Introduction: Mario Kart 8: B Dasher 1:6 Scale Model
Since the release of Mario Kart DS way back in 2005, the B Dasher instantly stood out among most Mario kart designs within its long series and with its latest rendition in Mario Kart 8 Deluxe on the Nintendo Switch, It looks as good as ever and I couldn't pass up the opportunity to make one, and now, I'll show you how to make one!
Step 1: Tools & Materials
Materials:
- Chemiwood/Dense Urethane Foam ([X2]100X100X400mm)
- Epoxy Putty
- 1-2mm Sheet Acrylic (Cast)
- Strip Styrene
- Car Body Filler
- 1-2mm PETG Sheet
- Modelling Putty (air drying)
- Automotive Primer/Filler Primer
- Red, Green, Pearl Blue, Rubber Black, Red, Silver Model Paints
- Gloss White/Satin Black Automotive Spray Paint
- 2Kg RTV Silicone (Optional)
- 2Kg Polyurethane Casting Resin (Optional)
- Painters Tape/Tamiya Masking Tape
- Masking Vinyl (Optional)
- Packing Tape
- Epoxy Glue/Superglue
- 6mm Dia. Metal Rod
Tools:
- 80, 120, 180, 240, 320 400, 600 Grit Sandpaper
- Dremel w/ Grinding Heads
- Hot Glue Gun
- Basic Sculpting Tools (For Epoxy Putty & Modelling Putty)
- File/Rasp Set
- Jig Saw/Band Saw
- Access to 3D Printer
- Access to Laser Cutter
- Access to Milling Machine (Optional)
- Lino/Carving Tools
- Drill & Drill Bit Set
Step 2: Templates, References & Assets
I've included scaled templates I've drawn, alongside Lasercut files for the acrylic pieces and screenshots I got from my hours of "research" on the game...
3D models are included later on in the Instructable...
Step 3: Base & Engine
If we're gonna start anywhere, the base is the place to go.
Urethane Tooling Foam (known as Chemiwood in my University) among other names like Renshape, is really awesome for model making, as it's really dense and strong (denser than some woods in some cases!) but it sands and shapes with far greater ease compared to other materials. This grade of Chemiwood is pretty dense; as long as it's not too soft any density will work.
Cut the outline and depth profile shown on the templates using a power saw; I used a band saw as I had one on hand but a jigsaw would work just as well.
To hollow out the interior, I had the privilege of using a 20mm end mill to get my desired perimeter. Alternatively, the slot can be cut out using a jigsaw, then the sides can be cut off and added back to the body. I removed the rest of the interior material with lino tools.
The Engine Block is separated into 2 pieces. The bottom half is part of the main body and the top is a separate block. I used a flat rasp & flat file to get the chamfers.
Note:During the build process, I was still working on the final design and noticed the Engine Block chamfers in, instead of parallel. I corrected this by sawing & filing off the excess and reshaped; This has been corrected in the templates so you won't encounter this hiccup.
Step 4: Front & Nose
The Front of the body is pretty straight forward, it's all about the symmetry and making sure it looks right from all angles. Using the outline and the font and back templates, you want to match the profile from one side to the other.
Start by knocking off the corners of the Tooling Foam; you'll be surprised just how much can be taken off, then all you have to do is file the edges made by the initial removal of material until you get a consistent curve.
The nose is quite similar, however the internal material has gotta go. A large drill bit removes the initial material, and the rest is removed with a spindle sander; a Dremel with a drum bit will work as well.
The nose block is also cut to the same size as the Front to match, then with a rasp & a file, taper the back of the block down to the lip of the opening.
Step 5: Seat
Like the rest of the Chemiwood pieces, it starts as a squared block, then the necessary material is removed. the sides of the seat need to match the angle of the interior so it slots in, so off with the side with a saw.
Keeping one of the sides I cut off, I add it back on with double sided tape and lay it on its side so the curve outline isn't slanted. The curve is also cut out with a band saw and cleaned up with the spindle sander, again, a Dremel will work well for this as well.
Next is to scoop out some internal material to make it more, well, seat shaped. A grinding head on a Dremel is perfect. Start from the middle and draw out the grinding head; you want the middle to dip the most with the sides rising up.
To plump up the seat, a healthy dose of Epoxy Putty (Milliput) is mixed in equal parts and sculpted onto the block with basic sculpting tools & water to smooth the shape. Once cured, Milliput sands amazingly smooth.
