Introduction: Making a Cat(?) Mask With Fiberglass
I'm not new to Instructables, but I figure it is about time I get an account and give back to a website that has given me so much inspiration and information. This is my first post, so all comments and critiques are welcome.
I've always enjoyed making masks and costumes, and about a year ago I decided I wanted to make a semi-realistic cat mask. The design got more complicated as I went along, and though the prototype was not a complete failure...let's just say that this one came out better.
I've broken this Instructable down into a few different pieces, and as the full costume develops more will be uploaded. For now, I've uploaded how to make the head, with an eye tutorial to follow.
This is how to make a mask head, and copy it in fiberglass for stability. The original "head" will be reusable for future projects. Some features that the mask has is a non-electric moving jaw, faux-fur, and tear-duct vision (more on that later).
Step 1: Materials Needed
Many of these items are interchangeable and depend on the style and materials you are most comfortable with.
For the Base of the Head:
-fiberglass resin and hardener
-fiberglass cloth*
-wire mesh (for ears only)
-1/2 to 1 yard of any faux fur
-tinfoil
-a glue gun and glue
-disposable plastic containers... yogurt cartons, butter containers, old Tupperware you don't want anymore...
-a small acrylic sheet, sheet metal, or anything thin and strong with little flexibility. This will be used to attach the jaw to the main part of the mask. I used pieces of an old acrylic sheet. If you don't want a movable jaw, skip this.
-two bolts long enough to go through both layers of acrylic sheet, plus a washer, with room for a nut on the end
-four washers to accompany the above bolts
-two lock nuts that fit the above bolts
-drill bits to match the bolts
-assorted bolts and nuts for other fastenings. It's important that the materials above match because they will be used to create a hinge. These will be used to attach other parts, so matching sizes and lengths are not necessary.
For Eyelids, Teeth, Accents:
-Some form of moldable material that dries or cures over time: polymer clay, a good air drying clay, moldable plastic...
I used Instamorph Moldable plastic for the smaller details, and plaster cloth for the horns.
-acrylic paint
-leather/pleather (optional for nose)
-large taxidermy eyes (available online) OR make your own eyes with my tutorial here:
Tools Needed:
-rubber gloves (multiple pairs!)
-safety glasses
-respirator (for fiberglass fumes)
-cheap paint brushes (for fiberglass)
-dremel
-drill
-sand paper
-markers/pens/pencils
-good paint brushes
-scissors
-a hairbrush
*Alternatively, you could use paper mache or plaster and cover that in fiberglass resin. The result won't be as strong as using fiberglass cloth, but it will still be water tight (easy to clean) and possibly cheaper.
Step 2: On Fiberglass...
If you've worked with fiberglass before, you can skip this.
This was the first time I used fiberglass resin, and it is now one of my favorite materials. It is a bit intimidating at first, but once you get the ratio of hardener to resin down it's easy. There are many tutorials on this website alone which can get you started as well as videos online. Though I am by no means an expert, here are some of the things I learned along the way.
Lessons Learned Part 1:
-I found it's cheaper to buy fiberglass resin and cloth it in the automotive section than the boat section of a hardware store. This might be a regional phenomenon, but keep it in mind when shopping for materials.
-Thin cloth works better than thick cloth for this project. You will have to use two layers of the thinner stuff, but it picks up detail much better than the thicker cloths.
-Do it outside.
-On that note, weather does affect the curing time of fiberglass. So if you're doing this over a span of a few days and the resin is behaving differently, know that not only temperature but humidity as well will change things.
-Try not to touch wet resin with the gloves. The resin from the cloth will stick to it, and soon you'll be covered in little white hairs which are surprisingly strong.
-Fiberglass gets hot as it's curing. Don't touch it.
Step 3: Making the Mold
This could be either the easiest part or the hardest part, depending on the person. When I say "mold" I'm using the term to mean a basic form from which you can make more masks of the same form. Calling it a sculpt may be more accurate, but as I did little sculpting the term feels inappropriate.
