Introduction: Man & Woman Sculptural Pendant Desk Lamps
I have been building furniture and interior decor items as a hobby for over 10 years now and lighting is easily one of my favorite categories to build. Why? Any couch, desk or bed, no matter how creative you try to be, is going to be quickly recognizable as a couch, desk or bed in the end. This is because form has to follow function for any of those things to be useful items, and the function of most furniture ends up dictating quite a bit of the finished form. A light fixture, on the other hand, only needs to provide illumination. Additional requirements beyond that are slim, and as a result there are few items that can add intrigue to a space as much as an interesting and unique light.
I came up with the idea for the Man & Woman Sculptural Lamps while doodling design ideas several months ago, and have been slowly building them since then as a project that just never seemed to make it off the back burner. However if all supplies were gathered before the build I think this project could be completed in 3-4 hours. Total cost is roughly $100 if buying everything new.
Bill of Materials:
- 1/8" Baltic Birch Plywood (or any other suitably thin wood you can get your hands on)
- Qty. 2 of Antique Filament Light Bulbs
- I ordered several different styles to be able to see how each looked in the finished fixtures
- Order relatively low wattage bulbs (40W or less) unless you plan on adding a shade somehow
- Qty. 2 of Cast Solid Brass Socket
- 18/2 Twisted Wire, Red Cotton
- I used a 12' length for each lamp
- Qty. 2 of Transparent Gold Lamp Plug
- Qty. 2 of Transparent Gold Toggle Switch
- Qty. 2 of Brass Strain Relief
- Spray Paint
Required Tools:
- Laser Cutter & Graphics Software
- A scroll saw, band saw, jig saw, or router with template bit could easily be substituted for the cutting operations if you're not equally spoiled with access to a laser cutter
- Hand drill and drill bits
- Wire Cutters/Strippers
- Screwdrivers
- Sand Paper
Step 1: Frickin' Lasers
I started putting together my cut file by drawing a single line that evoked the form of a man and a line that evoked the form of a woman. I used a few photos copied from the internet as initial guidelines, but these are no longer included in the downloaded file for obvious reasons. After some tweaking and critiquing to get the silhouette line just right I used the "Offset Path" function in Illustrator to turn the line into a 2-dimensional pattern.
Once I was happy with the single-sided patterns, I duplicated and flipped them to form the full man and woman silhouettes. The circular pieces for the top and bottom were then created based on the measured distances at the neck and base of the silhouettes. The final decision to make is how many vertical pieces will form the finished sculpture. I opted for 12. The notches were removed from the top and bottom circles by copying the notch rectangle 12 times around the center of the cap pieces and then using the "Pathfinder" tool.
If you download the attached file the only detail worth revisiting is the width of the rectangular notches. I created mine for 1/8" Baltic Birch (3 mm), and it was a pretty tight friction fit. It's probably worth increasing their sizes by a few thousandths if using the same material. Everything else worked perfectly. Also note that the pieces are oriented at an angle to maximize the yield from the 24" laser cutter.
Attachments
Step 2: Wood Makes the Man
With the completed file in hand, the next part is easy. Load up the laser bed with wood and press play. Then gaze in awe at the precision CNC awesomeness. If you're doing this on your band saw in a 90 degree shop, I'm sorry. I don't mean to gloat. I still use real tools for every build over 24 x 18" which is just about everything.
The cut pieces were assembled using a friction fit. No glue required. Several of the joints were tight enough that some tapping from a hammer was required to fully seat the pieces. As mentioned in the previous step I would increase the size of the notches by a few thousands of an inch if repeating this project in the future.
Once assembled, I painted the sculpture frames with a gold spray paint that matches the brass hardware nicely and really makes the red cord pop. Lastly, I designed the laser cutter file with a small reference hole to mark the location of the strain relief but wanted to wait until I had the hardware in hand before drilling the final hole size which turned out to be just under 3/8". I glued the black piece of the strain relief to underside of frame using CA glue, although in retrospect this is probably not necessary since the piece won't have any chance to get lost once the socket has been placed on the end of the cord.
Step 3: Electrify Your Lady
The electric components I chose for this build are all solderless. The socket uses screws to capture the wires, the plug has metal points that stab through the wire insulation to contact the wires, and the toggle switch similarly presses the wires onto the switch conductors once screwed together.
Remember:
Hot Lead = Black Wire = Brass Screw = Small Prong
Neutral Lead = White Wire = Silver Screw = Large Prong
I started by cutting two 12' lengths of lamp cord; one for each lamp. I then connected the plug to each wire, stripping back the decorative cotton outer and insulation layers as necessary. Use a DMM once the plug has been connected to the cord to make sure there is good continuity between the two. Few things are more frustrating than thinking you're finished with a wiring project only to discover that you've got to break your circuit to do troubleshooting and perform repairs.
After the plugs had been attached I fed the wire through the cord strain relief at the top of the sculpture frames. After tightening the strain relief the cord was then fed through all necessary components for the socket including the socket cap and cardboard washer. Strip the cord conductors, wrap the wire once around the screw terminals and use a screwdriver to tighten. Once again, use a DMM at this point to check continuity between the prongs and socket terminals.
The last electrical component to wire is the toggle switch which works by making or breaking the connection of one of the conductors of the lamp cord. I chose to locate my switch about 3 ft. from the strain relief at the top of the frame so that it wouldn't disrupt the look of the man and woman silhouettes. Cut roughly a 1" section out of one of the conductors of the lamp cord. Strip the insulation from both loose ends and press the wires onto the conductor prongs in the switch housing. Close the switch housing with a screwdriver, making sure that the wires stay in contact with the switch conductors. One more time, use the DMM to check continuity between the plug prongs and socket. The center contact on the inside of the socket should have continuity with the hot (small) prong, and the threaded portion of the socket should have continuity with the neutral (large) prong. Additionally, the switch should now make and break continuity on whichever wire was cut; it doesn't matter which one.
If your DMM checks are good then it's time to plug in the lights and admire your handy work.
Step 4: And I Said Let There Be Light and There Was Light
Assuming your lamps didn't pop a circuit breaker on your house (indicating a miswire) you should now be basking in the vintage glow of a job well done. These unique lamps catch the eye and create great atmosphere. They certainly look better lit, but the sculptural aspect and striking gold and red color combination ensures that they're a great addition to any creative space regardless of the time of day.
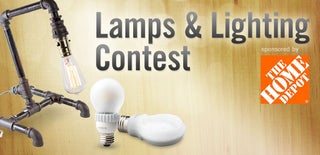
Second Prize in the
Lamps and Lighting