Introduction: How to Cast an Ear in Plaster | DIY Earring Display Stand for Jewellery Photography
I have wanted to have a go at casting plaster for ages, and since I've never seen an ear attempted, I thought it would be a good choice. Of course, I realised quite quickly why I haven't seen an ear cast before....it's very tricky!
I don't want my hair getting stuck in the alginate, and I don't want alginate in my ear canal, so I decided to use an ear model in place of a real ear :)
My second idea was to turn this cast ear into an earring display stand. I sell jewellery online and showing proportions is always difficult so this is going to be really handy.
I hope you enjoy this tutorial, and thanks for reading.
Remember to be careful around plaster....it can be irritating to skin, you mustn't breathe in the powder, and it heats up as it sets so caution is required.
Step 1: What You Will Need
- Realistic silicone ear model; often listed under medical supplies, I found mine on Ebay for about £8 or so.
Why did I not use a real ear? Well, unfortunately ears are very tricky things, often with a lot of hair next to them that gets in the way, and I don't want to risk getting alginate stuck in my ear hole either!
- Plaster; Fine casting plaster powder.
- Alginate; Moulding material often listed as dental supplies.
- Mixing cups/bowls; at least half a litre in volume, probably bigger. Small cups get awkward to use. Large plaster bowls would be perfect.
- A container for making the mould in; Because my mixing cups were larger at the base than the pieces I wanted to cast, I just used those to make the mould in. I've seen people use empty pop bottles, DIY cardboard moulds lined with plastic bags...you need a leakproof container, basically, that is a little larger than what you want to cast.
- Stirring stick; paint stirrer or plaster spatula for instance. I used a lollipop stitck but it was too small to be efficient.
- A stand for the ear; I used the stand of a 'helping hand' that I use for soldering.
- Measuring jug
- Weighing scales; Accurate digital scales if at all possible. My kitchen scales are not accurate and I think cause a few problems for me in terms of the mixing ratio.
- Drill/mini drill
- Glue; For attaching plaster piece together, which you may or may not needing depending on your design. I used superglue for this (UHU all-purpose). I also covered the finished cast with a diluted 'PVA Bond' glue which is meant for porous surfaces.
- Polymer clay, ceramic tile/baking tray, oven; I used a small amount of FIMO to cast an additional part for my stand, but this could be optional as you may choose to drill the hole for the stand directly into the base of the ear shape.
- Wet/dry sandpaper; I used 320 grit as that is what I had. I would recommend a finer grit though.
- Final finish; You may want to coat the plaster with a spray sealer or other finish to protect it. You could add a primer then paint it, or coat it in resin. There are lots of options for finishing.
- Safety specs & breathing mask.
- Utility knife
Step 2: Make Any Attachments or Additional Pieces
If you want to make any shapes besides the ear casting then sculpt them now out of your preferred mouldable material.
I wanted a piece on the back of the ear casting to attach it to the stand, so I made the shape I wanted in polymer clay.
I put it on a ceramic tile and baked it for the recommend time & temperature in the oven.
Step 3: Cast the Ear
I put some washable PVA into the ear canal of the model the day before casting anything in order to block the deep hole in the ear. This was to make sure alginate didn't get stuck in the ear or just be too difficult to remove later.
I poured my chosen amount of water (300ml) into my mixing cup, then weighed out the amount of alginate powder I required according to the packaging instructions (100g). My scales were inaccurate and I think my mix ended up a bit thick but it worked in the end!
I added the powder to the water bit by bit, mixing quickly as I did so. You have to work quite fast as this stuff sets in minutes.
I then transferred some alginate from the pot (with my stirrer) directly onto the ear model. I wanted to put some into the central detail of the ear to make sure I didn't get air bubbles here.
Unfortunately, this worked for the centre, but I completely missed the undercut on the upper part of the ear, and also the undercut behind the ear. I wasn't thorough enough! So you just need to make sure you put alginate anywhere you think the alginate may struggle to reach or the places most likely to get air bubbles (undercuts ad small details). You can work the alginate into these areas with your hands if it's easier. Remember to be fast though!
Then I pushed the ear down into the alginate in the pot, wiggling it a little to make sure it's all covered. I also tapped the pot a few times to try and knock out any air bubbles.
I held the ear model until the alginate turned to a jelly-like substance and could support it (only a couple of minutes).
A few minutes later (see your instructions), I removed the ear model carefully to reveal the alginate mould.
Step 4: Repeat for Any Additional Parts
I mixed alginate again (a little less this time because it's a smaller item) to make a mould for the clay piece.
I used a tiny piece of double-sided tape to stick the piece to the bottom of the mixing cup. I then mixed up the alginate and poured it over the top. This isn't the best method if you want to replicate this piece accurately (like I did with the ear), but I didn't mind if it was inaccurate because it will be at the back of the ear casting and out of sight.
Once the alginate is poured you can tap the cup on the table to try and knock out any air bubbles.
Once the alginate had set, I removed the polymer clay piece and turned the alginate mould the other way up inside the cup.
Remember throughout this process that alginate and plaster, even when wet, go in a bin and not down the sink :)
Step 5: Cast the Pieces in Plaster
Next, you need to mix up your plaster (water into the cup/bowl first, then the powder whilst mixing), in the ratio that your instructions state. It will be a creamy paste consistency, a bit like toothpaste.
Too runny and the plaster is more likely to contain air bubbles and be brittle when cast. Too thick and it might not be able to flow easily into small areas and details in the mould.
Wear safety specs and preferably a mask as you don't want to breathe plaster powder in.
Pour the plaster into the alginate moulds, trying to slide it in down one side rather than dropping it directly on top of the opening. You need to think about how to minimise air bubbles.
When you have poured enough in, tap the cups against the table a few times to knock out bubbles.
Leave to set hard.
Step 6: Finishing the Cast
I used my utility knife to cut the mixing cups to remove the alginate.
I then carefully removed the alginate from around the plaster pieces. Apart from the undercut areas of the ear that I missed - which I mentioned earlier - I was pleased!
Next I used wet and dry sandpaper (underwater, in a bowl of water) to make the edges smooth and straight, and basically shape the plaster how I wanted it.
I needed to drill the hole in the additional cast a little deeper with a drill so it sat nicely on the stand.
I then left the plaster to dry out for a day (at least) and then glued the 2 plaster pieces together.
Now it sits nicely on the stand to display.
If you want to add a sealer or other finish, you can do that now.
Step 7: Drill a Hole
If you intend to use the ear as a display for selling earrings, you can then use a mini drill to carefully drill a hole through the ear lobe.
I used a 2mm drill bit.
I think I might make a prettier stand for the cast in the future as this one is maybe a bit industrial looking :)
Step 8: Finished!
You have cast an ear!
I hope you enjoyed this Instructable.
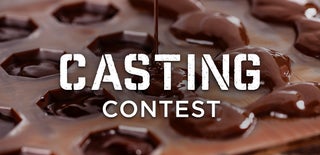
Runner Up in the
Casting Contest