Introduction: How to Create a Pneumatic System for (F.I.R.S.T) Robots
This is an instructable primarily for next years members of the Scarlett Robotics team (4733), however; it will also apply to all first or second year FIRST robotics teams who have never used pneumatics, or to anyone who wants to add pneumatics to their own robots(may want to consider other sources for parts the ones that are allowed in the FIRST competitions are expensive).
This isntructable contains the basics along with a few tips on speeding up flow rates.
For those that don't know F.I.R.S.T (For Inspiration and Recognition of Science and Technology) programs are designed to show kids that science and technology are cool and fun, a message I think Instructables agrees with. There are multiple levels of competition starting with the Lego League were elementary students build robots using the Lego mindstorms platform, then the First Technology Challenge that uses (I think) the Vex robotics platform, and then the First Robotics Competition were High School students build and design their own robots from scratch. Anyone using this website would probably really enjoy the program and I highly recommend it if you have the chance.
Also if you need help for anything that I don't (or do) cover please post a comment or go to the Chief Delphi Pneumatics forum
Step 1: Why Pneumatics?
Pneumatics are systems that used compressed air to accomplish their task. Anyone who uses tools connected to a compressor, like a dentists drill, or a city buss (the doors), has experienced a pneumatic system.
Ok, so that's great but why would I want to use it?
Pneumatics are actually really easy to set up, and they facilitate rapid changes, ie. when something breaks on competition day it is really easy to replace or add something new, they are also very powerful, the maximum allowed air pressure of 60psi (for FIRST competitions anyway) is more than enough to accomplish most things. Pneumatics are relatively light (our whole system was about 10lbs) and they don't require too much in the way of battery power. Pneumatics are also easier to design, you don't need to align chains and belts with special housings or anything.
Drawbacks: they do take up allot of space, and it requires more programming in order to get the compressor and solenoids to function, they also require a large investment in parts as the system requires all the pieces in order to function(one ram is not a stand alone piece like an electric motor).
Imagine wiring up a motor or any other electronic component, but instead of positive and negative you just have one set of tubes that work anywhere, there is no gauge(size of wires) or wires to be stripped, and you don't need any tools to put it all together(no more soldering and heat shrinking). I think we have all had difficulties trying to fit the right sized screwdriver into the correct slot and twisting it "just so" in order to get a wire to stay in place. All of that can be (for the most part) ditched, pneumatics are simple and clean (not like hydraulics).
Also if your doing this on your own you don't need any programming (it would help) their are valves that can be triggered by air, unfortunately this is not allowed by FIRST.
Step 2: What You'll Need
So what will you need? (I have adapted this from the 2014 FIRST Pneumatics manual found here)
Compressor: This is the device that squishes all the air together, it is the basis of all the pneumatics. It gets really hot during operation so make sure that it has a fan near it, and that no electric or pneumatic cables get close to it as it will melt insulation of wires and put holes in pneumatic cables. It also causes a lot of vibration so take that into consideration when you are mounting it to the robot, so don't put it next to the camera responsible for autonomous operation for example. Also when wiring it put the current through a 20 amp fuse or breaker(FIRST says breaker only but ours managed just fine on a fuse and the safety inspector didn't mind). The compressor we got in the pneumatics kit was a Viair 090C, If you have the choice don't get this one, most of the more experienced teams use a different one as this one starts to die when it gets warm, the run-time is about five minuets of run-time for about half an hour cooling. Don't wire the compressor backwards as it will break, its like an led not a motor. You can order one Here
You will also need a spike relay to control the compressor.
Pressure Release Valve: This is a piece that must be connected purely by brass to the air compressor (FIRST Rules if your doing it on your own it doesn't really matter), it is a mechanical safety measure that will leak air when the pressure gets too high. It can be adjusted by moving the rings that are threaded around it.(I'll cover this later). The one we got is a Norgren and it works perfectly you can order your own here.