Finally, a chamfer is added on both sides of the seat to match the width of the engine block.
Step 6: Side Vents
The side vents is made up of 3 pieces; Top, Middle & Bottom. Starting with the top and as always, start with the Chemiwood block squared & to size. Using lino tools, I notched out some grooves so the piece roughly matched the profile of where it sits on the body. To get a perfect fit, I taped up the receiving area and applied car body filler to the piece and squashed it onto the body; This forms the exact shape around the taped area and the tape stops it from bonding, making it easy to separate. From there, the curve is shaped with a rasp & files.
The middle is similar, cutting out a rough match to the body, then using body filler & tape to match the body. The last part is the bottom. Once again, remove the material to roughly match the body, then tape and body fill to shape.
The trickiest part about this section is getting all piece to match with each other, while keeping them separated. This boils down to taping a lot of sections, applying body filler, letting it cure, rinse & repeat until everything starts to blend together. At this stage, Using Milliput to refine the shape is easier than using body filler.
The Middle & Bottom can be glued together once everything is shaped accordingly; Epoxy Glue is best of Chemiwood.
Lastly for the grill detail, remove a small channel with lino tools or a utility knife and cut strips of rounded styrene to length.
Step 7: Acrylic Pieces
During this project, I had access to a laser cutter so for my plastic pieces I designed my parts around laser cutting 2mm acrylic. If you don't have access to a laser cutter, tools like a scroll saw or even a coping saw can be opted instead; use what you have!
The biggest advantage with laser cutting is engraving, so I did exactly that for my engine details. During this stage I wasn't anticipating doing it like this so I had to remove material to accommodate the thickness of the acrylic; bear that in mind. These were glued on with Epoxy Glue and the top block was also permanently glued down with the same glue.
The Steering wheel is made of 3 layers with the core connecting to the ring. The edges were rounded with files and sandpaper and that's that piece done.
The Grill is just a simple oval with 12 grooves and the engine piece is 2 layers with a cap on the end and finally, the dash matches the profile of the body but slightly reduced to form a lip.
Step 8: Final Body & Refinements
It's time to blend everything together!
The acrylic engine faces need matching with the sides so using body filler and painters tape as a guideline, I applied body filler to sharpen and flatten the faces. This was repeated on all faces, resulting in crisp, flat surfaces once cleaned up with sanding blocks.
For the dash, I used my Dremel to hog out a rough slot to glue the dash in; body filler covers and blends the gap. (Note: I used Milliput to reshape the ends so I had more control over its shape.)
At this time we can glue the Nose to the Front and the Front to the Base. The belly of the model needs rounding over, just like when the Front was shaped. I found with my Front and Nose they didn't match quite as well as I planned so I used body filler to blend it all into 1 seamless piece; it took a few passes to get the shape just right.
Any gaps at this stage between pieces can be blended together, like the sides and the interior. I also took the time to blend the seat to the interior with body filler and tape, leaving a perfect seam line between the parts, as well as the top side vent pieces to the sides of the seat.
Step 9: Windshield/Vacuum Forming
The final addition to the body is the windshield.
With last last piece of Chemiwood, I shaped a buck that emulated the shape of the body to get a close fit and filed the windshield curve to match the side profile of the body.
This buck was vacuumformed with 1mm PETG. Vacuum forming is a process that takes a sheet of material, heats it so it becomes flexible, and is then sucked over the buck to create the shape. The whole process of how it works and how to build your own can be explained in it's own Instructable, so I'll link a tutorial HERE. Once that's all cleared up, let's continue!
The newly formed piece is trimmed and can be blended to the body with body filler. A handy tip before continuing is to add painters tape on the formed piece to protect it from scratches. My form wasn't perfect, as I had to estimate the shape but because I got close, I only needed to use a small amount of filler to blend the shape. Once it's sanded down, the added material seamlessly blends into the curve.
Step 10: 3D Prints + Prep
Every part has been fabricated minus the 3D prints, now it's time to tackle that! Included are all of the models needed for the kart for the taking! Thingiverse links here!: ExhaustWheels
Note: I've included the wheels both as a whole piece, and 2 separate pieces as I had problems with the text on the whole wheel, with support structure ruining the text. If you can get a perfect print, I'd opt to use the whole tyre.
Depending on your budget, you can opt to print all the pieces twice & use the 3D prints as the final parts but I based my model around rigidity, so I designed these to be moulded & casted; the choice is yours!
