Introduction: Make a One Tube Radio
*** This is my entry in the Vintage Contest. When I read of the contest sponsored by Crosley, the first thing I thought of was tube radios. I've wanted to try building a tube radio for a while, so here's an instructable on how I did it. If you like it, please don't forget to vote for me in the Vintage Contest. ***
Do you ever wonder what it was like in the early days of radio? Have you ever wanted to build your own radio to listen to those invisible waves that propagate through our skies? Ever wonder how electronics filled with little glass lightbulb things managed to work decades before the invention of the transistor? Do you miss the days when phones were stupid, but people were smart?
In this Instructable I'll attempt to guide you through the steps of building a one tube radio for picking up AM broadcasts. This will include parts sourcing, prototyping and finishing steps.
Step 1: Why Build a Radio When I Can Buy One?
Unfortunately, it can be much cheaper and easier to buy a radio these days than build one. Good portable radios can be had for under the cost of parts used in this instructable and will almost certainly have superior performance, as well as be capable of receiving the FM band as well. This instructable is not about making a radio better than one you can buy, nor is it about making a radio for less than you can purchase one for.
I built this radio because I think that it's kind of amazing how a little evacuated glass tube with some bits of metal inside can turn radio waves into sound, and also because we don't seem to do much practical stuff in school, mostly just calculus... Through the course of building it I learned a little about how radios work, and got to try out a new prototyping method as well. Overall, I'm not disappointed about taking the time and spending the money to build this little receiver.
Step 2: The Circuit
Unfortunately I don't have any experience with CAD software for drawing schematics, so I've instead provided a scan from my notebook drawings of the circuit as I constructed it.
The radio is a regenerative receiver using a combination triode-pentode tube (which is like having two tubes in one, so I guess this is actually a two tube radio?). The triode section is used in an Armstrong regenerative detector and the pentode section is used as an audio amplifier. There is an output transformer (more on this later) so normal headphones or an external amplifier can be connected. If you have high impedance headphones, you can use them without the transformer, but I found my pair to be very uncomfortable.
Power is supplied from two batteries, an "A" supply to power the filaments (~ 6 volts) and a "B" supply to provide the plate current. I'll go into more detail on these parts in the following steps.
The original circuit is from
http://www.radiomuseum.org/forum/project_a_simple_...
which I built with parts I had on hand. I made a "spider web" coil form rather than the PVC tube used in the radiomuseum article. This instructable includes information on creating coil forms and winding them.
Step 3: A Little Bit of Theory
When I started building this radio I knew nearly nothing about radio, but through the course of this project I learned quite a bit about it and about tubes in general. I'd like to give a good explanation of the principles of operation and theory, but I feel that I still am not quite qualified to go too in depth into the subject. I will, however, provide a little bit of theory as I understand it. If I am wrong about any of this, please let me know so that I can correct it.
Nearly all that I have learned regarding this topic has been from Mr. Max Robinson's site, Fun With Tubes, and the radio construction pages of Mr. John Fuhring. Both of these websites contain a great wealth of information and I would highly recommend them to anyone interested in radio and vacuum tube technology.
First a little about tubes. In a diode tube, there are two main components; an anode and a cathode (also a heater, if the tube cathode is indirectly heated). When the cathode is hot, the electrons have enough energy to travel through the vacuum from cathode to anode (recall that conventional current flows from positive to negative, but electrons flow from negative to positive), similar to a semiconductor diode. When the cathode is cold, the electrons have less energy and current flow is little to none. In a triode tube, an additional component is added; a screen of wire mesh known as the "control grid," or simply, the "grid." Similar to the gate of a semiconductor FET, a small change in voltage on the grid can cause a larger change in current across the cathode and anode (the British often called tubes thermionic valves, as it's easy to imagine the tube as being a valve, with the grid being a handle which controls the flow of liquid [current] through the valve [tube]). This allows for signals to be amplified - a breakthrough at the time of the triode tube's invention. The tube used in this instructable contains both a triode and a pentode section. A pentode has three grids, an anode, and a cathode, adding up to five components. The addition of two extra grids give the pentode some slightly different properties, which are a bit beyond the scope of this instructable.