Other connectors that you need to attach the pressure relief valve: a male1/8in npt (national pipe thread) to 1/4in female connector order onehere. a 1 male 2 female 1/8npt can be ordered here. You could also use a triple female 1/8npt connector* and a male to male 1/8in npt connector* ( AndyMark doesn't sell these pieces but I would recommend using them as they have a much more broad use than the 2 female one male connector, *these links are untested they are for demonstration, we found our pieces locally*.
Pressure Switch: This piece works with the electronics as a sensor, when the pressure gets above 120psi (supposedly, ours tripped anywhere from 80-110psi) it sends a signal to the program that is used to turn off the compressor. A triple female 1/8in npt brass connector(link above*) can be used to connect this to the rest of the system.You can order one here.
Air Tank(s): These hold the compressed air for use later. You will probably want as many of these as you can fit on your robot. Beware don't get the white tanks that have a threaded port, as they have a tendency to explode. The black tanks have served our team well. You can order them from here.
Regulators: These limit the pressure to any components downstream, multiple regulators mean that you can have components that run on different pressures. Anyone who has been scuba diving has used these, they stop the air in the tanks(120psi) from blasting into your mouth.There is an arrow on the bottom that shows which direction the air should flow through them. If you put them in backwards pressure will leak out of the regulator once it gets above the specified pressure. The top of the regulators that we got have instructions printed on them, and have the ability to be pressed down to lock the knob and stop the pressure from being changed. They can be ordered form here.
Gauges: These show what the pressure is inside the system I would recommend getting 3-4 depending on how many different pressure lines you plan on having. These screw directly into the regulator. You can order them here.
Solenoid Valves: These are like breakers or transistors in an electric system. When they are triggered (from the program) they switch the flow of air from one port to the other, some are double acting and can be controlled in both directions, some are not and will automatically switch back once the signal is gone. These allow the pneumatic rams to be controlled remotely. The ones that we got were FESTO valves, we got two different sizes, the larger the holes (bore) the faster air can flow through the valve(for FIRST the max bore size you can have is 3/8in). So if you need speed get the larger valves. The small ones can be ordered from here and if you don't want to have to MacGyver a way to connect the wires to them you will want a couple of these per solenoid as well and the wires to go with them. You will also need three of thesesmaller push to connect fittings per small solenoid or you can order them in a package from here. I believe this is a larger solenoid, however we didn't order ours, we got ours locally.
Plug Valve(Ball Valve): these are a manual way to control the flow of air you will need at leastone in order to pass your safety inspection. Get lots of these(4-5) as you will find yourself wanting a fast way to block certain ports of the pneumatics without having to assemble a bunch of brass fittings and plugs together. They can be ordered from here. Our team used some brass ones, I think they came in the kit but it appears that they are not sold by AndyMark anymore.
Push to Connect Fittings: these are the pieces that connect all the components together. Get lots of these(50-60) they should all be 1/8in npt and 1/4in push to connect. They come in all shapes and sizes there are straight ones,elbow ones, flow controller ones(these are kind of like regulators, but they change speed not pressure), y connector ones, T- joint ones, or the package deal. Some of these come pretaped, but others(and ones that you use more than a couple times) will require Teflon tape(note the low density if you are buying else ware), there is a correct way to apply Teflon tape(I didn't make the video).
