Introduction: Leather Dice Tube
This instructable, goes through the basic steps on how to create a tube shaped dice bag. This instructable doesn't cover in depth steps such as sewing, or cuting the leather. I fully admit that I am an amateur and there are definitely areas of improvement. But It was fun to make, and fills a need that I had.
Supplies
Supplies:
- Veg Tan Leather.
- Sewing Thread.
- Leather Dye.
- Mink Oil.
Equipment:
- Craft Knife.
- Skiver.
- Groover.
- Thread Punch.
- Mallet.
- Awl.
- Swivel Knife.
- Leather Pattern Stamps.
- Leather Needles.
Step 1: Step 1: Design
The process started with drawing out a plan for what I wanted to create, the hand sketch shows the different pieces that I will need for this project. The PDF has the ones that are to final dimensions.
On the PDF I purposely did not include the stitches for the connecting piece, the top, or the bottom. This is because as the leather is bent into shape it will deform. If you punch those holes beforehand, they won’t necessarily line up when you are stitching things together. You can count out your stiches, and space them using a compass. However I found the best results come from gluing the pieces in place, then using a sharp awl to transfer the stitching pattern from one piece to the other.
Attachments
Step 2: Step 2: Cutting the Pattern.
When cutting out the pieces, be aware of defects in your leather. Often there are scratches, clamp marks, cuts, and rough patches. If you have a printed template, you can place the pieces to reduce wastage. I used leather that I had left over from a larger project but mixing leather from different supplies works too. For this project because I am doing tooling, I used veg tan leather.
To cut the pattern out of the leather, I used a simple craft knife with a very sharp edge. I like to cut to size on the first pass, so I used a straight edge metal ruler to guide my cuts. I found that tacking many shallower cuts gives a better result then trying to cut it in one go.
Step 3: Step 3: Stitch Supports.
The stitch supports are just two pieces of leather that will be glued in behind the stitches. Typically these don’t need to be added to stitching, but I was overly vigorous with my stitch holes and felt that more support was needed. I used a Skiver to thin the leather so that they weren’t too prominent.
Step 4: Step 4: Wet Forming Top & Bottom
To form the top and bottom, I soaked the leather until it was saturated. Them wrapped it around an aerosol container. I used rubber bands and painters tape to secure it while it dried. Instead of cutting out a circle before hand, I used a larger off cut then trimmed it to size afterwards.
Both ends turned out fairly well after trimming. There was a fair chunk of wasted leather on both caps, but I felt this could not be avoided.
Step 5: Step 5: Grooving the Threads
Next use the groover to cut grooves along all of the stitch lines. This will help the stitches lie flatter, so they wont get caught on things and wear out prematurely. Also, once the groover cuts in and starts gliding the feeling is a thousand times better than scissors gliding on wrapping paper.
Step 6: Step 6: Thread Hole Punching.
To make the holes for the stitches I used a stitch punch which will punch out 6 evenly spaced holes at a time. I then used my awl to widen the holes and make sure they went all the way through. You could also do this with just an awl and a ruler. It is important to have the same number of stitches present on any two mating surfaces.
Step 7: Step 7: Carving Main Pattern.
Too create a design in the leather, I drew out what I wanted on a Q-Card (which happened to be the perfect size). Then I traced the pattern onto damp leather.
Next I used a swivel knife to cut out the pattern. This can be done with a craft knife, but a swivel knife makes the task much more enjoyable. I would recommend not using a lined piece of paper, as some of it may transfer like it did with mine. However the leather dying covers the lines completely.
I was trying to go for a Dragon in a diving formation, I referenced pictures of Hawks and Eagles. In the end it turned out passable, but I am by no means an artist.
Step 8: Step 8: Texture Stamping.
I used the stamps that came with my kit to add texture to the pattern. This is definitely an area that I have plenty of room for improvement, but for this project I was focusing more on the stitching. That being said I am still happy with the outcome.
As with the carving of the pattern, the stamping must be done on damp leather. There is a lot of conflicting information on how to wet the leather. I am lazy, so I submerge the leather in a bowl of water until it is soaked through then I dry it off using a hand towel.