In the attached schematic, I have drawn a regenerative receiver, based upon the original designs of Mr. Edwin Armstrong, who created this design prior to the First World War. If you're familiar with crystal radios you'll
recall that the signal picked up by the main coil (adjustable through use of the tuning capacitor) is fed through a diode detector and then fed into a pair of headphones (or crystal earpiece). In this case, the signal is instead applied to the grid of the tube, through a resistor and capacitor (sometimes called the grid leak resistor). The small signal appearing on the grid causes larger fluctuations in plate current, which can be heard as sound through the headphones. However, what makes Armstrong`s circuit special is the addition of a second tickler coil winding, which allows some of the amplified signal to be fed back into the main detector coil.This signal is again amplified by the tube and the observed signal is even louder. However, the regeneration must be controlled, or else the set will begin to oscillate, creating an awful high pitched screaming sound, and also possibly radiating radio frequency interference which will disturb your neighbors if they listen to AM radio anymore. In the drawn circuit, the regeneration is controlled mechanically, by moving the tickler coil with respect to the main coil. I had hoped to build a radio using this method, but it proved difficult to prevent the tickler from shifting during use, so I decided on a more typical potentiometer regeneration control instead. In the circuit on the previous page, the triode section of the tube is used as a regenerative detector, but the signal is fed into the pentode section, which acts as an amplifier.
Step 4: Parts List
Here's a list of the parts used to build this radio. While most components are common, some are hard to find these days (the tube, variable capacitor and high impedance headphones/output transformer), so I'll include more information about those in later steps.
Components
1 x 6JC8 triode-pentode tube (details in step 5)
1 x Noval tube socket (or whichever type matches the tube you use)
1 x Tuning capacitor ( ~ 360 pf details in step 6)
1 x Output transformer or high impedance headphones (details in step 7)
1 x 3.5mm audio jack (if using output transformer)
1 x 100 Kilo Ohm potentiometer
Resistors
2 x 2.2 Mega Ohm
1 x 120 Kilo Ohm
1 x 10 Kilo Ohm
Capacitors
2 x 100 picofarad (marked "101")
1 x 0.01 microfarad ("103")
1 x 0.1 microfarad ("104")
Thin wire for winding coils (I used the insides of a cat 3 cable)
~ 50 ft antenna wire (shorter works, but longer is better)
Alligator clip leads
1 x 9V battery connector (mine was salvaged from a dead battery)
Hardware
Wood for the "breadboard" base (I used a scrap piece of alder)
Spray lacquer or other wood finish (optional)
Brass escutcheon pins (copper nails would also work if you can find them)
Piece of sheet metal for the faceplate (I used a piece of aluminum)
Cardstock or similar material for making dial
Sewing needle and disposable ballpoint pen for dial
Piece of dial cord (I used a strand from the inside of a piece of paracord)
Wood screws
2 x knobs
Scrap sheet metal for mounting components
Step 5: Finding Parts: a Tube
With transistors being so prevalent these days, it can be hard to find vacuum tubes anymore. In this radio I used the 6JC8 tube, because I could purchase it locally. The original circuit which uses a PCF801 is based off another circuit which used a 3A5 tube. I purchased my tube from PacificTV for $3
Antique Electronic Supply is a good source for tube radio parts, and a quick search for "triode - pentode" came up with 3 pages of tubes to choose from. They don't have the PCF801 or 6JC8 in stock, but I think that the 6U8 should work if the two cathodes are connected together.
When selecting a tube it's important to keep in mind the required filament/heater voltage and current, as you'll have to make up a battery to provide the required voltage. Most American tubes start with a number indicating the voltage (6.3 volts for the 6JC8 and 6U8). 6V and 12V at around 0.3 - 0.6 amperes are common, but other voltages are also available. Notably there are tubes such as the 1V6 which are designed to run on batteries and require much less filament current and a lower voltage (the 1V6 uses only 40 mA at 1.25V compared to the 450mA at 6.3V of the 6JC8).
You'll also need a tube socket to match your tube, which can be harder to find than the tubes themselves sometimes. I purchased mine from PacificTV, but Antique Electronic Supply also stocks them.
