Introduction: Industrial Style TV Stand
This is a project I have been meaning to build for quite a while. I like industrial design furniture. The warmth of the wood contrasting with the cold of the metal is captivating. I also love repurposing hard-edged industrial items into living spaces. With that being said, this is a fairly simple design for a TV stand that I came up with.
I hope you like it.
---------------------------------------------------------------
Tools used in this project:
Safety glasses, circular saw, miter saw, hack saw, drill/driver, drill bits, 1.5 inch hole saw, 1.25 inch forstner bit, router and router table, my home-made cutting table, and patience.
Materials needed:
4x4 foot sheet of cherry plywood, 4 feet of 1x2 poplar, 3 feet of 1x3 poplar, 10 feet of 1.5 inch EMT conduit, 4 pieces of 3/4 inch x 96 inch x 1/16 inch aluminum angle, 3/8 inch lag bolts, 2 feet of 3/8 inch threaded rod, glue, screws, stain and paint.
Step 1: The Design
A while back I had built a sofa table from 1/2 inch black pipe and some oak I had left over from another project. The inspiration came from some of the many awesome Instructibles found on this site. I was happy with the way it turned out (though more importantly so was my wife!). I was planning to do a similar design with the TV stand substituting the 1/2 in pipe with something larger. OK, I will admit it. I'm a little cheap when it comes to building projects for my home. When I started looking at the cost for the pipe and pipe fittings I knew I had to come up with a different plan. The pipe flanges alone cost about $7 each at the local big box store and I would need 16 of them. I estimated that the pipes and flanges would be about $170. That's not unreasonable but it is more than I wanted to spend. My next case of sticker-shock came when I started to look for wheels. It was time to get creative.
Step 2: Wheel in the Sky Keeps on Turning...
One thing I new I wanted to integrate into the stand was wheels. After spending some time searching on the interweb for wheels (and listening to some Journey), I decided to just make them myself. I crafted the wheels from some 3/4 inch MDF that a co-worker had given me. I think it was from a base for a bed. I chose to make the wheels 9 inches in diameter because the MDF pieces I had were 18 inches wide and that way I could minimize the waste (and number of cuts).
***Use a mask when cutting and routing MDF***. I didn't at first and after a while of cutting started to feel like poo. You should probably use a mask when cutting any type of wood but there is something in MDF that really messed me up.
I cut one of the boards up into eight separate 9 inch squares. I cut the MDF using my cutting table and a circular saw. (See link below)
https://www.instructables.com/id/No-Table-Saw-No-Problem-Build-a-Portable-Cutting-T/
The reason for eight squares was so I could double up the MDF to make the wheels wider. Using my DIY router table I was able to turn these squares into circles. I started by drawing intersecting lines from the opposite corners of the squares to find the center point of the square. Use a compass to draw a 9 inch circle on the square. Then, drill a 3/8 inch hole in the center of the square to accept the axle (a 3/8 inch bolt). I drilled a matching 3/8 inch hole in the router table top 4 1/2 inches from the edge of the router bit (remember geometry class? d=2r). Use a jig saw to do a rough cut just outside of the circle line in the MDF squares. It doesn't have to be perfect as we will clean it up with the next step. I used a 1/2 inch x 2 inch double flute straight bit in the router to clean up the edges. My first attempt at cutting a circle I used the straight bit only without first cutting with the jig saw. I brought the bit up in small increments to cut the circle from the square. It worked fine but made too much dust for my health.
Step 3: Rock Me Mama Like a Wagon Wheel...
I could have just left the wheels as is but where is the fun in that? I couldn't have this bad boy rolling on pizza cutters. To give the wheels come character I drilled 5 holes in the wheel face. I don't know why but wheels seem to look better when divided into an odd number of sections. "How do you divide a circle into 5 equal parts?" you ask. With more math and geometry (almost as unpleasant as the MDF dust).
First the math: 360 degrees divided by 5 = 72 degrees.
Then the geometry: Start by drawing a radius line from the center of the wheel to the edge. Then use a protractor and draw another radius line 72 degrees from the first line. Continue doing this until you have 5 equal size wedges drawn on the circle.
More math: Divide each radius line in half and mark the center point on the line. ( 2 1/4 inches from the center)
I used a 1 1/4 inch forstner bit to drill the 5 holes at the center of the 5 radius lines. Do this to four of the eight circles. Don't forget to clamp the wheels to a flat piece of scrap to prevent tear-out when drilling through the MDF.
Step 4: They See Me Rollin'...
They hatin'...that they are too skinny. I needed to create a lip and give the wheels some heft. Using the router table again I cut a smaller circle in each of the remaining 9 inch circles. This time I used a 1/4 inch double flute spiral up-cut bit. I made multiple cuts raising the router bit a little each time. Once the center was cut out I was left with a 9 inch ring (and four 7.5 inch circles for another project). I glued the ring to the wheels that were made in the previous step. Now it looks like a wheel worthy to support some tools, machinery, hardware, or maybe a PlayStation and TV.