Tubing: This is the tubing that the air will flow through to get to the various pneumatic components. This is also the chance to make your robot stand out during competition, advanced teams have all sorts of crazy coloured translucent, or glow in the dark tubing. All jokes aside the colour does help differentiate between high pressure and low pressure lines, or which tubing connects to which cylinder, so its best to get a large role of one colour(preferably black) and a bunch of smaller roles of other colours. All tubes should be 1/4 outside diameter. Ours came in the kit of parts that all teams get but you can order your own here
Pneumatic Cylinders(Rams): This is what all the other components are for, these use the stored air pressure to extend(or contract) in order to accomplish the task. There are all shapes and sizes, the bore (which is how wide the cylinder is) determines how much force the cylinders can exert( the larger it it the more square inches the pressure can act on therefore more force applied), please note that large bore cylinders (2") are not a good idea because they fill up slowly and they will use up a lot of the air you have stored. The cylinders that our team used were 1 and 1/4inches . The throw/stroke(how long the movement of the cylinder is) will determine how long the cylinder is, again I recommend keeping it reasonably small, as larger cylinders don't fit very well on the robots and are more prone o bending. All FIRST teams get two free bimba cylinders per year, in the kit of parts there is a coupon that you should use, even if you are not using them that year so that you can stockpile parts for later. You can also order them from here, but be careful to check that they have (max of) 1/8" threads.
Most likely you will already have these other tools if you are this far along in your robotics experience, but just in case:
Small crescent wrench
Allen Keys (imperial and metric)
Wire Cutters
Vice Grips
Whoa that's a lot of stuff, but trust me it's worth it, it will open up all sorts of design ideas for your team. And everything is reusable for the next year, so you really only need to buy it once.
Step 3: How Pneumatics Work
Pneumatics work by controlling the flow of compressed air. Much the same way that electronics control the flow of electrons. Pneumatics use valves to control the flow of air, these valves can be triggered by other sources of compressed air (however valves like this are outlawed in FIRST competitions) , or by a source of electricity, or by hand (these aren't very helpful for robots though). The valves that are controlled by electricity are called solenoids, because they use an electric current to induce a magnetic field which moves pieces of metal around and forces air to move in a particular way.
The most simple pneumatic system has only one valve that is controlled by hand. Anyone who has used an air nailer has used a system like this. The air compressor compresses and stores the air and then when the user pulls the trigger air is released and drives the nail into the wood(or whatever your nailing).
The valves that we use in FIRST robots are of the solenoid variety. The first picture shows how a double acting solenoid forces a piston into the down position by filling the top section of the cylinder with air. The second picture shows how when the solenoid is triggered by the program, the piston extend.
That's it pneumatics are actually really simple. Like everything though pneumatic systems can become really complicated, however for a Robot the simple systems work well and there is no reason to make it super complex.
Step 4: Basic Setup
The basic pneumatic system required for FIRST competitions goes like this
Compressor ---> Pressure Relief Valve ---> Air Storage Tank ---> Gauge ---> Pressure Switch ---> Ball Valve
- Attach the compressor to a Spike Relay, use a 20 amp fuse. Attach the spike relay to the power distribution board again use a 20 amp breaker. Attach a pwm cable to the Spike, and then ask your programmers which port on the cRIO (I/O board) to plug the other end into. (pic 1)
- Thread the 1/8" npt male to 1/8" npt male connector into the compressor, make sure to apply Teflon tape to all threaded connections. (pics 2-6)
- Thread one of the brass 1/8" npt T-Connectors to the exposed end of the 1/8" npt connector. (pic 7)
- Thread the 1/8" npt to 1/4"npt enlarger onto the base of the Pressure Relief Valve. (pic 9)
- Thread the Pressure Relief Valve assembly into the "top" of the brass T connector. (pic 10)
- Optional - orientate the Pressure Relief Valve so that it is close to the compressor in order to save space. (pic 11)
- Thread a straight 1/8" npt to 1/4" push to connect fitting into the last hole in the brass T connector and push a piece of tubing into it, then push the exposed end of the tubing int a Air Storage Tank. (pics 12-13)
- Push a piece of tubing into the far end of the Air Storage Tank and attach it via a 1/8" push to connect fitting to a threaded 1/8"npt T-connector.
