Introduction: Single Seat Skin on Frame Kayak / Canoe
Ever wanted a lightweight, beautiful, affordable, canoe you could paddle like a kayak? With some patience and about $200 you can! In this instructable I will explain the process, successes, and failures I experienced while building my first canoe. I will also talk about things I will do differently if I decide to make another one. Feel free to ask any questions or add critiques.
Note: Be sure to look through all of the pictures; I have embedded many tips and tricks in them.
Step 1: Location Location Location
Before beginning any project, obtaining adequate space is a must. Thankfully, over the summer, I was able to use the shop at my local University. It has adequate ventilation, good tables to work on, and some useful tools. A garage would also work for this project if you do not mind parking your car outside for a few weeks to a month. Here's a short checklist for picking a good location.
- Covered space, such as a large shop or garage. I would not recommend trying this in your living room. This is mainly to keep the area dry when applying sealants and treating the wood.
- Good ventilation. Some of the products used in this project can be harmful if high concentrations are inhaled.
- Drop cloth, or other material you do not mind throwing away. I used large packing cardboard sheets.
Step 2: Tools and Skills
Going into this project, I had no prior knowledge about building boats, canoes, or even steam bending. With any project, there are new skills to learn and experiences. I will try to explain all of the steps clearly, but I am assuming a basic knowledge of woodworking tools and applying paints, sealers, etc.
Necessary tools and knowledge of these tools for this project include,
- Table saw with guide rail or if you are brave, hand saw
- Sandpaper
- Planer, manual or machine
- Screwdriver
- Wood drill, a cordless power drill covers this and a screwdriver
- Some method to create steam and contain it over long periods of time (I will get into more detail with this later)
- Paint brush and protective gear (gloves, mask if not in well ventilated area)
- Clamps, the more the better
- Jig Saw, or coping saw (table saw may be used in place of this but helps when making the Rib Jig)
- Staple gun or hammer and small nails
- Tape measure
If you do not feel comfortable using any of the tools listed above, I would recommend starting with an easier woodworking project and then coming back to this one.
Some helpful tools which are not required include,
- Dremel
- power sander
- mill
Step 3: Planning and Design
It is good to have some direction of how you plan to use your canoe before hitting the workshop. Something to consider is the capacity; is it going to be a single seat or be able to hold two or more people? For a single seat, the boat may be around 10-15 feet long, and for a two person boat, it may be anywhere from 14-17 feet long. If you plan to add seats like a canoe, the depth of the hull will be around 12-16 inches, while a kayak hull is closer to 10 inches or less in depth. This article from PaddlingLight by Bryan Hansel has a good explanation for calculating seat positions. The seat positions will also drive the overall length of your canoe depending on how much leg room you desire. I chose to make my canoe around 11 feet long so that I could use standard 12 foot cut boards. This decision also confined me to a single seat adult or two seat for kids. I found the gun wales, bow and stern shape, and keel determined the general shape of my canoe. For this canoe, I made most of the design decisions as I progressed. Now that I have had the chance to test this design from building and use, I made a couple more detailed designs in a CAD program. At the end of this Instructable, I have included .step files with full designs for two more boats I hope to build sometime.
Step 4: Material Selection
Red Maple, Pine, and Oak were used in this design. These all steam bend fairly well but each have different advantages and disadvantages. I also experimented with some plywood; this does not steam-bend at all in my experience.
Red Maple is a very lightweight wood and has natural properties which guard it against rotting easily. It does not bend well when it drys out, however. I found it took much longer for this wood in the steamer and it will not bend unless it is soaked through. It is easy to do a few test pieces then cut through the middle and check. The dry and wet sections will have a slightly different color. I would also recommend pre-soaking this wood for a few days before steaming. Obtaining red maple directly from a saw mill is ideal as it has not had as much time to dry out. Red maple also has a pleasant aroma to it and looks absolutely beautiful with linseed oil applied.
Oak is the strongest out of these three. It was also the easiest to steam bend out of my experiences. It holds in moisture which is why it bends easily, but this also causes it to have less of a tolerance for rotting over time.
The pine was also easy to work with but it tends to have more natural knots. When choosing pine, be careful to pick out a piece without knots or with very few and it should be okay.