Step 6: Finding Parts: a Tuning Capacitor (or How to Dissect Clock Radio)
Another uncommon part is the variable capacitor (older sources sometimes refer to this part as the "tuning condenser"). Crystal radio builders may be familiar with the aluminum "air variable," type shown in the above image, but these are getting to be rare and expensive these days, so in this Instructable I use the more common miniature plastic "polyvaricon," (Polyester Varible Condenser) which are still manufactured and can be purchased from several online component suppliers, including Scott's Electronic Parts among others.
However, the most readily available, and often cheapest, source for the enterprising experimenter is the ubiquitous alarm-clock radio. I know, I know; it may seem crazy to tear apart a good radio for parts to build another (most likely inferior in performance) radio, but I couldn't find a cheaper solution anywhere else. Broken alarm clocks can be had for free, and I purchased the one in the images from a charity thrift store on half-off electronics day. Where else can you get the capacitor, mounting hardware and a few parts for other projects for only $1.12?
Step 7: Finding Parts: Output
If you have a radio you'll have to have a way to listen to it, of course. You can use a pair of high impedance headphones, like the pair shown above, but these are not produced anymore, and can be expensive. I purchased the pair in the picture for $12, which almost doubled the cost of this project for me.
The alternative is the use an output transformer which matches the high impedance output to the lower impedance of modern headphones. However, an audio transformer could cost as much or more than the high impedance headphones in some cases! But thanks to Charles Wenzel's incredible pages on building transistor radios, I discovered that common household step-down transformers (commonly found in "wall wart" plugs) can be used for the output. Simply attach the primary (120V) winding to the tube output and the secondary winding to the headphones. You'll have to experiment with a few to see which one works best. In fact, if you've taken apart a clock radio for the capacitor, you can also probably use its transformer as well; now that's an economical source of parts, eh?
Step 8: Breadboarding: Building the Base
Wow, over a half dozen steps before we even get into the build? Sorry for boring you up 'till now, let's get into the actual construction.
The circuit is built upon a wooden base with components soldered to little brass nails. This is the classic "breadboarding" technique used in the early days of radio (before those white plastic breadboards, or course; experimenters used to swipe actual bread-cutting boards from the kitchen to build circuits on).
I had a scrap of alder which was too long and too narrow, so I cut a couple pieces, planed and glued them together before cutting to the final dimensions. I gave the board a couple coats of spray lacquer before moving on to the next step. My final dimensions were approximately 15cm x 10cm (about 6" x 4"), which is actually a bit small; you'll see in later steps that the components get a little crowded near the end. I'd suggest a slightly bigger board to allow for easier component placement.
Step 9: Winding the Coils
The coils used in this radio are wound on "spider web" coils made from the hard board material found inside of binder covers. This was surprisingly difficult to work, and I found that it was easiest to hack out the rough shapes with a coping saw, then refine the circles with some stout scissors. The large disc is 6.5cm (about 2.5") in radius and the small disc has a radius of 4.5 cm (about 1 3/4").
Once cut, the coils are very easy to wind, providing that you remember that you must make coil forms with odd numbers of slots - my coil forms have 11 slots each.
To wind the coils, simply start at one slot and go around the circle, tucking the wire over one section, under the next, over again, and so on. I wound 45 turns on the large disc for the main coil, followed by another 6 turns (of a different piece of wire) for the tickler coil. The small disc has 15 turns and is used for antenna coupling (it is the small coil connected between the antenna and ground).
The coils are mounted on a scrap piece of wood which I stained with "mahogany water varnish" to contrast the pale alder breadboard.
Step 10: A Power Supply
What's an electronics project without power? This radio uses two battery supplies, the "A" supply for the tube heater/filament and a "B" supply to provide plate voltage. The "A" supply needs to match your tube heater voltage (in this case 6.3V) while the "B" supply is much higher, at 45-90V (or higher, in AC powered sets).
The "A" supply can be just about any ~6V source, such as 4 D-cell batteries in series, just remember that the tube will draw about 400mA (unless you are using a low current type) so small batteries (like AA) will be drained very quickly in this application. I use a couple of Li-ion 18650 cells with a large ceramic resistor in series (2.2 Ohm, 7 watt). A rechargeable lead-acid "gel cell" would also be suitable, and a 6V wall adapter should work as well, though I have not tried this.
