Introduction: Knife Grinding Jig
I was recently looking for a knife grinding jig so that I didn't have to free hand it if I didn't want to but they were all in the $70 to $150 range and there was no way I was going to pay that when I knew I could make one myself. I then started searching for DIY options and came across this: Adjustable Angle Knife Grinding Jig. I liked how it used a spring hinge which made this simpler and more cost effective. I have access to a decent amount of scrap steel so I modified the design to be more solid and include a couple additional features.
Step 1: Materials
Below is a list of materials and tools that I used to make this. This could be easily modified depending on what you have available.
Materials:
- Adjustable Spring Door Hinge (I used the largest 4.5 inch size for stability and strength but smaller sizes should also work)
- Bolt (Must be fully threaded and recommended to be at least 4.5 inches long. I used a 5 inch long 5/16 bolt.)
- Cap Nut/Acorn Nut that fits your bolt
- Steel Plate (I used a 7.5 x 3 inch and 6 x 2 inch piece of 1/4 inch thick steel. I originally used a 6 x 3 inch plate for the front plate but changed it to a 2 inch wide plate later)
- Steel Block (Around 4 x 1.5 x 0.75 inches)
- Plastic sheet to reduce friction on the bottom (must be the size of the bottom plate, 7.5 x 3 inches)
- Assortment of bolts (These can vary depending on what you have available. Future steps will highlight what bolts I used)
Tools:
- Angle grinder or hack saw
- Saw to cut Plexiglas
- Drill press and drill bits
- Tab and die set
- Sander/grinder/file to clean up edges
- (optional) 3D printer for knob
Step 2: Attach the Hinge
The hinge needs to be attached to both plates. I used the hinge as a template for where to drill the holes and then drilled and tapped the holes to accommodate the bolts that came with the hinge. There should be a little gap so that the plates do not rub against the round part of the hinge when it rotates.
Step 3: Bolt Post
To be able to adjust the angle, a bolt is used that pushes against the hinge. I used a small chunk of steel, not sure the exact dimensions but probably close to 4 x 1.5 x 0.75 inches, that I bolted down to the base plate and threaded a through hole to allow the bolt to thread into. I set the block at the back of the hinge so that I would have a large angle I could adjust to in either direction. You will need a bolt, preferably two, to be able to attach the post to the plate. I used two 1 inch long 1/4 inch bolts.
Step 4: Reducing Friction
I have seen other designs use a plastic plate on the bottom and I though it was probably there to reduce friction but I wanted to look up the friction amounts myself just to double check. For those who are curious, the following are the coefficients of friction for steel on these various materials: Hint, lower is better.
- Steel on Steel: 0.7
- Polycarbonate (Lexan) on Steel: 0.45
- Acrylic (Plexiglas) on Steel: 0.2
- Nylon on Steel: 0.1
As you can see, adding any of the above plastics on the bottom will allow it to slide easier. I only had a scrap piece of Lexan that was large enough but it still reduces the friction some. This layer also provides clearance for the bolts that hold on the bolt post.
I used the bottom plate as a template to drill clearance holes for the bolts for the hinge and the bolt post. I ended up switching from hex head bolts to button bolts for the bolt post because there was not enough clearance to turn them with the Lexan plate on. You could of course just put on the bolts and then the Lexan if you didn't want to switch.
I then drilled a hole in each corner and countersunk it so that I could use a small flat head bolt to attach the Lexan to the bottom plate.
Step 5: Getting It Ready
Now that it was mostly complete it was time to tighten the hinge and start cleaning it up.
To set the hinge, you need to use an hex key wrench to twist the side of the hinge and then insert the small pin when you have twisted as much as possible. The tighter the better.
Because I used the bolts that came with the hinge, the bolt end stuck out of the front of the plate. I just adjusted the front plate to be parallel with my grinder and sanded them down to be flush with the plate.
Step 6: Adjustable Angles
Because the bolt post is pretty far back and I used a long bolt, I have a large degree of adjustment. I can pretty much go 45 degrees in either direction of vertical.
Step 7: Smaller Front Plate
As I stated before, I didn't like how big the 3 inch tall front plate was so I replaced it with a 2 inch tall plate. If I were to lower my tool rest on my grinder then the 3 inch would work. Depending on your need, any sized front plate would work.
Step 8: Test It Out
If you want, this is as far as you need to go to have a functional grinding jig. I made some more additions that I will show in the next steps
But, I wanted to test out the jig at this point to just see how well it worked. I just did a quick grind and was really happy with how much faster it was to get a good even grind.
Step 9: Addition 1 (Set Screw)
During my test grind, I found that it was easy to accidentally adjust the angle when grinding. I originally wanted to put in a set screw but held off because I wasn't sure it needed it but after the test grind I think it would be very helpful. Definitely recommend adding this.
Step 10: Addition 2 (Knob for Bolt)
It was difficult to adjust the bolt by just turning the end of it so I decided to 3D print a simple knob that I glued to the bolt to make it easier to turn the bolt. If you don't have a 3D printer then you can just use a wrench , socket set or buy a knob like This One to turn it. I have included the Tinkercad link to the knob I made for my 5/16 bolt below.
Step 11: Complete
This is as far as I have taken this design at this time. If you are interested, below are some ideas of potential additions.
- Put a grid of threaded holes on the front plate so I can use bolts to hold knives in place,
- Add knob or handles to the back of the bottom plate to give you better handles to move it around.
If you have any recommendations on improvements or additions please let me know in the comments.
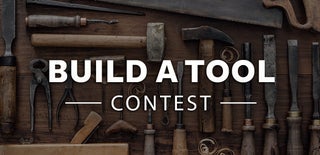
Runner Up in the
Build a Tool Contest