For the lashing, I used an inexpensive waxed nylon string. This worked very well and it is still holding up.
The skin of the canoe and choosing a sealant were the most difficult parts of selecting materials. I would appreciate any offered tips for skin and sealant options. I used a 1050 outdoor ballistic nylon weave. It was already water proof and shrinks a little with heat. This property helped when smoothing out wrinkles after applying the skin. For the outside coating, I used an elastomeric compound from a local paint store. It is still sticky to this day and pealing in some spots. I am not sure if it is the way I applied it or what.
Step 5: Building the Vertical Rib Jig
The rib jig aids in consistently bending the vertical ribs the correctly. It primarily consists of two parts or sections. The frame board, marked out in the picture, contains holes a couple inches apart to accommodate the bolts in the slider. The hole spacing on the frame board needs to match the width difference of each rib. for example, the narrower ribs go near the ends and slowly increase in width until the center, largest width rib. I chose the spacing of my ribs to be four inches apart length wise on the boat and it made their widths differ by close to two inches. To determine largest width rib, start in the middle of the canoe and it is simply the width of the middle of the boat. The narrowest rib in this design was about 12 inches from the bow. This length is determined by the shape of your bow and keel. This length is the distance from the tip of the bow to the end of the curvature of the bow along an axis following the length of the canoe.
Step 6: Steam Bending 1 (the Hard Way)
My first steam bending attempts proved to be troublesome. I used a tea kettle on the stove and a pvc pipe. The limited reserve in the tea kettle made it hard to leave the steamer for long periods of time and the pvc started sagging after about an hour. The pvc pipe was also not long enough to do any of the long pieces like the gun wales and horizontal ribs. In the next step I explain a better set-up for steam bending.
The advantage of this way is it was very inexpensive and quick. I did a few test pieces like this and they worked out after I got the hang of it.
Step 7: Fast Forward! Steam Bending 2 (The Easier Way)
I'm including this here because there is always a better way to do something and if you are one of those who follows along step by step, this will save you some time in the long run.
A ten foot piece of metal gutter worked very well for my application. Luckily, I found one of these someone was throwing away. I found the roaster, shown in the pictures, at a local thrift store for $5. The high capacity of the roaster allowed me to comfortably leave the steamer alone without worrying about refiling the water level. However, with the container you choose to use, make sure to watch it the first few times to get an idea of how long it takes for all the water to dissipate before leaving it alone. I then used a fuel grade hose to transfer the steam from the roster to the gutter (steam box). I got the hose used here from an auto-parts store for free. Just ask if there is any short sections or "left overs." I have been able to get free tubing sections for many of my projects like this.
To seal off the gutter on the tube end, I used a wooden block with a hole in it. This preformed well because the block swelled up from the heat and steam therefore sealing the end. For the other end I simply used a rag. make sure to place something under the ends of the steam box to catch condensation.
For the steaming process, the 1" by 2" cross-section oak for the gun wales took about 4-6 hours to become workable. Thin pieces used for the ribs were workable in as little as 30 min as long as the steam was already running. Because the box was shorter than my long pieces of wood, I had to do them one end at a time. This did not cause me any issues. If you do decide to make a box long enough for the whole pieces to fit in, you may want to position more than one steam entrance hole as this with set-up most of the steam collected on one end causing nonuniform pliability when working with the wood.
I will explain more of the bending techniques along with the specific pieces in later steps.
Step 8: Making the Bow and Stern
The bow and stern shape determine the very front and back of the boat. This part "cuts" the water and takes the first impact of any collisions or running on shore. There was a lot of prep work involved with these pieces. First, I split the 2x4 into two sections with an ax. Splitting the wood with an ax rather simply cutting it with a table saw allowed the break in the wood to follow the grain. This keeps splinters from developing when bending. Next. I planed the pieces close to square. Again, using a plainer follows the natural grain of the wood better. Note, when choosing wood for the bow and stern, make sure the piece has no knots and the grain runs parallel to the grain with the board. Otherwise, the piece will break and/or splinter. Because the sections were thicker, I pre-soaked them before steam bending. This helps the wood be more workable after steaming. I modified the rib-jig for bending the bow and stern shape but I wound up not using it because I was not able to get the metal band, clamp, and wood around it.
