Introduction: How to Make a Portable Bandsaw Table
I was recently gifted a portable bandsaw and knew immediately that I would be making a stand for it. I was lucky, a neighbor gave me a large piece of 1/4 inch steel plate that he didn't want. I also got some pieces of a bed frame from my brother. I wanted to keep the build simple since I don't really know how to weld, so I went with a really easy design. This was really easy to make aside from the material prep, there was lots of rust on the steel plate. If you were to go out and buy a piece of steel plate and some angle iron you could definitely knock this out in no time. While I haven't had much opportunity to use the stand I do like the way it came out. The blade is at 90 degrees and the quick release toggle clamp makes it fast and easy to set up. I hope you find this helpful.
I will be entering this in the Metal Contest if you are so inclined and think I deserve your vote please vote for this Instructable. Thank you.
Step 1:
This is the 1/4 inch metal plate that a neighbor gave me it was very rusted but it was free. The first thing I did was try and remove the rust as best I could. I used my angle grinder with a flap disc attachment and then my orbital sander to clean off the rust.
Step 2:
Next I measured the size I wanted my table, originally I was going to make it bigger but decided on a smaller size instead.
Step 3:
To try and cut a straight line I clamped the bed frame rail to the plate steel and cut along the edge with my angle grinder. The rail acts as straight edge guide for the cut off wheel. Once the cut is done I hit all the edges with a file to remove any sharp pieces.
Step 4:
Next I started to remove the extra pieces from the bed frame. These are the leg portions which I could have cut off but I chose to remove instead so that I could have the most material left over. I used a drill to remove the rivets and my angle grinder and a chisel. Eventually I got them off.
Step 5:
I used a scrap piece of wood to mark the length of the legs and used my angle grinder to make the cuts.
Step 6:
I clamped all the legs together and sanded them down to the same length using the grinding attachment on my angle grinder.
Step 7:
Next I prepped all the edges that would be welded. I used my angle grinder to bevel all the edges and remove any paint from the areas the would receive a weld.
Step 8:
I am not a welder by any means I just try to get a consistent amount of material on all the edges that I weld. I have a lot to learn but I figured this would be a good chance to practice. This will not be bearing any real weight as I plan to use it for flat stock and cutting out knife profiles. Here I welded the inside and outside corners on all the legs.
Step 9:
Since my welds were not that great I had to grind them down. The second picture shows me standing on the table I just welded. In the build video I also jump up and down on it to check the strength. It held up just fine.
Step 10:
Here I used the bed rail/angle iron as a straight edge again. This cut is for the blade of the saw.
Step 11:
I test fit the saw but noticed that the saw body was stopping the saw from reaching its full depth. So I marked the area that was causing the rubbing and ground that down. Basically I tried to grind in the profile of the saw body so that I could get a tight fit against the table.
EDIT: I added a pdf scan of a the Milwaukee Band Saw profile. This way if you have the same saw you can print this out and use it to lay out the profile on the table.
Attachments
Step 12:
After grinding the table I sled the saw back in to position. I used a marker to trace the work steady rest. I then welded a toggle clamp to the underside of the table so that I could lock the saw in place. The toggle locks down on the steady rest. It acts as a quick release.
Step 13:
This the underside of the table you can see how the toggle clamp catches the work steady rest.
Step 14:
I checked it for square and was extremely surprised that it didn't need any adjustment. I also did a quick test cut. It worked great. I have since used it quite a bit and I really like it. This table makes an already useful tool that much more useful. And the best part was that all the materials were free.
As I stated in the beginning I will be entering this in the Metal Contest if you are so inclined and think I deserve your vote please vote for this Instructable. Thank you.
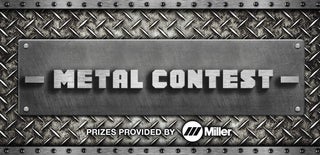
Second Prize in the
Metal Contest 2017
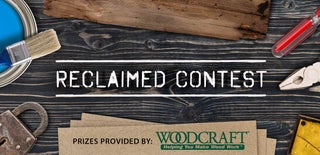
Participated in the
Reclaimed Contest 2017