It doesn't matter what you make this out of since you'll be using this as a base for the fiberglass, and removing it after. Work with whatever you are most comfortable with. It may help to build over one of those cheap blank masks you can get at craft stores. For those curious about my exact technique, I used Google Sketch to draft a basic head shape, then printed it using Pepakura and put it together (tutorials for this can be found here too!). From there, I used paper mache to smooth out the sharp angles, and then covered it all with plaster cloth for detailing and refining the shape. Regardless of whether or not you are making the jaw movable you should sculpt the whole head; chin, jaws, and all.
The only part that really needs to be aligned with your face is the eyes. Make sure that the bottom part of the eyes are where your eyes will be when wearing the mask. The mask's eyes will fall to either side of your own, resulting in sight holes in the tear duct area of the mask. This is known as tear-duct vision.
Keep in mind that the finished piece will be larger than this mold, due to both the fiberglass and the fur that will be glued on top of it. Basically, you are constructing the skull of the animal. This means that the head mold should be smaller than what you want your finished result to be.
Step 4: Fiberglass From the Mold
The easiest way to get a fiberglass copy of the mold is to fiberglass over one side of the mask, remove it, and repeat on the other side.
First of all, cover the mold it completely in tinfoil. Poke it through the eye holes, and wrap it around the edges. Tape may help it lie flatter in curvy areas. Make sure everything is covered to prevent the mask from sticking to the mold. Then, draw a line down the center of the mask with a marker, running between the eyes, down the nose, and up the chin. This will result in two halves of the mask which will be joined later.
Prepare the fiberglass as instructed. If you haven't worked with fiberglass before, check out step 2. First, brush a layer of resin over the surface of one side of the mask, right up to where you marked the line. Then begin adding small squares of fiberglass cloth about 1 1/2 to 2 inches wide to the surface of the mold, applying resin as you go. Try not to leave the edge of the cloth on a convex curve, because it may result in a sharp edge. A sharp edge can be fixed easily with sanding, but it's easier just to avoid.
Only place one layer of the fiberglass cloth on top of the mask at this stage. Later a second layer will be added. When the resin has fully cured, gently pull the half free from the mold. Most of the tinfoil will come free in the mask half itself...but the mask should not stick to the mold. Leave the tinfoil in the mask, because the second layer of fiberglass will cover it up.
Re-wrap the mask and repeat on the second half.
Lessons Learned Part 2:
-Put a notch or key on one side of the mask halves to fit them back together easier.
Step 5: Two Halves Make a Whole...
At this point, you should have two matching mask halves. Hopefully you took advantage of my lesson learned and have two notched mask halves which line up perfectly. For the rest of us; line up the mask halves as best you can. It may help to clean up the edges first.
To attached the halves together, start by spreading a layer of resin across the two halves. If you mix slightly more hardener in with the resin, it will cure faster and you won't be left holding your mask for half an hour (or more). Once it's cured, paint a layer of resin inside the mask and apply fiberglass cloth squares to the inner surface of the mask. This will add stability but prevent further loss of details on the surface.
Let it cure and see how you did. Your mask and mold should look alike. All that's left is sanding it smooth, and you should have a fairly exact replica.
Step 6: On Horns...
You might think that now is a good time to attach any sort of antler/horns you have planned for your creature. I did.
Lessons Learned Part 3:
-Now is not a good time to attach the horns.
If you attach them now you will have to work around them while making the jaw mobile. It is possible, but they get in the way and can be attached just as easily at the end (and this will prevent you from nearly breaking them multiple times).
I used a tinfoil base to form the basic shape, then covered that in plaster. I used e-pandemic's idea here: https://www.instructables.com/id/ram-horns/step3/making-ridges/ to create raised ridges on my otherwise smooth horns. I painted them black, then dry brushed grey over the raised areas for some added dimension. Finally, they were coated in fiberglass resin for strength.
