Introduction: Knife Making Early Start
I started grinding steel into sharp tools when I was 12 or 13 years old. There was not a lot of information available at the time and most was learned by trial and errors. I still have my first knife, it was a broken file that I ground a point on the break and beveled one edge to sharp. Over time I ground the file teeth off, sanded and polished the blade so it looked more like a knife than a sharpened file. At the time all I had access to was a bench grinder arbor type with a old washing machine motor for power the wheel was 8" diameter and was 24 grit.
The smaller kitchen knife was made for my grandmother, she had arthritis in her hands and did not grip a normal handle well, so I made a thicker handle so she could control it. It was used for about 15 years. The next is a chefs/clever style knife made from a lawnmower blade and had a thick walnut handle. This one was used for about 12 years. I also made a paring style knife, but this one disappeared after she passed away?
The long slender knife was made from a 12" file and the handle is automotive body filler (Bondo). It is not flexible, but it fillets fish very well. The sheath is corrugated cardboard folded and stapled.
All my early knives were ground from hardened steel, since I did not know much about heat treating or steel types. I used steel that was already a cutting tool.
Step 1: Samples of Today
Today I have a fairly complete shop for knife making, a coal forge, gas forge, plasma cutter, electric knife heat treating furnace, 3 bench grinders, 1x30 bench belt grinder, 1x42 bench belt grinder, 2x30 belt grinder, 2x42 belt grinder, 6x48 with 9 disc sander/grinder, 12 disc sander/grinder, several angle grinders 4-1/2", 6" grinder. 8" grinder. Am currently building a 2x72 belt grinder.
When I heat up the forge I make several blades that I grind when I need a present or just need to relieve stress. The blades above are one leaf from a rear spring of a 1960's pickup truck. I made 4 other large ones that were given away. The finished knife is made from the same spring, the handle is walnut with brass rivets, the sheath is handmade, This knife was made as a demonstration for a friend that wanted to make a knife for his son. He made the knife with the blue back ground. The steel is a high tech stainless steel that is used by one of the major knife makers.
I have also had a boy scout troop forge knives (letter openers) from railroad spikes that they provided. Usually I have 4 scouts and their leader. They are divided into two groups, one heats while the other forges the hot steel. They take turns holding and hammering. These are not fancy just forge the pointed end flat and rough shape it to a knife form. Then they grind the final shape and bevel. The spike is then heated red hot and quenched in oil and tempered at 400 degrees. Lastly they sharpen there prize. If they want they can wrap the handle with para cord. The leaders also made their own knives
Step 2: Bubble Jig to Get Consistant Bevels
The above web site sells an aid for getting a consistent bevel angle on a knife. It takes practice to get a good looking bevel ground on a blade. I found this device makes it possible for a beginner to get a satisfactory bevel the first time. The jig consists of a bracket that you attach to the blade, then you choose the angle block you want to use on the blade. The level has a magnet that attaches to the bracket and the level is adjusted to be level when the blade is held at the chosen angle. Then you grind the blade keeping the level bubble level while grinding. You make 5 passes on one side and then flip the magnet to the other side of the bracket and grind another 5 passes on the other side. You continue until the blade is ground to the desired form. Then a finer belt is put on the grinder to get a more polished surface. This is continued until the desired finished is achieved.
This device is a very good training tool for the beginner and is nice to the more advanced maker also.
There are various fixtures to control the bevel angle, but I find this much more simple to use and is not limited by the blade shape.
Step 3: Knife Sharpener
www.thesharpshoponline.com
After the blade is formed, heat treated and polished, and it needs to be sharpened. I have hand sharpened many blades and can get them razor sharp by hand, but this is not a great use of time and beginners just do not have the skill level to get their creation sharp.
I saw this sharpener at a craft festival and was impressed how quickly it sharpened the dullest knives. (it is not recommended for serrated blades) I wished for several years and finally broke down and ordered one, wish I had ordered it sooner. The sharpener is a slow speed belt grinder 800 feet/minute vs 3000 plus for a 2x72 grinder. The blade is clamped in an aluminum vise that has preset legs (screws) at either 20 (kitchen knives), 25(general use pocket knives), or 30 (cleavers or hunting knives) degrees blade angle and there is a step on the white plastic guide to give a 3 degree micro bevel on the blade.
The process is clamp the blade, then install a 150 grit belt, locate the leg of the vise in the front groove and make a pass of the blade, turn the blade over and repeat, keep doing this until a wire edge is visible on both sides, then switch belts to 400 grit and repeat (usually 3 passes) until wire edge is visible, then move vise to rear groove, repeat grinding to visible wire edge, change to felt belt and apply jeweler's rouge to belt. This time you want to remove the wire edge, rear groove (2-3 passes per side). You now have a blade sharp enough to peal curls off a harbor freight flyer. The first time a knife is sharpened this takes about 5 minutes, after the first time it usually takes 2-3 minutes.
This unit is work on blades from about 1 inch to swords 3 feet, I sharpen box knife blades and exacto knife blades when I do not have a spare available. Also sharpen carving knives.
Step 4: Touchup Honing
www.spyderco.com/catalog/details/204MF/Tri-Angle-Sharpmaker/77
Before I purchased the belt sharpener I used the Spyderco, I had been given a serrated Spyderco knife and needed a method of sharpening that knife. This sharpener works well on both straight blades and serrated. I keep this sharpener setting on my office desk and will hone my pocket knife after use. (letter opener) Also sharpen my wife's Cutco kitchen knives, she purchased before we got married.
This is one to the best hand sharpening systems, I have tried most of the others on the market and this one is simple to use and will sharpen serrated blades which none of the others do quickly or simply.
Step 5: 2x72 Homemade Belt Grinder
www.ibuildit.ca/Workshop%20Projects/belt-grinder-1.html
Am currently building a 2x72 grinder from these plans. Will probably do a separate instructable on the project. After the first is complete I have orders for 3 additional grinders from some of the previous students of my "school". The frame is made of plywood and I am using thread mill motors and controls so the belt speed can easily be adjusted. (watch Craigslist for cheap units sometimes free if belt is torn) Currently have all the parts cut and drilled will start assembly this week.
I hope you find this information educational. I have worked many years and started very simply. I have purchased items that were not good values and some were totally useless. These recommendations are made from experiences that have worked for me. I have no financial ties with any of these companies.
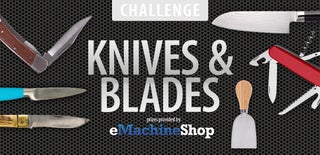
Participated in the
Knives and Blades Challenge
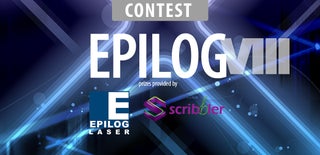
Participated in the
Epilog Contest 8
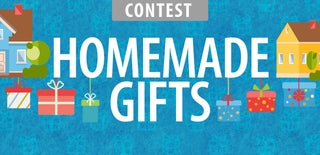
Participated in the
Homemade Gifts Contest 2016