The first attempt was a complete failure because the wood piece was mostly under tensile forces causing the grain to separate from itself. Because wood has much higher compressive strength than tensile, a method of bending where mostly compressive forces act on the wood is needed. An easy way to visualize these "pulling" and "pushing" like forces within a bent beam or member is to take a paperback book, hold it by the spine with one hand, and bend the book like an arch down its length. Notice the pages on the inside of the bend stick out further than those at the top? With a book the pages can move freely with each-other. Now imagine holding the edge of the book square while bending it. The pages near the top would most likely break under tensile "pulling" forces, and the pages on the bottom inside of the bend will wrinkle under compressive "pushing" forces. A metal band with stops on either side aided in solving this problem for the wood. It is .060" aluminum sheeting with wood blocks attached to either end. Because the aluminum's tensile strength and modulus of elasticity is much much greater than that of the wood, it may be assumed to have almost no deformation in this case. Thus, if placed on the outside radius of the bend, as shown in the picture, it will retain almost all of the tensile forces and force the wood on the inside of the bend to be under mostly compression as long as the ends of the wood do not slip relative to the band.
After completing a successful bend, I let the piece dry then cut it in half. That way I have an identical bow and stern curvature. With some light sanding, they were complete!
Step 9: Vertical Ribs and Using the Rib Jig
The vertical ribs are what determine the shape of the hull and support it. The rib jig shape and hole placement will determine their shape and curvature.
I cut all of the rib pieces from 2x4's on a table saw. They are just over 1/4" thick and an inch in width. Looking back I would have made these closer to 3/8" thickness. The 1/4" is too thin for an accidental step in the wrong spot. I would suggest, once you determine the rib spacing, take two blocks and set them this distance apart. then experiment with different rib thickness and width until you find one that can support your weight standing on it between the blocks. I preformed this test with mine after completing the project and found it took two of the pine ribs at 1/4" thick and 1 in width to support my weight across a 4" spacing.
Before steam bending the ribs, be sure to sand these very well. Any small splinters will split off into large sections when bending. These small pieces only took about 30 min in the steamer to become workable. Pull them out one at a time and bend them right away while they are still hot. I used a retaining block on the edge of my rib jig as a starting point then slowly bent the wood around the curvature of the jig. It is important to "feel" the wood during this process. It is hard to explain exactly what to watch for but if you start hearing any small cracking noises, it may not be steamed well enough or you are bending the wood too fast. This process just takes practice. I almost broke enough wood to make another boat while learning how to steam bend. Don't give up here if you experience issues.
Once you are finished with the ribs, double check the spacing with a ruler on the floor, as shown in the picture, and see if you are happy with the shape.
Step 10: Gun Wales! (and Place Holder Yoke)
The gun wales, are one of the most important frame members of the boat. When assembling the frame, they are the first piece.
At the first attempt steam bending the gun wales I had a few failures. These were due to using maple which was too dry. I bought some 12' oak sections and they steam bent much easier. The jig shown in the picture was for bending the curvature at the bow and stern. I nailed three wood blocks to a board so that they would spin freely around the nail. This allows the face of the blocks to match up with the face of the wood in the jig. Because my steamer was only long enough to fit part of the board in, I did these one at a time. Make sure to leave the wood in the jig until it drys out. If it is taken out too early, the wood will conform back to its original shape.
Once I finished bending the gun wales, I placed a place holder yoke in the middle which was the width of my largest rib. After placing clamps at either end, I marked the gun wales for cutting. Use clamps with rubber feet here to keep the wood from slipping out.
Next, measure the angle and make a wooden piece in the shape of a triangle to hold the ends together. I used wood screws to fasten the triangle piece then cleaned up the end with a coping saw and some sanding.
Step 11: Assemble Vertical Ribs and Keel
Placing the vertical ribs on the gun wales was fairly simple and a very rewarding step. It finally started to look like a boat!
Starting with the middle rib, I measured out my spacing 4" on either side and cut slots in the gun wales on the under side about 5/8" deep so that the ends of the ribs would sort of press fit in. Once you press fit all the ribs in and you are happy with the shape, take them all out and apply a little wood glue in the hole before returning them to the slots. I had to cut a few of them to make them all line up to form a smooth bottom shape.