Attaching the horns is easy, but should really be done just before you start to add fur to the mask. Start out by laying them against the mask the way you want them to lay. It may help to glue down tinfoil wedges to make the horns stick out even further. Once you have them how you want them, glue them securely in place. Then, paint a layer of fiberglass resin directly over the glue. Place a layer of fiberglass cloth over that, overlapping it onto both the horns and the base of the mask. Apply fiberglass resin over the cloth. The result is a very secure attachment to the base of the mask, with seam that will be unnoticeable under the fur.
Step 7: Creating a Moving Jaw- Hinge
I apologize about the blurriness of some of these photos. I was having fun and was excited to get done, and neglected my picture taking capabilities.
The idea here is that the jaw of the mask fits under your own chin. After a hinge is added, opening your mouth should push down on the jaw and result in the mask's mouth opening. Adding elastics will make it close. This is the most difficult step, because the more exact the jaw comes out, the more sensitive the jaw movement will be.
Begin by constructing the hinge itself. Cut four pieces of your chosen hinge material, metal or plastic, into thin strips 2''-3'' long. The width of the strips will depend on the strength of the chosen material. For a smoother look, cut curves into the pieces to mimic the creature's jaw line. Overlap the two pieces close to the end, and drill a hole slightly larger than the bolts. The bolts are basically going to be used as rivets, and need to be able to spin freely in the hole (without falling through). Put a washer on the end of the bolt, slide it through the first layer, then add another washer and the last layer of material (see picture). Screw the lock nut on the end, but not so tightly that it impedes movement. You should now have two pieces
Add padding around your chin as needed for comfort- a little foam or some fabric should do.
Step 8: Creating a Moving Jaw- Attachment
Remember, in the pictures I have made the mistake of attaching the horns beforehand. You won't make that mistake.
The hinges have to be attached to a flat surface. Unless your creature has interesting bone structure, odds are there are no good flat areas to mount a hinge on. Remedy this by gluing a large piece of tinfoil at the edge of the mask by the mouth. Press it into a desired shape, then flatten the surface with a flat object. This should result in a smooth surface. Do it on both sides of the mask, making sure that the two sides are as parallel with each other as possible. The closer they are to parallel, the better range of motion you'll end up with. Once you have it lined up satisfactorily, brush fiberglass resin over the top of the tinfoil. This will give the hinges a strong base to mount on.
But you're not quite ready to mount the hinges yet. Draw a line along the mask where you want the mouth to open. Using the dremel cut along this line, through the tinfoil mounts, and an inch or two past them. This way you don't have to worry about damaging the hinges (unlike those horns).
Finally, lay the hinges over their mounts and drill holes on both the top and the bottom piece all the way through the mask. It may help to glue it down first to prevent it from wiggling out of the way. This is where those spare bolts and nuts come into play. Drill at least two holes on both the top and bottom, and drill diagonally from each other for added strength. Slide the bolts through heads out- these ones should not pivot- and screw on the nuts, tightly. Just to be safe, I fiberglassed over the ends of the nuts to prevent them from unscrewing.
Your mask should look smooth from the outside, but resemble Frankenstein's monster on the inside. Cut the end of the bolt off as close to the base as possible using the dremel. Some sanding may be needed to keep it smooth, as well as padding.
Also, try it on now before you cut the jaw all the way off. The hinges should fall somewhere around your ears, where your real jaw is hinged. This will result in the most natural looking movement. If the placement is good, use the dremel and follow the line you drew to cut the jaw all the way off. If it falls open when you're done, you did it right. If it doesn't quite open, or seems to grind a bit as opening, loosen the lock nuts on the hinges. If the jaw wiggles back and forth and doesn't line back up, tighten the lock nuts. Play around with it and you should be able to find the perfect balance of being loose enough to open, yet tight enough to line back up.
Loop a rubber band over the nose and put the mask on. It should open and close with your mouth.