- Thread a gauge into the top of this brass T-connector (pic 14-15)
- Assemble another threaded 1/8"npt T-connector so that it has push to connect fittings on both of the "bottom" two ports, and thread the Pressure Switch into the "top" port.(pic 16)
- Attach the assembly you just created to the T-connector that has the gauge via a piece of tubing.(pic 17)
- Assemble a ball valve so that it has a Push to connect fittings on both ends, and attach to the T-connector that has the pressure switch in it via tubing.(pic 18)
-Attach two wires onto the terminals of the Pressure Switch and wrap with electrical tape. Then splice these two wires into a pwm cable, use only the wires from the pwm cable that connect to the two outside pins for this, the remaining middle cable doesn't attach to anything and should be wrapped in electrical tape. (pic 20)
- Ask your programmers which port to plug the spliced pwm cable into, this changes based on each team's program.(pic 21)
All the parts of the system are now together we just need to calibrate the system.
- Turn the robot on, the compressor should start running.
- Watch the gauge, when the needle reaches 120psi turn the robot off.
- Adjust the bolts on the Pressure Relief Valve until air starts to leak out of the small hole on the top.
The basic setup is now done, the next step deals with adding a solenoid and piston that can actually do something.
Step 5: Add the High Pressure Line
To add a high pressure line to your system, one that can actually do work, start by:
- Cutting the tubing between the Air tank and the pressure switch
- Insert a T connector into the space you just made by cutting the tubing
- Push a piece of tubing into the exposed hole in the T connector /* Keep the length of the tubing as short as possible from here on, as it will conserve air and make the system faster. */
- Push a regulator onto the piece of tubing extending from the T connector (will need to thread a push to connect fitting in), make sure that the arrow is pointed away from the tube not into it.
- Push another piece of tubing (possibly a different color depending on your color scheme) into the port opposite the one you put the tube in, the arrow should be pointing into this tube, from here on in the system the air pressure will be set by the regulator.
- Thread a gauge into either of the other two exposed ports on the regulator (make sure it is Teflon taped).
- In the package containing the regulator there should have been two small threaded pieces, they probably have an Allen key shaped hole in the top. Wrap one of these in tape and thread it into the remaining port of the regulator.
- Set up your solenoid by threading the m7 threaded push to connect fittings into ports.
- Push the tube extending from the regulator into the "bottom" of the solenoid, the bottom only has one push to connect fitting the top has two.
- Put different colored tubes into each of the remaining ports on the solenoid, one will extend the cylinder, one will contract it. We won't know which one does what until we turn the compressor on.
- Put these tubes into the top and bottom of the ram/actuator/cylinder. The cylinder will require push to connect fitting to be threaded into the holes on the top and bottom of the cylinder, I suggest elbows as they have the ability to pivot freely.
- Turn on the compressor. Watch out the cylinder may extend, so don't have it near you, it won't shoot out fast but be careful non the less.
- If the Ram extends out then the tube at the bottom is receiving air, if it doesn't the tube at the top is receiving air. Mark the tube that is getting air with a piece of tape.
-Turn the knob on the top of the regulator and watch the gauge attached to the regulator to set the pressure. When you have it at what you need (not above 60 for FIRST competitions) then push the knob of the regulator down, this will stop it from spinning and changing the pressure.
- Arrange the tubing to suit your purpose, do you want the cylinder to extend are contract when the robot is turned on?
- Attach the wires onto the "left" and "right" ends of the solenoid, these will probably need to be spliced into a pwm cord in order to fit into the solenoid breakout board, confer with the programmers to determine which port it should be plugged into.
- Now your robot has the ability to raise and lower a cylinder, what that will achieve is up to you. /* the program needs to be set up correctly, but I don't know enough about it to instruct you, there should soon be an instructable about programming a FIRST robot, so check that out. */
Step 6: Adding a Low Pressure Line
Adding a low pressure line is exactly the same as putting in a high pressure line, except that the regulator is set to a different pressure.
Cut a space in the tubing between the T connector of the high pressure line and the pressure switch, put in a T connector:
- Follow the same processes (step 4) for plumbing a regulator and solenoid.