Once the glue dried, I connected the bow and stern pieces to the tips of the gun wales with a through wooden dowel and wood glue to set.
An intermediate piece was custom manufactured which aided in connecting the bow and keel pieces. I made the keel from a strip of maple about 1/3" thick and 1" in width. I secured it to the vertical ribs with zip-ties before lashing.
Step 12: Lashing!
I used a Japanese square lashing for all my perpendicular joints. It allows the members of the frame to slightly deform with respect to each other therefore minimizing stress concentrations. This video by ITS Tactical was the easiest for me to follow when learning this knot. Before tying the lashings I used zip-ties to hold everything in place. I would recommend zip-tie-ing all of the joints before lashing. It is easy to make small adjustments while the ties are on and they hold everything together making tying the lashings easier.
Step 13: Adding the Horizontal Ribs
The horizontal ribs stretch the length of the boat and give it the streamline look when skin-covered. I used oak pieces about 1/4" thick and 1" in width. They are a bit shorter than the gun wales and meet up at the bow and stern on either side. Before lashing them in, make sure to zip-tie them to keep them in the proper spot.
Step 14: Treating the Frame
Once all of the ribs are attached, the frame is finished! Congrats! It looks like a boat now, although there are still a few steps before hitting the water. I added a simple deck of red maple. This may be seen in the picture. Some quick cuts and lashing worked well for this.
I choose to use linseed oil to coat the wood so it may be easier to reapply later and will not peel or flake over time like a lacquer or paint. So far this has worked well. It takes more than one coating, make sure to keep coating until the wood does not soak it in anymore. I cut the oil with some mineral spirits so it spread easier. This whole process took about two days.
Step 15: Put Some Skin on Them Bones and Finishing Trim
Once the wood soaks up all the linseed oil it can, it's time to apply the skin. Start from the middle stretching the fabric the best you can. It took me some time to figure out a method but a staple gun worked well, alternating sides and working my way to the ends. The better you can stretch it here, the less work with the heat gun there is later. When I came to the bow and stern where it curved, I cut a slit in the fabric so it could conform to this shape better. I put a small bead of epoxy on the edge of the bow, then fabric with staples. I repeated this step with the other side and I did not have any leaks. Because the fabric was already waterproof, I was able to make a test float like this. however, because it was only treated on one side, this caused a lot of drag and it would soak up water. Trim up any access fabric and it's ready to go.
For the finishing trim, I used a strip of red maple. I did not have to steam bend it because the red maple is fairly workable dry and thin as long as there are no sharp angles. The trim covers up where the fabric is cut. I attached it with epoxy.
Step 16: First Test Float!
Time to hit the water and enjoy! Remarkably, there were no leaks on this run. I did have to adjust the seat some and the place holder yoke was in the way. I plan to make another one a little more robust and place it where it is easier to enter and exit the craft. I have sense purchased a kayak seat and attached it using a couple eye hooks screwed into the gun wales on either side.
Update: Total weight without the seat came to be 24.5 lbs. This is absolutely wonderful for portaging, but when cruising, it loses its forward momentum quickly.
Step 17: Hindsight Is Always 20-20 and Future Designs
I have included two more boat designs here. One is for a rowboat, the files beginning with "Frame" and the other for a longer canoe labeled "CanoeFrame."
I have sense put about 30 miles on this canoe. I have not had any major issues except for adjusting the seat some to make it easier to paddle. I usually float just one person in this boat but I have tried two before, it was pushing the limits of this boat. We floated over a wake from a motor boat and we could feel the whole boat flex under the load. I believe we may not have been as lucky if I had chosen to use something other than lashing for my connections.
The one thing I have yet to figure out is a good coating for the outside of the boat. I used an elastomeric coating for this design but it is still sticky to this day. It was a less expensive option, so I may just need to bite the bullet and get a better coating. Any helpful information along these lines will be appreciated!
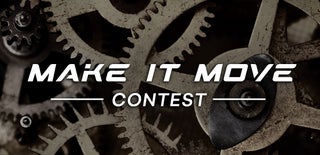
Second Prize in the
Make it Move Contest