Step 9: Creating a Moving Jaw- Elastics
Once you have the jaw opening properly, it's time to add elastics to help it close. At this point, a little bit of planning ahead is necessary. The elastics can't be placed too far back towards the hinge, or else they won't be strong enough to close the jaw. Using stronger elastics results in a mouth that's too hard to open. However, you don't want the elastic too far forward towards the mouth, or else it will be visible when you open your creation's mouth. Unless the snout of your creature is really long, I found the best spot to place the elastic is right in front of your natural jaw. The mouth of your creature will probably end around there when furred, and it makes the elastics easy to access if they ever need to be changed.
Mark where you want the elastics to go directly on the mask. Then, get the drill and switch the bit to match the bolt. It's best if the bit is slightly small, just wide enough to let the bolt through. Drill two holes on each side of the mask- one on the jaw and one immediately above it on the main part of the mask. Take the bolts and slide them all the way through so they stick into the mask, about a centimeter or so. I used barrel bolts (also called Chicago bolts in other regions) because they have a smoother surface and a tab on the end to keep the elastic from rolling off.
You should now have four bolts projecting into the mask, two on each side. Brush a layer of fiberglass resin over the outside to keep the bolts in place. Loop a rubber band or other small elastic (doesn't have to be too strong) over the top and bottom bolts. Put the mask on and open and try to open and close the mouth with your own jaw movement. You may have to adjust the length of the elastics a bit, to make the movement more comfortable.
Lessons Learned Part 5:
-Unless you are absolutely certain that the drill bit is the proper size, test it out in a scrap beforehand.
-If you're unsure, it's better to use a bit you think might be too small rather than one too large.
Step 10: Straps
To keep the mask on your head, use the dremel to cut slits on both sides of the mask by the eyes, and one on top. The top one will prevent the mask from sliding down when you move the jaw. Connect the two slits by the eyes with heavy elastic, and connect the top slit to them. It may be necessary to add an extra elastic band that goes under the base of your skull for added support.
I suggest simply tying the elastics in- it makes it easier to adjust them for proper fitting.
Lessons Learned Part 4:
-Don't make the top strap out of elastic, or else the mask will bounce around as you talk...or roar...
Step 11: Details- Teeth, Lips, and Nose
This part is a little more vague, since it depends upon what creature or look you are going for, as well as the materials you plan on using. It may help to have picture references to get an idea of the relative size/shape the teeth should be.
I found it's easier to start with the lips and interior of the mouth. Start out by wrapping a very thin layer of your molding material (clay, moldable plastic, etc.) around the edges of the mouth, only as far up as you plan to have exposed (about up to where the elastics are). Texture/shape it as needed, but don't worry about strength because fiberglass resin will later be applied. For the roof and bottom of the mouth, just press your molding material into shape, blending it in with the edges of the lips. Texture will be added later with a glue gun. For the roof of the mouth, it's easier to blend the edges with the lips first, then slowly stretch up and out into the desired form.
For teeth, press pieces of the molding material into desired shape gently push them into place around the edges of the mouth. Don't push down too hard, or else you might deform the tooth or mouth itself. Resin or glue can be added later as needed to keep the teeth in. When everything is aligned to your satisfaction (and your material has dried), ridges can be created by "drawing" with the hot glue gun. Using constant pressure, draw lines horizontally across the mouth between the teeth.
Lessons Learned Part 6:
- If you make a mistake with the glue gun while creating the ridges, don't try to go back and smooth it over with the gun.
It's nearly impossible to create a finished edge this way. Instead, wait for it to cool and peel it off, then try again.
The ridges may look messy now, but with a coat of paint they will look fine. Once everything is cooled and dried, paint it the desired colors. Paint the lips and mouth interior before the teeth, so you don't have to touch the teeth up later. Once the paint is dry, brush a layer of resin over everything. Make sure that the coat of resin is thinner on the teeth to preserve detail, but thicker around the base of the teeth to hold them in place.
If desired, create a tongue out of the modeling material or fabric (I used vinyl which is not pictured) and glue it in place.