- Adjust the regulator so that it has a lower pressure than the one ahead of it.
- Continue this processes for as many different pressure lines as you want in order of descending pressure. /* The order won't affect the system, but it is conventional to do it in this order. You may want to color code the different lines for easy changes once it's all tangled up in the belly of the robot*/
Step 7: Frequent Problems
This is sort of my FAQ page with frequent problems and solutions to said problems. Please leave a comment if you have something you would like to add.
It's Leaking What do I Do?
Make sure all the ball valves are fully closed, this has been an issue many times on our team.
Then listen for where the air is leaking, if you are somewhere that is loud (like the competition) you have two other options, a spray bottle full of soapy water, or a large diameter tube. If you go with soapy water, spray it near any connections that may be leaking and watch for bubbles. If you are using the tube, place one end near(or in) your ear and move the other around until you can hear the leak. The soapy water is a better alternative because even a small amount of pressurized air can seriously damage your eardrums.
Most of the time a leak is caused by push to connect fitting not being fully engaged, or coming loose. Make sure that the push to connect fittings are pressed in all the way and then give them a little tug out to set the teeth that are on the inside into the plastic.
It could also be that the tubing isn't cut at 90 degrees, tubes that aren't cut straight may leak.
If it's still leaking add Teflon tape to the threaded connections.
If it is still leaking look for damaged cables. They could have been melted by the compressor, cut by a fan, pinched in machinery ect...
It gets up to a certain pressure then leaks out?
This is one of two things:
1.) A regulator is installed backwards, switch the orientation of the regulator that is setting the pressure that the system gets up to before it starts leaking.
2.) A connector is leaking somewhere after the regulator. Check all of the connectors after the regulator that is set to the pressure that the system is leaking at.
Air leaks out of the solenoids when they are fired?
This is normal, the holes on either side of the input tube are exhaust ports that vent the air previously stored in the piston.
Any other problems please check the Chief Delphi forums and post a question there.
Also as promised a few ways to speed up the pistons, FIRST contests usually involve throwing something into a goal of some sort, so speed is usually more important than the force exerted by the piston.
In no particular order:
1.) Get larger solenoid valves. This allows air to flow through hem more quickly.
2.) Get small bore cylinders, this will reduce the amount of air that needs to flow into the piston to get it to extend all he way.
3.) If your piston needs to move fast forwards, then remove the tubing that goes from the port on the front of the cylinder to the solenoid. This means the air only has to flow through the solenoid once, but it also means you can't retract the cylinder.
4.) Shorten the lengths of the tubing from the solenoid to the piston, this uses the same principle as using small bore cylinders, less air to move.
5.) Add a surge tank (air storage tank) before the solenoid ,but after the regulator. This gives a large supply of air that is at 60 psi. And means that air doesn't have to flow through the solenoid. The downside is that you are going to use up all the air in the tank when you retract the cylinder.
6.) Make sure the regulator is set to the max pressure, 60psi for FIRST competitions.
Thanks for reading, I am headed of to University so I probably wont be on the site as often as usual (or maybe more often?). Please feel free to post comments about questions, answers, or anything I missed. I'll do my best to update this post.
-Lucas
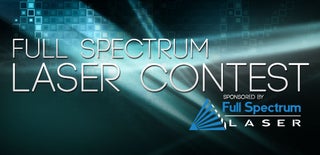
Participated in the
Full Spectrum Laser Contest
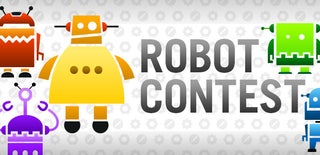
Participated in the
Robot Contest
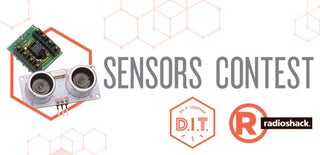
Participated in the
Sensors Contest