Either route you take, you'll want to work on your prints to make them look their best; nothing is worse than a great model that's hindered by unfinished 3D prints.
My prints were done on an Ultimaker 2 Extended+ at 100 micron for really good results. 120 grit is great for removing most print lines in an instant; only a few minutes are needed for each piece.
For an even better surface, apply a coat of filler primer. Filler primer helps fill in imperfections on the surface, smoothing out the surface and when it's sanded with a lighter grit like 240, it leaves a great surface!
Step 11: Moulding/Casting: Pt 1 (Optional)
(Apologies for lack of stages & image quality, it was crunch time during this stage)
Moulding & Casting, much like Vacuum Forming can seem intimidating the first time round, and there is a wealth of knowledge on how to go about it; I'll include a link HEREto Instructable's own class on moulding & casting!
There's a whopping 16 parts to mould in total! This doesn't mean it's any harder, it just takes longer. All the moulds I'm doing are simple 1 part moulds. The 3D prints are modeled with flat surfaces, ideal for 1 part moulds. These parts are stuck down on a sturdy board (Acrylic, in this case) with double sided tape and mold walls are made with cardboard and hot glue for big moulds and cups for small moulds.
The hot glue keeps the mould wall contained and acts as a seal to stop the silicone leaking; nothing is worse than silicone leaking during a pour!
To mix your silicone, you'll need your scales, a container, a mixing stick, a cover to prevent making a mess, vinyl gloves and of course, the silicone itself. (Note: Don't use latex gloves! Latex can react to the silicone negatively so always use vinyl!) My silicone is 10:1 in weight, meaning it's 10 part silicone, 1 part catalyst (eg. 100 grams of silicone, 10 grams of catalyst) Thoroughly mix the catalyst and silicone together, leaving no streaks!
All you have to do is pick a point in the mould wall and start pouring! It's best to pour a thin stream down into the mould and let the silicone rise slowly. When your piece is completely submerged (~10mm) you can tap the sides of the mould wall to help bubbles rise; you want as few bubbles as possible in your mould to reduce cleanup time later.
Once the silicone is poured & tapped, all you can do now is leave it to cure. Different brands of mould making silicone have different cure time, depending on their catalysts. Mine take 8 hours minimum, some can be longer, some are shorter. Don't disturb the silicone during this period! In the end, I used about 1.6Kg in total.
Step 12: Moulding/Casting: Pt 2 (Optional)
When all your silicone has cured, you can demould! remove the mold walls and carefully remove the prints from the silicone. All my parts were designed to pop out as easily as possible with only a couple of them requiring a bit more effort. The largest mould I made actually needed a seam line cut down the side to help pop out the part with an x-acto knife.
Prepare all the moulds on another sturdy board. The same requirements for making a mould are need for casting resin, with the addition of extra cups. (Note: When working with resin, it's important you cover your skin and work in a well ventilated area to be safe. I'd also advise wearing a respirator for this kind of work.)
My resin is mixed 1:1 by weight (eg. 50 grams Part A, 50 grams Part B). Mix thoroughly until you feel the heat through your mixing cup, then pour at a steady pace. Urethane resin activates very quickly and you can see it turn from liquid to solid; each pour only takes around 15-20 mins to completely cure to repour another cast. I needed 2 copies of all moulds so I did 2 full rounds. I used almost all 2kg I had so if you're worried about mishaps, another Kg will be far more than enough.
Step 13: Paint Prep & Initial Assembly
All pieces are on hand, now it's time to paint!.. Well before we put the final lick of paint on our parts, they need one final prep beforehand. All resin pieces need a coat of plastic primer to help bond the paint to the piece. This layer of primer also makes any bubbles trapped on the resin surface visible. Modelling putty patches these with ease and a quick light sanding after it's dried removes the pits completely.
Because I opted to split my wheels, they need blending together as well. I used more of that tape and body filler to match the surfaces & Epoxied them together; they also get the plastic primer treatment. As well as the wheels, the exhaust pieces were glued and blended.
Now we can finally prime the body! I used filler primer first as the Chemiwood is slightly porous; this seals the surface and can be sanded gloriously smooth. I started with 240, then 320 and 400, and a final wet sanding with 600 grit. Using water with 600 grit makes the model even smoother than if sanded dry.
Step 14: Final Painting: Pt 1
Paint time!