The nose was sculpted in a similar manner. First, draw some guidelines directly on the mask to get an idea of dimensions. It's also a good idea to use the dremel to drill holes in the mask for added air circulation and realism. Then, either press the modeling material into desired shape, or make it separate and glue it on afterwards. Keep in mind that once fur is added, the surface of the mask will be closer to the nose, so it is a good idea to make the nose project about a centimeter farther than you actually want it to appear.
For added skin texture, I wrapped the nose up in pleather and glued it in place. There was a convenient wrinkle in the nose which I placed between the nostrils.
Step 12: Details- Eyes
Again, if you are looking for how to make the eyes, a link will be inserted here when that Instructable is up. This is how to apply eyes to the mask.
Adding the eyes takes a lot of trial and error, because a few millimeters can be the difference between good vision and the inability to see anything. Start out by trying on your mask and getting a feel for the range of vision. If your vision is obstructed anywhere, I highly recommend shaving down that area with a dremel now, before you even add the eyes. Some blind spots are unavoidable, such as the ones that may occur with the mask's nose and eye sockets, but trim it back as far as aesthetically possible. It's also a good idea to widen the eye holes, particularly closer to the nose since that's where your main vision will occur.
Start out by placing the eyes on the mask where you want them to be. Lightly glue them in place with the glue gun if necessary. Take a look at the space between the eye itself and the mask's nose. This is the area that you will be looking out of. Try the mask on. If you don't have much of a range of vision, consider moving the eyes further apart or shaving off more of the mask. Remember that the vision will be reduced even further with the addition of sculpted details.
Once the eyes are in a position that maximizes both vision range and appearance, mark where they were on the mask and pull them out. Wrap a thin layer of your modeling material around the edge (rim) of the eye. Place them back in the mask and press down, using glue if necessary to keep them securely in place. Then, wrap the edge of the eye hole up in the modeling material as well. Take a strip of the modeling material and connect the top of the eye with the outer corner of the eye hole (see pictures for clarification). Repeat on both sides and do the same on the bottom. This will create the basic structure of the mask's "eyelid."
Repeat this process for the tear duct area, but flatten the strip against the side of the mask. Make it as smooth and flat as possible to minimize view obstruction. Detail and paint as desired and (you guessed it!) brush a layer of fiberglass resin over the sculpted parts, being careful to not allow any resin on the surface of the eye itself.
If desired, add further bone detail around the eye using tinfoil as a base and brushing resin over the top. Be aware that details like this may restrict vision even more. For reference, with the additions you see in the picture I can't see out of the side of the mask, thus eliminating my peripheral vision. However, the blind spot due to the nose is almost unnoticeable despite the nose's width, and I am able to see down and out of the mouth for climbing stairs or particularly rough footing.
When you try the mask on, take a moment to adjust to the blind spots. Don't just put it on and assume that you won't be able to see at all. It's surprising how quickly you can adapt to the new vision restrictions, to the point of being able to walk around almost like normal. I wouldn't go for a jog in the woods wearing the mask, but walking around in a crowd on fairly even ground should be fine as long as you are careful.
Step 13: Fur Part 1- Ears
If you've never worked with fake fur before, a great way to get used to it is by making the ears of your mask first. This way, if any mistakes are made very little fabric is wasted.
Also, unless it is the only kind you have, don't use a high heat glue gun. The temperature can actually melt the fur (remember, fake fur is basically plastic) into an unusable mass of chunky hair. If you only own a high heat glue gun, test it out on a small piece of scrap fur first.
Start out by creating the basic form for the ears. I used wire mesh so that I would be able to bend and pose the ears even after attaching them to the mask. Any modeling material would work as well. If you do use wire mesh make sure to fold the cut edges in, because the edges can be sharp and poke holes in the fabric...or you.
