: Face It and Drill It
I suggest that you make the cylinder first so you can test the piston fit without taking the piston off the lathe when you make it. First chuck up the aluminum bar, give the exposed end a nice finish cut. After you establish the finished face drill into it with the center drill first, then the 1/4, then the 3/8, then the 29/64, and finally the 1/2. Once the hole is established, check the finish on it. If it is smooth move on, if it is rough, I would suggest using a 1/2" reamer to clean it up. Mine was nice and smooth. Throw a center stock on that new hole and move on.
Step 3: Cylinder: Turn It Down to Size
Take some layout ink and mark the length to cut on the rod. Start cutting away. Each lathe is different on what it is capable of, mine is old so any cutting pass greater than .040" will stall it. Take rough cuts up until you reach an od of .890. The last pass will be a .015 finish cut and I would suggest the use of a powerfeed feature if you have one, will give you a really nice surface finish. I used a feed rate of .0015" per revolution for the finished cut. The cylinder should be nearly done now.
If you want to add some decorative grooves, now is the time to add them before we part this puppy off. I put six grooves in at no particular dimension, just 3 on either end. Looks nice.
Part it off, flip it and finish turn that puppy to its finished length.
Step 4: Piston: Facing and Turing
Chuck up the bronze bar, put a nice finished face on her like the cylinder. Use the center drill and drill to a depth at roughly 3/16-1/4. Put the center stock onto it and begin the turning process. Turn it all down to finished diameter of .875". Use the layout paint to establish the length of the smaller od. Cut away until you get to about .015" above the finished diameter. Finish turn the piston similar to how the cylinder was turned.
The next step is the most crucial, using a parting tool or groove cutter, cut the groove for the o-ring. If you have little experience cutting grooves, I suggest taking small cuts and checking the o-ring fit with the cylinder as you get closer to the finish dimension. It should be a nice fit such that when you put the cylinder on the piston, you should feel back pressure. The cylinder should be pushed back out by the trapped pressure when released. If you are at the finished dimension and cant get a seal, try changing out the o-ring. If that does not work, then either the piston or cylinder will need to be remade.
If you get a good seal, part off the piston, flip it and face it to the finished length.
Step 5: Extra Steps
I decided to add some holes to my design to attach some paracord to. I drilled a 7/32 hole in the piston and a 3/16 in the cylinder. Clean off the layout ink with a light sanding or filing.
Step 6: Finished Product
Put the o-ring on the piston and apply a couple drops of oil or lube. Do some compressions to lube up the cylinder and tie some paracord to her. This project took me a little under 4 hours to make start to finish; I did it in one sitting.
To use this guy, you will need to use it in conjunction with some char cloth. Put a little piece of char cloth in the opening of the piston, load it, and compress it really fast and hard. Repeat until you have embers burning. Does not work with paper, only char cloth. I will post a video and update this guy when I get some char cloth. Happy making, I hope you guys add this guy to your survival kits, I know I will.
UPDATED 2.17.2016 - Added a video of some embers burning and updated the pdf drawing.
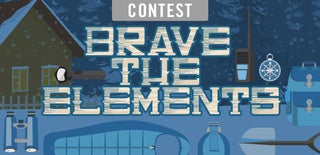
Participated in the
Brave the Elements Contest

Participated in the
Rainy Day Challenge