Step 5: Pipe Dreams
As I mentioned in the design step, I am kind of frugal (somewhere between thrifty and a cheapskate). I wanted the pipe to be larger than 1 inch in diameter but didn't want to spend the amount it would take using plumbing pipe and flanges. While wandering around the aisles of Lowe's ("How come it took you 90 minutes to buy a can of spray paint?" my wife asked) I came upon a perfect solution. In the electrical isle I found EMT conduit (Electrical Metallic Tubing). A 10 foot long section of 1.5 inch diameter was under $13. Good thing I drove the Suburban and not the VW.
I cut the pipe into four 22.5 inch pieces using a hacksaw. I then scuffed up the pipe with some 150 grit sandpaper.
Step 6: This Ride Is Going to Be Cherry
I had a 2 foot by 8 foot piece of 3/4 inch cherry veneer plywood left over from a prior project. I thought the warm cherry would be a good contrast with the metal pipe. I ripped the 8 foot sheet to a width of 16 inches. I then cut this piece down to end up with two 16 inch x 46 inch boards which made up the top two shelves of the cart. I had to combine two 8 inch boards to make the bottom shelf. I glued and screwed the boards together using my Kreg Jig and some scrap 1x3 polar boards. The bottom shelf is 16 inches x 27 inches.
Using a 1 1/2 inch hole saw, I created the holes to accept the pipes. I started by making the holes in the support pieces that go under the bottom shelf. I stacked and clamped all three shelves together after centering the bottom shelf on top of the other two. I chucked the hole saw into my trusty Craftsman corded drill (those hole saws take a lot of torque to turn) and drilled through the plywood to create the holes.
I sanded the plywood boards with 150 grit and 320 grit sandpaper until smooth.
Step 7: Flanges? We Don't Need No Stinking Flanges
To keep the cost of this project down, I chose to eliminate the floor flanges that are usually used to separate the shelves. Instead, I drilled through the edge of the plywood into/through the pipe and zipped in some 3 inch drywall screws.
The distance between the top and center shelves is 11 inches and 9 inches between the center and bottom.
Step 8: Let's Try to Keep the Wheels From Falling Off This Project
I made a simple suspension to connect the wheels to the cart using pieces of 1x2 poplar. It worked fine in principle but lacked the unnecessary complexity I usually wind up adding to my projects. I used some 3/8 inch threaded rod screwed into the axle beam to triangulate the suspension. I actually added this during the final assembly and am glad that I did. I like the mechanical look the threaded rod adds to the cart.
Step 9: Lovin', Touchin', Sandin'
Sanding is the one step of every project I like the least. And yet I love the feel of a piece of wood after it has been massaged with some extra fine sandpaper.
I started sanding the cherry plywood with 150 grit sandpaper and finished with some 320 grit. Be careful when sanding plywood as the outer veneer is only about 1/16 inch thick. Sand with the grain and don't be too aggressive (and listen to some more Journey).
For the final finish, I hand rubbed on some Danish Oil. I chose Watco brand natural finish because I like the way it brings out the warmth and the grain of the cherry (and because I had some left over from another project).
Step 10: It's Your One Way Ticket to Midnight...
Call it heavy metal. I wanted the wheels to have a steel/cast iron industrial look. Experts say you should always seal/prime MDF before painting but I was feeling lazy and didn't. I painted them with Rust-Oleum Silver Hammered Metal Finish spray paint. This was my first experience using this paint and I didn't care for the look of the wheels after painting them with the spray paint. I decided to sand them down and start over, this time using primer. A funny thing is that after I sanded them it really changed the look of the wheels, and now I liked them. I rubbed the wheels down with an old oily rag to further complete the transformation.
Step 11: Wrap It Up...I'll Take It
I wanted to wrap the outside edges of the plywood with metal to cover the screw holes and to give it a more industrial look. To do this I used 3/4 inch x 1/16 inch aluminum angle. Initially, I was going to put the angle on the bottom as shown in the second picture. However, when it came time to install the aluminum I decided to flip the angle and put the flat side on the top. This meant I had to be a little more precise with the miter cuts as they would now be visible. I made a simple jig to cut the aluminum angle to 45 degrees with my hacksaw. I glued the aluminum to the plywood with construction adhesive and clamped it in place until the glue was dry.
Step 12: Ain't That Tuff Enuff...
As I mentioned at the beginning of this Instructable, I am a fan of industrial design furniture and I'm happy with the way it turned out. If I were to make another cart I might paint the metal pipe and aluminum black. It was a relatively simple build and it didn't cost too much to make. I think I spent $50-$60 for the aluminum angle, EMT, threaded rod and paint. The plywood, poplar and MDF were leftovers from other projects but could be purchased for maybe another $50.
I wanted to drill holes through the top into the pipes so I could channel and hide the wires for the TV and components. Somehow I showed some restraint on making it more complicated. Oh well, there is always the next project ; )
Feel free to send me a message if you have any questions.
I'm sorry but I do not have any plans or blueprints for this project that you can download.
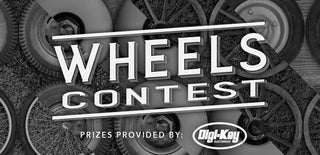
Participated in the
Wheels Contest 2017