Once you have the shape you want, I recommend making a basic "pattern" for the ear so you don't end up wasting fabric. Take any piece of scrap paper or fabric and simply fold it around the ear (see the pictures). Cut off any excess paper, leaving a only a slight overlap. This will be the basic shape of the piece of fabric you cut- generally a square or rectangular piece depending on the dimensions of the ear.
Before you move on to cut the fabric, there is something else you need to consider. The fur of the fabric will all be pointing in one direction, called the grain. When you construct the mask, you want to make sure that the grain of the fur is in the same direction for all pieces, otherwise you'll end up with awkward gaps and ridges in the fur. Generally speaking, on an animal the fur starts at the nose and points towards the head, and from the head points to the back. If you do an image search for "animal fur direction" there are some excellent images that help illustrate this point.
Basically, what I'm saying is be careful what direction the fur is pointing, otherwise it might not lay properly.
When cutting the fur, make sure that the grain is pointing towards the tip of the ear. Not only is this a more natural look, but it makes it easier to blend in the base of the ear with the rest of the head. I drew arrows on the underside of the fabric to help keep me straight. Lay down your pattern with the top of the ear "pointing" in the direction of the grain and cut it out.
Lessons Learned Part 5:
- When cutting fur, cut on the backside of the fur with a box-cutting knife or other bladed implement, not scissors. Scissors cut the fur down short around the edges, which makes it nearly impossible to hide the seams. They also make a mess.
Mine came out in a diamond sort of shape. From there, I placed the wire mesh on the backside of the fabric and glued first the center, then the edges in place. I then carefully folded the rest of the fabric inwards, gluing and trimming overlapping edges as I went. In the end, you should end up with something with no loose fabric, no raw edges, and a desperate need for a haircut.
Unfortunately, I did not take progress pictures for trimming the fur for the ear, but see the "Trimming the Fur" steps for some tips on how to do it. Again, photo references can help to make the ear more realistic.
Step 14: Fur Part 2- the Hood
Since this mask sits on your head more or less like a helmet, a hood helps both hide the wearer and keep the mask in place.
I had a pattern from an old ninja costume for constructing a hood which covers all of the head except the eyes. Cutting larger eye holes resulted in a hood which fit around the edges of the mask and kept a nice shape in the back. For those of us without ninja mask, winter warmth mask, or balaclava patterns hanging around, Simplicity has a guide to making "Ninja Costume Hoods" here: http://www.simplicity.com/t-how-to-make-ninja-hood.aspx. There are also a couple of Instructables here on making ninja masks, but out of stretchy material. Most Faux fur has no stretch whatsoever, so while these tutorials will definitely help with fitting, keep in mind that a zipper or some other fastener will be necessary.
See my third and fourth pictures for help with clarification. Since the fur should be pointing back towards the body of the wearer, the fur grain should be parallel with the "chin" area of the mask. This means that once applied to the mask, the fur will be pointing backwards from the chin, cheeks, and forehead. When being worn, the fur around the shoulders will wrap around and drape down, following the lines drawn in the diagram. If your pattern has the little extra triangles for shoulder padding that mine did, the fur should point towards the bottom edge of the triangle.
Once everything is cut out, it may be easier to sew by hand. Don't bother trying to finish the seams by rolling the edges, because fake fur generally does not unravel. Place the two halves furry sides together and sew the entire chin seam, and only five inches or so on the top seam (from the edge of the face back). Brush the fur over the seam, to pull out any hair that got caught in it and effectively hide the seam. Then, wrap the face opening of the hood around the edges of your mask, trimming if necessary to make it fit. The hood should wrap snugly around the entire outer edge of the mask, with a 1/2 inch to 1 inch overlap for gluing. Begin to glue the fur down with the glue gun from the top of the head down. Don't glue over the hinges themselves, but make sure that the fur fits snugly around them.
After you've glued the fur down to the surface of the mask, glue along the inside edge for extra security.
At this point you may be tempted to give your mask a haircut, but you should really wait until the whole face has fur.