Make sure you are hammering the textures on top of a solid surface. You don't need a ton of force, but it does require a bit of effort.
I used stamps designed for leather texturing, however you can use anything with an interesting pattern for this. In the past I have used the bottom of a glass bottle for the texture on a coaster.
Step 9: Step 9: Dyeing
I use water based “ECO” dye, because it is what my local store had in stock when I went there. All my dyes are water based which means I can mix colours easily.
I am fairly colour blind which means I tend to make things garish and clownish if no one helps me. Here I was going for a rich brownish red on the main pieces.
I applied the dye with a sponge brush. It is important that the leather is dry when you apply the dye, if not it looks washed out and monotone. It is also important to apply plenty of layers, while alternating brush strokes, this will help avoid streaking and dark patches.
There are leather dyes that can be made at home, however I have not had a chance to experiment with them yet.
Step 10: Step 10: Sewing Set-up.
When sewing, I like to thread the thread back through itself and rub a bit of wax on it. This keeps the needle attached better and doesn’t waste too much thread. Typically you put needles on both sides of the thread so that you can work from one end to the other without having to double back.
After tying off a stitch I melt the ends with a lighter to stop it from fraying. Tying off and melting the thread is not necessary, you can double back the stitches and then just cut them, but I wanted to make sure the stitches wouldn't come loose.
Step 11: Step 11: Sewing the Main Body.
The pattern on the main body is cross stitching, I have included a diagram of the stitching (blue is on top of the leather, and red is under the leather).
Altogether I am please with the look of this stitching pattern, however some of the holes tore out so I had to make some alterations.
The next project I do with fancy stitching, I will use a lighter thread so that it is highlighted a bit more, by the time I realized that I had already done quite a bit of stitching and didn’t want to undo them.
Step 12: Step 12: Sewing the Connector.
The connecting piece was placed in position then I used an awl to transfer the holes. I used a modified dot stitch to secure it to the body. This piece friction fits with the top to keep the tube closed. Originally, I was going to add a strap, but I found that the top stays on with friction alone. Unfortunately the stitches don’t line up, this is because I had to make some adjustments and trimmings to the main body.
Step 13: Step 13: Sewing the Ends
The cap has the same cross stich on the side. The top (as well as the bottom of the main body) have simple dot stitching. I transferred the holes by placing the parts together and pushing the awl through the pre-existing holes.
One of parts of this project I would change drastically, would be to have a larger diameter for the tube. There wasn’t much room inside of the tube to maneuver the needle.
For the bottom of the main body I considered doing a whip stitch, but I didn’t want the thread to be jutting out on the surface that will cause it to fray.
Step 14: Step 14: Finishing
Now comes my favourite part, finishing the leather. For the edges I finished them using beeswax and the wooden handle of one of my tools.
For the leather itself I used mink oil, you can see the effect the oil has on the first two picture where the dragon head hasn’t been oiled yet. I prefer mink oil for two reasons; firstly, it leaves a nice supple finish and secondly it is mildly water proof.
The trick I have found with the mink oil and beeswax is that you have to rub the oil in fairly vigorously so that the oil will heat up enough to easily be absorbed.
Step 15: Lessons Learned:
Be aware of how close to the edge you are punching the stitch holes, tear through is a pain.
Design for ease of assembly, stabbing yourself with a needle because there is not much room is no fun.
Dying and finishing can hide a lot of crimes, they can also cause some.
More rigorous planning reduces the amount of stick handling you have to do.
Practice carving and tooling…. a lot.
Thanks to everyone for reading through this. This is one of my first real leather projects that turned out like what I had in mind. Its a hobby that I find really enjoyable and look forward to working on bigger and more intricate projects.
If you enjoyed this Instructable, please vote for it in the leather contest, I would really like to expand my leather tools (Especially since almost all the tools I have are borrowed from a family member).
If you have any questions, feel free to ask down in the comments I will help as best I can. Also if you have any constructive criticism I would welcome that in the comments as well.
Have a good one, and stay safe out there.
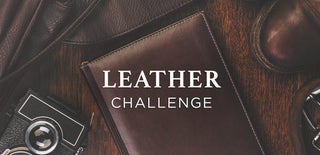
Runner Up in the
Leather Challenge