Introduction: Make a Magnetic Welding Earth Clamp From an Old Speaker
I made this, firstly, because I got sick of using the dodgy alligator clamp that came with my welder originally. Also when welding on cars and other awkward machinery there’s not always a spot with a clamp here sticker to attach a clamp. I saw you could purchase magnetic clamps from various places and not being one to want to spend much... or anything I thought it was something I could make myself. I also have a love for not letting anything go to waste so I used only stuff I had in the shed. So here is my instructable on how to make a magnetic earth clamp using an old speaker.
Supplies
Tools Needed:
. Hacksaw or Grinder
. Welder
. Tap (Size depends on speaker size I used 3/8”)
. Drill Press or Hand Drill
. Screwdrivers
Materials Needed:
1x Old Speaker
1x Bolt and Washer (to suit Tap Size)
Safety:
Please be sure to wear all Personal Protective Equipment necessary to complete the job safely.
Step 1: Find an Old Speaker
Firstly, yes I know this speaker looks far from old but I purchased this speaker a while ago and not long after I bought it, it broke (teach me to be cheap). Of course like always I never kept my receipt so I couldn’t return it but today it shall live on in a new form!
Please note:
The size of the speaker will determine the size of the magnet and your clamp your making so pick the right size speaker that will suit the size magnet and the strength you desire. I’ve used a small one just because that’s what I had. While these steps may change slightly depending on what speaker you have the basics of this instructable will be the same.
Step 2: Pull Apart Speaker Unit
This step obviously will differ depending on what unit you have. Really all you need to keep for this is the speaker, it being slightly damaged isn’t much of an issue so don’t feel you have to be too careful pulling it apart unless there’s anything else in it you want to keep. Just be cautious that you don’t puncture the battery (if it has one) in anyway!
Step 3: Dismantle Speaker
Now you need to pull apart the actual speaker into it’s various components. I used a cold chisel and worked the top apart, if this doesn’t work you can hacksaw or grind this top section off and then throw it away. Once the top portion is removed and disposed of you can try seperate the centre base piece (usually glued on). Don’t stress if you can’t seperate them, it’s not super necessary I just found it easier to be seperate for the rest of the steps.
Step 4: Drill Out Centre
Now you will need to drill out the centre, that your also going to tap. So the bolt size you want to use will determine the size hole needed. In this case I drilled a 5/16” hole to be tapped with a 3/8” tap. Remember to drill nice and steady and don’t overheat your drill bit.
Step 5: Tap the Hole
Now you will need to tap the hole you have just drilled. In this case I used a 3/8” tap. Remember to oil it up and go slow. My set of taps are extremely cheap, but they did the job just take your time. The last thing you want is to have it snap off half way.
Step 6: Weld the Pieces Together
Now you will need to weld the two pieces together so they can’t pull apart and to make sure you get a good solid earth between the top and base of the magnet. Be careful how much heat you put into the piece because the magnet can permanently demagnetise with too much heat so weld slowly for best results. Once the magnets temperature reaches over about 80°C (176°F) it will lose magnetism temporarily, once it cools it will come back provided you haven’t heated it beyond its critical point. Once you’ve finished welding it, sand it flat and smooth so it gives a nice flush fit against your future workpieces.
Step 7: Install and Cut Bolt
Now you can thread in your bolt. If it’s too long (like mine) cut it flush with the magnet. Don’t stress if it’s a millimeter out, once you add a washer and the electrical spade from the welders earth it should sit in, if it still doesn’t then you may need to take a bit more off after.
Or as suggested by Tinker_001 in the comments below you could keep the bolt long with a lock bolt on it so you can simply attach your current earth clamp to it.
Step 8: Bolt Together
Almost there just make sure all your surfaces are clean from rust or anything else that may effect the metal earthing correctly. Once that’s done all you have to do is bolt the electrical spade from your welders earth cable to the magnet, using a washer to make sure it clamps down nice and tight. Now you are free to use your new magnetic earth clamp that you’ve made from recycled materials.
Hope you enjoyed my instructable and I hope this turns out to be a fun mini project for someone. If you make it please feel free to share it here as I’d love to see it. The whole project took me less than an hour (and I dawdle).
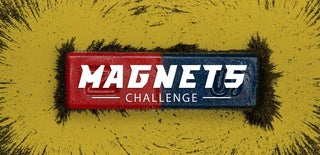
Runner Up in the
Magnets Challenge