To close the two panels, sew in some sort of fastener. I used hook clasps (also called "frog" clasps) and sewed them in every couple of inches on the inside of the fabric. Use whatever fastener you're most familiar with. Don't worry about hiding the stitches either, because they should disappear under the length of the fur.
Step 15: Fur Part 3- the Face
The biggest thing I can say to you for this step is to take your time. It did take me one full afternoon just to lay down the fur right. If you rush this, the only way to fix any mistakes is to pull all the fur off and do it again. Take it slow and get it right the first time. There is also an exorbitant amount of pictures for this step to help you along the way.
It may help to roughly trim back the fur as you go to keep it out of your way, but be careful not to cut too deep.
Again, make a quick pattern to see how much fabric is needed by laying scrap material over the surface of the mask. Be sure to tuck the material in around all curves your mask might have, so the proper amount of fabric is cut. When in doubt, use more than you think you should, because it's easier to cut extra off than it is to patch areas over. Mark which end of the pattern is the nose/mouth end, and draw an arrow pointing towards the back of the head. This is the direction the grain of the fur should run.
Cut out the fabric and lay it down on the surface of the mask. It should cover the mouth and nose, and chin if you pinch it together. Make sure the fabric is centered and smooth. Begin by gluing down the center of the fabric along the center of the face (the bridge of the nose). Glue all the way up to the edge of the nose you sculpted. Cut a slit in the fabric along the tip of the nose, leaving about half a centimeter or so of overlap for finishing later. This slit should go along the entire length of the nose. Make another slit from the edge of the fabric to the center of the slit you just made (see the 6th picture). These two edges will form the cheeks. Slowly lay and smooth the fabric down around the nose and cheeks, gluing as you go. Glue right up to the edge of the upper lip, but leave the mouth for last.
Slowly make your way towards the eyes. You should be using a lot of glue to make sure the fabric stays down and does not pucker. If your mask has extreme curves (like the cheekbones mine has), be sure to press down firmly while gluing and give the glue a moment to set. If you end up with a wrinkle, pull the fur around it off and smooth out the fabric again. Don't glue right up to the edges of the mask yet.
When you get to the eyes cut a small slit right in the center, about where the pupil is, in the fabric. Slowly widen and glue down the area around the sculpted eyelids, taking particular care around the "tear duct." Any misalignment might result in further reduction of vision.
Continue back from the eyes across the forehead. Smooth out any wrinkles right up to the edge of the mask, where the fur of the hood meets the fur of the face. Trim the edge of the fabric so that it just meets the edge of the hood and glue it down, careful not to get any of the fur tips caught in the glue. Once the glue dries, brush the fur along its grain, across the seam. The result should be a virtually seamless transition between face and hood.
The mouth takes a little extra effort. Start out by cutting along the lip line of the top jaw, leaving a bit extra around the edges. Cut slowly and carefully and stop before you hit the elastics. Glue this down and worry about finishing the edges later. Open the mask's mouth as wide as you want it to be able to open and wedge something in there to keep it open. This will assure that while you are gluing down the fabric, you don't leave enough to prevent the mouth from moving. Wrap the fur around and down to the bottom jaw, pulling it out as smoothly as possible. It will probably be necessary to trim down the bottom fabric as well. Glue all along both sides of the jaw, saving the bottom for last. In the end, you should have two flaps which meet below the chin (see picture). Trim off the excess and glue the two tabs down so that their edges meet. If done correctly, this "seam" won't be noticeable. Finish all edges by trimming and gluing right up to the edge of the lip.
The edges of the mask's mouth might bow out a bit when the mouth is closed, but this can be fixed easily by pinching the fabric inwards and putting a little dot of glue on the inside to hold the pinch. This will create a little wrinkle that will bend towards the inside of the mask when the mouth is closed, rather than the outside.
You're almost done now! All that's left are some finishing touches. First up: a haircut.
