Introduction: Industrial End Tables
I recently moved into an apartment with a relatively small bedroom, and couldn't find any small end tables I liked. Of course that means time to make some, so they could be exactly what I wanted! I love the industrial rustic look that is oh so popular right now, and went with angle steel and redwood. These were relatively simple to make, but between sanding time and curing time they weren't as quick as I'd initially hoped. Still, I'm quite happy with them, and they fit well in my small space.
Supplies
- Wood of your choosing. I used one 12" board of rough cut redwood.
- Angle steel. These are 18" high exactly so used one 6' 1.5" bar each.
- Wood finish of your choice. I used this tung oil with a little tint.
- 1" flat head wood screws.
Step 1: Cut Steel
First I cut the 6' steel into 4 equal pieces of around 18" each. Because I was using one length to its full extent, I was careful to mark and cut in the middle of the mark so as not to end up with uneven lengths due to loss from the blade width.
Once done, I ground down the sharp edges at either end.
Step 2: Drill Holes in Steel
Next, I marked and drilled the holes. This took a little more planning and testing of various shelf positions before making a decision. I also experimented with different screw lengths and positions so as not to have them intersect, and positioned the holes accordingly (I didn't use the screws pictured as they are tapered, but they were reference for length).
Once I knew where to drill, I marked on the inside of the angle, and punched each of my marks to give the drill press an easy start. Setting things up in the drill press took some doing, as you can see from the piece of wood I used as a spacer to give enough room for the drill to access where the holes needed to be. This set up ended up working quite well.
When finished, I deburred a little bit, and cleaned up my steel. That was it for metal work, then I moved on to the wood.
Step 3: Prepare Wood
I had decided on rough cut redwood because I wanted some texture, but in the end I probably should have gotten something else as the texture that really stood out was the saw marks. Ah well, it was cheaper :)
I cut three identically sized lengths per end table (these were 13"x12"), and sanded them down until the surface was to my liking.
Step 4: Oil Wood
The last step before assembly was to finish the wood. I wanted to use something that was more on the natural side. I chose this tung oil because it is billed as non-toxic with zero VOCs, but man it took MONTHS to cure. I think it took a full 6 months for the smell to totally dissipate. That said, I am quite happy with the quality and color of the finish. I also made a table top at the same time which was a more amber tone, and I really like how the tint came out on that piece. I was worried the tint might be muddy on the redwood, but I'm happy with the color on that tone as well.
I followed the directions on the bottle, and added as many coats as I could before it seemed as though the wood was totally saturated, then left them overnight, and applied a final single coat in the morning. After wiping off any excess, I leaned them each individually against the walls in my stairwell so all sides were exposed to the air.
If any woodworkers out there have other natural finishes you like that don't have much in the way of VOCs, I'd love to hear your suggestions!
Step 5: Assemble
Once I waited months for my zero VOC tung oil to cure and stop smelling quite so much (at least a month), it was finally time to assemble. The wood had warped a bit in the meantime, so that was the biggest challenge. I learned this the hard way by attaching all four legs to the top shelf piece, then adding the two underneath only to find a lot of huge gaps.
To manage this, I added all three shelves at once with only one screw per angle bar, with them all loose enough to have some wiggle room. From there I tightened bit by bit, in whatever way seemed to mitigate the irregularities the best. This was a lot of tightening, loosening, and swapping shelves, but in the end I managed to get the top shelves flush and the bottom shelves good enough.
Step 6: Done!
With that the end tables were done (save a few more months of off-gassing). If you make some, do share them in the comments!
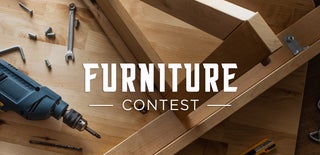
Participated in the
Furniture Contest