If you nail this stage, your model will shine at its full glory! To get that iconic Mario "M" on the front, red is applied first, then an "M" stencil is layed over the red; I used adhesive paper for this but painters tape cut out works just as well, just trace the "M" over a cut out!
Once aligned, the gloss white is applied. You want to spray multiple thin coats of gloss white to build up colour and sheen. Once dry, the M can be removed, leaving a wonderful sharp contrast!
To create a white ring around the white paint, I overlayed a circle stencil, covering the M and resprayed white over the stencil. The paint thickness reveals the circle once removed.
While the circle is still covered, we can add the iconic stripe and the black interior. Using 6mm Tamiya tape, wrap 2 bands around the body, then mask the entire vehicle with painters tape except the interior; you wouldn't want red overspray at this stage! I only needed 2 coats of red to get a vibrant colour, but still remember to spray thin; we don't want drips here! When the red is dry, spray the interior black.
Let the paint dry, and carefully remove the tape.
Step 15: Final Painting: Pt 2
The vehicle is drying, time to paint the rest!
Most of these pieces are either small or don't stand upright, so some blocks with sticks and double sided mixing sticks are great for helping during painting.
Taking advantage of the 8mm holes in the exhausts, I stand them upright with 8mm dowels & a large block. The exhausts are base painted with a pearl blue and black paint is hand painted in the slots. Once dry, tape up the entire exhaust minus the band & apply gloss white.
The grill is double sided to a mixing stick and the steering wheel is held up with a wooden rod. 2 coats is all that's needed.
The Exhaust caps and side vents are painted dark grey & detail colour is hand painted on each part. (Silver for the side vents, black for exhaust caps.)
The caps & axles are light colours, so I added a white base coat, then painted them their respective colours. any recessed detail is filled with black paint.
The seat is the easiest part to paint; no sticks required to hold it up. 2 coats of green is all that's needed.
Finally the tyre's got a couple coats of "Tamiya Rubber Black" for a real tyre-like appearance; regular black works too but I prefer this flat colour instead.
Step 16: Final Assembly
All the pieces are painted; it's time to assemble!
The last piece to fabricate for the model is the exhaust pipes that connect the exhaust to the engine. Using 8mm acrylic rod, you can bend the rod if you apply enough heat onto it; I used a heat gun in this case. I used this to bend hooks so it can plug into the engine. I drilled 8mm holes into the engine and Epoxied the rods in place. In hindsight, using grey acrylic rod would be better than clear acrylic rod. (I ended up not painting them, as my deadline was looming to submit the model.)
The acrylic rods are sturdy enough to hold up the exhausts, and no glue is required for the connection either; they come on and off in case I need to transport the model a little easier.
A similar procedure was done for the axles, using a 12mm flat bit for the front axles & a 16mm flat bit for the rear axles; I won't lie, it was nerve wracking drilling into my finished painted piece! Take your time when doing this!
A few pieces were pressure fit into their place, like the wheels caps on both sides & the exhaust caps (not pictured) no glue required!
Further to add were the side vents, the steering wheel & the seat. The seat required no glue; it just slides in pace. The side vent pieces were glue to the body, capping the seat in place. Finally, the 6mm metal rod was glued in place and the steering wheel added on the end.
Lastly, the windshield was glued with Epoxy glue, being extra cautious not to use too much glue. Use clear epoxy for this!
Step 17: Complete!
The model is complete! Ready to rev up 'n throw some blue shells!
This was a really fun major project for me, I learned a lot and I got to make a dream project of mine, now it's on to the next thing! Perhaps a scaled Mario to sit in my new ride would make for a good fit...
As always if you have questions, just gimme a shout in the comments and if you're super generous, throw a vote my way for the Wheels, Homemade Gifts and Epilog Contests :) And if you guys have any suggestions for future builds, I'm all ears.
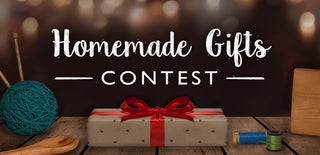
Second Prize in the
Homemade Gifts Contest 2017
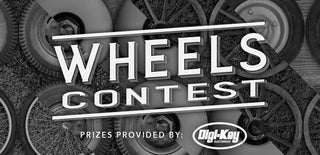
Second Prize in the
Wheels Contest 2017
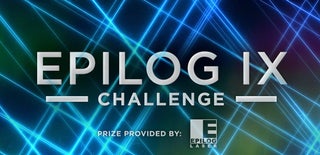
Runner Up in the
Epilog Challenge 9