Introduction: How to Forge a Throwing Knife From Recycled Farm Steel
This is my series on forging a throwing knife out of an old hay mower blade. These have a tendency to accumulate around a working farm so I decided to try to have some fun with them. They are made of good quality steel suitable for knife making, but the challenge comes from not having a lot of material to work with.
Dividing up forging a knife into steps is a little tricky because of the fluidity of the work, but I will give it my best shot.
Lets try breaking it down like this: Material Selection, Forge the Handle, Forge the End Ring, Forge the Blade, Grinding, Heat Treat and Function Test. Six steps ought to do it.
In this Instructable I will be using.
A location that is suitable and made as safe as possible for blacksmith type activities, and all appropriate safety equipment.
An old hay mower blade
A coal forge.
A 2.5 lb. farrier's rounding hammer, and a 2 lb. ball peen hammer
Tongs for flat stock
An Anvil
A Craftsman 2x42 belt sander
Birchwood Casey Permablue
Step 1: Material Selection
The first step is choosing your material (Fig.1). You want to choose a blade that is not chipped or cracked, and has enough material to make what you want. At this time you can inspect the blade and see if there are any features that you can incorporate into your finished product. For instance, I kept the existing bolt hole, I just made it larger.
The first forging video with show all of these steps up to the "Crank Up The Grinder" step.
Step 2: Forge the Handle
These blades are quite thin, so you really need to watch them if you are use coal or charcoal. Gas is a little more forgiving but it will not take too long at a welding heat to damage them beyond usefulness.
I found that they forge well at a orange/yellow heat(Fig. 4).Once you notice the steel cooling you should stop and put it back in the forge.It is ok to planish-smooth out with a few light taps, or straighten slightbends at a black heat. But use extreme caution because you can crack the steel or damage your tools.
These have an edge for mowing but we need to get rid of that for our knife making purposes. You start buy squaring up the edges and hammering the existing bevel back into the main blade. This is preferred over grinding because you do not loose any material.
After it is squared up take it to the horn and start shaping the curve with the round side of the hammer. We are basically shaping and stretching at the same time. We want to get the main shank of the handle down to about 5/8" or so and have symmetrical radii on our curves.
While forging this style of throwing knife it is important to keep it symmetrical. You can do this by not working one side for very long before you flip it over and do the identical thing to the other. In the video you will notice that I am constantly flipping it and looking at it to try to keep the symmetry. The better you do this during forging the less grinding you will have to do.
Also with this material it is very important to keep the edges from rolling and the entire piece as flat as possible while you are forging. Use the round side of the hammer to push any rolled edges back into shape.
The video in the first step with show all of these steps up to the "Crank Up The Grinder" step.
Step 3: Forge the End Ring
In this step we are just basically enlarging the existing bolt hole. This is mainly for balancing the knife, but aesthetics also plays a role. This may be used to attach a bit of ribbon to assist with throwing. Makes it more like a dart.
The way to do this is to hammer the corners back into the ring while you have it on the horn. You want to turn the piece around as you strike rounding the end (Fig.10). This shop fabricated anvil has a very finely tapered horn that works well for this. You may have to fabricate tool that will work.
Once you get the hole to the desired size and its round, you should stop. The more you fool with it the more of an chance you have of getting it out of round. If the outside of the ring is not the way you want it you will fix this during the final grinding.
Step 4: Forge the Blade
To get the square end to a tapered point you must first knock the corners into the blade and make the end into a round or oval shape (Fig. 12). You do this by working the material from the end swinging back toward you and rotating the angle of the hammer in between each strike.
Once you get the corners effectively rounded, you can start tapering the point (Fig.13). You will mainly use the flat side of hammer for this. Hold the piece at the desired angle on the anvil and angle the face of the hammer as you strike as well. As the point develops move the piece to the edge of the anvil, but not over it (Fig. 14-15). While striking let part of the hammer hang over the anvil edge with glancing blows. This will allow you to get a fine point with out hitting the anvil with your hammer(Fig.15-16).
In figure 17 I was using a tool called a spring fuller tool to put a small concaved curve in the face of the blade called a fuller. In this size of blade it is mainly for aesthetics, but in larger blades and swords it provides extra strength if done correctly.
As you get closer to finishing it is a good idea to brush the scale off the piece and the anvil before you strike (Fig. 16.A). This will keep the piece smooth by not forging over the debris that creates imperfections.
When you have your profile the way you want it you will then start beveling the edges. (Fig. 19) This is done much the same way as creating the point on the edge of the anvil, except that a rounded hammer profile is used. This will cut down on hammer marks in the blade. This is more of a finishing stage and does not require very heavy strikes, multiple light strikes works better.
Again, the video in the first step includes this step also.
Step 5: Crank Up the Grinder
The next step is grinding to final shape. I use a 2x42 Craftsman Belt sander but this can be done in a number of ways as long as you can move up to finer grades of sanding media. I used 32,80,180, and 400 grit belts with a little hand polishing with 1500 and 2000 grit wet/dry sheets.
As with the forging, symmetry is key for this style of knife. Grind one side a little then flip it and grind the other. Constantly looking at it and feeling of it(after cooling it in water) to make sure you take off material where you want, once its gone you can't put it back. Just take your time. Cooling it water is a must to allow you to hold it.
Step 6: Heat Treat and Function Test Finale
For the heat treat I used my homemade gas forge, its half a muffler, fire clay and fire bricks. I purchased a Mini Atlas style burner. This setup works ok for this sort of thing. Planning on building a better one soon.
In my research I came to the conclusion these blades should be close to 1065 steel. I normalized this by heating it to non magnetic then sticking it in a can of vermiculte to cool over night, did this a total of three times.
Then I heated it up to non magnetic again and quenched it in a mix of olive and walnut oil, just left overs we had.
When quenching make sure to keep it straight down and move it a little with the direction of the edge, like if you were cutting something. This will reduce the risk of warping.
Immediately after quenching I put it in a preheated 375°f oven for 2 hours to temper it.
After it cooled all the way I sanded the scale off and polished it a little with the 2000 grit sheets.
Then I degreased it with acetone and applied some Permablue to it to give it a nice dark color. After that I went back to the sander and brightened up the edged again. If you do any sanding after a heat treatment make sure not to let it get too hot or you will loose your temper, cool in water constantly.
Finally I gave it some test throws. It is surprisingly well balanced and throws well. I threw this holding it by the blade from about 5 steps away, so it should have done a half spin. I'm not a knife throwing expert but I got it to stick and had a lot of fun with it. Which is all that really matters right?
Thanks for checking out my very first Instructable.
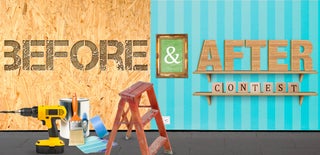
Participated in the
Before and After Contest

Participated in the
Metal Contest