Step 16: Trimming/Coloring the Fur
Trimming and styling the fur all comes down to personal preferences on how you want the finished mask to look. All I used is a basic pair of scissors. Unless you really love vacuuming, it should probably be done outside.
Trimming Tips:
- To make a smooth transition from short fur to long (such as from the nose to the forehead), cut in the direction of the grain. Pull little portions of the fur out straight, and angle the scissors to make the cut.
-To thin the fur out (such as in the ears), pull the fur out straight and cut against the grain, keeping the scissors fairly straight. This will result in little portions of the hair to come out, resulting in thinner volume without decreasing the length.
-Making a smooth, short, flat area (such as the nose) is difficult with the scissors, but doable. First, cut perpendicularly to the fur, as short as you want it. Multiple cuts next to each other will result in a shorter, yet somewhat ridged surface. Then, cut in the direction of the fur as before to smooth out the ridges.
-If you want to have spikes or other "styles" in the fur, a mixture of hairspray and/or glue can be sprayed on the hair to hold it in place. I used a little glue for the tips of my ears, to keep them pointed
There are a few different ways to color the fur, from using dyes to airbrushing paints. I wanted to work with materials I either already had or could obtain cheaply. With some experimentation, I found the best (inexpensive) materials to be either basic acrylic paints or permanent/paint markers. You'll need either a fine toothed comb or wire brush to help you out (one that you don't mind getting paint in).
Before painting directly on your mask, I suggest experimenting on a scrap piece first.
Tips for Coloring the Fur
-If you decide to use acrylic paints, water them down a little first. This will make them blend easier, and decreases the possibility of the hair clumping together due to the paint. Dab a little of the paint on the area you want to color, close to the base of the fur. Then, brush the paint in, brushing in the direction of the fur.
-For darker results, work layer by layer- putting a thicker layer of paint on gets messy fast.
-For permanent marker, dab it on close to the base of the fur and brush it in.
Even if you aren't putting any markings on your mask, you can use these techniques to make the transition between the eyes, lips, and nose ("skin" parts) to the rest of the fut more natural. Just use paint the same color as the part, and dab it on both the base of the fur and the edge of the part, brushing the paint in afterwards.
Step 17: Attach the Ears...
All that's left is attaching the ears. All depending on the weight/size of the ears, you may only need to glue them down. My ears were quite large, so I ended up having to sew them on as well.
Experiment with the angle and position of your ears until you figure out where you want them. Then part the fur, pulling it away from the area that you are going to attach them. Place a bit of glue in the middle of the parted area and press the ears down. Then, glue all around the edge of the base of the ear, being careful not to get any of the fur from the head caught in the glue.
After the glue is dry, if needed get a needle and thread and stitch directly through the ear from the underside of the mask. If you used wire mesh, the needle should pass right through.
Once attached, brush the fur back in place over the base of the ear. It should hide the seam between the head and the ear. A little glue may be necessary to keep the fur in place.
Lessons Learned Part 6:
-If the base that you are keeping the mask on is smaller than your head, it will change the angle that your ears stick out. Keep this in mind and pad the inside of the base to get the best idea of how the ears will stand up.
Step 18: ...and You're Done!
Aside from some last minute modifications, the mask is complete. Try it on! For any rough areas, or if it ended up larger than your head, a little bit of foam padding may be necessary.
*It's also important to note that if you made this in a span of days instead of the weeks that I spent, the inside of your mask might still have a chemical fiberglass smell. The smell will fade (for the brand I used it took about a month), but it will always be vaguely present. If the smell bothers you, I've heard that spraying in a lacquer can be used to seal in the scent (though I haven't tried it, and I'm not sure if at that point you are swapping the fiberglass smell for a lacquer smell).
At some point you will need to swap out the jaw elastics, but it was made so that the elastics are easy to access from the inside.
Thank you for taking the time to look at my Instructable, and I hope it can help or inspire you to make your own projects!
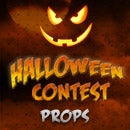
Participated in the
Halloween Props Contest