The "B" supply is not much more difficult to construct. You'll need a half dozen of the cheapest 9V batteries you can find (the low cost "heavy duty" type will work here as current draw is very low, expensive alkaline types are not required). I bought three packs of "Sunbeam" batteries from the local dollar store for $1.25 each. Soldered in series they give ~ 54V. A connector can be made from the terminals of a dead 9V battery.
Step 11: Breadboarding: Mounting the Tube
Now that you've built the breadboard, I suggest that you mount the tube first, before any other components. First bend out the solder lugs of your socket (if possible), then mark their positions on the board. Next drive brass pins into your marks. The tube socket can then be soldered into place. This connection method is quite secure and allows you to change the tube if required.
I prefer to add another row of pins in a circle around the tube socket lugs, which can be soldered to instead of soldering directly to the lugs themselves. This is very useful as it allows you to experiment with different types of tubes. You'll see in the next step why this was especially important for this build...
Step 12: Breadboarding: Building the Circuit
Once the tube is mounted, mark the tube pin configuration onto the breadboard keep in mind that the datasheets list the pinout as a bottom-view of the tube. I neglected to remember this, and as a result wired the tube pins backwards. Luckily I had a second row of pins around the tube socket lugs, so I just cut the bare wires and rewired the tube socket, saving a bunch of time.
Unfortunately I didn't get many pictures of the breadboard wiring, but it's fairly easy; just add more pins as needed and connect the components, taking care to reference the schematic as you go.
Step 13: Breadboarding: Testing
Once you have the circuit wired you can begin testing it. Connect your high impedance headphones or transformer and pair of ordinary headphones. Attach as long of an antenna wire as possible (I use 50 feet of wire thumb-tacked to my ceiling) and connect the ground to some grounded metal object (if possible, this is not absolutely required). Connect the batteries and wait a few seconds while the tubes heat up. You should be able to hear a hissing sound when the regeneration potentiometer is turned up, which may turn to an unpleasant squeal when turned too high.
With the regeneration turned to a point where the hissing is loudest, but not quite a squeal, you should be able to hear the distinct "radio tuning sound" (the stereotypical radio sound used in movies) - a series of whistles and varying tones as you turn the dial. If you "tune in" on one of these whistles and turn the regeneration down slightly, the whistling should turn into the sound of a radio station.
I was able to hear the local AM station clearly, and proceeded on to building the faceplate. If your radio is not working at this point, then please see the troubleshooting page (step 19)
Step 14: Building the Faceplate
Once you have the breadboard circuit built to your satisfaction, it's time to build a faceplate to hold the knobs and give a more finished appearance. My construction techniques again borrow heavily from the webpages of Charles Wenzel, who uses similar construction for a some of his transistor radios.
I cut a piece of aluminum sheet to the width of my breadboard with a pair of tin snips (final dimensions were roughly 15cm x 10cm, or 6" x 4"). Next I used some sanding sponges to sand down the surface, then followed the sponges with steel wool. Finally the surface got a good rubbing with some automotive aluminum polish for a shiny finish. I wasn't able to get a perfect mirror finish using this method, but the images show that the surface is quite shiny. If I were to do this again I'd purchase some fine grit automotive sandpaper or extra fine steel wool and use those before the final polish. Alternatively, paint would probably have been an easier solution.
If you do choose to polish the faceplate, I'd suggest covering the whole thing with painter's tape to prevent scratches in the subsequent steps.
Step 15: Mounting Components
Now this is where you have to get a little creative. Of course the way you mount components will differ depending on what components you have on hand. Here's how I secured my components. The images have a couple of additional notes.
The potentiometer and tuning capacitor bushing-thing are mounted through holes in the faceplate and are fitted with black knobs. I attached the coils using four brass pins.
Some very small holes were drilled to prevent the wood from splitting.
The output transformer was simply mounted with two wood screws.
I used a common PCB mount audio jack, but the panel mount variety would have been easier to use. I fixed it in place with hot glue then drove in a couple of pins to stop it from shifting backwards when a headphone plug is inserted.
The indicator LED was mounted in a common chromed bezel. I chose green because it reminded me of the green "tuning eye" indicators which some tube radios have.
Step 16: Making the Dial
The radio dial pointer was made from a common (at least in Canada) Bic brand pen. The smaller front piece (I call this the "section" in the pictures) holds the needle, which is made of, well, a (sewing) needle. The section couples with a piece of the pen barrel which is glued to the tuning capacitor with hot melt glue. I think that the pictures and notes can do a better job of explaining this than my text can.
The dial is fashioned from some cardstock and red paper. I had thought that this would allow the user to note down the position of stations on the dial, but in the end I couldn't bring myself to write upon the radio dial...
Step 17: Putting It All Together
At this point I must apologize for my lack of pictures for this important step. With the impeding contest deadline, and more importantly, rapidly approaching exams, I neglected to take many pictures for this step. If you have any questions, please let me know so I can include any details I have missed.
Once you have the parts mounted, you can screw on the faceplate and attach your knobs. Mine are simple black knobs affixed with setscrews. I just used clip leads for antenna and ground connections, but you could always use terminal strips for a more finished look.
Step 18: Finished!
Well, thanks everyone who got read this far, and sorry for being so lengthy in some of my writing.As I've stated before, I'm no expert of radios, and this is the first that I've actually built (other than a couple crystal radios, and some transistor ones that didn't really work). If you have any suggestions for me, please feel free to contact me and let me know how I can improve this design, or my methods in general. Also, as this is my first instructable, I'm interested in any feedback, so please give me some advice on how to make my next instructable better!
If you do make a radio like this, I'd love to see some pictures of yours as well. If you're considering this project, I'd suggest collecting up all the parts first, then putting the radio together a little at a time. If you ever get frustrated, just take a break and come back to it later. In the few projects I've built I can say that rushing through constructing electronics often leads to damaged components and that lovely burnt resistor smell...
If you liked this instructable, please don't forget to vote for me in the vintage contest.
The next step will have a little about the performance of this radio as well as some basic troubleshooting procedures.
Step 19: Performance and Troubleshooting
Overall, I was happy that my radio worked, but not all too thrilled with it's less-than-stellar performance. However, it did do a better job than any crystal radios that I've built so far, so that could just be due to my poor quality antenna (~ 50 feet of wire attached to my ceiling). I was able to receive the local AM station clearly and with good volume, but any more distant stations produced squealing, but all but disappeared when I turned the regeneration down. If you have any advice on how to improve this set, please let me know.
Troubleshooting
This list comes from Chapter 9 of Alfred Morgan's "The Boy's First Book of Radio and Electronics" (with some modifications to the original text to better fit this instructable)
1) Test that your headphones are working - If you are using modern headphones, simply test them with an MP3 player, or the computer you're using to read this instructable with. If you have high impedance type headphones, put them on and touch the wires to the terminals of your "A" battery supply (6 Volts). You should hear a click each time you touch the wires to the terminals.
2) If the tube heater does not illuminate, check that your "A" supply is good. If the batteries are good, then check that your heater wiring is correct, as well as that you have copied the tube pinout properly. I copied mine backwards first and had to do a bit of rewiring.
3) With the heater/filament warm, disconnect and reconnect the "B" supply. If you can hear sounds in the headphones when you connect and disconnect the headphones, then your wiring is likely correct. If the radio does not regenerate (squeals and whistles are not heard on any setting of the regeneration control) try reversing the tickler windings. If your tickler coil is attached backwards, the radio will not regenerate.
4) If regeneration is inconsistent across the band, you may have to add a turn or two to the tickler winding.
5) If you can't cover the whole band with the tuning capacitor, you could try adding or removing a turn or two on the main winding. The downside to using spider coil forms is that the tickler must be unwound to modify the main coil. A coil tapped every few turns (like a crystal radio) would be interesting to try.
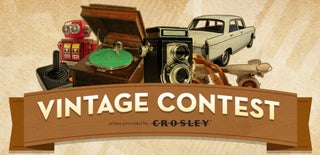
First Prize in the
Vintage Contest